Epsten Group, Inc.
Vital Stats
Certification Status | Petal Certified |
Version of LBC | 3.1 * |
Location | Atlanta, Georgia, USA |
Project Area | 7,400 square feet |
Start of Occupancy | July 17, 2019 |
Owner Occupied | Partial |
Number of Occupants | 40 |
* The project was registered under LBC 3.1, but when 4.0 was released, the team opted to pursue the requirements of the 4.0 version of the Materials Petal. Because the Petal certification structure and remaining Petals correspond to the 3.1 version of the Living Building Challenge, though the requirements of the 4.0 Materials Petal were met, the certification is considered to be under 3.1.
Project Team
Owner | The Epsten Group, Inc. |
Project Manager | Uma Patwardhan |
Architect | The Epsten Group, Inc. |
Contractor | Dilweg Co. LLC |
Mechanical Engineer | Covalent Consulting, LLC |
Electrical Engineer | Covalent Consulting, LLC |
Plumbing | Covalent Consulting, LLC |
Lighting Design | The Epsten Group, Inc. |
Interior Designer | The Epsten Group, Inc. |
Place Petal
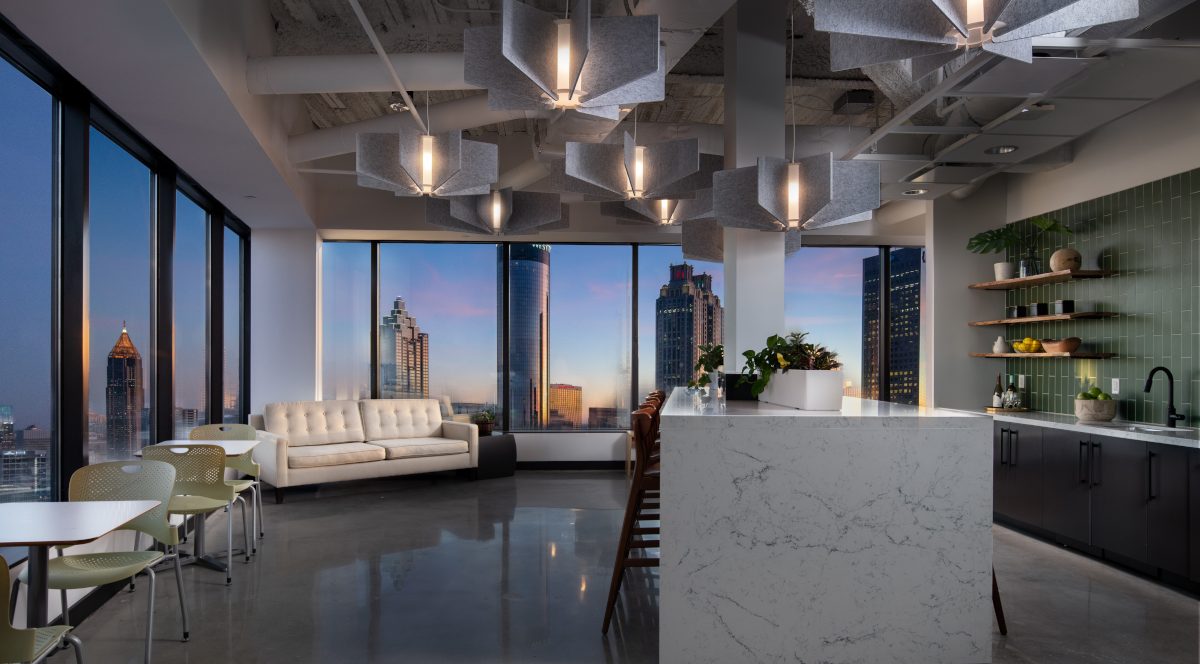
01. Limits to Growth Imperative
Epsten Group chose an existing high-rise building in downtown Atlanta, GA (Centennial Tower, built in 1975) to house its new headquarters. The site was selected in part due to its proximity to existing infrastructure and public transportation. The office space occupies a portion of the 26th floor of the building, and pursued certification under the Renovation Typology. No alterations were made or allowed to the existing building structure or site, therefore, landscape requirements were not applicable to the project.
