Humanscale is the premier designer and manufacturer of ergonomic products that improve health and comfort of work life. Their functional yet minimal designs and ergonomic consultation services help transform traditional offices into active, intelligent workspaces. Humanscale has become an industry leader in sustainability, advocating for more rigorous standards and incorporating a Net Positive philosophy into every aspect of their business. As a global company, their approach focuses not only on minimizing negative impacts but working to produce significant positive contributions. Humanscale’s goal is to make an overall Net Positive impact on the Earth. Achieving Living Product certification for the Float® table and Diffrient Smart™ chair in 2016 gave the company a tangible example of what being Net Positive looks like. Humanscale has embraced the Living Product Challenge once again, this time, for a total of 26 products across all of its manufacturing facilities.
Path is an evolution of Humanscale’s commitment to sustainability: with each new product, Humanscale sets a higher standard for and finds ways to embed sustainability into our designs. Path upcycles more plastic waste than any other chair in the industry. Like all Humanscale chairs, it is produced to reduce our impact on the climate. While Path is new, it is Humanscale’s 26th net positive product, which is more than any other company has. Humanscale was the first to take this approach and remains the only manufacturer in its industry to have products that are certified climate positive.
Humanscale chose to certify/re-certify 26 products in 2020 as a next step in having a Net Positive impact on our environment. Getting buy-in across the organization to not only significantly expand their LPC-certified products, but also to include all their global manufacturing facilities, was a crucial component of achieving this goal. The company then had to evaluate each facility individually to address any necessary upgrades required by the Challenge. By assigning tasks to different teams, the effort was more evenly spread out across the company and departments felt greater ownership of the work that Humanscale was doing. The LPC framework has become a part of how Humanscale approaches manufacturing, making sustainability integral to its other goals, and not a competing force.
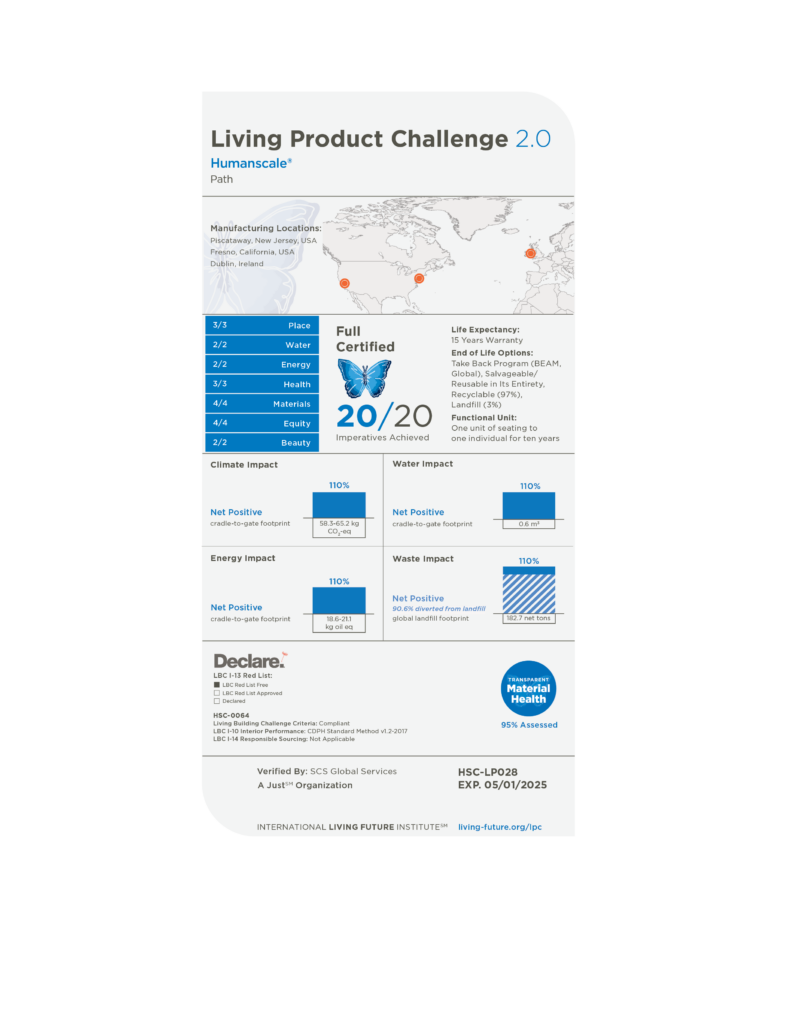
TOP HURDLES TO CERTIFICATION
Top Hurdles to Certification | Description of Solution/Changes Implemented |
---|---|
1. Red List Ingredient/Chemicals of Concern Removal | Humanscale’s efforts to remove chemicals of concern from products began many years ago. As part of its initial Living Product Challenge certification, Humanscale worked with suppliers to remove PFC stain-resistant coatings from textiles, Chromium (VI) from chair caster wheels, began to use formaldehyde-free medium-density fiberboard (MDF) table tops, and updated supplier contracts to clarify that Halogenated Flame Retardants (HFRs) are not acceptable after discovering them in textile backing without the company’s consent. Since then, Humanscale began exclusively offering chrome-free leathers sourced from a carbon neutral tannery that does not use chromium in its tanning process. With some success in the past, the availability of Red-List free alternatives remains one of the main hurdles the company faces in Red List-free requirements. When Humanscale upgraded its monitor arm product lines to M2.1, M8.1 and M10, there were very few facilities accommodating Chrome (III) plating. The company instead eliminated chrome plating altogether by redesigning its products. Humanscale has also removed PVC from several task lighting products, including Nova and Infinity. Looking for PVC-free alternatives for task lighting is especially difficult due to the limited solution for PVC-free cables in electronic products. With that being said, the company still went above and beyond the Red List requirements in LPC. When redesigning the Sit/Stand product QS Eco, Humanscale found that the powder coating used on the platform contains PFAS-based chemicals. Although the chemical is less than 100ppm of the product, Humanscale worked with that supplier for several months to find the alternative to replace the PFAS Red List chemical. As part of expanding Humanscale’s certification this year, the company analyzed process chemicals at all manufacturing facilities to confirm that they are free of Red List ingredients. Operational cost increase is a huge hurdle for process chemical Red List removal. At the Piscataway location, Humanscale worked with landscapers to swap the fertilizer with a petrochemical-free alternative. At the Nogales location, after finding out two chemicals contain Red List ingredients, Humanscale had to switch to a completely different cleaning and paint preparation system to eliminate the two chemicals for safer and healthier operations. |
2. Waste Diversion | Waste Diversion from Landfill has been a big hurdle to certification for Humanscale’s wide array of products. Meeting the LPC’s 90% Diversion from Landfill was challenging for many reasons. First, the nature of Humanscale’s products as high-function and high-aesthetic end-user furniture increases the type of materials and packaging entering the facility and stresses the need for supreme protection on upstream and downstream transport. Second, various parts arrive via pallet in differing containers and protective packaging. This creates many waste streams that need to be individually separated in order to be recycled or reused, and a high level of entropy on the production floor as the various components are removed form vendor packaging, assembled, and repackaged. If Humanscale’s products were more like standard raw building materials, there would be less waste streams, individual waste components, and easier collection. To meet this hurdle, Humanscale created an iterative system for material separation and a continuous improvement process for waste stream identification. Material waste is tracked by type across all production facilities. Humanscale’s waste diversion program began at the Piscataway facility in 2016 and has since been implemented across the organization. Each facility has specific waste streams customized to its place in the production process and the products that are assembled there. Color-coded signage and regular specific training have been the key to a heathy waste diversion system. Accomplishing and maintaining this feat requires a coordinated effort among several teams. Site managers gather data and send hauling reports from the many vendors that service each location, which the Sustainability team compiles. This compilation produces the diversion rate and identifies areas for improvement in the diversion system. The facilities and operations teams implement actions to separate waste and maximize diversion, rearranging bins on production lines, setting up collection areas, and reviewing daily contents of bins. Humanscale held meetings with all internal stakeholders, reviewed current waste haulers, and the RFQ process to source vendors with ability to recycle additional materials. Periodic landfill audits show any sources of error and opportunities for new diversion streams. The final key was placing select individuals in charge of final diversion in all facilities. This provides a last check and opportunity to re-sort materials before they are removed from the building. Additionally, Humanscale has referenced existing Zero Waste certification systems like TRUE Zero Waste and Green Circle Certified Zero Waste to find new upstream waste diversion options and standardize with best practices. |
3. COVID-19 Pandemic | The COVID-19 pandemic began affecting Humanscale’s locations in the midst of preparation for the Living Product Challenge. With many businesses closing down, and on-site and in-person appointments put on hold, many checklist items for completing the Challenge were delayed for months. This included indoor air quality testing, rainwater harvesting system installation, community outreach events, and others. Many handprinting activities were also put on hold because of COVID-19. In-person visits to homes for LED light bulb installations were put on pause. Earth Day handprinting events had to be reimagined. Rather than park clean-ups and in-person LED give-outs, Humanscale held a virtual Earth Week campaign, inviting employees and the extended network to join in completing one handprint action each day and to log it on Humanscale.handprinter.org. A few facilities’ open house events were postponed indefinitely because of the pandemic as well. Data collection in relation to the challenge was also delayed because so many companies were shut down. The pandemic also affected the way in which Humanscale was audited for the certification. Rather than in-person audits at each manufacturing location, virtual audits were held. This required appropriate technology and pre-planning in order to have these audits run smoothly. |
4. Handprinting Requirement | Creating handprints equivalent to 110% of the LPC-certified products’ footprint was a top hurdle to certification. Accomplishing this for each impact category required a variety of handprinting activities and a combined effort from many people. Humanscale planted trees, distributed high efficiency light bulbs to conserve energy, supported environmental programs in schools, encouraged and tracked handprinting actions completed by employees. The most impactful handprints came from sponsoring the installation of solar panel systems for non-profit organizations. These installations are being built at an animal shelter, a housing, support, and services center for people with autism, and at affordable housing organizations that assist low-income and rural residents. Each of these handprinting initiatives required significant research and backend calculations to determine their full impact. After each product’s footprint was calculated and verified with Life Cycle Assessments, Humanscale conducted further research and calculations into handprinting possibilities that were impactful and realistic. After much trial and error, the company has found that having a wide variety of handprinting initiatives is imperative to creating handprints in all three impact categories for so many products. |
5. Volume and Complexity | Humanscale manufactures complex products with many configurations and a global supply chain. This challenge wasn’t limited to a few configurations of each product nor to one manufacturing location. All configurations for all 26 products from all four global manufacturing locations were included. This amounts to hundreds of product variations. This required communicating with suppliers all over the world to research material composition and it required all factories worldwide to rise to meet the rigorous standard of the Living Product Challenge. |
place petal
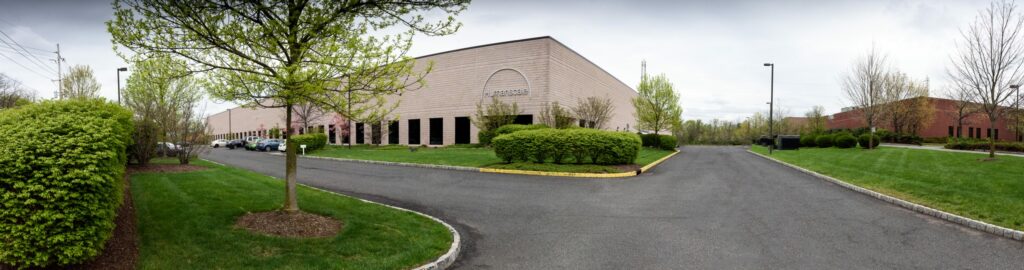
The Path chair incorporates nearly 22 pounds of recycled content, including 9.5 pounds of fishing nets from the ocean. Humanscale intends to incorporate more ocean-bound plastics into many more of our products. The transition to this sustainable material not only leads to cleaner oceans, but it also reduces our need to extract this raw material from nature.
On a local level, each of Humanscale’s owned manufacturing locations have unique three-year landscaping plans to support surrounding ecosystems. They include removing invasive species and replacing them with indigenous varieties to provide habitat and diet for local wildlife and for more robust biodiversity.
01. RESPONSIBLE PLACE IMPERATIVE
Humanscale operates out of four manufacturing facilities globally: Piscataway, New Jersey; Fresno, California; Nogales, Mexico; and Dublin, Ireland.
The New Jersey factory is located on the south side of the Raritan Valley in Piscataway. Founded in 1666, Piscataway remains home to a number of forests and a good population of wildlife. It also contains a significant amount of industry and manufacturing, including a number of global headquarters. Humanscale Piscataway is situated in an industrial campus, surrounded by similar warehouse facilities, roadways and parking lots. Humanscale installed a walking path through the trees, along the stream, and around the building to encourage employees to reconnect with nature and to maintain an active and healthy lifestyle.
Like Piscataway, our Fresno location is located in an industrial corporate campus, surrounded by similar warehouse facilities, roadways and parking lots. Founded in 1872, Fresno is a city in California’s San Joaquin Valley and is the fifth most populous city in the state. Humanscale rents this space in Fresno and therefore does not have control over the property nor its landscaping.
Humanscale Dublin is located in the Poppintree neighborhood of Ballymun in an industrial park, surrounded by similar warehouse facilities, roadways and parking lots. An outdoor lunch area for employees is set up next to the on-site pond, which is used regularly during the summer. It also has vegetable gardens on the grounds that are shared among employees during the annual barbeque. Humanscale maintains the pond and has identified every plant species on the property. Invasive species have been removed and replaced with more indigenous varieties.
The Nogales facility is located just south of the United States-Mexico border and on the northern border of the Mexican state of Sonora. Established in 1884, Nogales is located 1,000 meters above sea level and does not get as hot as the Sonora desert. Nogales is a semi-dry, sub humid climate with rainfall occurring during their very hot summer season. A coordinated “Green Event” takes place annually, where employees spend the day planting gardens with native plants.
Industrial centers are often located in close proximity to wildlife. However, in researching the International Union for Conservation of Nature (IUCN) species report, Humanscale determined that its manufacturing facilities do not directly contribute a threat to recognized endangered species in the area. As part of landscaping plans, Humanscale assessed the plant species present at its three owned facilities, removed any invasive varieties, replaced damaged/poor health plants in existing landscape plan and planted new indigenous plants to increase density, biodiversity, and wildlife habitat. As part of the three-year plan, Humanscale will expand garden spaces specifically situated for local pollinators and endangered wildlife and will begin to transition to circular system for irrigation. By connecting the sprinkler line to the output from the rainwater cistern, the water demand for the garden will be 100% met with rainwater.
Humanscale’s facility in Fresno consists of a leased portion of a larger building. Humanscale has no control or influence over the landscaping.
02. HABITAT EXCHANGE
Beyond the facility, Humanscale actively contributes to the World Wildlife Fund (WWF). Humanscale CEO and Founder, Bob King, has been a member of WWF’s National Council for more than 15 years, and believes the non-profit is a natural extension of Humanscale’s mission.
King had an idea to restore a wild place to its natural existence before being exploited by commercial hunters and loggers. He selected the Eastern Plains in Cambodia for their rich ecological diversity and habitat of many endangered species. Since 2008, Humanscale has committed significant resources to the project, which focuses on the Phnom Prich Wildlife Sanctuary and the Mondulkiri Protected Forest.
03. LIVING ECONOMY SOURCING IMPERATIVE
Humanscale pursued the alternative compliance path.
PLACE PETAL LESSONS LEARNED
Humanscale’s Nogales location embraced its landscaping plan and goals by creating fun employee events around gardening. At Nogales’ Green Events, Humanscale employees break out into teams to assess and replace existing invasive or damaged plants with healthy indigenous varieties. Not only did this increase plant density, biodiversity, and habitat for wildlife, but it was also an enjoyable bonding experience for the Nogales team.
While completing the requirement of this Place Petal, Humanscale asked landscapers at each of its owned manufacturing locations to disclose the type of fertilizers they use. This led to the discovery that at the Piscataway location, a petrochemical based fertilizer was being used. Humanscale asked that landscaper to immediately stop using fertilizer until an acceptable 100% natural alternative was found.
water petal
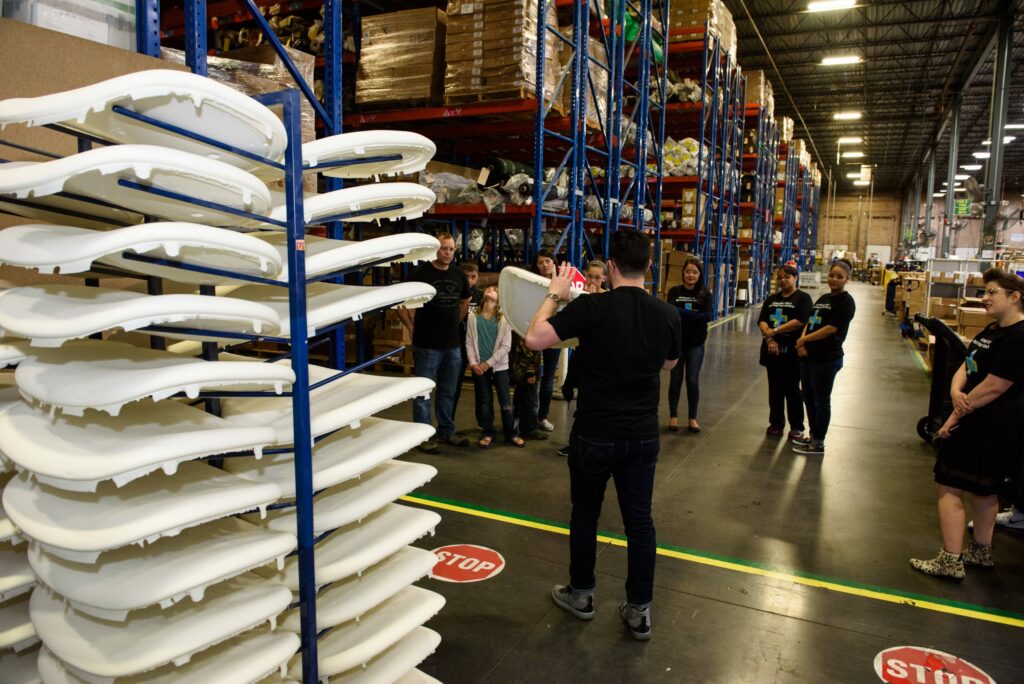
Water is our most critical natural resource and vital to life. Without care and attention, manufacturing operations could consume a significant amount of water. With that in mind, Humanscale is always seeking ways to reduce its consumption. The Sustainability team reviews water bills from local municipalities and water companies and tracks usage over the course of a year. The approach is iterative in nature – the company regularly look for ways to reduce consumption and use natural rain harvesting where feasible. The process water needs at Dublin, Nogales and Piscataway locations are met completely with on-site captured rainwater. As part of the three-year landscaping plans, rainwater will be used for on-site irrigation needs. By connecting the sprinkler line to the output from the rainwater cistern, the water demand for the garden will be 100% met with rainwater.
04. WATER FOOTPRINT IMPERATIVE
Very little water is used in the assembly of Humanscale products. In fact, water is only required onsite during the manufacturing of foam seat cushions for the seating line and in the powder coating of metallic parts.
At the Piscataway and Dublin locations, cushions are made of a two-part polyurethane, which chemically reacts in the mold. Water is used to regulate temperature for each of the two chemicals prior to being injected in the mold, as well as the mold itself. This ensures the chemistry will react the same way each time, allows the process to be controlled, and produces consistent quality parts. The foam machine is used for all Humanscale chairs requiring foam cushions. 100% rainwater is used for foam production, which is captured and re-used in the process. As part of its first LPC certification in 2016, Humanscale implemented an on-site rainwater harvesting system at the Piscataway location and have since implemented the same system at the Dublin location as part of the Living Product Challenge certified product expansion.
At the Nogales facility, process water is used in the powder coating metallic parts including seating bases, seating chassis mechanism parts, and aluminum monitor arm components. Parts are rinsed with water prior to coating to ensure debris has been removed from the surface. Water also helps prepare the surface to be coated with chemicals that assist in powder coat adhesion. Water is also used to dilute the chemicals involved with surface preparation. As part of the LPC certified product expansion, Humanscale installed an on-site rainwater harvesting system at the Nogales location in the Fall of 2020.
On site water annual use: | Dublin: 10.27 Fresno: 6,266 Piscataway: 5,064 Nogales: 5,039 |
Average cradle-to-gate water footprint for all final assembly locations: | 0.6 cubic meters of water |
water hotspots
- Injection molding
- Polyurethane, flexible foam
- Steel
- Glass fiber
- Polyurethane, rigid foam
05. NET POSITIVE WATER IMPERATIVE
Humanscale calculates the water footprint of each of its products through Life Cycle Assessment using the OpenLCA software with the most current version of the Ecoinvent database, version 3.6. LCA models followed established Product Category Rules to determine the scope and many assumptions. Data were pulled from a number of sources, including production Bill of Materials, ERP data about vendor location and shipping method, and primary data for on-site energy and water consumption and waste. The system boundary started with point of extraction, included processing, shipping, manufacturing, and ended with final assembly by Humanscale. Through the use of recycled content, Humanscale substantially reduced its products’ water footprint. To maintain net positivity for water, the company launched a variety of handprinting campaigns in which water was conserved. Through the installation of high efficiency light bulbs, and solar panel systems, Humanscale was also able to conserve significant electricity that also resulted in a substantial water handprint.
WATER PETAL LESSONS LEARNED
Humanscale has installed rainwater harvesting systems at all owned manufacturing locations in order to eliminate the need for municipal water in the final assembly of its products. As part of three-year landscaping plans, Humanscale will connect sprinkler lines to the output from the rainwater cistern to lessen dependence on city water even further. Water demand for the garden will be 100% met with rainwater. These efforts will lower Humanscale’s water footprint, however, with the understanding that much of its products’ water consumption occurs upstream of the facilities. By increasing the amount of recycled content in its products, the company can have a positive impact to the upstream water footprint.
ENERGY petal
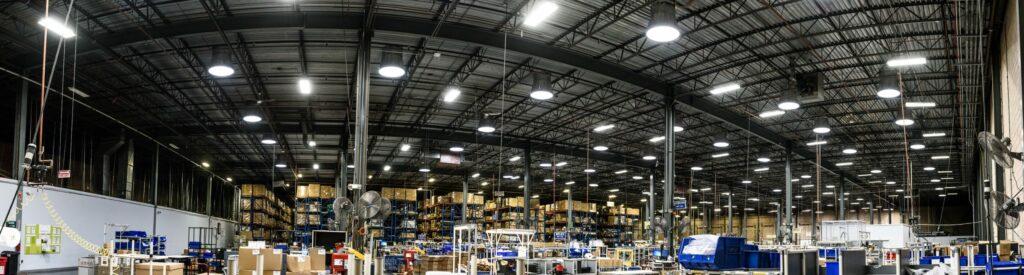
Energy consumption is a significant contributor to greenhouse gas (GHG) emissions, so Humanscale considers measuring and reducing them a major indicator of company sustainability. The company keeps careful track of energy used during production and looks for ways to use less. The sustainability team tracks monthly energy use and matches it against the anticipated annual goal, and uses cloud-based software to easily examine energy use, intensity, and reductions based on data from previous years. Each year, Humanscale’s executive team reviews annual total energy use and progress. The company continually looks for opportunities to reduce usage globally.
Main uses for energy at the facility of final assembly include natural gas for heating, and electricity for lighting, machinery, processing, assembly power tools, a central air compressor, and air conditioning. Whole building energy use is tracked annually. Energy use was allotted to the each of our products’ production based on the proportional amount of total production from the facility, calculated by total weight. At each manufacturing facility, sky lighting and LED lighting have been installed to reduce energy consumption. At the largest manufacturing facility, electricity is generated on-site by a 775.5 kilowatt photovoltaic system.
06. ENERGY FOOTPRINT IMPERATIVE (CORE)
Electricity, natural gas, and propane are the energy sources at Humanscale’s manufacturing facilities. Electricity provides power for air conditioning, lighting, air compressors that drive hand tools and assembly mechanisms, machinery including sheet metal presses, automated textile cutting machine, industrial sewing machines, CNC router and foam molding equipment, a machine shop, and computing equipment. Natural gas is used to provide heat and hot water. Propane is used to fuel forklifts.
On site energy annual use: | Piscataway: 2,731,549 kWh Fresno: 197,547 kWh Dublin: 657,289 kWh Nogales: 2,531,935 kWh |
Average cradle-to-gate footprint for all final assembly locations: | 19.7 kg oil equivalent |
ENERGY HOTSPOTS
- Market for injection molding
- Transport, freight, lorry 16-32 metric ton
- Market for polypropylene, granulate
- Market for glass fiber
- Market for polyurethane, flexible foam
07. NET POSITIVE ENERGY IMPERATIVE
Humanscale calculates the energy footprint of each of its products through Life Cycle Assessment using the OpenLCA software with the most current version of the Ecoinvent database, version 3.6. LCA models followed established Product Category Rules to determine the scope and assumptions. Data were pulled from a number of sources, including production Bill of Materials, ERP data about vendor location and shipping method, and primary data for on-site energy and water consumption and waste. The system boundary started with point of extraction, included processing, shipping, manufacturing, and ended with final assembly by Humanscale. Through the use of recycled content, Humanscale has been able to substantially reduce its products’ energy footprint. To maintain net positivity for energy, the company launched a variety of handprinting campaigns in which energy was conserved or produced through renewable energy sources. These included installing high efficiency light bulbs, hosting on-site tire pumping events, encouraging and tracking employee handprinting actions, and sponsoring the installation of solar panel systems at non-profit organizations.
ENERGY PETAL LESSONS LEARNED
Through Life Cycle Assessments, Humanscale observed that most of the energy required to manufacture its products occurs upstream during material extraction and pre-processing. This makes the product design process even more important. For example, creating virgin aluminum requires significant amounts of energy. It has been much easier to source recycled aluminum to be used in die cast parts, so product designers aim to use die cast aluminum instead of extruded aluminum parts. As Humanscale continues to increase the amount of sustainable material and recycled content in products, the company can have a substantial impact to the products’ overall energy footprint.
HEALTH + HAPPINESS petal
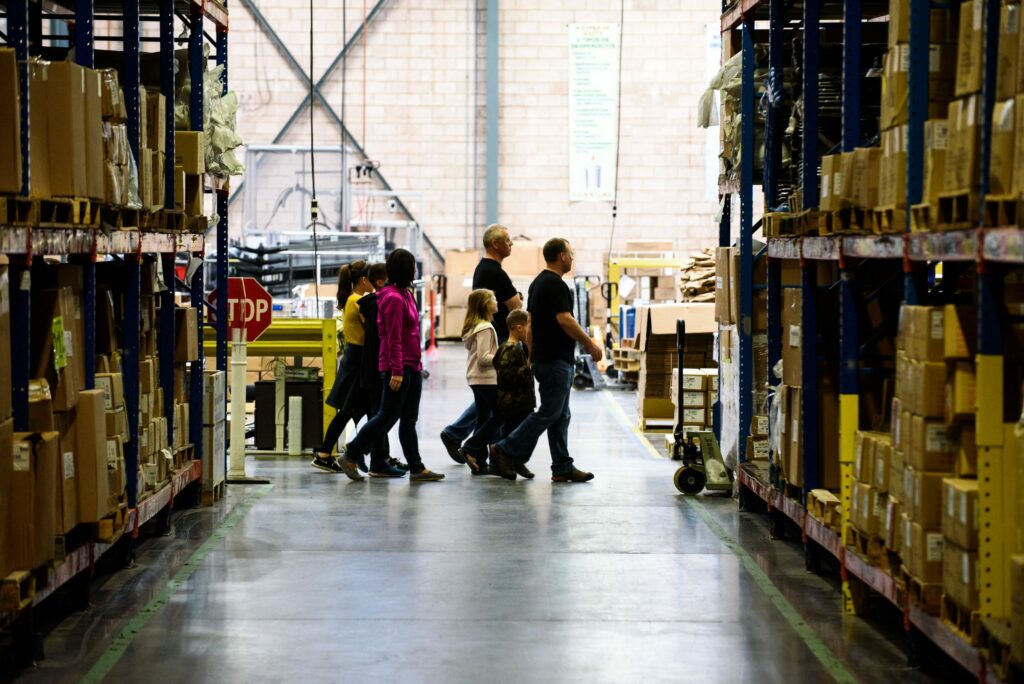
Humanscale provides its employees with numerous opportunities to access nature, natural light, and programs that encourage an active, healthy lifestyle. In addition, all employees have access to ergonomic chairs, lighting and desks. As a result of the Covid-19 pandemic, most office employees have transitioned to working from home. In an effort to continue providing employees with a healthy and ergonomic working environment, Humanscale offered all employees a significant discount on work-from-home ergonomic office furnishings.
Humanscale focuses on creating a more comfortable place to work. This is reflected in the products it manufactures, which are aimed to keep people in healthy, natural body postures. Its products aim to fit technology to the human body, instead of the other way around. Humanscale has pioneered workplace design that promotes healthy movement. Helping to create an active workspace, Humanscale’s products are intelligent designs built on ergonomic principles, each helping to support users build more activity into their daily routine for long term health and well-being.
All of the company’s products go hand in hand with this concept of active, natural movement. Humanscale work tools and its essential workstation make a workplace active simply by their design, and with intuitive features, the products themselves are active, too.
By using these products, at the office or at home, the user enjoys benefits of the active workspace such as improved health and productivity. Humanscale’s designs create a workspace that automatically adjusts to the individual user’s work style, embracing each person’s unique approach to work.
All Humanscale products are LEVEL 3 certified which examines multiple attributes of each product, including water use, energy use, emissions, chemicals, waste, and design for environment. LEVEL is audited by a third party, and reviews the product itself, the manufacturing facility, and the company as a whole.
Each product is also SCS Indoor Advantage™ Gold certified, ensuring it meets strict indoor air quality chemical emission limits. Humanscale tests all major product lines to confirm they do not off-gas and meet SCS IAQ Gold.
08. RED LIST IMPERATIVE (CORE)
The Path chair was designed using materials free of toxins including the Red List of Chemicals, considered the “worst in class” materials, chemicals and elements that are hazardous to humans and the environment.
DECLARE ID: HSC-0064
09. TRANSPARENT MATERIAL HEALTH IMPERATIVE
As an organization, Humanscale is committed to using healthy materials. Understanding and being transparent about what is in materials is the first step to driving change. Humanscale is constantly working with suppliers at all levels to identify and evaluate the ingredients in products, packaging, manufacturing processes, and key partners in the supply chain.
It is Humanscale’s mission to publish thorough and accurate lists of material ingredients for all products. Like nutritional labels on food, standard formats to publish the ingredients are used: Health Product Declarations (HPDs) and Declare labels. Humanscale is committed to informing and educating customers about the contents of its products, so they can make the best decisions possible.
Once identified, each ingredient is evaluated for its impact on people and the environment. Humanscale systematically replaces chemicals of high concern with safer alternatives.
Full material transparency required the company to change business practices, which requires a strong commitment, but is now part of the normal way of operating. Humanscale spent years thoroughly researching all of its materials and hired a full-time materials scientist to lead the effort, third-party auditors to ensure the accuracy, and a toxicologist to review the results.
10. HUMAN THRIVING IMPERATIVE
Humanscale focuses on creating a more comfortable place to work. This is reflected in the products it manufactures, which are aimed to keep people in healthy, natural body postures. Its products aim to fit technology to the human body, instead of the other way around.
It is also reflected in the manufacturing facility, which provides numerous opportunities for the employees making the products to have access to nature, natural light, and programs that encourage an active, healthy lifestyle.
materials petal
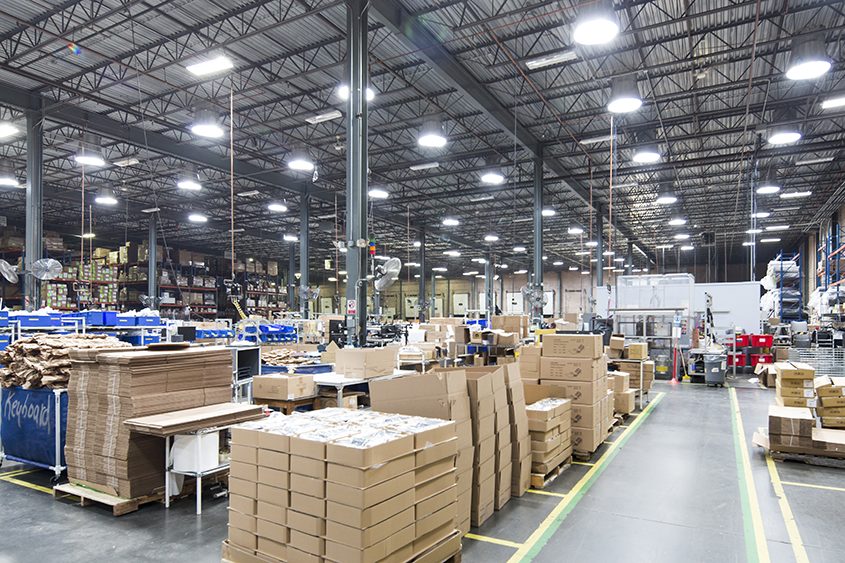
Humanscale’s Design for Environment process for all new product development is designed to comply with the requirements of the materials Petal. The sourcing, durability, and end of life treatment of materials is systematically reviewed prior to manufacturing launch. Humanscale also mandates all wood components and corrugate meet FSC CoC standards.
Humanscale had to evaluate the usage of Single-Use Plastic in its packaging due to imperative 12 and is developing SUP-free alternatives including reusable packaging and compostable materials. The wide range of products being certified, the nature of furniture logistics, and customer expectations of aesthetics and performance upon delivery make the removal of Single Use Plastic a very difficult challenge. The entire industry is looking for solutions, and Humanscale hopes to lead the way in this regard.
Additionally, the Net Positive Waste imperative pushed Humanscale to evaluate Zero Waste certification schemes and adopt many principles and strategies to bring diversion from landfill above 90% globally. Humanscale implemented upstream source reduction efforts to reduce waste from coming into the facility to begin with and improved separation of materials coming off production lines to reduce landfill contamination.
11. RESPONSIBLE INDUSTRY IMPERATIVE (CORE)
Humanscale follows FSC Chain of Custody guidelines and requires FSC-certified material in its certified Living Products. The Float tabletop is the sole wood product Humanscale certifies to the LPC, and all tops are FSC-certified.
Humanscale also ensures that packaging is either FSC-certified or 100% recycled and vets new vendors for these criteria.
As part of its supplier agreement, Humanscale mandates all vendors state compliance with the RMAP protocols. Additionally, Humanscale does not use materials that fall into other protected categories outlined in the Responsible Industry Imperative.
12. REGENERATIVE MATERIALS IMPERATIVE
Durability is one of the core tenets of Humanscale’s company philosophy. Creating the longest useful life product is the most beneficial and respectful use of the materials that are consumed to make it. Humanscale has industry-leading product warranties and test durability of products to the length of those warranties.
Humanscale also considers end of life and recyclability as part of its Design for Environment process. Full disassembly of the product is required in order to maximize potential recyclability. Materials and resins are selected based on their recyclability, and Humanscale has a program called BEAM (Building Equipment and Material) that assists customers in diverting their end of life products from landfill, whether that result is donation, resale, or recycling.
13. NET POSITIVE WASTE IMPERATIVE
Humanscale follows the principles of the True Zero Waste framework to reduce waste overall and increase diversion from landfill. Brought out by GBCI, “The TRUE Zero Waste certification system enables facilities to define, pursue and achieve their zero waste goals, cutting their carbon footprint and supporting public health.” Waste is considered in the Design for Environment program, which evaluates potential reductions of overall material use, scrap reduction, incoming packaging materials, and customer-facing packaging. An emphasis is made to reduce or eliminate Single Use plastic where possible. All facilities follow the same principles and guidelines, with adjustments to materials separated and process as needed.
Inside Humanscale’s manufacturing facilities, an evaluation is conducted to understand the sources of waste, the material nature of the waste, and the available reuse and disposal options for each within the framework of local laws and waste regulations. Once waste streams are identified, external vendors are contracted for pickup, and the material stream is separated using color-coded signs and bins to prevent disposal in landfill. All materials are separated with the aim of reuse or recycling prior to being thrown out for landfill waste. Vendors and internal material managers supply monthly volume amounts and diversion rate is calculated.
Humanscale’s specific waste program includes training of production and warehouse staff on the various material types that emerge as waste from daily operation and providing means for separating each material. The main streams of waste in our facilities are Pallet Reuse, Corrugated Cardboard, Pallet Scraps for recycling, Single Stream Recycling, Plastic Stretch Wrap, Scrap Metal, and Landfill. Signs and bins are placed as defined by each production line’s needs and are iteratively improved based on employee feedback.
Material handlers collect separated materials and bring them to a central waste collection point. There, materials are taken at specific times of day to their final disposal point, whether that is a baler, dumpster, pickup trailer or compactor. Only designated representatives may access the landfill compactors or dispose of materials in final collection points.
The Design for Environment program also prepares Humanscale products for reduced waste at the end of life. All products receive a Design for Disassembly and Recycling Evaluation. Designers and engineers review the products and identify components of differing materials that once assembled, cannot be separated. These components are suggested for redesign with a goal of full disassembly. The process also stresses specification of recyclable materials and provides instruction for disassembling and properly disposing of material waste at end of life.
As with other imperatives, waste is evaluated on a product-share basis.
Final percentages diverted from landfill: | |
---|---|
Metals: | 100% |
Paper and Cardboard: | 100% |
Soil and Biomass: | Not found in material streams |
All others, combined weighted average: | 90.6% |
Humanscale is creating targeted Waste Handprints where the Living Product Challenge is looking to make its biggest impact: the built environment. The BEAM (Building Equipment and Materials) Handprint Program connects facilities managers, purchasers, and office managers with certified diversion partners who assist in diverting waste from landfill at the end of life. Humanscale has seen that many building products from flooring, lighting fixtures, office equipment, and furniture are not disposed of properly and the default option is to have material taken to a landfill.
The BEAM program offers participants the opportunity to donate, recycle, or resell these materials and provides transparency back in the form of weight diverted from landfill and emissions prevented. The BEAM program is designed to scale as it does not accept only Humanscale material, but provides these diversion connections to any type of material in the built environment.
14. NET POSITIVE CARBON IMPERATIVE
Average cradle-to-gate footprint for all final assembly locations: | 61.0 kg CO2 equivalent |
CLIMATE HOTSPOTS
- Market for injection molding
- Market for steel, unalloyed
- Transport, freight, lorry, 16-32 metric ton
- Market for glass fiber
- Market for forging, steel
MATERIALS PETAL LESSONS LEARNED
The sources of embodied carbon in Humanscale’s manufacturing and supply chain are directly from energy use, leading the company to understand that giving preference to lower energy manufacturing process, and sourcing recycled material (for which extraction and initial processing has already been done) will significantly affect the carbon footprint. Packaging materials and transportation method have the next highest impact, which goes past the product design and into logistics.
EQUITY PETAL
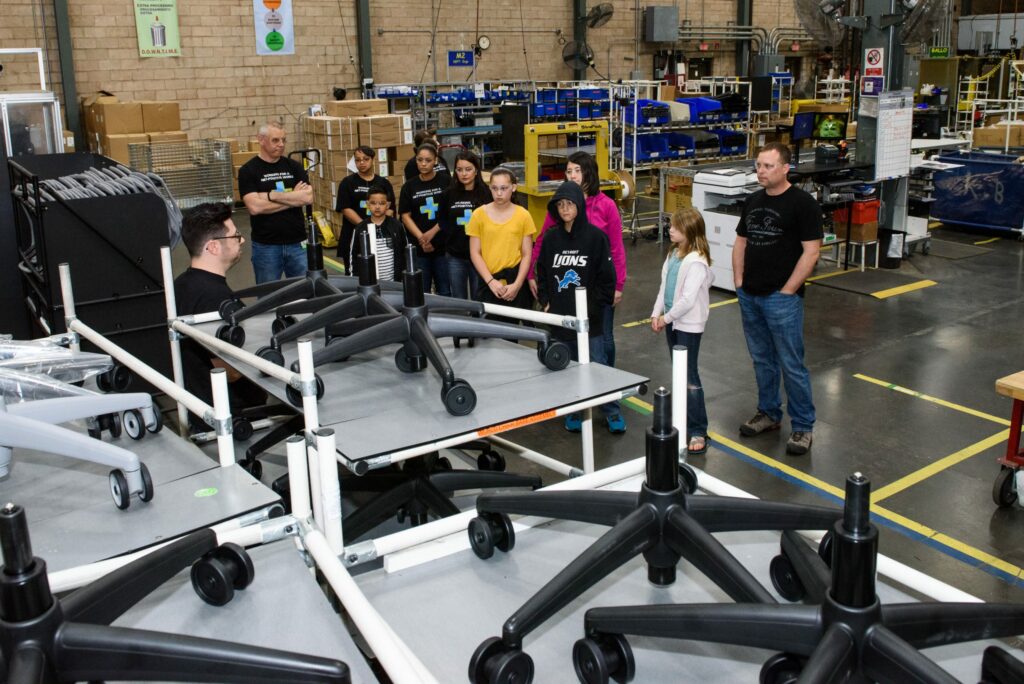
Humanscale understands that the impacts from the decisions made for its products and operations go beyond its offices and factories. It is part of a much bigger community; an ecosystem. Therefore, for every product the company makes, the impacts from the supply chain and the impacts on customers are all taken into consideration. The Ethical Supply Chain Core Imperative is useful to provide some high-level information of the risks, hotspots and relevant standards landscape. But it was just the very beginning of the ethical supply chain for Humanscale, which started an onsite audit program in 2019 to gain more first-hand information of its suppliers’ social and environmental performances, which will be important to form the bases of improvement and capacity building in the future. The JUST label also continues to present certain social and diversity issues to the management team and allows the company to continue conversations for transparency and improvement. Lastly, each handprint activity had social benefits. Through tire pumping events, drivers benefitted from free tire assessments and drove away with safer tire pressure levels; through campaigns that saved energy, individuals were able to save money on their electricity bills; and through supporting tree planting initiatives, national forests, which are valuable for a multitude of reasons, were reforested. Additionally, the organizations where solar panel installations were installed will save money and be able to better serve their communities and increase the impact of their cause.
15. ETHICAL SUPPLY CHAIN IMPERATIVE (CORE)
Humanscale has done supply chain mapping for its material transparency program. After identifying the top 10 suppliers and understanding their location and manufacturing operations, the team cross-referenced it with the system required by LPC and identified the following supply chain social risks.
After risk identification, the company reviewed its own supplier sustainability audit program and confirmed that all critical social risks have been assessed and audited onsite.
Country | GTAP Sector | Critical Social Risks |
---|---|---|
China | fmp | Labor Rights & Decent Work |
China | rpp | Labor Rights & Decent Work |
USA | omf | Labor Rights & Decent Work |
Mexico | rpp | Governance |
China | ele | Labor Rights & Decent Work |
South Korea | tex | Health & Safety |
Taiwan | omf | Health & Safety |
fmp = