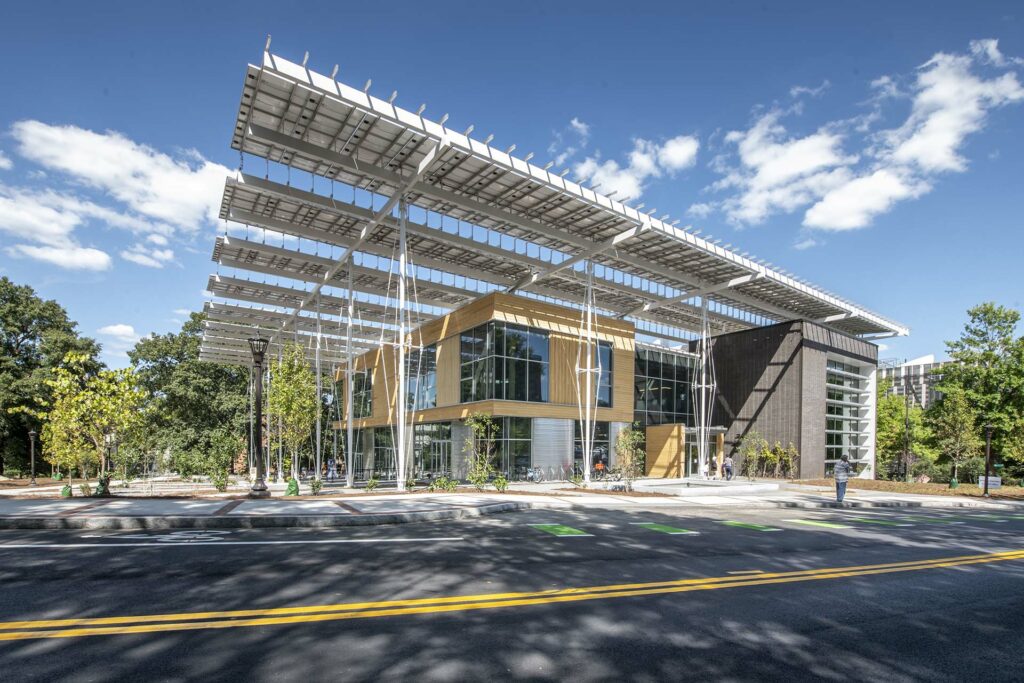
Kendeda Building for Innovative Sustainable Design
The Kendeda Building for Innovative Sustainable Design at the Georgia Institute of Technology physically supports instruction and research, and serves as a public forum for related campus engagement and community outreach activities. The project provides a unique opportunity to physically demonstrate how Georgia Tech practices sustainability as well as providing a campus “hub” for sustainability for their academic, research and community outreach efforts. The building serves as a fully functional, working model of sustainable principles for a variety of audiences to access, study and replicate.
Vital Stats
Certification Status | Living Certified |
Version of LBC | 3.1 |
Location | Atlanta, GA, USA |
Gross Building Area | 36,978 SF |
Start of Occupancy | October 2019 |
Owner Occupied | Yes |
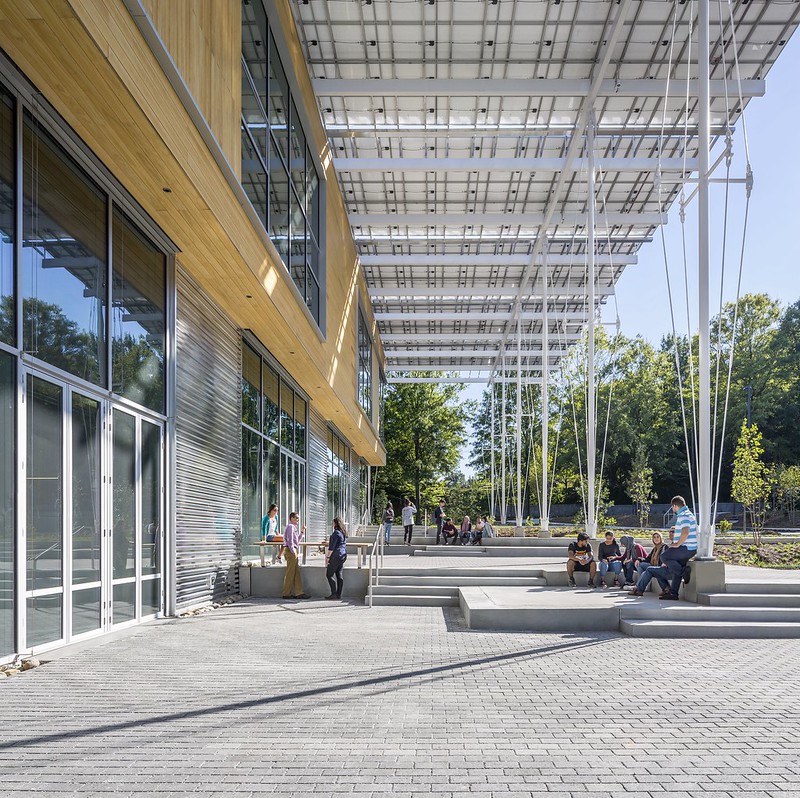
Project Team
Owner | Georgia Tech |
General Contractor | Skanska, USA |
Project Manager | Georgia Tech Facilities, Inc. |
Design Architect | The Miller Hull Partnership |
Architect of Record | Lord Aeck Sargent, A Katerra Company |
MEP of Record | Newcomb & Boyd |
Collaborating MEP | PAE Engineers |
Civil Engineer | Long Engineering |
Structural Engineer | Uzum & Case |
Landscape | Andropogon |
LBC Consultant | The Miller Hull Partnernship |
Lighting Design | Lighting Associates, Inc. |
Geotechnical | Professional Service Industries, Inc. |
Interior Designer | Lord Aeck Sargent, A Katerra Company |
Water & Ecology | Biohabitats |
Life Safety | Jensen Hughes |
Biophilic Consultant | Sonja Bochart Wellbeing+Design |
Place Petal
01. Limits to Growth Imperative
The Kendeda Building occupies a former greyfield site. In place of a pre-development parking lot and street, the Kendeda Building and surrounding site now celebrate biophilia and a highly-sustainable built environment. In combination with the building, the site design navigates competing performance demands for rainwater management, passive building cooling, tree protection, healthy ecology, and urban agriculture, while providing adequate space for human occupancy and year-round seasonal character. The resulting site provides social benefits (e.g. shade, food, beauty) and ecological services (stormwater management, carbon sequestration, wildlife habitat, pollinator foraging), while taking cues from the region’s local ecology. Two of the site’s three main planting zones are modeled after local, reference habitats: mesic woodland and seepage wetland. The third zone provides an edible landscape to help satisfy the urban agriculture imperative, and includes a rooftop farm, edible vine wall, edible landscape, and pollinator nectar course. All three zones are intended to offer rich, didactic opportunities through curriculum integration and self-exploration of novel landscape types.
