VITAL STATS
Certification Status | Zero Energy Certified |
Version | 1.0 |
Location | Boston, MA, USA |
Typology | New Building |
Gross Building Area | 8545 SF |
Start of Occupancy | December 2020 |
Occupancy Type | Commercial Building |
PROJECT TEAM
Owner | Boston Building Materials Resource Center |
Owner Representative | Paul H. La Pointe |
General Contractor | Landmark Structures |
Architect | Black River Architects |
MEP Engineer | Wozny/ Barber & Associates |
Structural Engineer | Kanyao Lala, Professional Engineer |
Civil Engineer | Boston Coastal Consulting |
Energy Consultant | DEAP Energy Group, LLC |
Surveyor | Framingham Survey Consultants |
Fire Protection Engineer | LVR Fire Corporation |
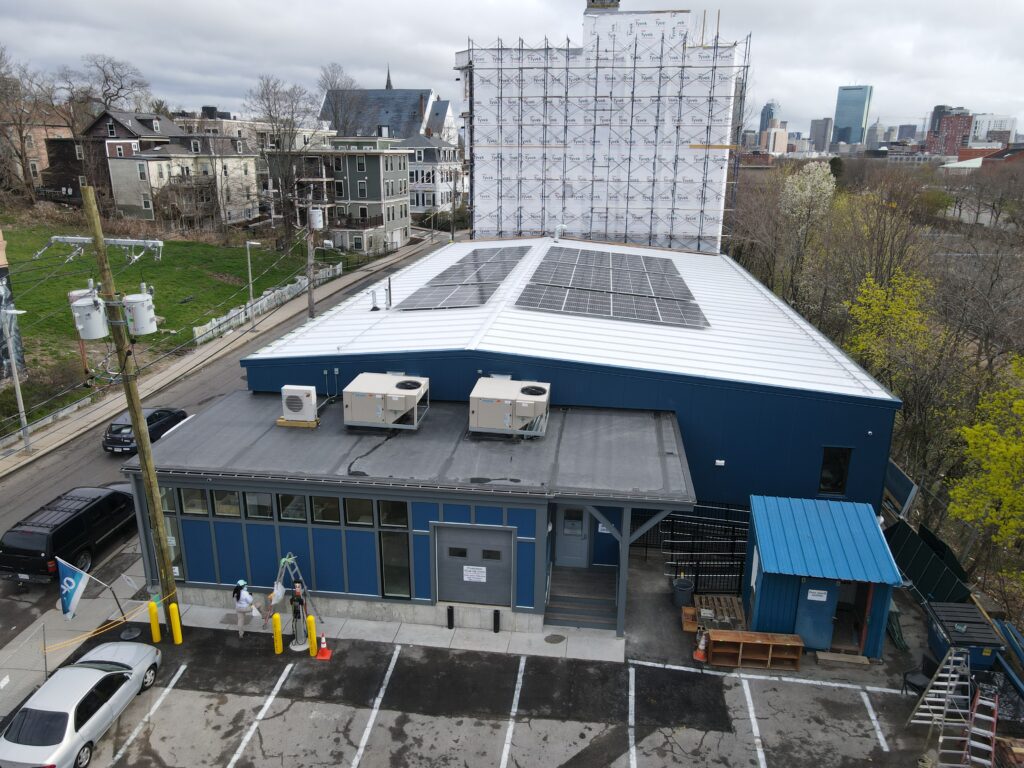
RENEWABLE PRODUCTION SYSTEMS INFORMATION
ENERGY PERFORMANCE
Renewable Type | Solar Electric (PV) |
Total Renewable Capacity | 45.89 kW |
Renewable Location | On-site |
PROJECT LEADERSHIP AND STORY OF THE PROJECT
The Reuse Center at Boston Building Resources is a building that houses high-value, affordable materials, both new and saved, for home maintenance and improvements. Customers can also find expert advice, technical assistance, and hands-on workshops that teach home improvement skills. The renovation of this building includes a new interior layout and storage solutions, as well as an addition that serves as a waiting area and kitchen cabinet display. The program holds customer waiting areas, materials and lighting displays, offices, processing areas, a break room, and a vehicle loading dock.
ENERGY SYSTEMS NARRATIVE
The project is a renovation with an addition to an existing warehouse, processing area, and retail sales area for a Co-Op-based building materials reuse center housed in an 8,545 sq ft pre-engineered metal box.
Energy efficiency strategies incorporated include completely re-cladding and sealing the envelope with high-performance structurally insulated panels (SIPS). The team also installed a new high-performance air-source heat pump-based HVAC system(s) and integral ventilation to replace the gas space and radiant heating systems.
Energy is generated by on-site PV panels with a roof-mounted array on the Warehouse roof, integrated into the local Grid with “Net Zero Metering.” The project was modeled for all energy needs planned for operations in the design, and the array was designed to meet that need. A fair amount of buffer was planned for, and any excess production would go to the sister Co-op building adjacent to the property or to the staff/member EV charging station in the parking lot. The original warehouse roof structure needed additional structural framing to support the array, so about 60% of the roof was upgraded.
LESSONS LEARNED
The project was quite an adventure for its scale and budget. There were many lessons learned, but the three key ones were:
- A very robust and tight envelope makes managing energy consumption significantly easier, predictable, and comfortable. The staff, members, and customers are all astounded at the level of comfort and consistency of the indoor climate.
- The openness of the larger spaces and the simplicity of the systems meant that even small adjustments to operational use all had significant impacts on energy consumption. These adjustments included having set points, educating staff and customers on the importance of using the overhead door and truck bays airlocks to manage air quality and energy loss concerns and incorporating minor adjustments to air-sealing during commissioning. It took several months of operations to identify user and operational impacts and opportunities to reduce energy consumption and bring the building into NZE.
- There is a need to commission the envelope to effectively persist in validating and improving the air sealing to reduce infiltration and dust movement. The testing (blower door test) and pressurizing led to the identification of several areas and connections that had not been properly executed during construction. The GC was able to locate and remedially seal these locations, leading to significant improvements in performance.