VITAL STATS
Certification Status | Living Certified |
Version of LBC | 3.1 |
Location | Williamstown, MA, USA |
Gross Building Area | 12,875 SF |
Start of Occupancy | February 2021 |
Number of Occupants | 13 |
TEAM ROSTER
Owner | Williams College |
Architect | Mesick Cohen Wilson Baker Architects |
General Contractor | A/Z Corportation |
MEP Engineer | Quantum Engineering Co. P.C. |
Structural Engineer | Spring Line Design |
Interior Designer | Mesick Cohen Wilson Baker Architects |
Building Science- Envelope | Camroden Associates |
Civil Engineer | Guntlow and Associates |
Landscape | JSR & Associates |
Green Building Consultant | Sustainable Design Consulting, LLC |
Commissioning Agent | MH Professional Engineering, PLLC |
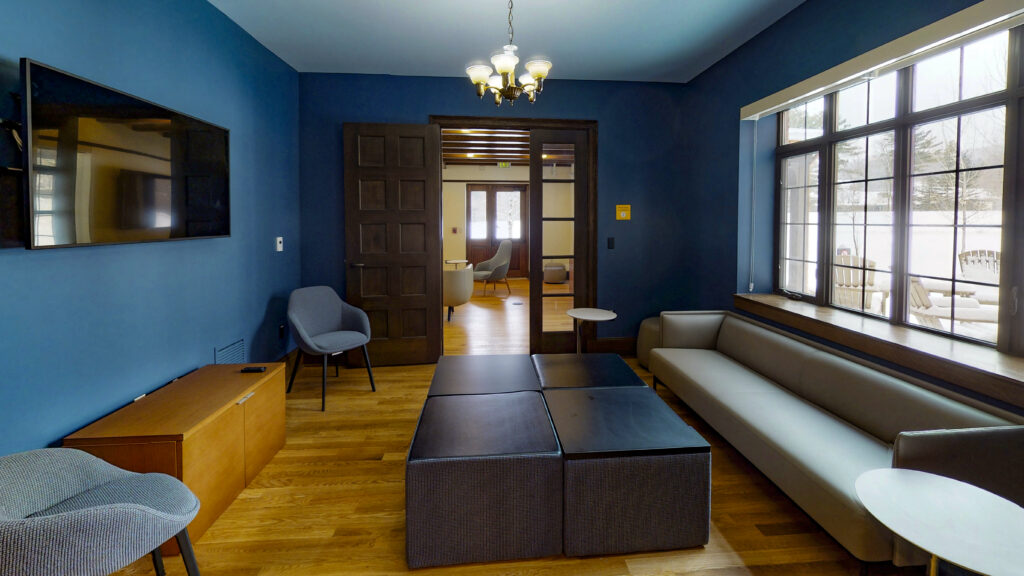
PLACE PETAL
01. LIMITS TO GROWTH IMPERATIVE
Fort Bradshaw was originally built in 1931. Ownership of the building was transferred to Williams College, and it now serves as a residence to 13 students in the Williams College Graduate Program in the History of Art. The project is located on previously developed land and is renovating an existing structure, which reduces the harmful impacts to the site and surrounding environment. Fort Bradshaw is located 0.5 miles from the Williams College campus, allowing for easy bicycle access. The project will provide 8 interior secure bicycle storage spaces and 10 exterior spaces for its residents and visitors to encourage the use of bicycle transportation.
More than 30% of the project site area is open space, with over 66% of the open space being restored to native vegetation. This vegetation is in line with the neighboring Clark Museum creating a larger expanse of a native meadow than with the site alone. The project provides wildlife and avian habitat that is appropriate to the project’s location with the use of native plants and topsoil. The plant species selected for the site are native to the New England Acadia Forest Ecoregion and include boxwoods, hydrangeas, maples, and magnolias. The project reduces light pollution by adhering to the Backlight Uplight Glare (BUG) ratings for the project’s lighting zone.
HEALTH AND HAPPINESS PETAL
I07. CIVILIZED ENVIRONMENT
Operable windows are included in every room to provide occupants with access to fresh air and daylight.
I08. HEALTHY INTERIOR ENVIRONMENT IMPERATIVE
Smoking is prohibited on the Williams College campus per the school policy. No-smoking signs are placed to ensure occupants are aware of the college policy.