02. Urban Agriculture Imperative
The Kendeda Building’s 5,406-square-foot rooftop farm satisfies a portion of the LBC’s urban agriculture area requirement while simultaneously offering valuable curriculum and research opportunities; reconnecting students, faculty, and visitors with their food system; modeling sustainable, productive infrastructure; supporting pollinators and pollinator habitat conservation awareness; managing stormwater; and lowering the roof’s albedo. Additional urban agriculture area is achieved through two edible vine walls. To supplement the rooftop and vertical agricultural program, the ground landscape contains a 2,912- square-foot shade-to-partial shade edible landscape. The project’s remaining urban agricultural requirement is met with at least 1,893-square-feet of Tulip Tree (Liriodendron tulipifera) canopy, which supports spring flowers that provide southern, honeybee foragers with a critical, early season nectar source.
03. Habitat Exchange Imperative
In order to meet the Habitat Exchange Imperative requirements, the team participated in ILFI’s Living Future Habitat Exchange Program.
04. Human Powered Living Imperative
The project was developed in an existing greyfield. Previously a parking lot, the site is now home to an approx. 36,980 SF multi-disciplinary academic building, pedestrian paths, outdoor gathering spaces, and native landscape.
The project plan includes weather-protected and secured bicycle storage for up to 44 bicycles. The project includes showers for commuters, and multiple pedestrian and bike paths, connecting to the greater campus and city systems. The building is sited on campus transit routes that connect to regional bus and rail transit. Inside the building, human-powered living is promoted through the design of stairs and ramps, and elevators strategically placed out of direct sight line.
Georgia Tech is nationally recognized for their advocacy of alternative modes of transportation. They have worked for years to create safe bikeways on campus and safe connections to the greater city. The Kendeda Building is no exception. The building and its site connect seamlessly to the campus system, and will support the campus’s greater initiatives towards a safe and robust bicycle culture.