Materials Petal
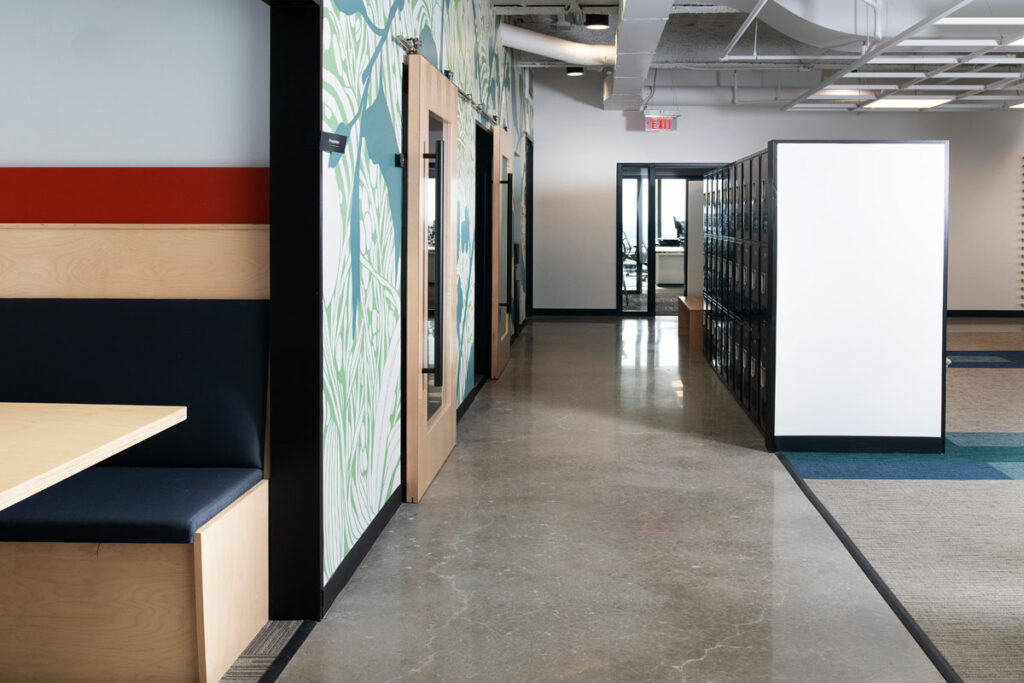
11. Embodied Carbon Imperative
For the Materials Petal, Epsten Group chose to pursue compliance using the LBC 4.0 requirements. Because the team was not pursuing the Energy Petal, which contains the embodied carbon requirements under 4.0, they were required to comply with v 3.1 I11 Embodied Carbon.
Not only is the embodied carbon of the project reduced by virtue of its being undertaken within an existing structure, the team achieved reductions for the materials within scope (studs, gypsum board, insulation, paint), by improved material selection, prioritization of local vendors to reduce the transportation distance, and selection of higher recycled content products than the industry average. The offset calculation was carried out with One Click LCA software and Green-e Climate Certified offsets were purchased through Carbon Solutions Group.
13. Red List Imperative
Epsten Group’s in-house design worked closely with their consulting teams throughout the conceptual and design phases. We set a hierarchy to follow for material election: Living Product Challenge products, then Red List-Free Declare Label products, then LBC Compliant Declare Label products, then Declare Label products without Red List verifications, then products that met the Building Product Disclosure and Optimization requirements (LEED v4.0). Where it was not economically or logistically feasible to select our most preferred products, we researched comparable products and reached out to manufacturers asking for documentation confirming that the products were Red List-free. We also sent the manufacturers information about the Declare program and encouraged them to pursue the transparency label. Lastly, there were some products that included Red List materials that had to be specified for the project due to an overall lack of viable alternates in the marketplace. We used previously established exceptions for these cases, while at the same time providing additional manufacturers information on why they should try to eliminate the Red List ingredients from their products. In multiple instances, we utilized the vast ILFI network for guidance.
During construction, while the selected contractor did not have experience focusing on sustainability and healthy materials, his small local team and eagerness to learn made the job fairly easy to manage from a construction administration perspective. From the beginning, the LBC Red List requirements were made clear to the contractor and his subs, and our team provided additional education, direction, and clarification whenever needed.
14. Responsible Sourcing Imperative
All of the wood used in the project is FSC certified and we used several products that had Declare labels, to support the transparent labeling of products. For the products that did not have a Declare label, or for which manufacturers were not willing to disclose 100% of ingredients, we advocated regarding the need and benefits of material transparency.
