VITAL STATS
Certification Status | Zero Energy Certified |
Date of Certification | December 1, 2017 |
Version of LBC | 3.1 |
Location | Watertown, CT, USA |
Typology | Building |
Project Area | 3,891 SF |
Start of Occupancy | April 2015 |
Owner Occupied | Yes |
Occupancy Type | Single-Family Residence |
Number of Occupants | 2 |
PROJECT TEAM
Owner | The Taft School |
Project Manager | Elizabeth Disalvo, AIA |
General Contractor | Mike Trolle + Chris Trolle, BPC Green Builders, Inc. |
Architect | Trillium Architects, LLC |
MEP Engineer | Dean DeMague, High Performance Energy Services |
Electrical Engineer | Jason Kayfus, Amp Electric, LLC |
Lighting Design | Trillium Architects |
Interior Design | Mak Design + Build |
Plumbing | Joe Fusaro, Fusaro Plumbing + Heating |
Key Subcontractors | Geotechnical: Dr. Clarence Welti, P.E., P.C. Civil Engineer: Scott Meyers, L.S., Meyers Associates, P.C. Structural Engineer: Joe Carone, P.E., DiBlasi Associates, P.C. |
Specialty Consultants | Steven Winter Associates, Inc., Provider, Rater, Verifier for Energy Star v3.1, Indoor airPLUS, Water Sense, DOE Zero Energy Ready Home, LEED BD+C Homes v4, Passive House |
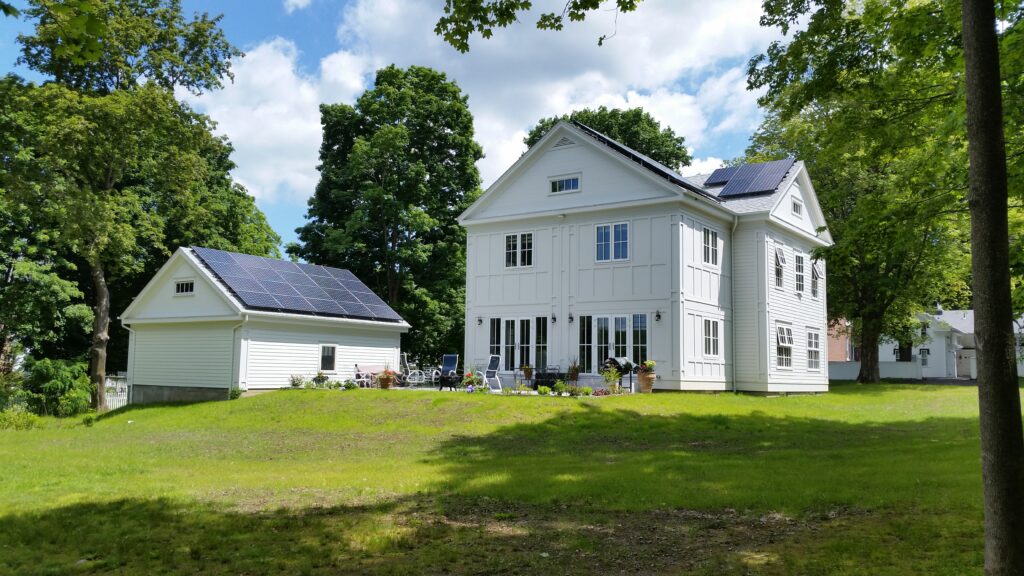
BUILDING SYSTEMS INFORMATION
Wall R value and section specification | 54.9. The home’s thermal envelope starts with a 10 inch thick poured concrete basement wall insulate on the inside with 3 inches (R-19.2) of closed-cell spray foam. A 2×4 wall at 24″ OC is built to the inside of the applied spray foam and filled with R-13.3 of blown cellulose for a total wall insulation value of R-32.5. |
Roof R value and section specification | 35.1. The attic contains 24 inches of blown cellulose installed over the attic floor, which consists of 3/4″ plywood layer installed over the second floor’s 9.5 inch deep engineered ceiling joists. |
Floor R value and section specification | 35.1. The basement slab floor is wrapped with R-20 (4 inches) of EPS IX rigid foam at the slab’s perimeter, where it meets the foundation wall and 8 inches (R-35.6) of EPS IX rigid foam extends under the entire slab. |
Windows | 0.137 U-value. The windows are uPVC-framed in the basement and aluminum clad wood framed elsewhere. All windows are triple-paned with argon gas fill and two low-E coatings to minimize heat losses and gains. |
Air infiltration rate and sealing protocol | 0.44 ACH50. ZIPS taped seam complete air barrier exterior and cell foam in cavities and air sealing penetrations with foam and caulk. |
NON-MECHANICAL SYSTEMS
The majority of the home’s heating load is satisfied by internal and solar heat gains, with more glazing placed on southern exposures to capture those gains. The southern, eastern, and western walls of the house have 406 SF of glazing with a center of glass U value of 0.11 and a 0.61 solar heat gain coefficient (SGHC) that admits beneficial solar heat during the heating season.
