VITAL STATS
Certification Status | Zero Energy Certified |
Version | 1.0 |
Location | Countryside, IL, USA |
Typology | New Building |
Gross Building Area | 34,600 SF |
Start of Occupancy | October 2019 |
Owner Occupied | Yes |
Occupancy Type | Government |
Number of Occupants | 36 |
Number of Visitors | 20 |
PROJECT TEAM
Owner | City of Countryside |
General Contractor | Frederick Quinn Corporation |
Architect | Dewberry Architects |
Mechanical Engineer | Dewberry Engineers |
Electrical Contractor | Dewberry Engineers |
Interior Designer | Dewberry Architects |
Plumbing | Dewberry Engineers |
Fire Protection | Dewberry Engineers |
Civil Engineer | Eriksson Engineering and Associates |
Landscape | Hitchcock Design Group |
Structural Engineer | Dewberry |
Commissioning | Smith Seckman Reid |
Certification Consultant | Dewberry Architects |
Educational Signage | Cardosi Kiper Design Group |
RENEWABLE PRODUCTION SYSTEMS INFORMATION
ENERGY PERFORMANCE & EUI
Renewable Type | Solar Electric (PV) |
Total Renewable Capacity | 225 kW |
Renewable Location | On-site |
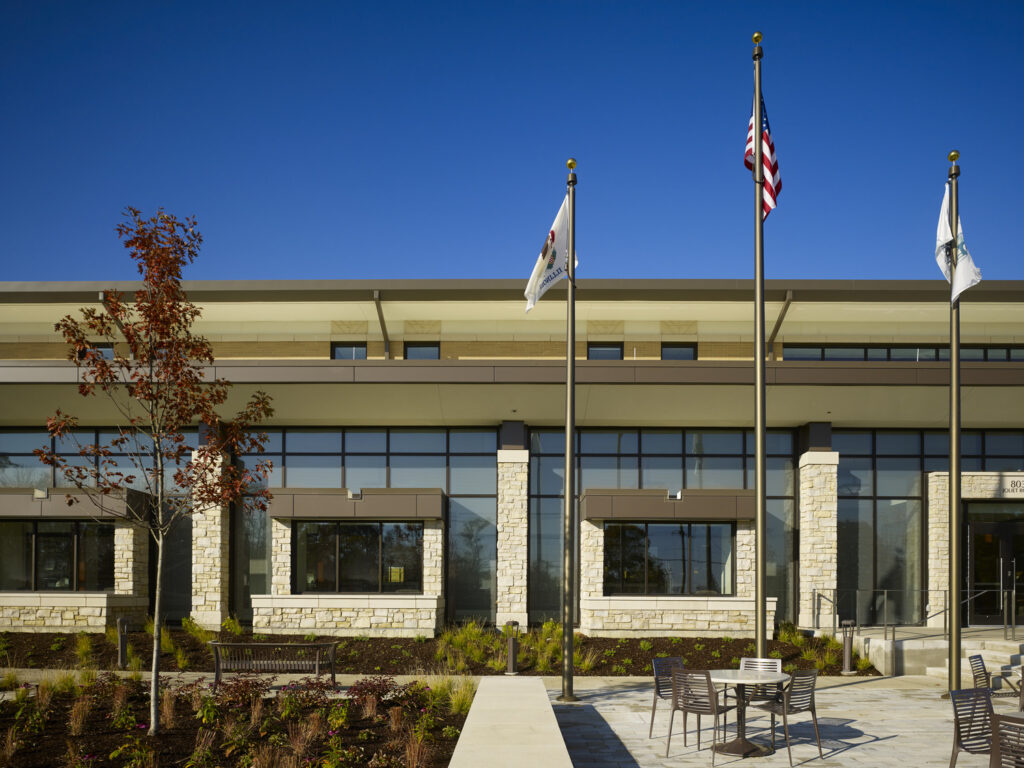
PROJECT LEADERSHIP AND STROY OF THE PROJECT
In 2017 the City of Countryside knew they had outgrown their facility for both city administration and police departments. Good customer service was difficult to achieve, and the safety of the police officers was compromised by the existing facility layout. At the same time, new economic development in the city had been progressing, and the city was seeking a catalyst for future development along historic Route 66 (Joliet Road). This led to the acquisition of the Flame restaurant, a popular restaurant from the 1950s to 1980s that served as a point of interest along Route 66 before people traveled thru to Chicago.