Water Petal
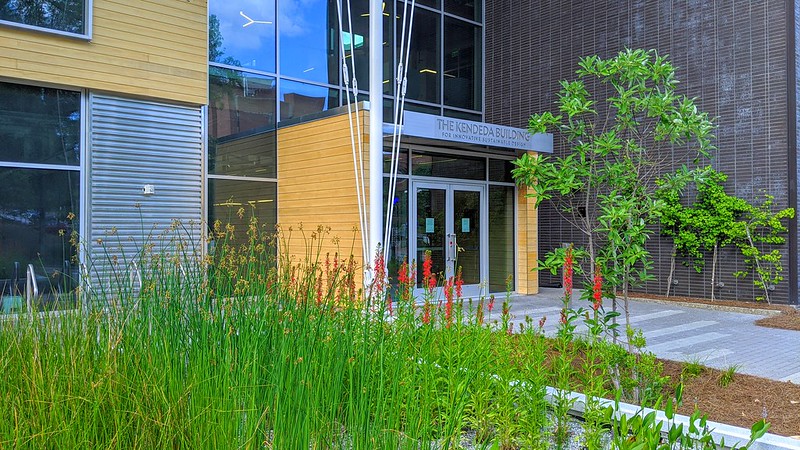
05. Net Positive Water Treatment
The project meets the goal of being “Net Positive” by harvesting, treating, and managing water onsite to preserve the ‘ecological flow’ of downstream water sources. The building collects and infiltrates into the ground more water than it needs for its operation. All water is treated and discharged onsite, including the excess water that overflows from the rainwater cistern and treated greywater. No blackwater is generated on-site due to the use of composting toilets.
The following Water Systems are integrated into the project to meet the Net Zero Water Goals:
- Rainwater capture and treatment to serve as the sole potable water source for the project. A 50,000- gallon cistern located within the basement is sized to store adequate volumes of water to support the building even through sever periods of drought. A potable water treatment skid filters and disinfects the water for potable uses throughout the building.
- Composting toilets and waterless urinals are used throughout the facility in place of conventional flush-fixtures. Removal of flush toilets from the facility has the effect of drastically lowering the water consumption and ‘wastewater’ generation by up to 70%-80% from conventional construction because toilet flushing comprises the majority of water demand for those kinds of facilities.
- A greywater treatment system with a constructed wetland for treatment followed by a soil-based underground drain field system manages greywater produced from the building.
- Condensate generated by the building’s cooling systems is harvested in a reuse tank and reused for irrigation, with backup water from the rainwater cistern when needed.
- Offset district/campus cooling water use (via use of chilled water loop) through infiltration of excess rooftop rainwater. Approximately 74,550 gallons of water will be used at the campus central plant. That water use will be offset on-site by infiltrating at least 74,550 gallons of water from rooftop harvesting (via cistern overflow) over the course of a year.
- Utilize the campus/municipal water supply for Fire Suppression.
Energy Petal
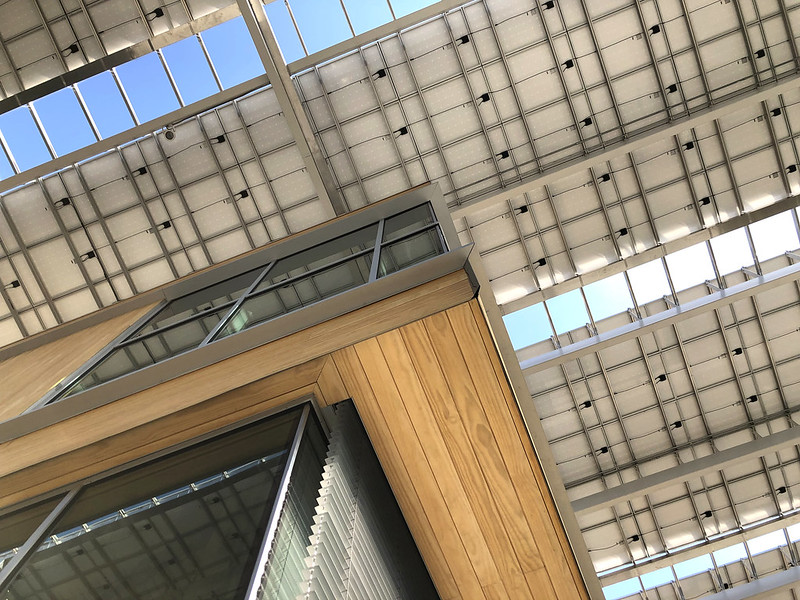
06. Net Positive Energy Imperative
The project used Building Information Modeling (BIM) to construct the physical aspects of the building while also allowing the owner to have embedded information available for use during the life of the project. This starting point allowed for better integration of the Integrated Environmental Solutions Virtual Environment energy modeling tool to provide an incredibly detailed construction of the building and provided confidence in the results over the many iterations of modeling used throughout the design and construction process. For example, the energy results from the various iterations were then compared to the allowable photovoltaics (PV) to ensure the required balance was reached.
Several innovations were utilized in order to achieve the extremely high energy efficiency of the building. These were all balanced against the client’s requirement that this would not be a one-off project, and that each item could be replicated in climates similar to the Southeast US.