15. Living Economy Sourcing Imperative
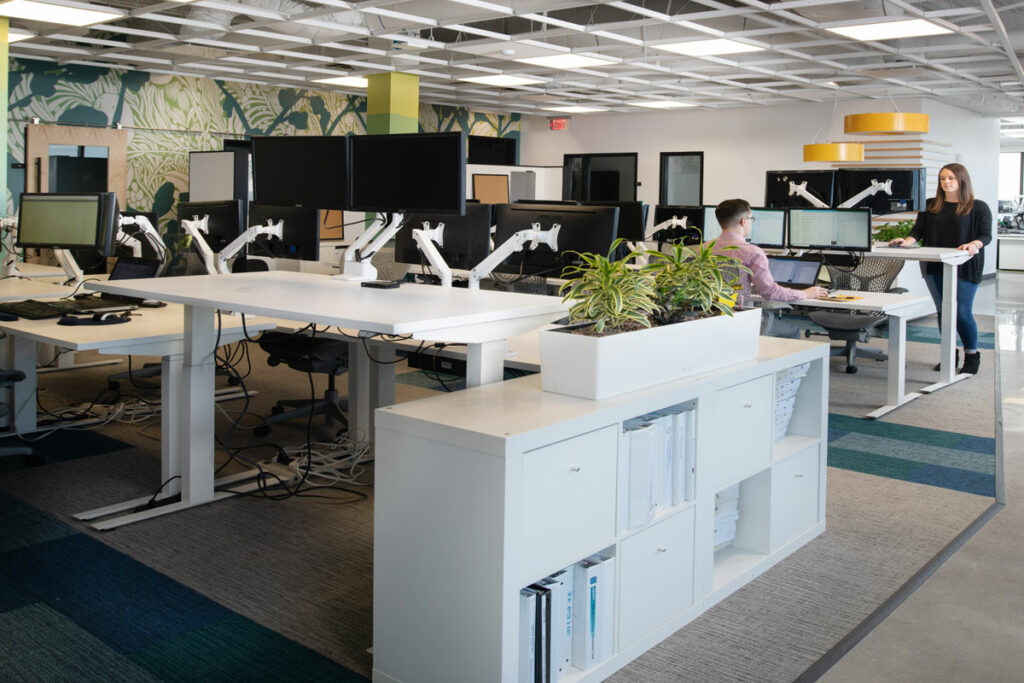
Our aim was to reduce our footprint by supporting local businesses, whenever possible, and minimizing transportation impacts. Balancing this with responsible sourcing, materials transparency, and non-toxic materials was our main focus for this interior renovation project. We challenged ourselves to find most of the products within 500 kms and achieved that by identifying the big ticket items that could meet the requirements of other Materials Imperatives as well. This helped us connect with local manufacturers and contribute to local economy while educating them about various green building and sustainability initiatives, including Living Building Challenge.
16. Net Positive Waste
Prior to construction, a Material Conservation Management Plan was developed, and the general contractor was educated about the intent and requirement of this imperative. We indicated to the contractor that our aim was to eliminate waste generated during construction by means of either integrating the waste back into the industrial loop or working closely with the local recycling hauler to collect the leftover material. Local recycling haulers were engaged to collect the onsite separated waste materials such as metals, wood, drywall, and acoustic ceiling tiles. Due to proper training given to the contractor, the materials were separated accurately on site and we were able to achieve almost 100% diversion rates. The contractor maintained the waste materials log diligently.
In addition, we both used tables and chairs from our previous office space and sought manufacturers of systems furniture that have take-back programs for the cardboard packing used to deliver the furniture.
Equity Petal
As a Renovation, the project was not subject to the requirements of either I15 Human Scale and Humane Places or I16 Universal Access to Nature and Place.
17. Equitable Investments Imperative
Epsten Group made contributions to a variety of organizations to meet the donation requirement of Equitable Investments.
As long-time supporters of Zoo Atlanta, we make a yearly contribution during its fundraiser event. We have completed multiple projects for the zoo, and appreciate that the money raised during the event goes to the animal keepers and to support the animals with whom we have built a relationship during this time.
The Garrison Institute is a non-profit organization that invites people from across the globe to visit their center where they offer free classes that focus on health and wellness. We became acquainted with the Institute through the WELL Summit that took place in 2019.
Peter Lyon, a former employee of Epsten Group, passed away in 2019 from cancer. In his honor, we contributed to the Dana-Farber Cancer Institute that was created to support cancer research and patient care.
Georgia Parent Support Network, Inc. is a local institute takes furniture and refurbishes (or uses it in their facilities) it to sell to help fund their youth programs. As a part of our move, we donated some of our furniture.
18. Just Organizations Imperative
The Epsten Group is a Just organization and advocated to project partners to participate in the Just Organizations program.
