The Class of 1966 Environmental Center on the campus of Williams College houses the Environmental Studies department and the Zilkha Center for Environmental Initiatives. The project began in 2013 when Williams College instituted its first Environmental Science majors and made the operational decision to co-locate the department with the college’s Center for Environmental Initiatives. The historic Kellogg House (1790s) needed renovations and an addition to serve its occupants well. The committee that formed to oversee the project asked for a LEED Platinum building or an equivalent. The Living Building Challenge became the goal when the Class of 1966 got involved and selected the project as its class gift. The building committee (consisting of faculty, staff and students, representing a range of college interests) shared conceptual visions and programmatic needs with the architects. At monthly meetings, the architects and other members of the design team shared the evolution of the design with the committee. This group made all major design decisions (i.e. the size of the offices; motion sensor or manually switched lights, composting or regular toilets).
VITAL STATS
Certification Status | Petal Certified |
Version of LBC | 2.1 |
Location | Williamstown, MA |
Typology | Building |
Project Area | 47,268 SF |
Start of Occupancy | April 2015 |
Owner Occupied | No |
Occupancy Type | College faculty, staff, students, visitors |
Number of Occupants | 13 FTE |
PROJECT TEAM
Owner | Williams College |
Owner Representative | Amy John, Director of the Zilkha Center for Environmental Initiates |
Project Direct/ Manager | Bruce Decoteau, Williams College |
Architect | Black River Design Architects |
Contractor | Consigli Construction Company |
Mechanical | Kohler & Lewis |
Electrical | DuBois & King |
Plumbing | Kohler & Lewis |
Lighting Design | DuBois & King |
Geotechnical | Guntlow & Associates |
Civil | Guntlow & Associates |
Landscape | Wagner Hodgson |
Structural | Novelli Engineering |
Interior Design | Black River Design Architects |
Specialty Consultants and Roles | Integrated Eco Strategy – Sustainability; Efficiency Vermont – Energy Modeler |
Key Subcontractor | Albert Cummings – carpentry |
PLACE PETAL
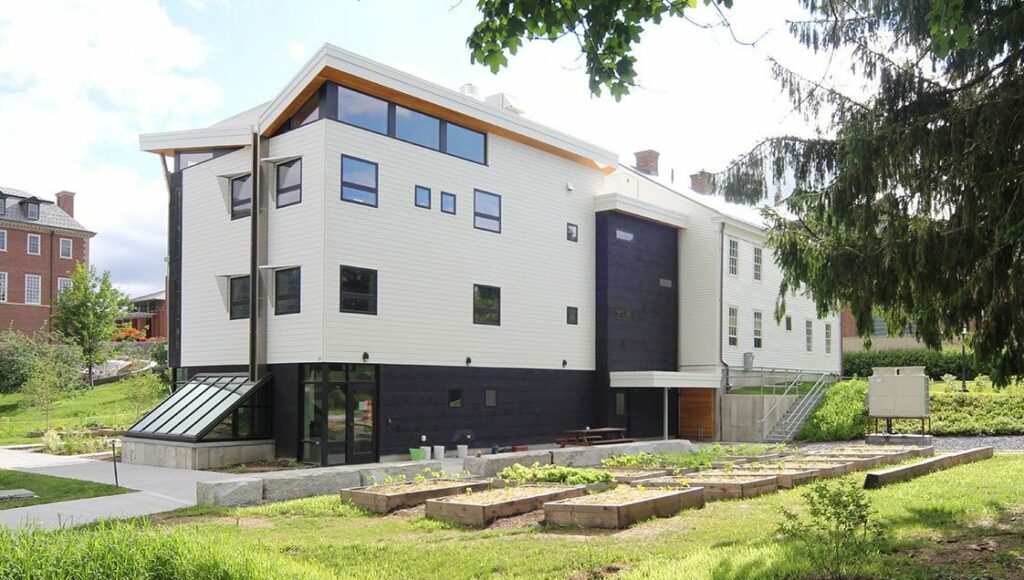
01. LIMITS TO GROWTH IMPERATIVE
The project site was previously developed. It is a portion of a campus that has been developed and redeveloped since the early 1900s. Immediately prior to this project, it was landscape consisting of sloped lawn. A building occupied a portion of the site in the years prior to the move of Kellogg House. The project site is in the center of the Williams College campus, adjacent to the library, academic buildings and dormitories. Beneath the soil surface there was infrastructure for water, communications and electricity conveyance for surrounding campus buildings. Three different landscape types were designed for the project: the Collegiate Landscape, the Agricultural Landscape and the Regenerative Landscape. The Collegiate Landscape is defined by the Upper Entry Courtyard and the Lower Patio Amphitheater. The Agricultural Landscape includes the Orchard, Berry Rows, Perennial Herbs & Vegetable Gardens and the Student Garden. The Regenerative Landscape includes the ponds and rain gardens, constructed wetland and meadow landscape. Each landscape type incorporates some level of agricultural practice, which is the main connective design element of the site.
