VITAL STATS
Certification Status | Zero Energy Certified |
Version of LBC | 3.1 |
Location | Davis, CA, USA |
Typology | Building |
Project Area | House: 1,944 SF, Garage: 477 SF |
Start of Occupancy | October 2014 |
Owner Occupied | No |
Occupancy Type | Single Family Residence |
Number of Occupants | 4 |
PROJECT TEAM
Owner | American Honda Motor Co., Inc |
Project Manager | Michael Koenig |
General Contractor | Monley Cronin |
Architect | Lim Chang Rohling |
MEP Engineer | Davis Energy Group |
Lighting Design | UC Davis California Lighting Technology Center |
Interior Design | Mak Design + Build |
Plumbing | Gary Klein |
HVAC Design | UCD Western Cooling Efficiency Center |
Concrete | Syar Concrete |
Key Subcontractors | AP Plumbing and Fire, Country Bear Electric |
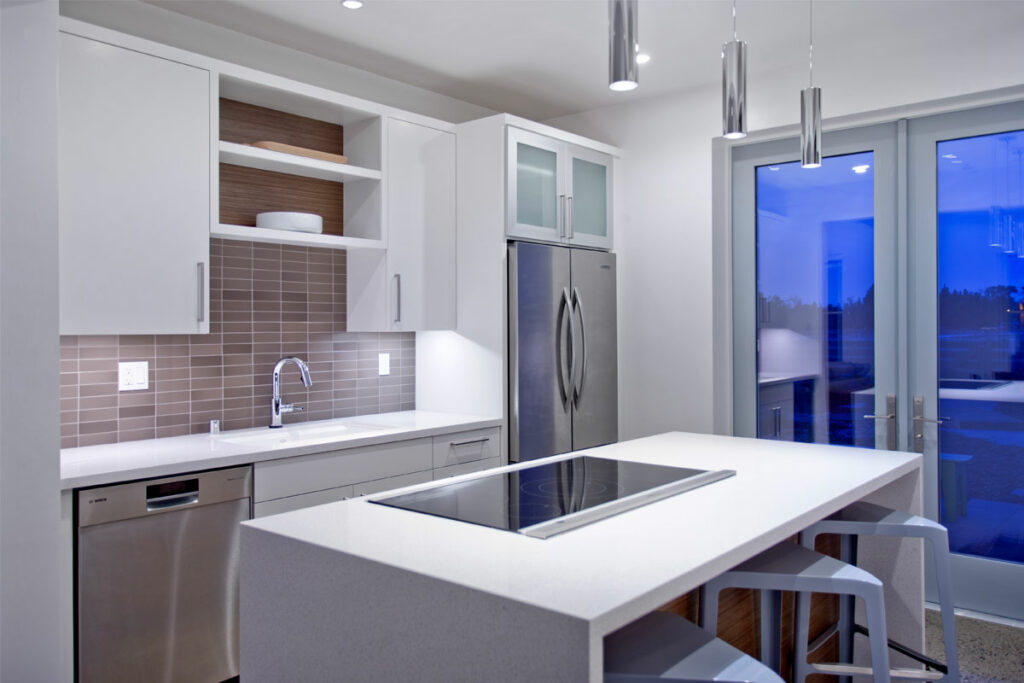
BUILDING SYSTEMS INFORMATION
Wall R value and section specification | R31. Double stud 9.25” cavity, dense pack cellulose |
Roof R value and section specification | R60. Loose fill cellulose, vented roof deck |
Floor R value and section specification | R10. Viega underslab insulation for hydronic installations |
Windows | All windows Alpen triple pane. U values = 0.11 ~ 0.20, SHGC = 0.10 ~ 0.32 |
Air infiltration rate and sealing protocol | 1.9 (ACH-50). Sealing consisted of conventional caulk sealant, plus application of a prototype aerosolized sealant system (UC Davis) |
NON-MECHANICAL SYSTEMS
The passive design strategy optimized the orientation of fenestration for daylighting (north clerestory windows) as well as the southern windows’ overhangs; note that the roof overhang is optimized for 2F windows, as well as the additional awnings applied over the lower windows on the South side. Also, although the shades are primarily provided for privacy, the 2F West window shade will automatically lower at noon for heat gain, but will open again at sunset for a nice view of the mountains.