To drive down energy consumption, energy load on the building was reduced with the integration of the PV array acting as a porch roof over the side of the building. This provides afternoon shade to a large portion of the building while still allowing significant daylight penetration. External shades compliment the effect and lower during times of the day when the PV array does not block the sun. Triple-pane glazing and natural ventilation add to this effect on reduced mechanical loads.
The mechanical system for the majority of the building consists of radiant flooring made with slabs that are cooled and heated with a Dedicated Outside Air System (DOAS) providing 100% outside air to satisfy the ventilation requirements. A heat pump chiller provides the heating water to the building while its ‘waste’ product is chilled water that is fed into the campus chilled water loop.
This project allowed the design team to fully-integrate on an aligned mission, evaluate a number of alternatives and innovations, and provide a high-performance building that can be repeated in many places across the world.
Health and Happiness Petal

07. Civilized Environment Imperative
On Level 1 and Level 2, each regularly-occupied space is in compliance with access to fresh air and daylight. There are operable windows located within 30′ of regularly-occupied spaces. The high amount of glazing encourages occupants to have a visual relief and engage with the outdoor environment. The implementation of interior window shades, exterior blinds, and fixed louver shades allow for occupants to manage glare control and how much daylight is needed in each space. Each space has an override button to control the operable windows, interior shades, and exterior blinds. The atrium in the center of the building has two skylights above with several operable windows that allow for natural daylight and air to be brought into the immediate areas of the atrium at Level 1 and Level 2. The basement level is exempt from the operable window requirements because it contains the electrical room, composting room, mechanical room, circulation space, custodial, recycling, and bike storage.
08. Healthy Interior Environment Imperative
In order to prioritize occupant health, multiple measures have been included in the Kendeda Building to minimize indoor pollutants. As required, the project is in compliance with ASHRAE 62. The project also complies with Georgia Tech’s campus-wide no-smoking policy. The IAQ test before and after nine months of occupancy meet the guidelines of LBC standards and the project is in compliance with CDPH standards. There is dedicated exhaust for the restrooms, which are a part of the composting toilet system that is exhausted by the rooftop fans. There are metal walk-off grates at each main entrance of the building to reduce particulates being brought in by occupants of the building. Additionally, the entrances include vestibules with air curtains above the interior doors to keep outside air from infiltrating into the interior of the building. Georgia Tech Facilities have a cleaning protocol with products that comply with EPA Safer Choice label. Furthermore, there are CO2 monitors installed throughout the building to ensure the quality of air is maintained.
09. Biophilic Environment Imperative
At the very beginning of the project, the team engaged in an interdisciplinary, immersive, and interactive biophilic design workshop, where a biophilic framework and implementation plan were developed. Attendees included Georgia Tech staff, faculty and students, project funders, local environmental organizations and activists, architects, landscape designers, interior designers, engineers, leading industry experts and community members. Its format included mindfulness, biophilic design education, biomimicry integration, nature-immersion, reflection, play, interdisciplinary team-based project work, dialogue and review.
The Georgia Institute of Technology Living Building, Biophilic Design workshop was designed to help explore and together, develop a unique, place-based biophilic design framework for the project that supports the intent to encourage and inspire meaningful connection between people and place.
Materials Petal
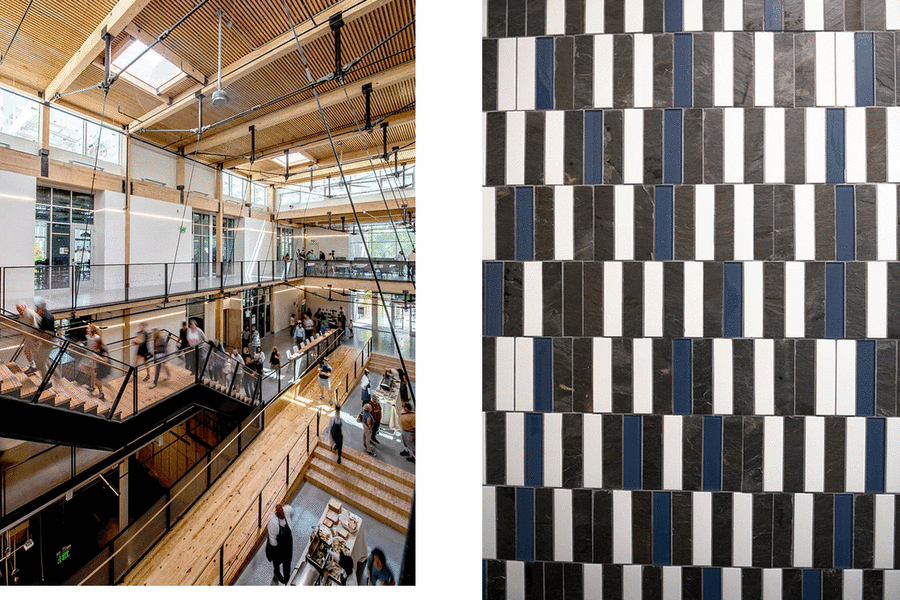
10. Red List Imperative
The vetting and documentation process was a design and construction effort developed early on in the Design Development stage and continually addressed through the submittal process during the Construction phase. At the Design Development phase, the team wrote specifications to ensure red list compliance and competition began with a review of the ILFI Declare database for products having a Declare Label that was particularly noted as Red List Free or Red List Compliant. Not all building materials are Declare, so the design team then reviewed products that were fully disclosed or products that showed promise of no Red List materials.