02. URBAN AGRICULTURE IMPERATIVE
Thirty-five percent of the Class of 1966 Environmental Center’s site is devoted to food production. On site, organic agriculture is practiced to grow annual and perennial vegetables, high- and low-bush berries, herbs, and fruit trees. The pollinator garden attracts beneficial insects to the site. Seeds and starts are purchased from local nurseries, which helps to insure that they are regionally climate appropriate. High-bush and low-bush berries were purchased from Vermont- and Maine-based nurseries that focus on regional varietals. The harvesting of on-site produce is done largely by student gardeners and people passing by the site. In summer 2015, the student gardening group was interested in distributing the harvest to a wider swath of the college community. However, they did not anticipate such demand for the
harvest from students on campus using the building and possibly overestimated the amount of food that would come from the site in year 1. The harvest is used for widely-promoted campus events. The student gardeners regularly put out calls asking people to come and participate in the harvesting. Campus dining staff came at the end of the season to collect herbs to dry to be used in the dining halls. Longer-term, the project aims to contribute to the main dining services with fruit out of the orchard once the trees are substantially producing. The team recognizes that over the years, the plan will most likely change based on the individuals and groups who join this community-facilitated planning team as well as the changing needs of the college and surrounding communities.
03. HABITAT EXCHANGE IMPERATIVE
Williams College donated to support 2 acres of a 101-acre conservation easement managed by Vermont Land Trust.
04. CAR FREE LIVING IMPERATIVE
Prior to this project, the site contained a paved parking lot for 12 vehicles. The existing parking lot was removed and replaced with an organic garden. Six parking spaces associated with the project were reconstructed at the perimeter of the site. Handicap spaces were relocated along Mission Park Drive. Standard parking spaces were added to an existing surface lot. The campus master plan encourages density of development, mindful that not all employees work within walking distance of the site. This project contributes to a walkable community. Within 1⁄4 mile, many types of public and campus services are available.
WATER PETAL
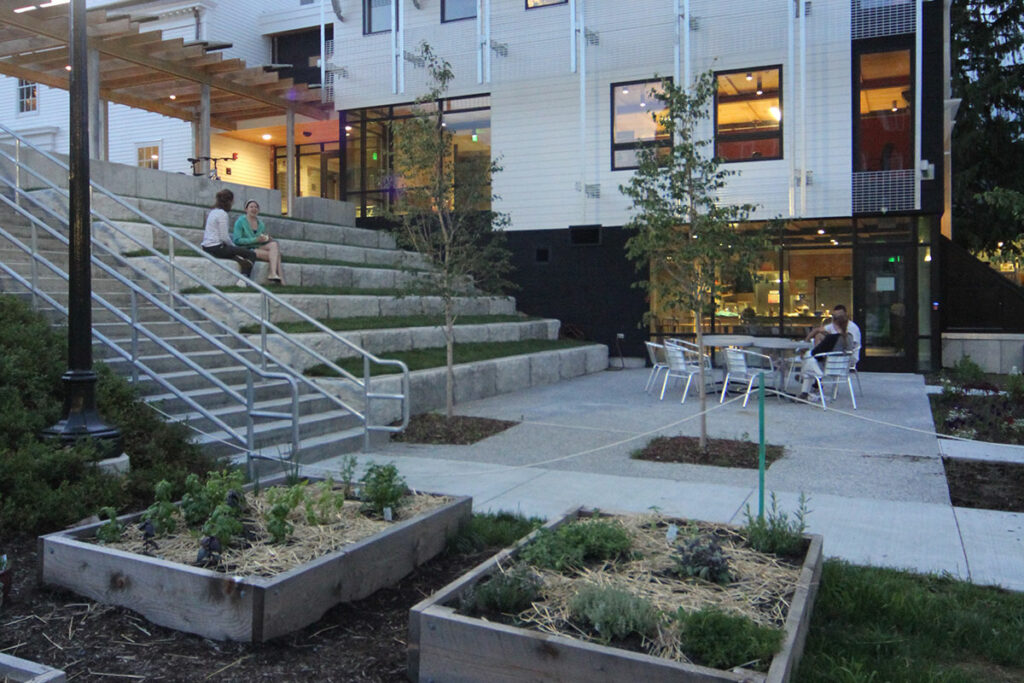
05. NET ZERO WATER IMPERATIVE
All on-site water is provided through rainwater capture. Water falling on the roof is diverted through a first-flush system and captured in a single 6,000-gallon underground cistern. Water is pumped from the cistern through fine cartridge and carbon cartridge filters, through UV disinfection and out to all interior fixtures and exterior hose bibs.
