VITAL STATS
Certification Status | Zero Energy Certified |
Version of LBC | 3.1 |
Location | Hermosa Beach, CA, USA |
Typology | Building |
Project Area | 2,150 SF |
Start of Occupancy | April 2012 |
Owner Occupied | Yes |
Occupancy Type | Single Family Residence |
Number of Occupants | 3 |
PROJECT TEAM
Owner | Robert and Monica Fortunato |
Project Manager | Owners |
General Contractor | Owners |
Designer | Owners |
MEP Engineer | P2S Engineering |
Lighting Design | Chris Bowsher – Lighting Design Studio |
Specialty Contractors | Charisse Bartholomew – Green Point Rater; Gary Klein – Hot Water Systems Design; Harding Construction and Sustainable Solutions – Building Envelope; Roark Parks – Hot Water Systems Installation |
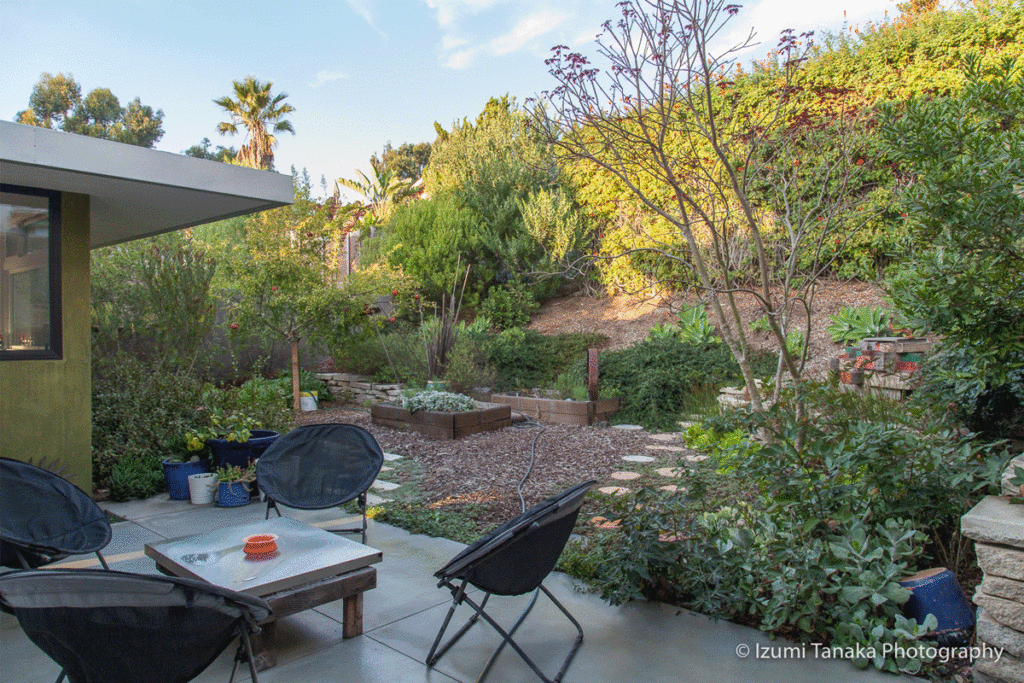
BUILDING SYSTEMS INFORMATION
Wall R value and section specification | R15.25; ThermalCORE phase change drywall, 2″x4″ framing filled with cellulose insulation; 2 layers of staggered BlueRidge fiberboard sheathing; air sealed with Knauf EcoSeal |
Roof R value and section specification | R28; Light grey TPO with .46 reflectivity factor |
Floor R value and section specification | R-19 |
Windows | Double-pane |
Air infiltration rate and sealing protocol | 376 cfm50/1.12 ach50; wall cavity sealed with Knauf EcoSeal; 2 layers of fiberboard sheathing, installed with seams staggered |
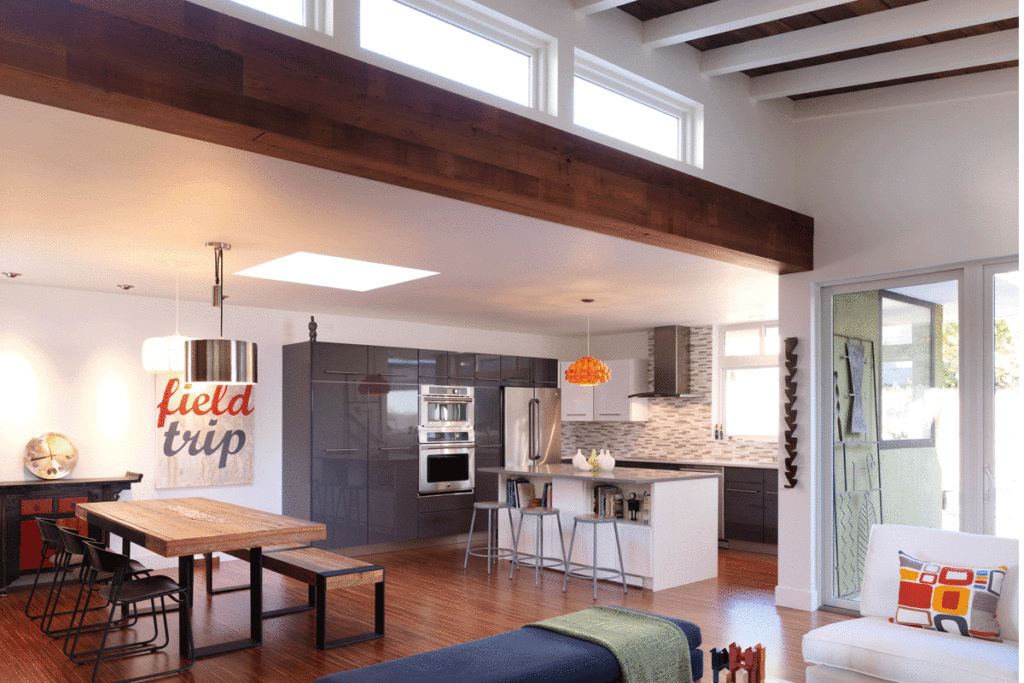
NON-MECHANICAL SYSTEMS
PASSIVE SYSTEMS
Passive Conditioning and Ventilation – The need for air conditioning was eliminated by a 5-foot roof overhang that shades the home in the summer.
In winter, the southwest orientation of the house heats the living spaces. The thermal garage is also heated passively via a window in the insulated garage door. The heat is used to increase the efficiency of the GE heat pump hot water heaters.
A thermal chimney in the stairwell ventilates the house and eliminates the need for air conditioning. Warm air rises naturally and is exhausted from the house through venting skylights and a window at the top of the stairwell.
Thermal Mass – ThermalCORE phase change drywall was used on most ceilings and on the living room wall. The dry wall regulates room temperature by absorbing heat during the day and releasing it in the evening, when it cools down in the house. One half inch of this dry wall has the same thermal effect as a layer of brick a foot and a half thick.
Shower Drainwater Heat Recovery – The Green Idea House has two drainwater heat exchangers. Upstairs, RenewABILITY’s Power Pipe transfers the heat from the hot shower water as it goes down the drain, to the cold water pipes supplying the shower (vertical drop). Downstairs, the Eco-drain hot water heat exchanger is used in the same way, but over a horizontal run.