MECHANICAL HEATING AND COOLING
Bosch TW025 water/water heat pump with hydronic distribution. The ground source heat pump uses a novel helical-coil exchanger design for high performance and moderate cost; primarily “dry” bores are used for source side exchange, but wetted bores are also in use for data comparison.
MECHANICAL VENTILATION
Depending on need, we ventilate the house using up to 5 bath fans (Panasonic FV-13VKS3), and/or the whole house fan (Motor: GE/ Regal-Beloit 1 hp ECM 2.3, Blower: Morrison 12-10 forward curve centrifugal blower) pressurizing the house with filtered air distributed by registers into the great room. This is used to take advantage of diurnal temperature swings (to pre-cool the house on summer nights) and also to provide 62.2 ventilation. This is also used to moderate excessive solar gain in the house during shoulder seasons so mechanical cooling is not required.
HOT WATER
Bosch TW025 (same unit as heating/cooling) with desuperheater, stored in Triangle Tube Smart SME 80 tank. We also use a PowerPipe R3-72 Drain Heat Recovery unit to pre-heat incoming makeup water during showers.
LIGHTING
100% LED with occupancy sensor and daylight sensor. 5 scenes per room (depending on time of day) with wall-button override, and novel “sleep” setting for bedrooms. Lutron Ecosystem control.
USER LOAD REDUCTION STRATEGIES
Real time energy performance, as well as 24 hour history are presented to the occupants on the home screen of the control tablet.
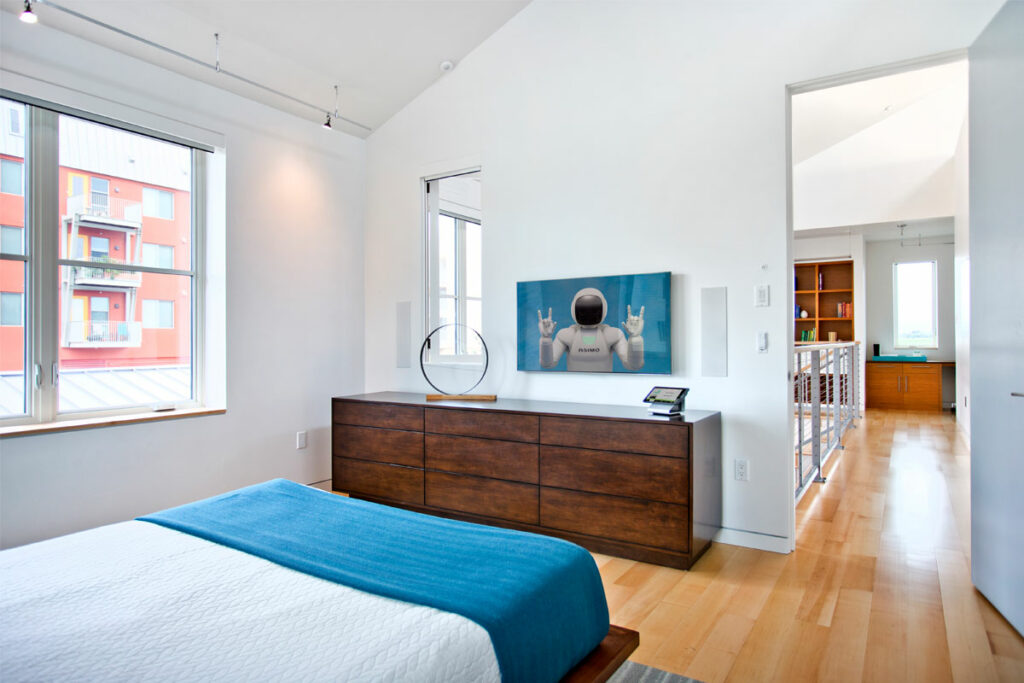
RENEWABLE PRODUCTION SYSTEMS INFORMATION
36 – Suniva Optima 265W = 9.54kW nameplate PV Inverter is Honda proprietary equipment, integrated with the Home Energy Management System, 10kW bi-directional capability. Location is a dedicated Equipment Room in the garage with auxiliary cooling available.