Later in the construction phase, the team created a Materials Committee consisting of sustainability product experts from Skanska and the Miller Hull Team. These folks had experience with Living Building projects and knew the best path forward for documenting each product. The design team logged 187 product research-related discussions during this parallel submittal phase to achieve compliance or the best available due diligence in the market. It was at the final material procurement stage that the design team were most able to influence the market and work with the suppliers to make changes to or towards full Red List compliance. For products that needed due diligence, which consisted of a minimum of two similar product manufacturers, the team sent out Advocacy Letters to ensure the manufacturers of this product type were aware that the product contained Red List chemicals and advise them to fully disclose their ingredients and/or revise the ingredients to be red list free in their products. The team also sent out Advocacy Letters to ASTM, NAAMM, and NSSGA to advise these companies to develop a third-party certification program to ensure sustainable and ethical harvest of resources.
The design team for the Kendeda Building specified EcoBatt Unfaced Knauf Insulation for its thermal and acoustical properties. Most importantly, the mineral wool insulation product is Red List Free and has a Declare Label. This product uses an ECOSE Technology plant-based chemistry that is phenol/formaldehyde-free. A typical fiberglass insulation, a common product that most architects specify for non-living buildings, usually contains this toxic chemical. Mineral wool is more expensive but has these advantages and more. It is also more resistant to fire, contains a high percentage of recycled bottle glass, a higher sound barrier, and less energy to manufacturer than fiberglass insulation. The product is also easier to install and it resists tears with low dust. It has high resiliency and recovers to become full thickness for a snug fit to prevent gaps in the installation of the insulation. This sustainable mineral wool product should be specified in all buildings and not just Living Buildings.
11. Embodied Carbon Footprint
The Kendeda Building has minimized embodied carbon through strategic design methods, analysis, and an offset purchase. During the design phase, the team intentionally used mass timber as the main structural member with minimal use of steel and concrete. Since the structure of a building is understood to be where 80% of the overall embodied carbon emissions reside, tackling this item greatly helped the team with the building’s carbon footprint. Besides being sustainably sourced, mass timber sequesters carbon while steel and concrete emit carbon. The use of salvaged materials throughout the building prevented new carbon emissions altogether. Intentional specification of products furthered the carbon emissions reduction with high-recycled content such as mineral wool insulation, brick used as rainscreen, etc. The life cycle carbon emissions of the project were quantified using the software Tally, so as to include manufacturing, transportation, construction and end-of-life stages. The project team then purchased a one-time carbon offset through Schneider Electric based on the quantified carbon emissions.
12. Responsible Industry Imperative
Salvaged Materials were often used for several features throughout the Kendeda Building. The wood platform that is used as the main structural member for the floor is called Nail-Laminated Timber (NLT). The Lifecycle Building Center captured thousands of two-by-fours from movie production sets that were no longer in use. The NLT is comprised of two-by-fours and two-by-sixes nailed together, which create a distinctive fluted pattern. Naturally fallen trees on campus were also captured and formed to create live edge countertops throughout the building. The exterior benches are made out of white oak from fallen trees from a severe storm that occurred in central Georgia. The accent wood walls and ramps were salvaged from a church that was demolished adjacent to the campus. The treads on the monumental stair are comprised of salvaged wood captured from the 1880’s Tech Tower joist renovation. The structure of the building is made from Glulman beams and columns which are made from the local southern yellow pine. Wood is used throughout the building using sustainably harvested or salvaged material to reduce the overall embodied carbon of the building.