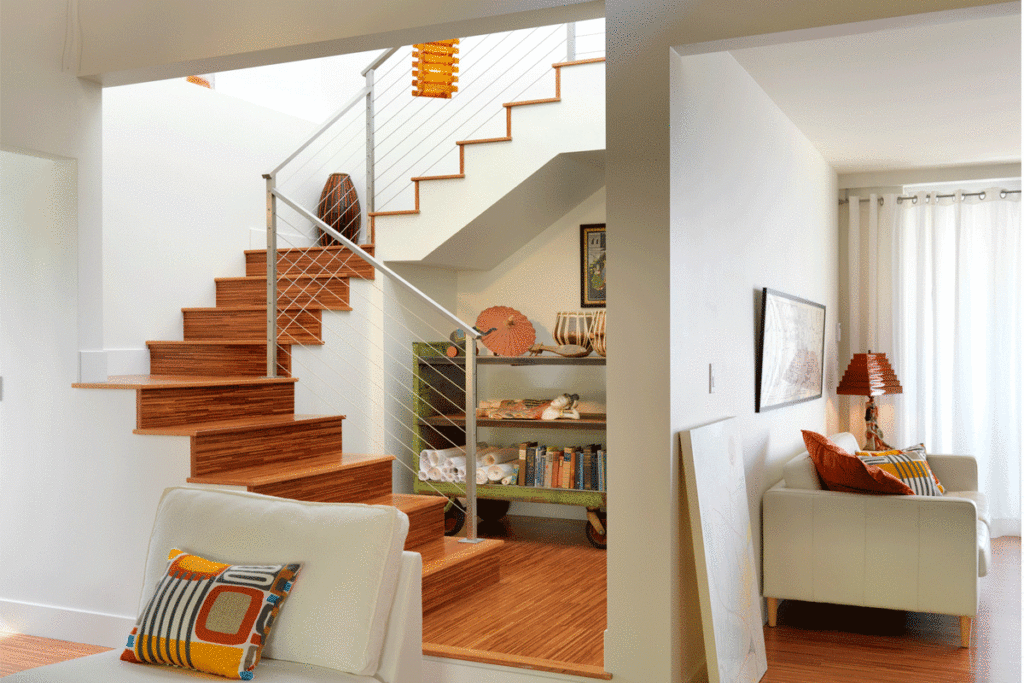
MECHANICAL HEATING + COOLING
Heat pump water heater – A typical tankless water heater is rated at best as 95% efficient. In contrast, two GE heat pump water heaters with an efficiency of 238 % (at the same cost or lower than tankless) were installed in the thermal garage. One heats domestic hot water and the other serves the home’s space heating system. In addition, the tank from the home’s old gas hot water heater was stripped of its insulation and burners, and repurposed to preheat incoming city water to ambient temperature, a savings of 20°F worth of energy use, with no wattage at all.
Hydronic radiant baseboard heating system – The remodel was originally planned to include radiant floor heating, but at a cost of $24,000, the owners felt that this feature would not represent an economical upgrade option for average homeowners. Instead, they chose a Runtal baseboard heating system, with Uponor piping manifolds and controllers ($12,000). The Runtal heaters are comprised of 40% recyclable content and are made in the United States.
LIGHTING
Daylighting – The design and placement of skylights and windows eliminates the need for artificial lighting during the day.
Energy-efficient lighting fixtures – The home has minimal recessed can or incandescent lighting. Wattstopper lighting control fixtures are used in every room.
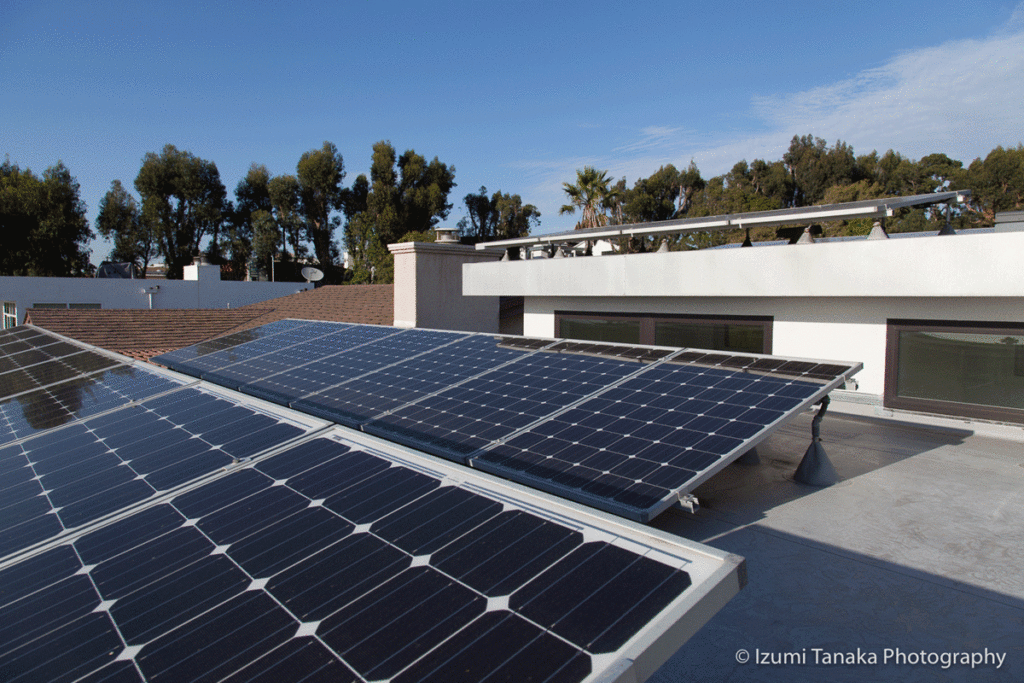
RENEWABLE PRODUCTION SYSTEMS INFORMATION
Photovoltaic solar panels – At a cost of $18,000 after rebates, 26 photovoltaic solar panels with the capacity to produce 6.5 kW of electricity were installed on the rooftop by Mediterranean Solar. The array is oriented to the southwest and incorporates Enphase micro inverters.