PERFORMANCE
Actual energy use during performance period | 10,634 kWh |
Actual energy produced during performance period | 11,236 kWh |
Net Energy Use | -602 kWh |
EUI | 18.7 kBTU/sf/yr |
PROJECT LEADERSHIP AND STORY OF PROJECT
This home was imagined as a demonstration of a Zero Carbon future, including not just the home but also the daily transportation. The purpose was to engage society in a discussion to try to move forward to a future of renewable energy and electrified vehicles; it was therefore conceived as a package including the home, vehicle, and energy management system. In order to bring as much societal value as possible, we also wanted to highlight discussions of sustainability beyond energy. So while energy is clearly a focus, we also tried to demonstrate sustainability of the materials themselves, water use, waste, and occupant health.
The project was developed by Honda, led by the Environmental Business Development Office (EBDO) within American Honda Motor Co., Inc.
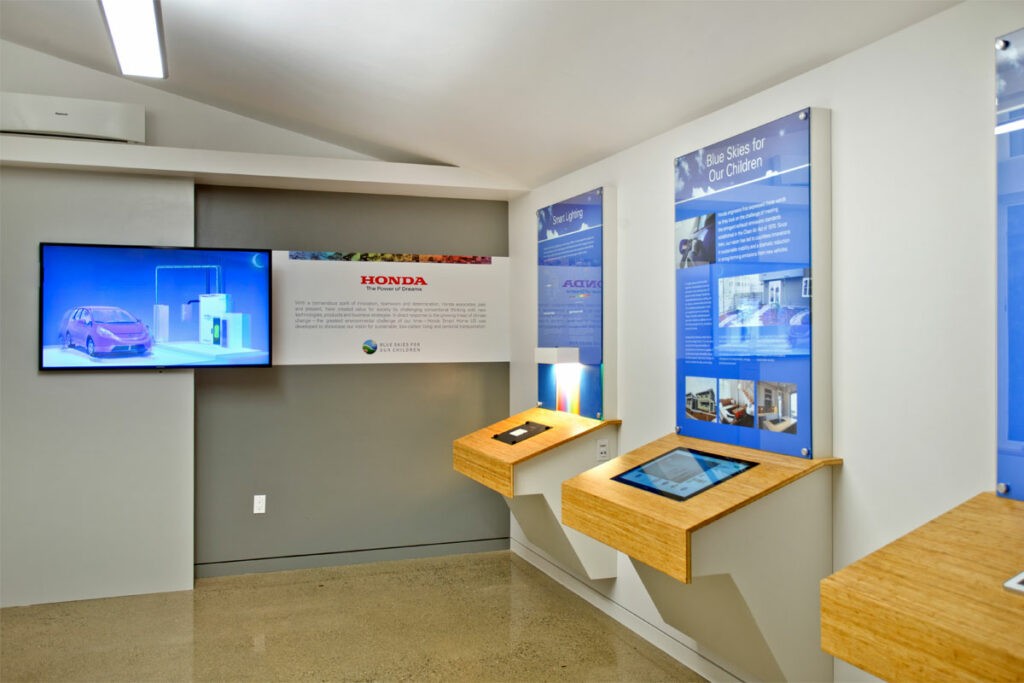
DESIGN PROCESS
The name “Honda Smart Home” refers to the Smart design and use of energy. We therefore began with a holistic, integrated design process considering all aspects of sustainability. As with most “real-life” projects, our site required specific layout features in order to make full use of solar access, while providing for access to the garage. To make full use of solar energy, our roof form is biased towards southern exposure with minimal roof penetrations to disrupt panel layout; and the North side is designed for natural daylighting. Every detail of design was similarly considered, which meant continuous discussion among the architect, HVAC designer, mechanical engineers, certification members, and EBDO leadership.