Construction of the facility started in 2018, with an early bid package that included the demolition of the Flame and site grading and utility work. This is where an interesting challenge arose: the discovery of contaminated soils from a leaking fuel tank that served as heating oil for the former restaurant. This changed the designation of the site to a brownfield site, which required remediation.
As construction began, design continued for the facility, and the energy models showed a low energy use intensity (EUI) as a result of the focus on designing a low energy consumption facility to maximize points for LEED® Silver certification. Later, the team would learn the project achieved LEED Gold. As a result of the energy modeling and discussions with the city, the team decided to pursue the Illinois Clean Energy Foundation Grant for Net-Zero Energy facilities. Photovoltaics were added to the design of the project, which served to protect the police vehicles from direct sunlight in the form of canopies and power the facility.
Construction was completed in October 2019. Today the facility is a place where the community can come for city and police services and to learn about sustainability and how they can implement strategies to save energy in their own buildings.
DESIGN PROCESS
As a public facility, including the stakeholder and the community throughout the design process, was important to make sure the plaza and all pathways to get to and inside the facility were accessible. The city and design team would host community discussions about the design and invite questions and design input. There was a focus on the sustainable aspects of the project and a bit of education about how different sustainable features work, such as the geothermal mechanical system and shading strategies to reduce direct sunlight heat gain. The community was also asked for feedback on the exterior design of the facility, which influenced the design of the public plaza on the east side of the site and the fence around the staff parking areas, as well as additional plantings as part of the landscape design along the areas of the site adjacent to the residences.
ENERGY SYSTEMS NARRATIVE
The city’s goal for the project was to achieve LEED Silver certification. The facility has exceeded the goal and achieved LEED Gold certification and continues its mission to inspire sustainable design and construction for future development projects in the city. The design focused on energy savings to achieve LEED Gold; as a result, the project had a low EUI of 26.1, and 638 photovoltaic panels were added through a grant to attempt to achieve Net-Zero Energy design.
Five-foot overhangs, ceramic frit glazing, geothermal mechanical system, and solar panels are used to design for energy savings. The overhangs of the roof shade the glazing from direct sunlight hitting the building and in the early mornings, while the ceramic frit on the east-facing façade blocks half of the direct sunlight from entering the lobby, which helps reduce the cooling load. The geothermal system is a low-energy design that uses the heatsink of the earth to heat and cool the building. The design team was able to include the high-efficiency geothermal design by being awarded a grant to support the more expensive mechanical system. The grant also helped to offset the costs of additional insulation in the walls and roof and the incorporation of photovoltaic panels.
The facility is also designed for an air infiltration rate of 0.2 cfm/ft2 of building surface area (vs. 0.4 cfm/ft2 code), which allowed for the mechanical systems to be sized smaller than typical facilities of the same size and type. The tighter air infiltration rate allows for less work by the mechanical system because the building is losing less heated or cooled air than a typical facility. Also, the smaller mechanical equipment means less energy used by the system and more energy savings for the facility.
The facility’s electrical system is beyond IECC-2015 compliant. With an interior lighting power density of 0.65 watts/sf and reduced exterior lighting, the lighting power is one-third of the maximum code allowable lighting power.
The City of Countryside Municipal Complex supports ecological health through night sky-compliant lighting and using plantings that are native to the region that does not require irrigation systems. The exterior lighting is controlled through motion sensors and will automatically dim and turn off if there is no motion detected in the parking lots, which is beneficial to energy savings.
The design supports water conservation. All faucet and toilet fixtures are electrically powered automatic, low-flow fixtures, which saves water usage and prevents faucets from continuously running. The city also wanted to provide water bottle filling stations and not allow the use of plastic bottles in the building, which has an impact on reducing pollution.
Stormwater is 100% mitigated onsite. The design has an intensive rooftop garden to benefit water filtration from the roof and provide wellness and respite areas to city and police staff. Stormwater from the parking lot runs to the retention pond with a slow release to an underground vault located under the public parking lot. The soil testing showed that this area of the site allowed for a high rate of water infiltration and suggested strategically locating the vault in this location. All the water that falls on the site is absorbed through the earth, on-site.
The design team also considered how the facility would serve the city and community for the next 50 years, choosing materials that would best support the facility’s longevity. The use of natural stone, wood, and terrazzo provides durability, beauty, and a lasting civic presence to the community.