13. Living Economy Sourcing Imperative
The Kendeda Building supports the southeastern economy by utilizing local products and suppliers. This not only minimizes the environmental impact associated with the transportation of products and people but also helps strengthen the local community. Green Leaf Brick is a great example of an environmentally friendly product that is locally manufactured in North Carolina by Red Tree Group. The Black Special architectural brick is not on the Red List and is made from 100% recycled materials in which up to 31 percent comprised of post-consumer recycled ingredients. The subcontractor that installed this product was Cronos Contractors, a company located in Georgia. Kawneer Curtain Wall Systems is another example. Eleven of the company’s products have Declare Labels and none of these products are on the Red List. The product is manufactured by Kawneer, located in Norcross, Georiga. The subcontractor for this product was CrownCorr which is located in Lithia Springs, Georgia. These are a few key examples of ways the Kendeda Building stimulates and supports the local economy of the Southeast.
14. Net Positive Waste
One of the main methods that the Kendeda Building used to reach net positive waste was by incorporating one salvaged material per 500 square meters of gross building area.
Through design, coordination, and resourcefulness, the project team reused a series of salvaged materials to incorporate 27 re-purposed components, more than tripling the minimum requirement. Below are some examples.
- Slate shingles were removed from the roof of the Alumni House on campus and reused as tile for the walls of the restrooms.
- Wood panels and joists from a razed church on the edge of campus made the central ADA ramp and wall features.
- Dismantled movie sets provided 25,000 linear feet of two-by-fours that were incorporated into the exposed nail-laminated floor and roofing decks.
- The granite curb around the entrance was salvaged from the demolished Georgia State Archives Building that used local granite from Stone Mountain.
- The Kendeda Building’s monumental staircase treads are salvaged heart pine dating back to the late 1800s from joists that were captured from Tech Tower’s egress stair renovation.
- The live-edge counters and benches were derived from the storm-felled trees on Georgia Tech’s campus and were left with a live-edge to embrace the natural appearance of the tree itself.
Equity Petal
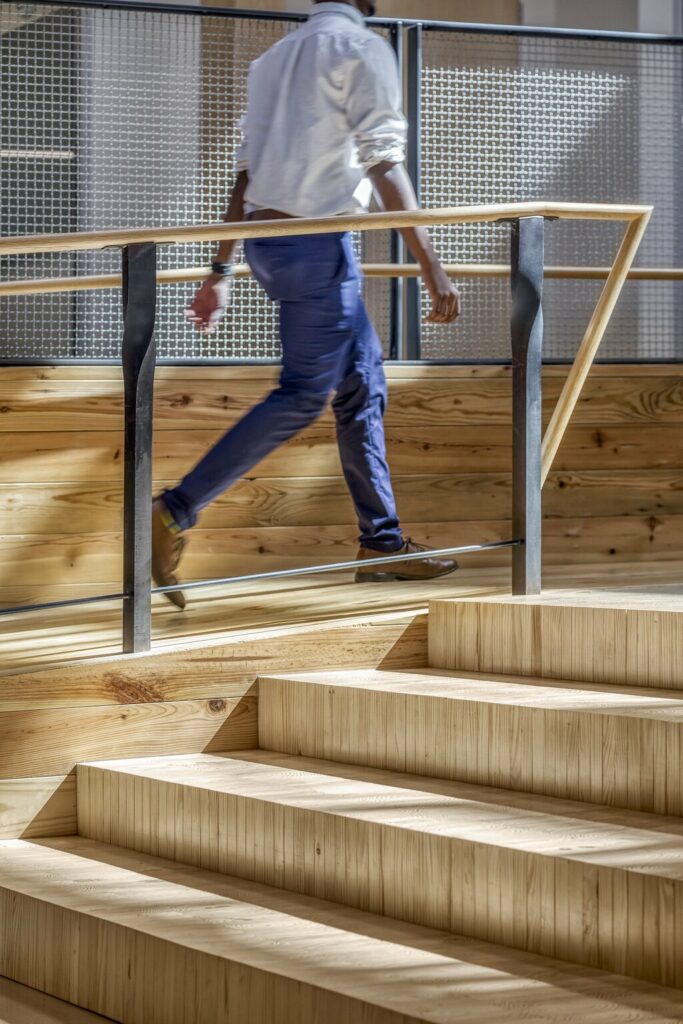
15. Human Scale and Human Places Imperative
The Kendeda Building contains human-scaled places that promote human interaction with these elements listed below:
The building promotes human interaction by fully eliminating automobile-scaled areas. The site does not have parking spaces directly within the project boundary. The Kendeda Building is located on Georgia Tech’s campus that has shared parking decks and spaces. The new construction of the building removed all existing parking spaces that existed on the site. The Dalney Parking Deck is the parking structure that would be most often used if people were visiting the building. The parking structure contains 784 parking spaces with 20 electric charging stations.
For signage, there are no signs on the site that are considered large which is exceeding four square meters (43 square feet). The largest sign on the site is located at the corner of State Street and Ferst Drive. It is the standard sign that Georgia Tech requires for each building on campus that shows the name of the building and street address. It is 3’-0” wide by 5’-2” tall which is 15.5 square feet.