MECHANICAL HEATING AND COOLING
Space conditioning is provided by a split-system air-source heat pump which was installed with mini indoor air-handlers on each floor. The heat pump equipment has a cooling efficiency of 16.5 SEER and a heating efficiency of 9.3 HSPF, exceeding the minimum federal standard of 13 SEER and 7.7 HSPF. Air-handlers are ducted to each of the rooms through the shortest routes possible, except for the basement unit which is wall hung without any ductwork. A central return and transfer ducts exist in the walls for both the first and second-floor air-handlers.
MECHANICAL VENTILATION
A highly efficient heat recovery ventilator (HRV) was installed. The HRV provides balanced ventilation, bringing in and exhausting the same amounts of air. The two air streams cross within a heat exchanger core inside the HRV transferring sensible heat from the warmer path to the cooler to minimize heat losses in the winter and heat gains in the summer. The HRV has a 93.3% heat transfer efficiency and includes a high-efficiency MERV 7 filter.
LIGHTING
92% percent of the home consists of LED lighting.
RENEWABLE PRODUCTION SYSTEMS INFORMATION
SunPower 327 Watt, 40 panels, inverter model, 2-SMA Inverters, Total watts installed – 13.1 kW, SUNNY Boy 3000TL-US inverter. 97% efficiency
PERFORMANCE
Actual energy use during performance period | 5,420.3 kWh |
Actual energy produced during performance period | 15,288.8 kWh |
Net Energy Use | -9,868.5 kWh |
EUI | 4.75 kbtu/SF/yr |
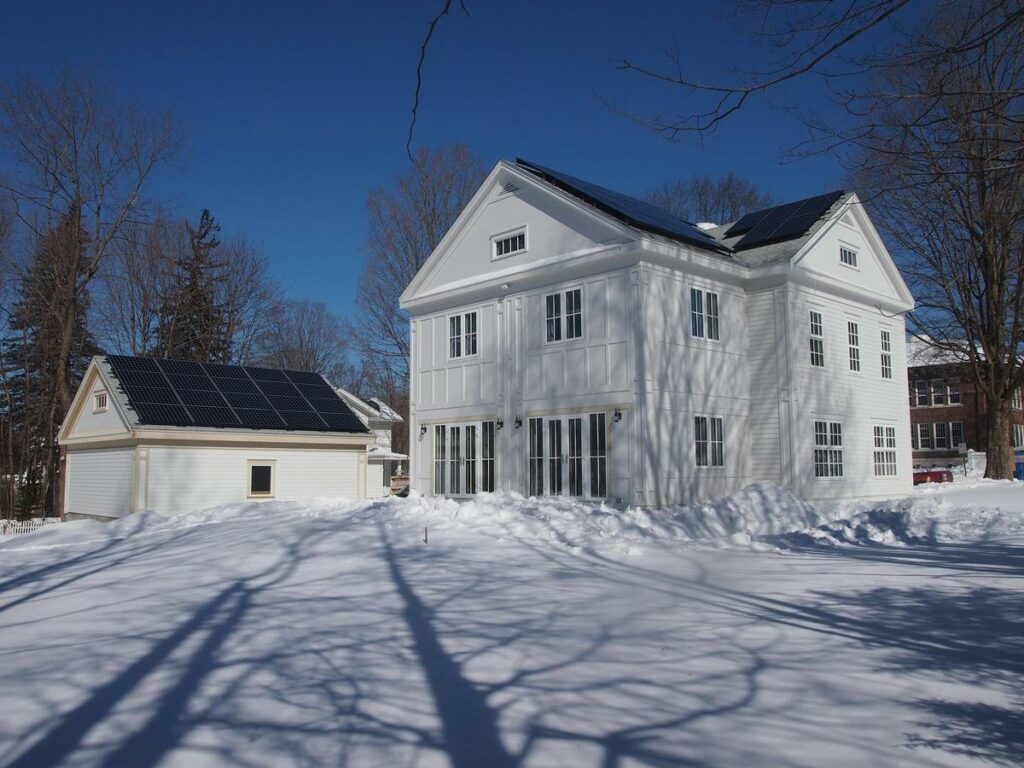
DESIGN PROCESS
The Taft School requested a new faculty home that would be as energy efficient as possible. It was required that the house meet historic district requirements for aesthetics. This meant that the project team could not design a house that primarily placed windows on the southern side. The team had to evenly disperse the windows around the house to resemble a classic Greek Revival. They planned the windows on the front of the house (east side) to be smaller and the windows on the south side to be larger while maintaining the classic order. The back (west side) of the house, is not seen from the street, therefore, the team was able to place larger windows there. The north side of the residence is less visible to the street, enabling the project team to design the internal uses to load utilitarian space on the north side. There, they placed few windows as possible. The 12” thick walls (double studs packed with cellulose and wrapped in continuous foam board) make for a sturdy and charming interior. Part of their design goal was to make the home appear more like a historic house. The window configurations, thick walls, trim and historic paint colors all help to achieve the goal. Since there are windows on all sides of the home and because the house has a near perfect colonial layout, allows daylight to each side and each room in the home.