06. ECOLOGICAL WATER FLOW IMPERATIVE
Storm water: All rainwater that falls on site is either collected in the cistern for use or channeled to an engineered rain garden or a pond at the lower side of the site. Existing soil conditions do not allow complete infiltration through rain gardens, so they were planted with species chosen to maximize evapotranspiration. A solar irrigation station in the largest rain garden at the bottom of the drainage maximizes storage recharge between major storm events. No water leaves the site via pipes or stormwater infrastructure. This is an improvement over the pre-development condition.
Greywater is collected in a subsurface septic tank. From there, it is treated in a subsurface wetland treatment cell that was planted with native species for nutrient uptake. Outflow from this cell is continuously re-circulated back to through the wetland cell and through a vegetated sand filter. This planter-filter operates in an aerobic environment, opposite of the anaerobic wetland, to provide further reduction of contaminants. This continual process of sending effluent through aerobic and anoxic zones provides an increased level of BOD and Nitrogen reduction by bacterial and other processes. When the downhill sampling structure reaches capacity, overflow takes place by gravity to a subsurface leaching trench. The proposed effluent quality, prior to leaching trench, is intended to be less than 30 mg/l of BOD, 30 mg/l of TSS and 10 mg/l of Total Nitrogen.
Advocacy to enable land application of compost toilet products will continue. At present, Massachusetts DEP requires that this be discharged only at a municipal wastewater treatment facility.
REGULATORY APPEALS
Grey water: Massachusetts Department of Environmental Protection provided a pilot permit to allow this project to avoid use of the municipal water treatment facility and a typical Title V septic field. The combination of treatment wetland and leech trench will match or outperform either standard system in terms of water quality.
Potable water: Massachusetts Department of Environmental Protection allowed a chlorine-free public water supply which has become the model of potable water innovation in Massachusetts.
LESSONS LEARNED
State regulators required unexpected daily turbidity monitoring; vagueness over NSF vs EPA UV validation requirements led to early replacement of the UV disinfection system
HEALTH PETAL
During design, the goal of achieving the Materials Petal helped the team identify materials that would have less impact on worker health and occupant health, and eventually, the health of future workers occupying the building. During construction, the contractor followed an IAQ protocol to eliminate introduction of contaminants (source control, regular housekeeping, and site meetings with subcontractors to reiterate the goals of a clean job site) and intentionally staged work to reduce contamination of installed systems. The kitchen has significant ventilation with a commercial range hood. The photocopier has a direct connection to ERV exhaust. Foot-scraping grilles at each of the entrances reduce contaminants entering the building. The flooring material (polished densified concrete) does not absorb dirt, water or mildew. Wood floors can be cleaned easily and their finish is a low-VOC sealant.
08. CIVILIZED ENVIRONMENT IMPERATIVE
The Class of 1966 Environmental Center project was created in a scale that facilitated the goal of a civilized environment: the building depth allows all rooms to have a view and access to daylighting, as well as ventilation. In the new portion of Kellogg, the building was designed to provide optimum daylighting – tall south-facing windows with interior glass enable light to penetrate even into the north-facing offices. Curiously, in the historic half of the building, where the 200-year-old fenestration was retained, the daylighting is not far off from the ideal amount of opening as calculated in the daylighting studies and energy analysis. With every room having its own windows directly to the exterior, these are also very pleasant spaces. The proof is in the fact that this building attracts students even in non-class times. Even on weekends, students are found in sun-filled spaces. As is evident in the floor plans, all occupied rooms and spaces have operable windows and daylighting, as well as heat recovery ventilation.