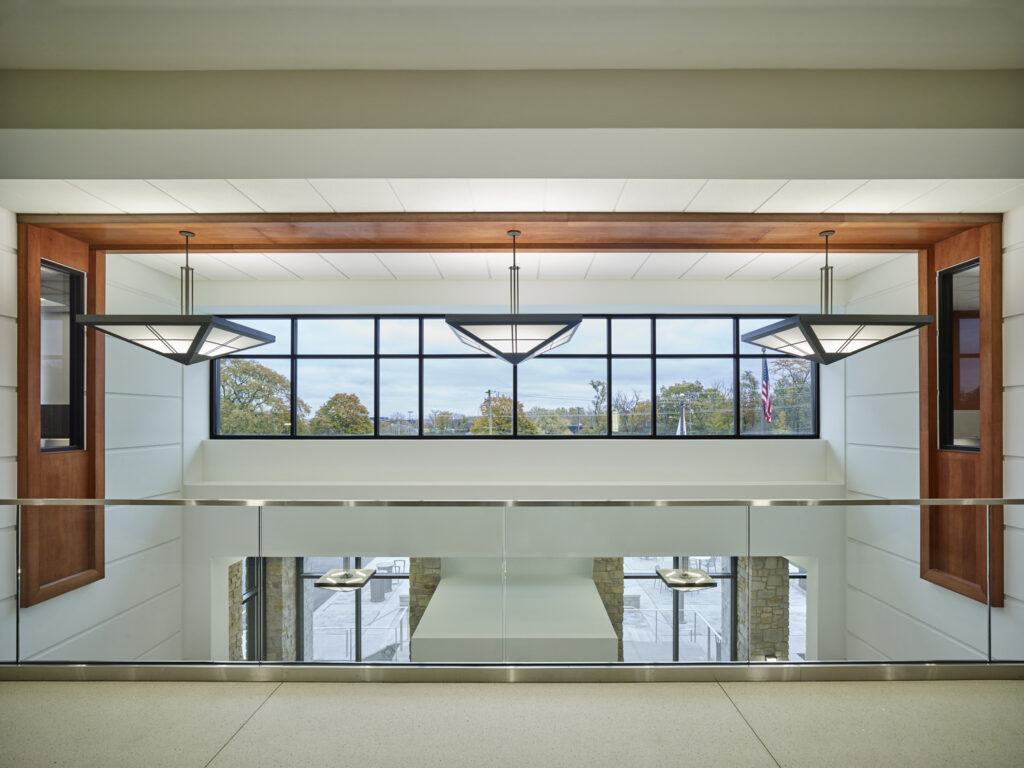
BUILDING COMMISSIONING, START-UP, AND OPTIMIZATION
During the design phase, Smith Seckman Reid Cx (SSRCx) performed design reviews of the DD level and CD level documents to confirm the mechanical, electrical, and plumbing (MEP) designs met the owners’ project requirements and followed the basis of the design set by the engineer of record. Multiple comments and recommendations were provided to the design team by SSRCx for review and consideration.
During the construction phase, the project equipment submittals were to confirm all equipment could be commissioned through functional testing. The building automation submittal was reviewed concurrently with the design team and the controls contractor to confirm all sequences of operation were correct and compatible with the equipment approved by the engineer. Site visits were performed by SSRCx on a regular basis to review construction progress and backcheck installations against design drawings and specifications. All issues uncovered were documented using web-based commissioning software and provided to the design team, construction team, and ownership for review, comment, and resolution.
The functional testing phase was executed at the completion of construction. MEP equipment, including the geothermal system and photovoltaic array, were tested against the sequence of operation written by the design team to confirm the equipment functioned as designed, including verification of safety features and alarms. The building automation system was thoroughly vetted during testing to confirm the state of operation of all equipment controlled or monitored by the system was accurately represented on the user interface. All issues uncovered were documented using CxAlloy commissioning software and provided to the design team, construction team, and ownership for review, comment, and resolution.
A total of 90 MEP issues were uncovered during the commissioning process and documented in the final commissioning report. The design team, construction team, and ownership worked together during the project to resolve the issues in a timely manner. LEED documentation was completed and submitted to the U.S. Green Building Council.
The commissioning process proved successful in confirming through review and testing that the owner received a facility efficiently functioning per design intent.
Though the building was designed and constructed to achieve high performance and net zero energy status, ongoing monitoring and commissioning of the building’s HVAC systems would be needed to ensure the intended energy savings persisted long-term. As a result, the City of Countryside contracted with the commissioning agent to provide 21 months of monitoring-based commissioning. They used a cloud-based automated fault detection and diagnostics (AFDD) platform that integrated energy system monitoring with near-real-time data from the building automation system, providing actionable feedback to facility managers. The AFDD platform parsed through daily trends for over 1,000 data points, and by applying algorithms for over 60 project-specific fault conditions, the commissioning agent was able to identify and diagnose the root cause for operational issues leading to potential energy waste, occupant discomfort, and faulty equipment operations. In collaboration with the facility manager, contractors, and design engineers, any identified issues were resolved so that the performance of the building met or exceeded the design intent for the building, including the achievement of net zero energy.