To preserve the architectural character of the building by not altering the brick entrance façade, the project team created an entry approach that reduces particulates from being brought into the building. The existing covered entry was enclosed and converted into a vestibule with a walk‐off mat extending 6 feet in the direction of travel. A new door set back into the building allows for the additional length in the vestibule required by ADA. Inside the foyer, an additional walk‐off mat, 4 feet in length, which results in a total of 10 feet, reduces particulates while preserving the arch entryway.
In addition to the entryway strategies, Williams College has a standard green cleaning
program that specifies the use of cleaning products that comply with the EPA Safer Choice label.
Additionally, interior building products with the potential to emit VOCs have been tested for
compliance with the California Department of Public Health (CDPH) Standard Method
v1.1-2010. All information collected on products, and all attempts to contact manufacturers,
were cataloged by materials researchers in the Red2Green software. Each product reviewed
was coded with a unique identifier, an LBC ID, to enable tracking during the construction
submittal phase. MCWB Architects, Sustainable Design Consulting, A/Z Construction and
Quantum Engineering had full access to Red2Green and worked directly in the software with
IES to ensure pertinent information was communicated appropriately. Products were
assigned to researchers after being added to Red2Green and all information regarding VOC
content and emissions. Product sourcing was tracked and reviewed for accuracy by a team of
quality assurance specialists. Researchers reviewed the information, collected supporting
documentation, and made final determinations on the products’ Healthy Interior Environment
status and exceptions.
Indoor Air Quality testing passed the required thresholds prior to occupancy. An additional test will
be performed 9 months after occupancy. Ongoing testing will become part of the
building operation.
I09. BIOPHILIC ENVIRONMENT IMPERATIVE
Biophilic Design is the deliberate attempt to translate an understanding of the inherent human
affinity to affiliate with natural systems and processes – known as biophilia. (Wilson 1984,
Kellert & Wilson 1993). This project developed a biophilic design plan and framework based on
two half-day charrettes to identify the priorities and design strategies to integrate biophilic design
into the project. The key areas of importance were Environmental Features, Placed-Based
Relationships and Evolved Human-Nature Relationships. The following were some of the
strategies implemented into the project. Some of the strategies are subtle but integral to the
success of the project.
- Environmental Features: With an emphasis on sunlight, natural materials, and views, the team used strategies to construct new openings, allowing more daylight into the building. Functional spaces were aligned to provide access to views, and locally sourced, natural materials were used as much as possible.
- Place-Based Relationships: To preserve the historical connection of the building, the addition matches existing building materials and style on both the interior and exterior. Connections between the dining room and porch were created to enhance the indoor/outdoor relationship.
- Evolved Human-Nature Relationships: The separation of spaces and degree of privacy were incorporated based on function, and individual/unique spaces were created for bedrooms to provide refuge. Improvements in visual contact from the interior spaces to the outdoors/landscaping were made while integrating art representing nature as a part of building décor.
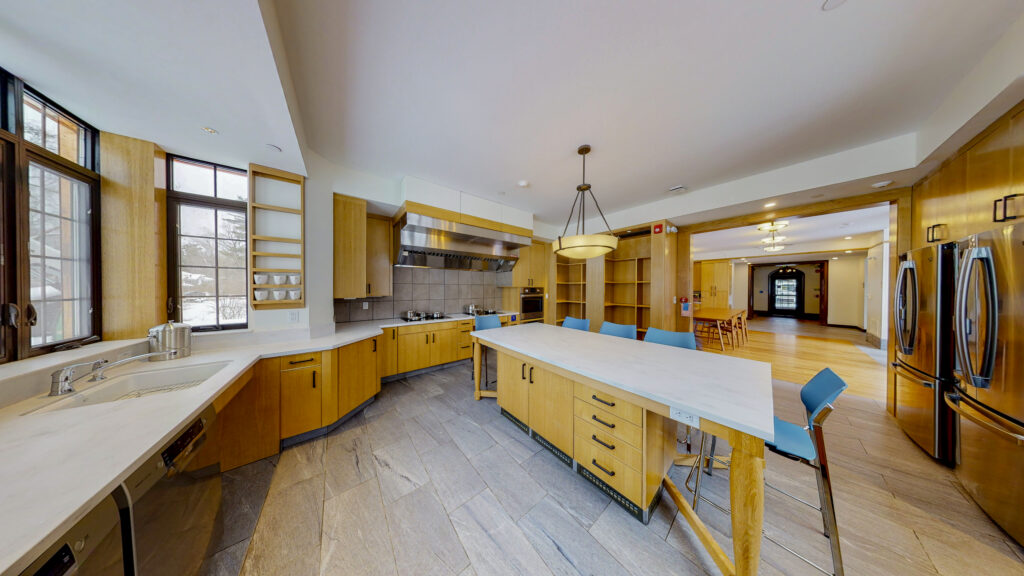
MATERIALS PETAL
I10. RED LIST IMPERATIVE
Every effort was made to specify products that met the Red List requirements. The Red List’s
intent is to eliminate the use of worst-in-class materials/chemicals with the greatest impact on
human and ecosystem health. Products were assigned to researchers after being added to
Red2Green and all information regarding Red List were tracked and reviewed for accuracy by a