The panels were manufactured in the United States by SolarWold Panels. At the end of the panels’ 40-year life, the manufacturer commits to removing the silica from the panels and recycling them.
PERFORMANCE
Actual energy use during performance period | 6,655 kWh |
Actual energy produced during performance period | 7,768 kWh |
Net Energy Use | -1,113 kWh |
EUI | 10.56 kBtu/ft²/yr |
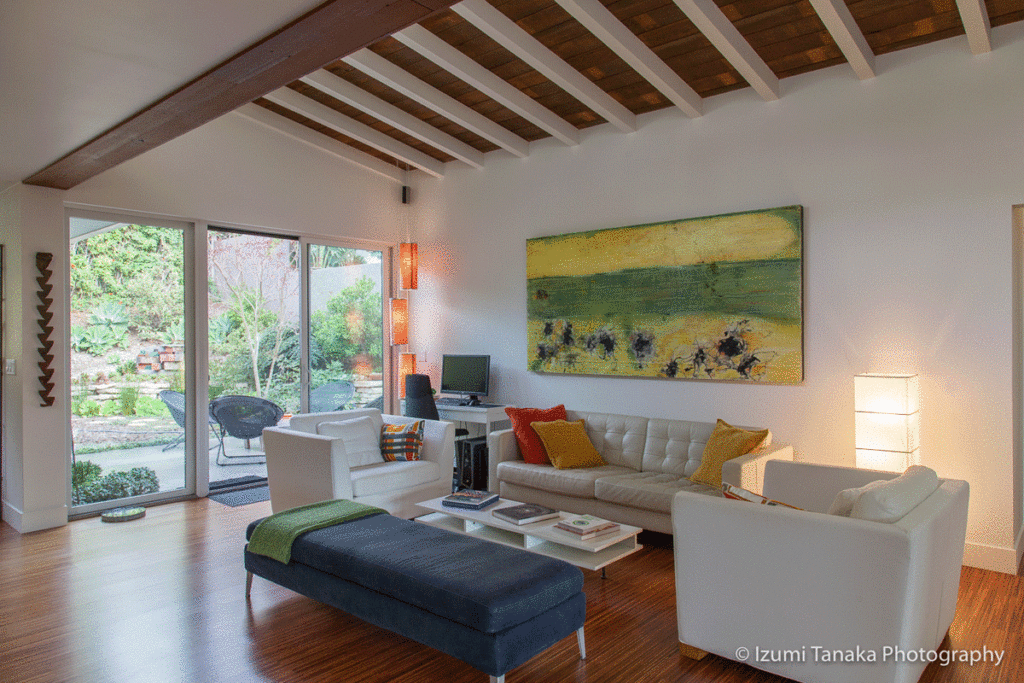
PROJECT LEADERSHIP AND STORY OF PROJECT
In 2002, the owners noticed soot accumulating outside their newborn son’s bedroom window. On that day, their ambition to convert their 1959 Hermosa Beach house to an economical, carbon-emission-free, zero-net-energy home was born.