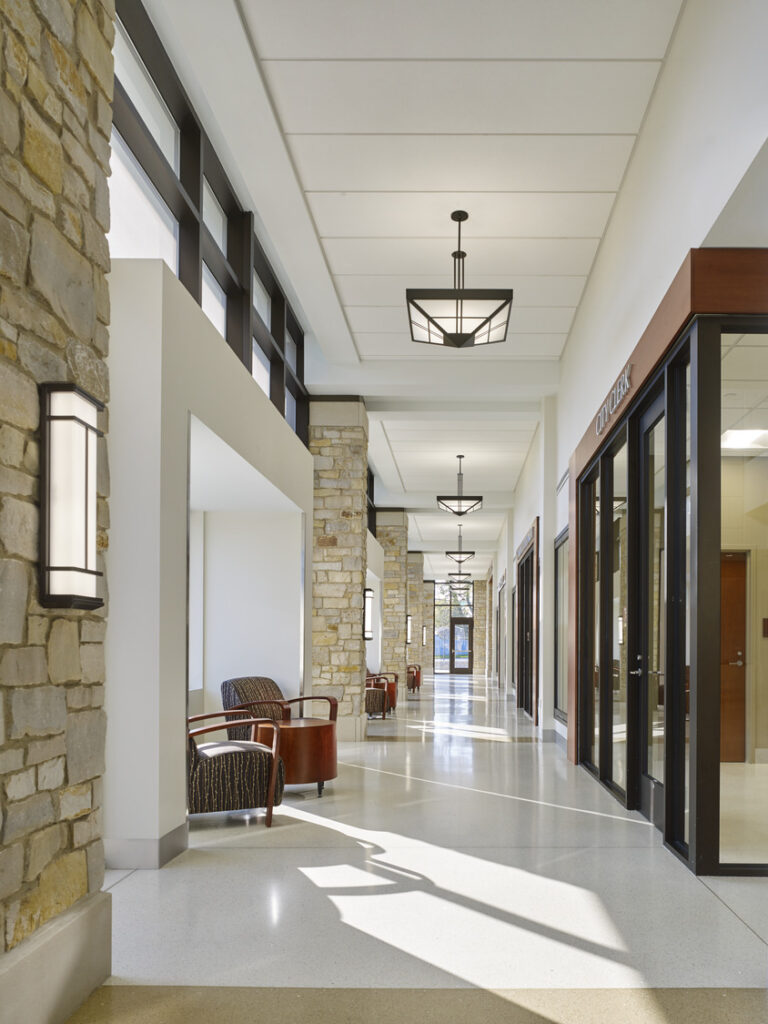
LESSONS LEARNED
LEED v4 Silver Certification was our first known challenge for the project design. The changes between LEED v3 and LEED v4 are significant and made the design team think critically about how to achieve the goal set by the City of Countryside. To achieve this goal, the design team, city, and police decided the best approach for receiving the most LEED points was to focus on energy savings, which also translated into design opportunities. The overhangs of the roof to shade the glazing, the ceramic frit on the glazing blocks direct solar heat gain in the mornings, the mechanical system choice of geothermal, and designing for as much natural light infiltration as possible into the facility to reduce reliance on artificial light, were all resulting impacts. These design decisions also made it possible to reach for NetZero Energy (NZE) design for the municipal complex.
With all the ins and outs of the design and the aspiration to achieve NZE design, it was important that the designers and contractors were on the same page when it came time to build the project. The city, construction manager, and architect agreed that the contractors should build full-scale mock-ups of challenging areas of construction before they were built at the actual facility. Each of the four mock-ups was fully enclosed and built with the intention of pressure testing to ensure that the contractors met the required specification of 0.2 cfm/ft2 air infiltration rate.
Designing the signage for educating visitors to the Municipal Complex on its sustainable features was a great opportunity and challenge. The challenge was how to make the sustainable design features of the building engaging and easy to understand by an eight-year-old. The design team created simple graphics that would convey the ideas of energy savings, geothermal systems, solar power generation, and water conservation, to name a few, and give short descriptions of how these features work and where they can see them in and around the building. We also incorporated interactive questions and facts and queried visitors on building facts in a way that was relatable, such as: how deep is a geothermal well? The answer is 450’ or the length of 18 buses.