team of quality assurance specialists. IES generated disclosure forms for different types of items, such as simple products, complex mechanical products, plumbing, and electrical products, to
standardize the requests to manufacturers. Researchers reviewed the information, collected
supporting documentation, and made final determinations on the products’ Red List status and
exceptions. The Fort Bradshaw project requested transparency on close to 2,000 products from
over 700 manufacturers, advocated for chemistry improvement, and generated awareness of
the healthy material requirements of the Living Building Challenge. Over three thousand hours
were invested in this effort, with the singular focus of meeting the client’s goal of building a
dormitory residence that serves as a model for sustainability and health.
One of the biggest challenges in this area is that most manufacturers lack information, or the
research required information up the supply chain. In some instances, the information was
inaccessible to the team. As part of the research effort, the College contracted Red2Green to
perform the material research related to LBC. Each product type was researched, looking at
at least three different manufacturers. There were a couple of circumstances where the
technical requirements were only met by a non-compliant product, and in those instances,
advocacy letters were sent to the manufacturer explaining the challenges and opportunities to
update the materials and make them compliant. As with every project, we discover a couple of
products that were discontinued, and the research for these products mostly resulted in other
compliant products. The substitution took roughly a month for the entire review and vetting process prior to approval before being able to be integrated into the project.
Many college standard products did not meet the Red List requirements. This review process
became an opportunity for the College to upgrade many of their non-compliant preferred
products, as well as educate the operation and maintenance team on the new technologies and
products.
I11. EMBODIED CARBON FOOTPRINT IMPERATIVE
The project must account for the total embodied carbon (tCO2e) impact from its construction
through a one-time carbon offset. Embodied carbon is the carbon footprint of the materials used
in the project from extraction of raw material to installation on site. Since this project is the
renovation of an existing structure, there were big opportunities of preserving the structure and
reducing the total embodied carbon. Based on the LCA model developed using Athena, this strategy saved 94 mtCO2e. The total footprint of the project is 224 mtCO2e. Using exception
I11-E1 Renovation Offset Reduction the final footprint of the project was reduced to 177
mtCO2e. Williams College was already purchasing offsets for the campus and an additional
one-time carbon offset purchase was done for the project.
I12. RESPONSIBLE INDUSTRY IMPERATIVE
Declare label products were integrated as much as possible into the project. The Declare label
shows the full disclosure of the material composition and life cycle assessment, allowing
designers to select materials that will reduce the impact on the environment when compared to
standard practice materials. When stone was used, the development team verified the source
and practices of the quarry and encouraged the use of the Natural Stone Council (NSC) 373
Standard. Most of the wood used in the project is FSC certified.
I12. LIVING ECONOMY SOURCING IMPERATIVE
The project must incorporate place-based solutions and contribute to the expansion of a
regional economy rooted in sustainable practices, products, and services.
Manufacturer location for materials and services must adhere to the following restrictions:
- 20% or more of the materials construction budget must come from within 500 kilometers of the construction site.
- An additional 30% of the materials construction budget must come from within 1,000 kilometers of the construction site or closer.
- An additional 25% of the materials construction budget must come from within 5,000 kilometers of the construction site.
- 25% of materials may be sourced from any location.
- Consultants must come from within 2500 kilometers of the project location.