Ten years later, the family moved back into a remodeled upgraded home, 800 square feet larger than the original. While the project had then not been entirely completed, the family was already enjoying harvesting all of the energy they needed from their rooftop solar panels, and sending 80 kilowatts back to the grid each month. But the remodel went beyond the typical energy upgrade, the home is entirely electric and features numerous other green strategies including:
FSC Certified Lumber
The structure used advanced framing, and where possible, lumber certified by the Forest Stewardship Council.
Local, Recycled, Reused Materials
The living room ceiling is made from 80-year-old redwood salvaged from a structure in Los Angeles. Recycled permeable Stepstone pavers create a path from the driveway to the stairs, and recycled tiles from Oceanside Glass and Stonepeak are used in the interior.
Recycle/Reuse of Demolition Waste
The project was able to recycle 97.5% of the demolition waste and incorporate salvaged materials through thoughtful deconstruction by the Reuse People and RER. Lumber from the existing home was used in the remodel, and broken-up patio material was repurposed into backyard garden walls. Materials that could not be used in the project found new homes via internet and newspaper ads.
Rainwater Harvesting
Rainwater is captured in a 1,200-gallon Norwesco tank, where it is stored for use on the landscape.
Air Sealing
Attention to both airtight materials and air sealing details during the remodel led to an 80% reduction in air leakage. This translates to a significant reduction in both unintentional entry of outside air and loss of conditioned interior air.
Giving Back to the Community
The owners have used the Green Idea House as an opportunity to engage and educate the community about green building. Work crews from Youthbuild, a non-profit organization that teaches trade skills to at-risk inner-city teens, helped deconstruct and install portions of the project.
In addition, the family has opened the house for many tours and shares their story on www.greenideahouse.com.
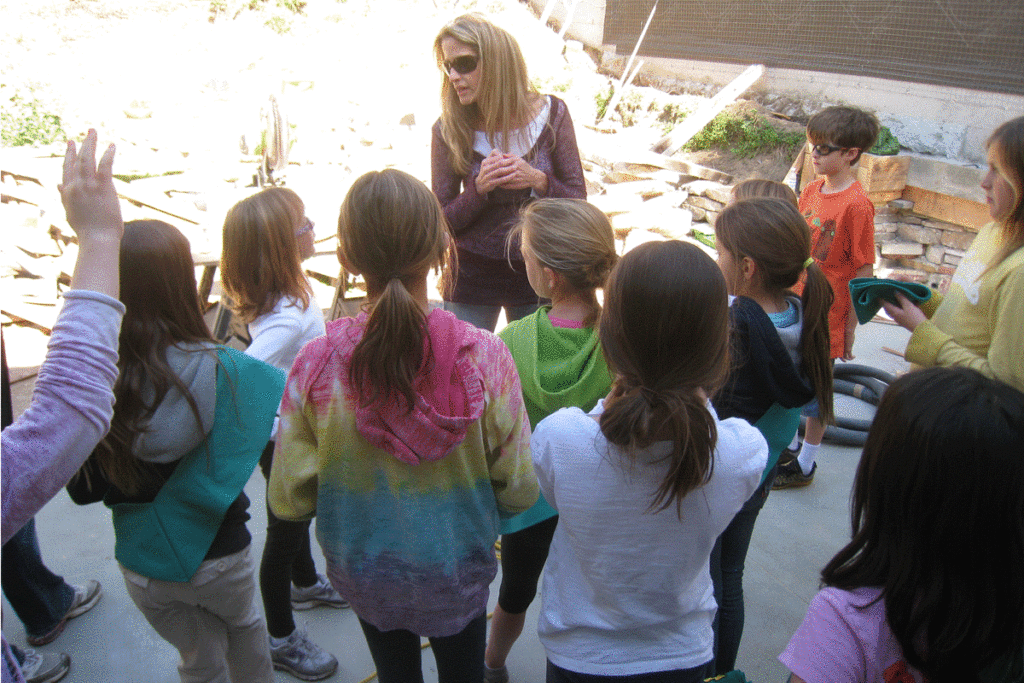
DESIGN PROCESS
The owners’ objective was to achieve net zero energy with zero carbon – that is, to harvest more renewable energy than they consumed on an annual basis.