ENERGY SYSTEMS NARRATIVE
The basic viewpoint for the project was to first build the home as efficiently as possible: the envelope, HVAC system, lighting, appliances, and MELs. Then to allow the occupants to live without sacrificing quality-of-life. Of course, they are aware that they are living in a demonstration home, and that their usage data will be recorded; but the intent is not to try to coerce specific behavior. If the occupants need to run laundry or wash dishes, then the home should respond as requested, but if this would cause hardship for the electrical grid, then the HEMS machine will seamlessly step in to allow them to continue their daily routine, but also provide value to the grid.
We therefore do not control any of the appliances with the HEMS machine. In extreme cases, we can use the thermal mass of the home to slightly shift the HVAC run times, but in general we only actively control the vehicle charging to minimize CO2 (and use the stationary battery to provide grid support).
The home is oriented for maximum winter sun collection, but with careful design of the roof overhangs and addition of awnings to shade the South windows from summer sun. The home also takes advantage of the cool summer evenings by pre-cooling using only fresh air, and throughout the year ventilates primarily at times of day when the outdoor temperatures are preferable (note that this climate has low summer humidity which allows for this pre-cooling strategy). We are also able to track vented air from the central vacuum, range hood, or bath fans so that we do not over-ventilate on days that have supplemental sources of fresh air. We use a passive heat exchanger to recover heat from greywater, then further remove heat (mechanically) from that greywater as it percolates through our wetted boreholes. And of course, the windows provide excellent natural daylighting for most of the day (the lighting system uses daylight sensors to reduce consumption when enough light comes from the windows).
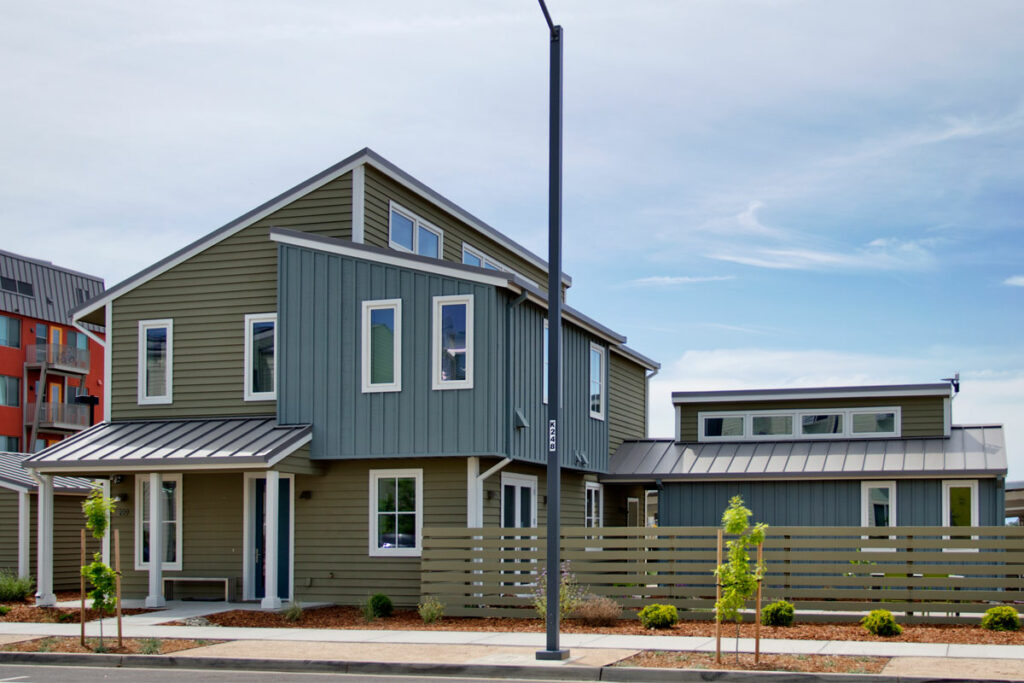
OCCUPANCY ISSUES
The home is continually being updated with new features and controls, and our occupants have always been very flexible and accommodating. In some cases, as we develop new HVAC controls, we have had to work with them to fine-tune the system to their preferences (for example, the blower settings for pre-cooling and the zoning for the hydronic distribution).