Every effort was made to specify products which were manufactured closer to the site. The big
challenge in this area is that most mechanical and electrical equipment components, which are
in some instances a significant cost to the project, are fabricated in Asia. As part of the research
effort, the College contracted Red2Green to perform the material research related to LBC. Each
product type was researched looking at least to 3 different manufacturers. One of the deciding
factors for selection was the distance to the project site. The project achieved the following
thresholds:
- From within 500 kilometers of the construction site: 27%
- From within 1,000 kilometers of the construction site or closer: 15%
- From within 5,000 kilometers of the construction site: 53%
- 25% of materials may be sourced from any location: 5%
- Consultants must come from within 2,500 kilometers of the project location: 100% of consultants.
All information collected on products, and all attempts to contact manufacturers, were
cataloged by materials researchers in the Red2Green software. Each product reviewed was
coded with a unique identifier, an LBC ID, to enable tracking during the construction submittal phase. MCWB Architects, Sustainable Design Consulting, A/Z Construction, and Quantum
Engineering had full access to Red2Green and worked directly in the software with IES to
ensure pertinent information was communicated appropriately.
Products were assigned to researchers after being added to Red2Green, and all information
regarding product sourcing was tracked and reviewed for accuracy by a team of quality
assurance specialists. IES generated disclosure forms for different types of items, such as
simple products, complex mechanical products, plumbing, and electrical products, to standardize
the requests to manufacturers. Researchers reviewed the information, collected supporting
documentation, and made final determinations on the products’ Red List and Healthy Interior
Environment status and exceptions. The Fort Bradshaw project requested transparency on
close to 2,000 products from over 700 manufacturers, advocated for chemistry improvement,
and generated awareness of the healthy material requirements of the Living Building Challenge.
Over three thousand hours were invested in this effort.
I14. NET POSITIVE WASTE IMPERATIVE
Initially, a survey of the existing structure was done to evaluate the feasibility of preserving as
much of the structure as possible to reduce the amount of waste. The team identified
organizations that would receive donations of components such as mechanical and electrical
equipment, casework, doors and hardware, and other miscellaneous items. The College also