09. HEALTHY AIR IMPERATIVE
This project’s approach to ventilation at points of concern (range, bathrooms, copier) is to ventilate at the source. The kitchen has interlocked ventilation (range hood) with dedicated make-up air (hood must operate for cooktop to work). The bathrooms are ventilated constantly through the composting toilets. There is ventilation at the copy machine tied into the ERV. Dirt track-in is addressed by the use of walk-off mats at all entrances to the building, including both indoor and outdoor mats at the main entrance.
09. BIOPHILIA IMPERATIVE
IDENTIFY NATURAL ASPECTS
The first and most important aspect of biophilic design is to include in the project site nature and natural elements that are meaningful. In this project, these include: vegetable garden, berry garden, orchard, herb garden, constructed wetlands, and retention ponds.
FOSTER CONNECTION TO THE NATURAL ELEMENTS
Beyond the general connections to the sky, the diurnal and seasonal cycles through natural daylighting, and pleasant views of campus trees and greenery afforded to all spaces in this building, specific connections to the immediate natural elements listed above are an important part of the design.
MAKE NATURAL BUILDING OPERATION SYSTEMS IN THE PROJECT VISIBLE
Where natural systems – net zero energy, net zero water, on site stormwater retention, constructed wetlands, water collection, water filtration – are an integral part of the operation of the building, as they are in a Living Building Challenge project, showing them off is an important goal.
USE NATURAL MATERIALS
Pushed by the Red List requirements for healthy building materials, the design team sought finish materials that have direct reference to nature.
INCORPORATE SYMBOLIC ELEMENTS
Where it is not possible to make direct connections to nature itself, provide symbols of the natural environment through use of organic forms and symbols, natural elements and materials.
MATERIALS PETAL
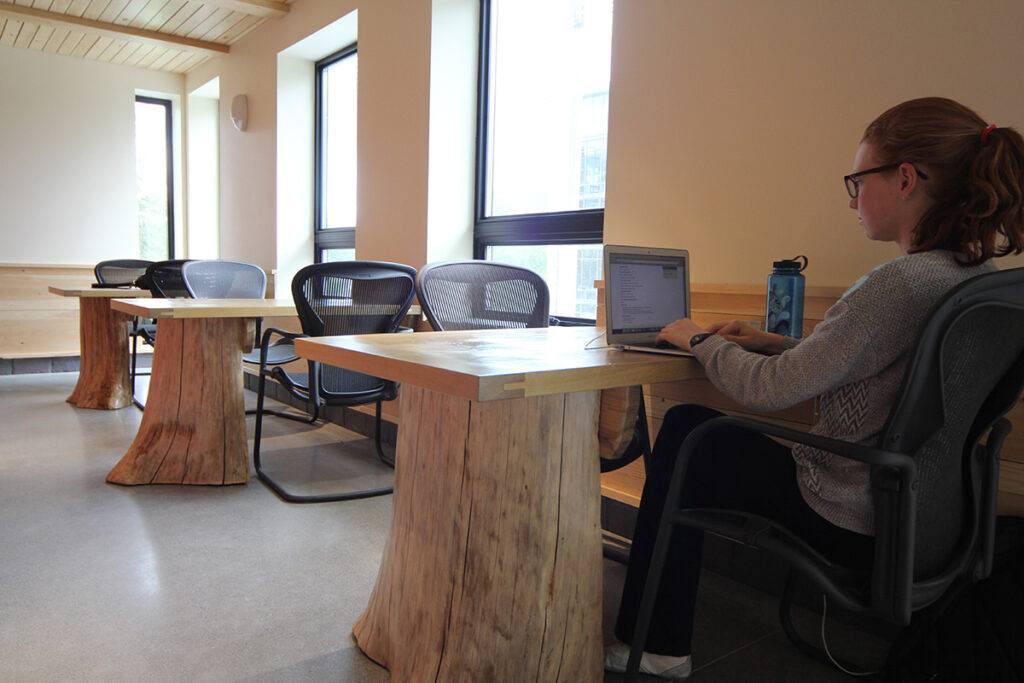
During early conceptual design meetings, the team discussed the impact materials would have on the project design and construction timeline, and the owner, architect, builder, and most MEP engineers were involved early on to discuss how materials criteria would be met. Items that were identified as being key to the design and function (including energy and water systems) were given an early review in order to avoid surprises when construction commenced. Life cycle cost analysis was performed for major mechanical components, with a preference for systems with long service life. The inclusion of the historic Kellogg House in this project conserved materials on a large scale, but also presented challenges with regard to adaptive reuse, and deconstruction and removal of non-historic portions of the building. The existing wooden floors in this building were sanded and refinished, and all of the major structural elements were maintained. Original windows were reused as storm windows, with custom-made, triple pane windows added to the interior. In the new addition, polished concrete floors were selected for durability and ease of maintenance, and a simple material palette was followed to reduce the number of materials that would need to be vetted. The building’s size was the subject of intense study, and the minimal footprint achieved the programmatic goals while reducing construction material costs, particularly when compared to business-as-usual design approaches on the rest of the campus.