Proportionally, the curtain wall openings and doors do not exceed the maximum distance of 30 meters. The Kendeda Building footprint is 19,141 square feet which exceed the required maximum footprint of 1,000 square meters (10,763 square feet) before articulation occurs.
For human scale articulation, the building contains places for people to gather and connect within the interior and exterior of the building. These spaces are throughout the building and allow for students, faculty, and visitors of Georgia Tech to connect and socialize. On the basement level, there is an area that allows tours to occur where visitors can view the mural on the south wall or view all the various systems which include the electrical room, composting room, water treatment area, and mechanical room. On Level 1, there are multiple break out areas where students and visitors can study and have conversations. The occupiable stair is an area where people can sit and have impromptu interactions. Live edge tables throughout promote areas of studying. Also, throughout these spaces, there are two nanowalls that open up to the exterior space under the PV array canopy. This allows a fluid movement from exterior to interior. People are encouraged to be outside where there are several benches, tables, and seating in this area. As you move to the second floor, there are also live edge tables and seating to promote social interactions as well as a green roof area that have tables and chairs for people to gather and enjoy the outdoors. Along the western and southern edge of the building contains several benches that support human scale. These spaces encourage opportunities for engagement while promoting human-scale articulation.
16. Universal Access to Nature and Place Imperative
The Kendeda Building transformed what was previously a parking lot into a building that has indoor and outdoor spaces that are inclusive of everyone and allowing equal access to nature and place. The ramp is situated, front and center, of the open atrium inside of the building and serves as a beautiful celebration throughout Level 1 of the atrium, as opposed to hiding or diminishing the ramp as an access route. Adjacent to either side of the ramp are the monumental and occupiable stairs which encourage movement and interaction. While the stairs are functional, they also are comprised of salvaged materials in an articulated manner that celebrates the use of natural materials. The outdoor space has several areas for bike racks, benches, ADA accessible pathways intertwined within rain gardens and vegetation underneath a large “porch” created by the PV array. The result is a place that encourages socialization and interaction with each other and nature.
17. Equitable Investment
The team at Georgia Tech has many plans to give back to the community through programming and partnerships. An example, that occurred during the construction of the project was a paid partnership with the construction management firm, Skanska, forged with Georgia Works!. Georgia Works! is a local organization that trains formerly homeless individuals in construction trades and helps place them at job sites. Six Georgia Works! graduates helped build the Kendeda Building nail laminated deck, thereby gaining marketable skills. One of the graduates was hired by Skanska!
Beauty Petal
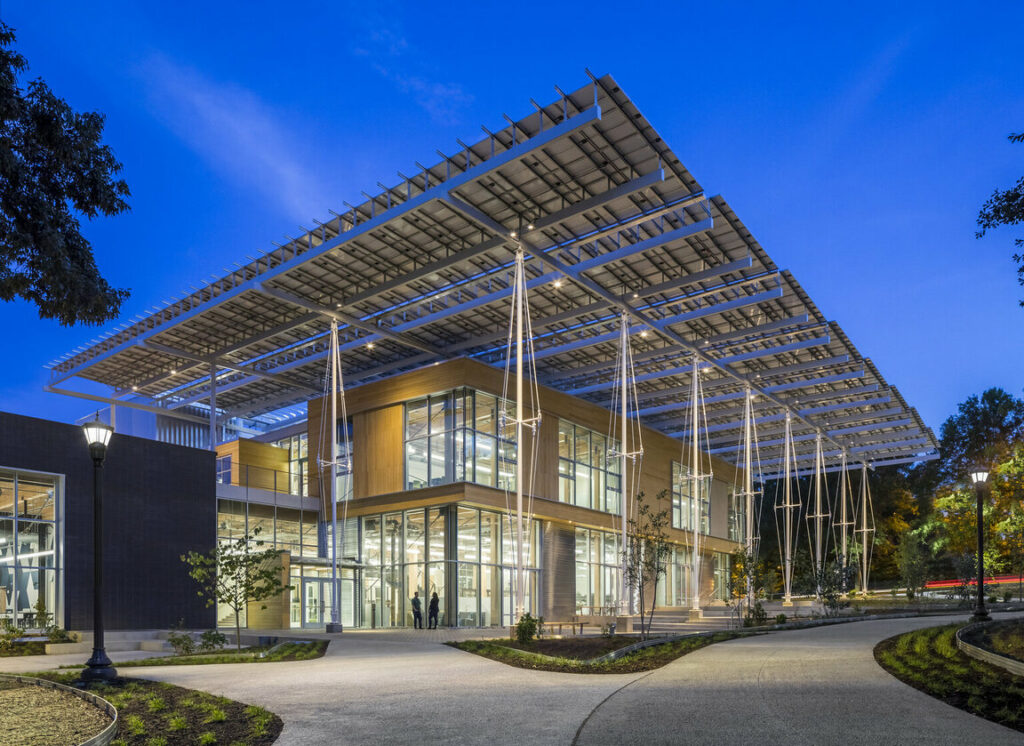
19. Beauty and Spirit Imperative
In designing the Kendeda Building, the architect team of The Miller Hull Partnership and Lord Aeck Sargent recognized that sustainability is not limited to the preservation and conservation of natural resources, but rather incorporates many factors including the aesthetic quality of the built environment.