identified items that could be salvaged and reused in other locations on campus. The team then
identified items to be reused in the project, such as the stairs, coffer ceilings in the living room, and the stone fireplace mantel.
During construction, every effort was made to divert waste from the landfill. Items that could be
recycled were separated on-site and diverted to the appropriate recycling facilities. A challenge
during this process was the trade conflict with China and the reduction in acceptance of
recyclable materials. At the end of the project, the team achieved an 85.37% diversion rate for
the entire project.
Other features of the design are the inclusion of many materials which contain recycled content
and have recyclable content. The design was performed considering deconstruction at the
end-of-life stage, where items could be removed and donated for other uses. One such example
was the reuse of the fence scrim that surrounded the construction site. Designed by the staff of the adjacent art museum, vinyl scrim was attached to the construction fencing throughout the
duration of the project. It served as a visual barrier to the ongoing construction efforts. Upon
completion of the project, a local artisan upcycled the (half an acre of) material into tote bags which were then sold locally.
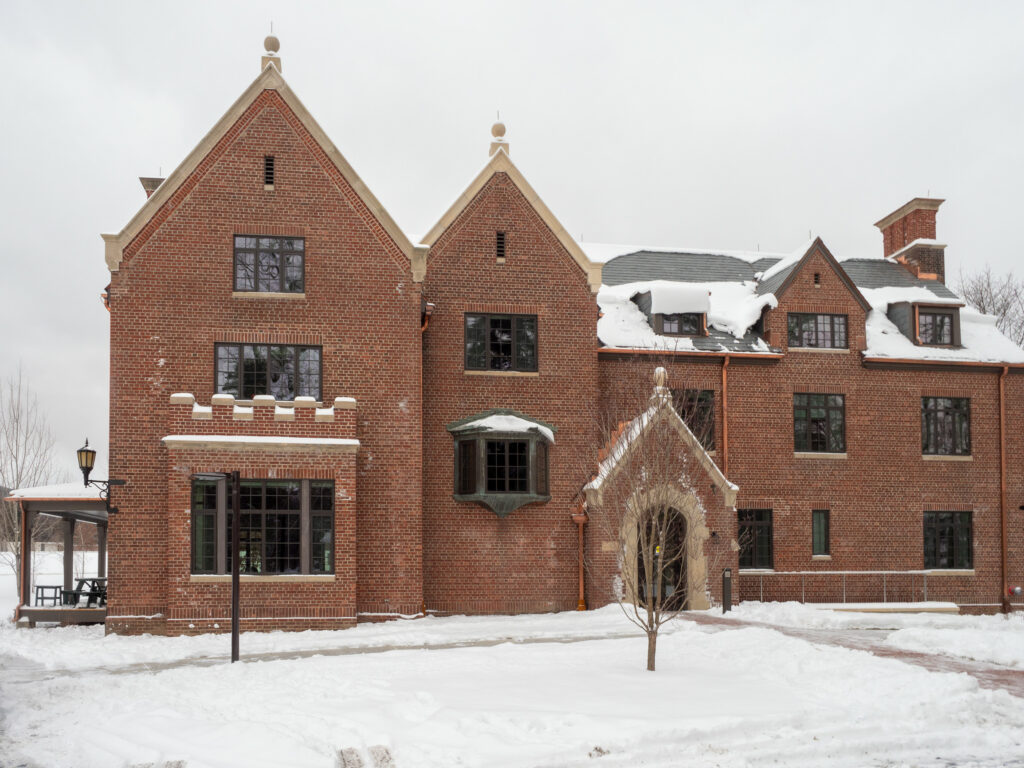
EQUITY PETAL
I17. EQUITABLE INVESTMENT IMPERATIVE
Williams College is a 501(c)3 education organization. We will be following Exception I17-E1
04/2015 Exempt organizations to comply with this imperative.
I18. JUST ORGANIZATIONS IMPERATIVE
JUST Organization and advocacy. JUST is a social justice label for organizations larger than 5
employees. Sustainable Design Consulting (Sustainability consultant for the project) is a current holder of a JUST label. All organizations participating in the project received an advocacy letter
encouraging them to participate in the JUST program.
BEAUTY PETAL
I20. INSPIRATION + EDUCATION
A case study has been developed highlighting the sustainability features of the project here. There is, in addition, educational signage throughout the building highlighting the features. A welcome brochure provides new residents with an overview of the building’s sustainability features and
how they can help reduce energy use. As part of the public education component, open
houses will be available to the public to understand the sustainability features of the project. Operation manuals have been developed to give guidance to WC staff for ongoing operation and
maintenance that is in line with the sustainability principles implemented in the project
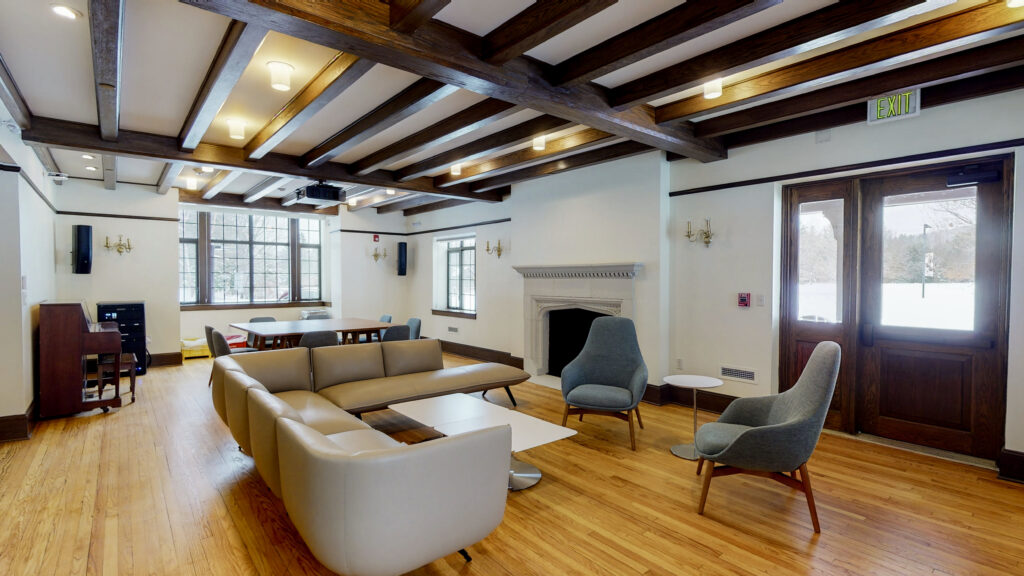