Beauty Petal
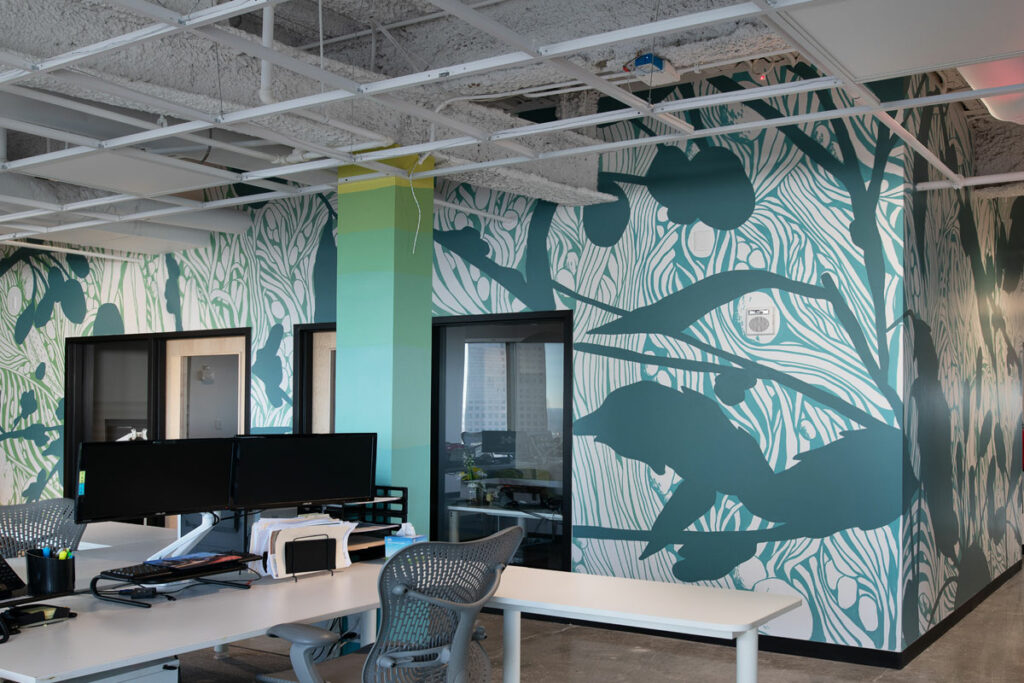
19. Beauty and Spirit Imperative
Epsten Group originated in Atlanta’s Old 4th Ward neighborhood and when we chose to move downtown into an office tower, we hoped to retain some of the neighborhood feel. We divided the firm’s departments into “neighborhoods” and created a breakroom that provides a calming, central gathering area for all employees.
The space makes extensive use of bright colors, inspired by 1950s and 60s Knoll modular offices, meant to evoke nature, specifically, grass, flowers, and water. Many natural wood elements were included to ensure that our space offers biophilic details that help nurture the mind, and remind both employees and visitors that Atlanta is truly a city amongst the trees. These elements include maple wall slats and natural edge shelving. The natural edge shelving is made of reclaimed 100-year old red oak that was preserved for use on this project. Minimal finishing was done to the slabs to ensure that the natural hues were preserved. The shelving is integrated into the kitchenette and breakroom areas. When an occupant is taking a break, he/she will have views of the Atlanta downtown, distant landscapes, reclaimed materials, interior plant life, and natural felt lighting fixtures. The project also includes multiple workstation types to ensure that workers have options to suit their individual needs and preferences.
The most impressive element included for human delight is our mural from the renowned artist Tellas of Sardinia, Italy, which includes natural elements from his own childhood growing up in Italy overlaid with shadows of native plant life in our region. The multiple colors and expansive mural provide a sense of place for the occupants, as the old headquarter office was in an area of the city that features multiple murals on almost every corner.
The completed mural brought a vibrant energy and completely transformed the feel of the space. The intersection of the mural, office neighborhoods, wood elements, and multi-use space types create a work place that celebrates the culture of the Epsten Group and Atlanta area, the spirit of the workers and the future of the company, and a company that has been invested in the local community for the past 30 years.
By engaging with the female-run organization Living Walls, we were able to bring Tellas to the United States and offer him his first chance at including his own handprint and artwork in a city that loves its murals. As a part of his collaboration with us, we were also able to help coordinate another piece of his artwork being featured in a blighted neighborhood elsewhere in Atlanta (Summerhill).
20. Inspiration and Education Imperative
At Epsten Group, we pride ourselves on being a pioneer for sustainability in the built environment. With the design of our new headquarters, we set an ambitious goal to achieve Living Building Challenge Materials Petal certification (in addition to LEED, WELL, RESET Air, and Fitwel). The Materials Petal certification challenged us to push the envelope with our selected building materials, building systems, and firm operations, in addition to creating an interesting and beautiful workplace. Naturally, after the project was complete and the space occupied, the Owners decided to showcase the success of the project by educating and inspiring people via an Open house day, informative signage installed throughout the office space, and through the firm’s website. The aim was to show that with early planning and conviction, even a medium size office space can provide a sustainable and mindful environment for its occupants. Hopefully, we inspired people to think “out of the box” to create interesting spaces without compromising on selection of Red List-free materials and overall functionality of the space.