Careful attention was paid to site-generated waste. The team researched the best options for waste handling early in the project timeline in order to identify sites that accept nearly all components for reuse or recycling (as opposed to landfill or incineration). In some cases, this required significant hauling distances, as municipal facilities for construction and demolition recycling are not available in Berkshire County. The plan calls for major components of the building envelope to be separable (without, for instance, large expanses of spray foam insulation). This will ensure that any future deconstruction will be a relatively straightforward task, and that most major structural components will not be contaminated with wet finishes that would limit their reuse potential. The design team also tried to identify products during the vetting process that have cradle-to-cradle or recycling potential. Electrical products presented a particular challenge to the project team, with the path for electrical product vetting less clear than the vetting process for products within other divisions. Working with those involved with lighting and electrical design, the project team found it took longer to identify companies that offered RoHS compliant small electrical components, and that many products within electrical and plumbing CSI divisions led to the use of I11-E3 Small Components. This required a considerable amount of data collection from manufacturers (and convincing manufacturers to break down their products).
11. RED LIST IMPERATIVE
As noted above, the electrical and plumbing divisions were challenging because they involve many complex products and obtaining a breakdown of component parts for these items, and material ingredients for each component, takes time. Often, the repeated queries would lead to a dead end (information wasn’t provided, or red list items were found and the manufacturer wasn’t able to make a substitution). Doing due diligence for complex products was necessary for a number of these products, due to either the presence of Red List ingredients, or the inability of a manufacturer to provide all the requested information. Exceptions for EPDM, PP, MDPE and the other plastic polymers outlined on page 6 of the Materials Petal Handbook (May 2013) were used extensively, especially within the divisions for site work, utilities, electrical and lighting. Due to the need to purify water to EPA and MA DEP standards for public water supplies, the team had few choices for products, and most of these contained Red List items (UV lamps, PVC end caps in filter media, PVC coated power supply cords for wet locations, etc.) so the performance/code exceptions were applied. When the vetting team understood what elements of products were subject to RoHS compliance, this was a huge help, as there are a growing number of electrical manufacturers that are able to supply RoHS certificates. However, there are a larger number of manufacturers who need circuit boards, switches, etc. that change suppliers often, and they, and their suppliers, don’t have this information to share. PVC in lighting was ubiquitous as UL Listed power cords are almost always coated in PVC. Many times when there were cords, the fixture was also considered “complex”, so the team was often able to apply I11-E3 Small Components. Zone jumps for performance reasons were also key, especially for systems related to energy and water (heat pumps and rainwater filters in particular). Another challenge was sourcing FSC structural timbers while also ensuring no added formaldehydes. For paints, coatings, and adhesives the team made use of I11-E15 Proprietary Ingredients, as no manufacturer was willing to fully disclose the ingredients of their product. At the onset of the project, Declare lacked a number of critical items, but the expansion of manufacturers and products in Declare in recent years should help future projects considerably.
12. EMBODIED CARBON FOOTPRINT IMPERATIVE
The team used the Athena EcoCalculator to estimate the embodied carbon of the building. Williams College has offset 600 tonnes for this project.
EMBODIED CARBON FOOTPRINT (TCO2e) – 520 metric tonnes
AMOUNT OFFSET – 600 metric tonnes
PROVIDER – Carbonfund.org
CARBON CALCULATOR – Athena EcoCalculator
13. RESPONSIBLE INDUSTRY IMPERATIVE
Appropriate sourcing drove the approach to rock, stone and metals. The team created an advocacy letter for the various trade associations, including regional ones and ASTM International, that were sent upon completion of the project. The specifications required FSC wood for all applications: pure if possible, and mixed if FSC pure wood could not be obtained. Due diligence was required for all wood sourcing. Working with local quarries and mills to source stone and wood was rewarding, as these entities were most interested in why the team was pursuing a project with such stringent material standards, and were motivated to provide what was needed. All purchased wood products came either from a nearby FSC-COC sawmill or from one of 2 local FSC-COC lumberyards. White Pine, Spruce and Black Locust were also harvested from the site.