The occupants have been very positive on the home’s overall layout and open plan, and the lighting.
BUILDING COMMISSIONING, START UP, AND OPTIMIZATION
One of the most impactful issues we had was with our original strategy to use the whole house fan to pressurize the house, and open the clerestory windows to allow the cool air to flush the home on summer nights. The third-party motors used to actuate the windows were intrusively loud, and did not reliably lock the windows when closed. The fan itself was also too loud to operate when occupants were sleeping. Using the bath fans to pull cool air into the house (through a dedicated outside air damper, and through a filter) resulted in an uncomfortable depressurization, and limited effectiveness. Ultimately, we replaced the whole house fan with a quieter version, and now use it combined with the bath fans to exhaust the warm air while keeping the clerestory windows closed (balanced ventilation).
REGULATORY ISSUES
There were no issues. All of our systems were permitted and installed using the “typical” process, without any request for variance. At the time of installation, there was some question regarding the use of a stationary battery, but ultimately the utility determined that the system could be interconnected using the same process as a typical solar system.
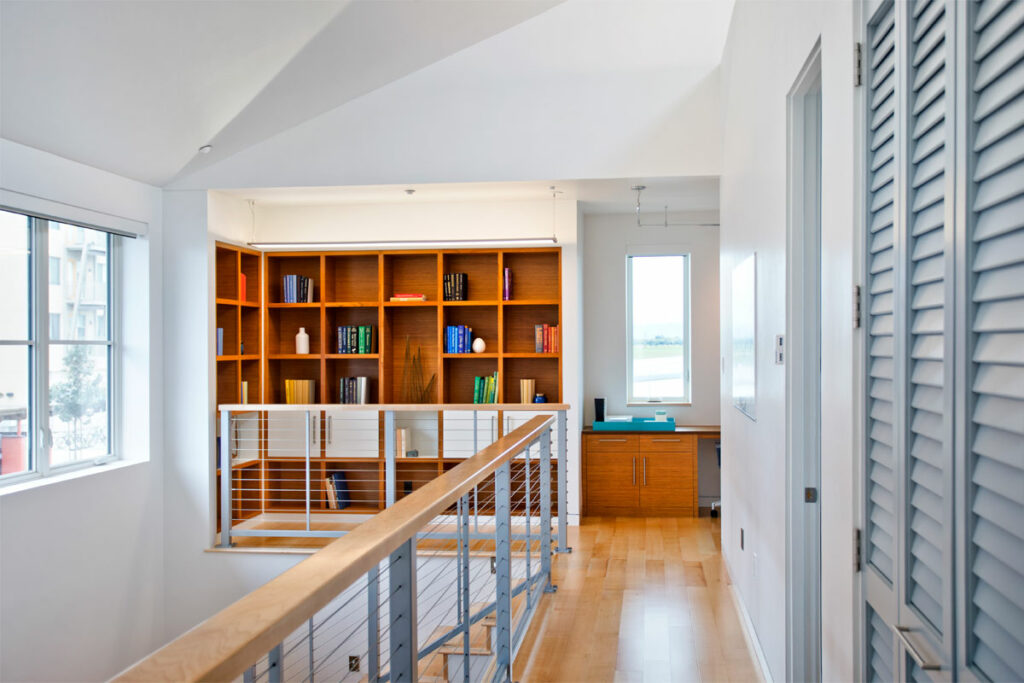
ENERGY RELATED BUILDING COMPONENT SUGGESTIONS
Although our HVAC system is an elegant design, it required substantial development and engineering. A turn-key solution for a water to water heat pump with integrated Heating, Cooling, and Hot Water functions, as well as thermostatic control would be welcome.
LESSONS LEARNED
There are a lot of specific lessons to be learned in areas ranging from the door latch hardware, to the thermal modeling, to the solar gains, to the use of polished concrete! The public is invited to reach out to us at HondaSmartHome@hna.Honda.com to discuss any of these topics with the project leader. We post all of our monitoring data, as well as videos, specs, and drawings to www.HondaSmartHome.com