“We liked the simplicity of the definition. We did a series of design charrettes that paid close attention to materials, waste, energy, water, and toxicity. We capped off the gas line, which was seen as radical back then (2002), and none of the energy models that were done at the time could fully capture what we were attempting to do. The building turned out to work far better than predicted We ended up diverting 97% of the demo and construction waste and reducing our water bill by about 1/3. On the energy side, we over-generate enough to cover our two electric cars.
The trick to getting the project to cost less was to think of the problem more holistically. For example, if the overhangs, insulation, and air sealing could help heat and cool the building naturally, their incremental cost would be more than offset by the smaller mechanical heating and cooling systems that would need to be installed. That does not even contemplate the operational costs over the life of the building.
Also, we partnered with over 70 public and private entities on the project (see Partners page on the www.greenideahouse.com). We very rigorously vetted their products and gave them feedback on their sustainability features. Some partners donated products or gave a discount in exchange for cross promotion with our project.”
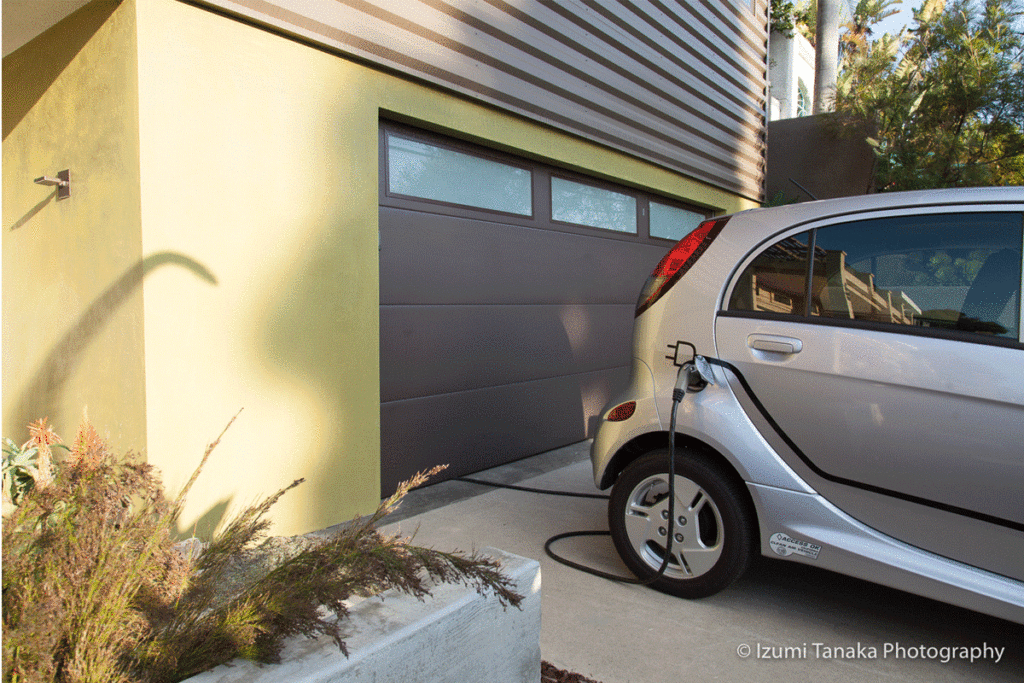
Photo Courtesy of Izumi Tanaka Photography
LESSONS LEARNED
Some lessons were obvious, others went unnoticed for months.
“As soon as the roof was finished, we installed the solar system. But because we were so busy with construction, we did not meter the solar array. When we finally got around to it six months later, we found that half the array was not connected properly! In addition, a couple of years into occupying the building, the local utility had a severe power surge that wiped out half of our inverters. We now recommend that everyone install whole house surge protectors for all the sensitive electrical equipment in these houses. Cheap insurance indeed!
On the plus side, the overhangs work better than we expected. They both cool and allow the building to absorb heat beautifully.
We have learned many more lessons from living in the house for several years now, and we share them when we give tours or do public speaking.”