WOOD SOURCES Forest Stewardship Council (FSC) Certified wood, Wood harvested on site
NOTABLE MANUFACTURERS OF FSC CERTIFIED WOOD PRODUCTS Hall Tavern Farm (Shelburne, MA), FD Steritt Lumber (Watertown, MA), Feldman Lumber (Brooklyn, NY)
TIMBER HARVEST/LUMBER SEASONING PROCESS Hall Tavern Farm, Lou Zelazo
NOTABLE BROKERS OF SALVAGED MATERIALS Landscape granite – Olde New England Granite (Wakefield, MA)
14. APPROPRIATE SOURCING IMPERATIVE
If Asia was within the appropriate zone for the east coast project, the team would have had fewer challenges in lighting, electrical and HVAC, as many of these products contain source material from that region and/or are manufactured in Asia. Exit signs, heat pumps, and ERVs are just some examples of products from this region. Germany also falls outside of this project’s Zone 5, and this is where many high efficiency electrical meters and thermally advanced window assemblies are manufactured. The team found I14-E6 Miscellaneous Hardware and Accessory Products to be an important tool here because of the sheer quantity of products that fall in this category. I14-E13 Function was equally important, as many of the systems were unique and few options existed (water collection/filtration and Energy recovery units). Some metals presented a challenge because New England no longer has any active foundries, and most metal fabrication falls beyond the project’s Zone 2 (for structural metals, in particular). The team had to work with manufacturers to identify which plants could fabricate parts within the required zone and had to ensure the contractor requested the correct location. Drywall also presented a challenge when attempting to source Red List free materials within the appropriate zone. The “75%” rule was appreciated for many complex assemblies, such as electrical panels and curtain walls, as it wasn’t possible for all components to meet the sourcing criteria. Documenting percentages led to the aforementioned challenge of getting a manufacturer to break down the product by weight/material/and source location.
NOTABLE REGIONAL PRODUCTS Slate – Vermont Structural Slate Co. (Poultney, VT)
15. CONSERVATION + REUSE IMPERATIVE
In the planning phase, conservation of resources focused on reuse of the historic Kellogg house. The building design process focused on minimizing building area, reducing the need for material and energy. Where possible (in offices, for instance) spaces support typical functions in 25-40% less floor area than comparable campus buildings. During construction, the team paid attention to the hauling of construction debris and waste from the site (though the hauler required more oversight than they had hoped). Now in the operation phase, the building takes advantage of the College’s standard recycling program, which collects recyclable material from every campus building once or twice per week. Occupants and custodians are well familiar with this practice from other campus buildings. Food scraps are composted on site and used in the garden. It is expected that the building will serve the College’s needs for more than a century.
SALVAGED MATERIALS
In addition to the reuse of historic Kellogg House, several salvaged items were incorporated in the design. Most significantly, landscape granite was salvaged from coastal railroad trestles. On the wooden stair, handrails are salvaged. Salvaged shutters were used to supplement those that could be reused from the historic house.
INNOVATIONS
IES drew from the experience of vetting products for this project and developed a task-oriented database to speed material vetting and streamline documentation of material compliance. We hope that this software tool will become the standard for all LBC projects.
EQUITY PETAL
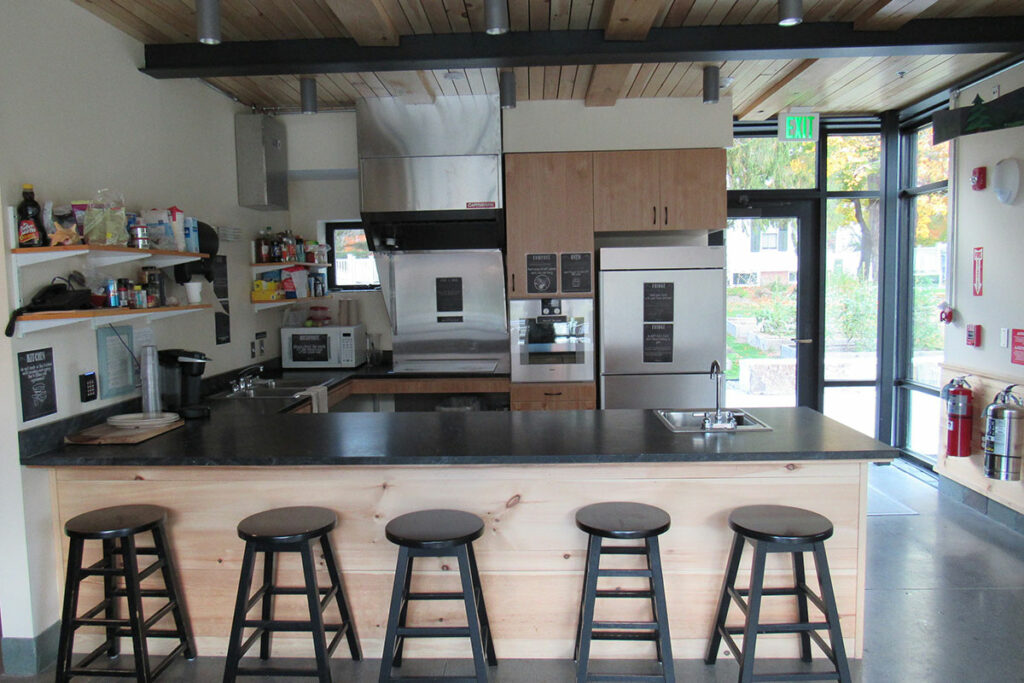
16. HUMAN SCALE + HUMANE PLACES IMPERATIVE
Exterior rooms and their connection to interior spaces are an important component of the design of this project. The design team welcomes the metric of success once stated by a late president as “voting with your feet.” They consider the ability of this project to attract and engage people from the larger college community as a measure of project success, and have created human scaled spaces both immediately outside the building and inside the building. The emphasis on framed living rooms, the outdoor classroom, and amphitheater is not accidental. These spaces must be carefully designed and furnished to attract people and promote interaction.
Activity in and around the building is encouraged by the incorporation of interesting functions. In this project, occupants and participants are part of the program: gardening, harvesting food and enjoying food prepared on site.
“We are fortunate to have a building program with such exciting social and educational activities already part of the curriculum.”
17. DEMOCRACY AND SOCIAL JUSTICE IMPERATIVE
All members of the Williams College community will be able to appreciate, explore and use this building and its surrounding habitable spaces and functional gardens.
The design team has defined success as the “ability to engage and attract people to this project.” It began with creating a south facing outdoor area that is warm and inviting in the cooler months and provides shade in the summer; informal sitting areas of different types, all exposed to passersby along a major pedestrian path through campus; and the uniqueness of the landscape that includes both an abundance of solar panels, food gardens, water features and walking paths. By opening up the building to the public functions within, the hope is that people are drawn inside.
The concern is that success defined by the popularity of the building creates challenges in relation to the energy budget and achieving net zero. This dilemma invites a discussion about which metric of success we wish to use: energy use per occupant or energy use per square foot.
18. RIGHTS TO NATURE IMPERATIVE
The only adjacent building that is affected by shading from the Kellogg House is Goodrich House, located to the north-northeast of the site. Solar path analysis confirms that at 10am on the winter solstice, shadows do not hit the Goodrich House. At 2pm, shadows shade the building by less than 8ft.
Other site elements to the north of the building (particularly ground-mounted solar arrays) are not taller than 6 meters, ensuring that they cast shadows no higher on adjacent facades.
This project is designed to have no features or program elements that contain Red List chemicals. The tanks related to the treatment wetland have ventilation stacks. No odors have emanated from these devices, and none are expected, since only greywater with low nutrient loads are present in the system.
BEAUTY + INSPIRATIONPETAL
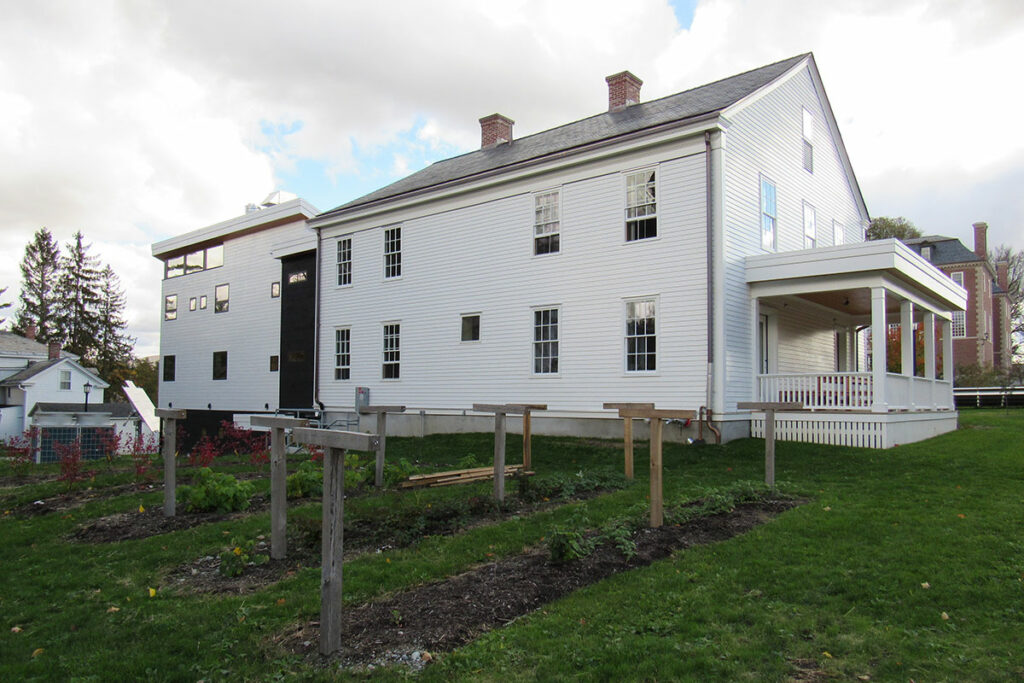
19. BEAUTY + SPIRIT IMPERATIVE
A NOTE FROM THE TEAM
As Architects, we fancy ourselves as the members of the team that are the defenders of beauty and design, in the face of the seemingly unending onslaught of needed but unattractive mechanical equipment (outside condensers, rain collection systems, interior heating elements, electrical gadgets, fire alarm pull stations, electrical and fire alarm panels, security systems, wifi routers, thermostats, and light switches). Add to this solar panels and their supporting racks and framework, and building signage, and one can understand how difficult it is to achieve elegance, simplicity, and beauty. Exposing the systems added to the general challenge of making our projects beautiful and attractive (in the literal sense of the word – after all, our building is not just an object, but an Environmental Center at a liberal arts college, where they are trying to expand their environmental programs by attracting people to the place), but we are also faced with the new and interesting challenge of showing off some of the systems that are unique to this Living Building Challenge building. It is often said that beauty is in the eyes of the beholder, which makes it difficult to define what constitutes beauty. With constant pressure to create something which is new, fresh and the latest fashion, it is difficult to determine a universal description of beauty. For this reason, the International Living Futures Institute’s endorsement of beauty and its attempts to define and identify those aspects of beauty that impact humans in a positive way is a worthy effort. By reinforcing the scientific connection between beauty and its positive impact on human spirit, work production, and the ability to learn, the pursuit of beauty is more rational and understandable in its purpose. Here follows our efforts in pursuit of creating a project, which, along with its biophilic elements, creates uplifting and attractive spaces for humans to inhabit (not just observe from afar).
HISTORIC PRESERVATION – THE RIGHT SPIRIT
We believe this project is one of the first LBC projects to involve an historic structure. This brings unique challenges, but buildings that are old and unique statements of their own time are almost universally considered beautiful, or are revered and appreciated. They also represent a healthy spirit of connection to the past, as well as serve as the best example of recycling, rather than throwing buildings away and building new
20. INSPIRATION + EDUCATION IMPERATIVE
Directed by the Zilkha Center for Environmental Initiatives, there has been strong student involvement in communicating valuable educational and inspirational messages. The building is used in class curriculum and special studies. A student wrote and designed the self-guided tour brochure, and students are involved in the open-house building tours.
These are the survey questions for the building occupants:
- What are your favorite and least favorite things about this building?
- Does this building look or feel different from other campus buildings? If yes: what looks/feels different?
- On a scale of 1-5, could you rank these aspects of the building: Your General Comfort while in the building Aesthetically Pleasing Light Quality Air Quality
- This building was designed to elevate and lift your spirit, the underlying concept being that beautiful built environments are a necessary precursor to getting people to care about preserving and conserving our environment. In your opinion, has it succeeded in a way other campus buildings have not?
- Are you aware that this building is pursuing Living Building Challenge certification, and what that means?
- When you are on this building site, do you use energy, water, paper, food differently or the same as you do in other buildings? Please explain
PROJECT WEBSITE: http://env-center.williams.edu