The intent of the Living Building Challenge’s Beauty Petal, which is one of seven stringent performance criteria, is to ensure that care is exercised in creating places and spaces that are inspirational and enjoyable to all. The Beauty Petal requires design features that are intended solely for human delight, including opportunities for public art. It also requires the building to include educational opportunities for regular occupants as well as visitors.
Below are examples of how beauty is being incorporated into the design for the Kendeda Building.
PUBLIC ART
The integration of public art has occurred throughout the building. On the basement level, a local Atlanta artist Beardy Glasses painted a mural on the south wall that shows how the water treatment process works throughout the building. In addition, the building displays rotating art throughout the building. In Fall 2019, the building displayed artwork by artists Virginie Drujon-Kippelen and Shannon Davis from their project entitled “Urban Wilderness + Man-Made Nature.” The subject of this particular art piece was nature, through two opposite lenses: one is “urban wilderness,” which explores the experience of nature redefined by human proximity. The other presents “man-made” nature, how nature is manipulated by man in order to co-exist. There are also free-standing signage that move throughout the building that displays information about each petal. In general, all of the pieces relate to the Living Building Challenge’s sustainability goals.
STAIR AND ATRIUM
The circulation through the site and the building is essentially the connective tissue of discovery that links the Kendeda Building with the adjacent EcoCommons. The two-story central atrium is the heart of the building. The wide, open volume draws people in and through the building. It delivers daylight to the interior of the building while also serving as flexible circulation and program space. Gracious proportions with oversized landings provide places to pause and take in views of the central atrium space where select building systems are on display. The monumental stair, ramp, and occupiable stairs are front and center of the building to encourage movement from one level to another. While they are functional, they are also beautiful where they use salvaged materials in articulated ways. The functional and yet beautiful center of the building is eye-catching and encourages interaction and movement within the space.
MATERIALS
Simple, straightforward methods of construction emphasizing a material’s palette primarily found in nature are used. The palette used is regionally appropriate, low carbon, durable, non-toxic, and cost-effective. Limiting the use of high carbon materials such as steel and concrete to only where they are most needed helps minimize environmental impact.
Sustainable and/or salvaged wood sourced from the Southeast are used for their beauty, durability, and regional relevance, without needing significant additional materials or coatings for finishing. All materials were carefully selected to make an appealing composition to the occupants of the building.
REGIONAL DESIGN INFLUENCE
The porch typology has come to define the vernacular architecture of the southeast. It is a typology that is familiar to people within the southeast region. The porch is also a transitional space allowing connection between the built and natural environments and between the building occupants and the community. The porch of the Living Building at Georgia Tech wraps the façade to create a welcoming, covered open spaces that give access to the south, west, and north. It blurs the line between inside and out while passively mitigating the climate.
The west porch steps with grade, linking the building directly to the landscape and constructed wetlands and serves as the primary orientation to the site. The building also steps with the site along the western edge, integrating the pedestrian experience with the building. The north porch, which is the green roof area on Level 2, fosters a strong connection to the outdoor spaces beneath the canopy of the great oak and pecan trees. The west porch roof overhang not only provides critical western solar gain protection in addition to what the grove of trees will provide, but it also offers an ample array of sheltered outdoor spaces that blur the line between indoors and the outdoors.
20. Inspiration and Education Imperative
The Kendeda Building is an exemplary educational opportunity that Georgia Tech uses to teach others in the community. It is similar to the analogy of the pebble being thrown in the pond causing a ripple effect to it’s surroundings. Georgia Tech is continuously giving weekly tours of the building; as well as hosting events and conferences. Throughout the interior and exterior of the building, there are several interpretive signs that inform visitors and occupants about the Living Building Challenge. There are also simple brochures that describe the design ideas and environmental features of the project. An educational website dedicated for the Kendeda Building is also available for people who want to know more information about the building and those who are not able to visit the project in person. This includes a virtual tour, news updates, and rolling a blog posted on the website. An “Opening Day” event first took place on October 24, 2019, with guided tours throughout the day. Georgia Tech plans to make this an annual event, open to the public.