An additional challenge with windows arose. The historic board required double-hung windows. However, these windows cannot be manufactured with a decent U value to meet the goals of the Passive House. So, the team came up with a window configuration – with Klearwall, a window manufacturer- which resulted in an awning over a fixed configuration that looks very much like a double-hung window. The window that needed to provide egress, includes a casement with a thick check rail as a compromise, which ended up looking less like a double-hung window.
On the lower level, the design team opted for an open floor plan, a nod to our more modern lifestyles. This works very well around a central core that houses utilities and provides short plumbing and HVAC throughout the house.
The design of the attic allowed the team to put a 24” blanket of cellulose insulation on top of the house. This makes a tremendous difference in the temperature swings inside the house (there are none!)
OCCUPANCY ISSUES
Upon occupancy, the owners did not believe the air subsystem was on. The combination of minspilts and a Zender ERV were so quiet and modulated that the occupants could not hear them and thought the system was not working. The temperature and air quality proved to be fine. The general contractor took them to the mechanical room and showed them, that all was working perfectly.
BUILDING COMMISSIONING, START UP, AND OPTIMIZATION
The builder is a professional engineer who designed the HVAC system and monitored the systems installation, HVAC trade balanced space conditioning and ventilation air systems during equipment startup, proved the proper refrigerant charge, verified thermostat control to each indoor unit, and indoor units all communicate with the single outdoor mini-split unit. Ventilation system controls and remotes were also adjusted to house size and number of bathrooms.
SWA provided verification of plumbing DHW flow rates and times based on occupant calls from each bathroom as well as HVAC air flow rates during house blower door pressurization testing.
Convincing the town’s historic commission to accept Euro alternative to American-made double-hung windows, proved to be challenging.
REGULATORY ISSUES
The only major issue was with the Historic Commission, which enabled traditional building codes to influence the overall look of the residence and the placement of the windows in the house. Town regulations required strict water management that yielded a rain garden which the chickens and other wildlife enjoy.
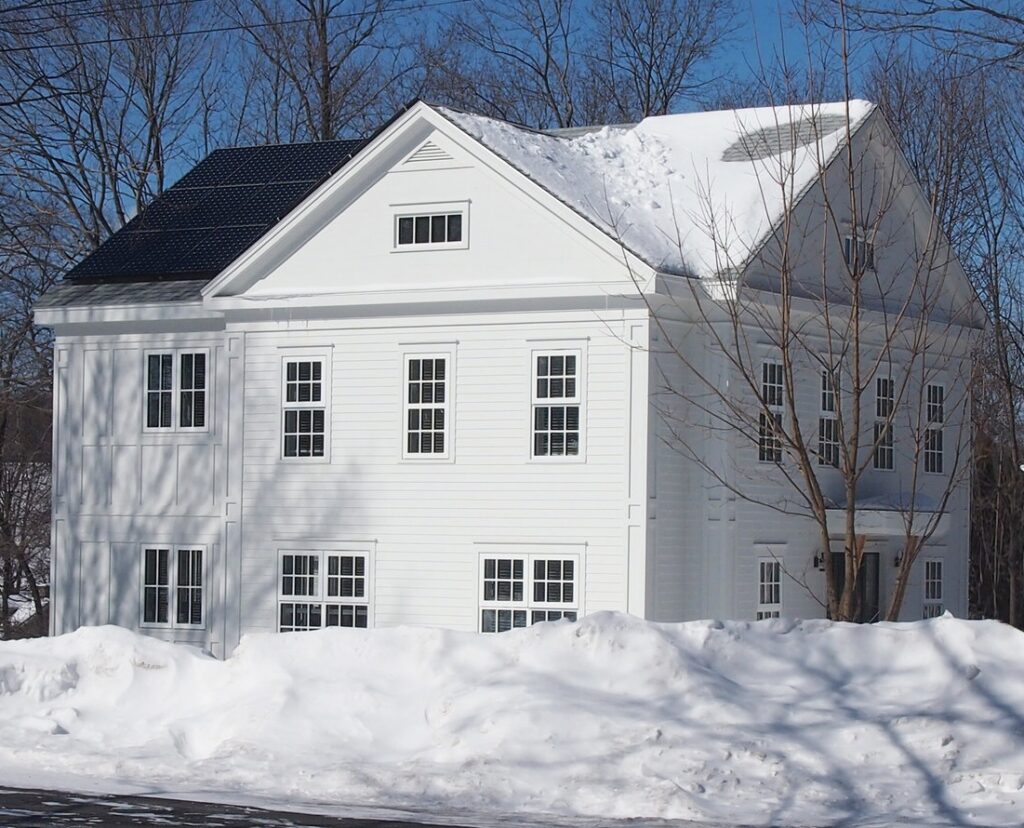
LESSONS LEARNED
The house uses a lot less energy than was projected. This is the result of a combination of thrifty occupants and construction that went better than planned. The team was able to seal the house better and provide more insulation in the attic than originally thought. The simplicity of the plan with a central core worked so well for this house, not only for occupant happiness but for the efficiencies of all systems.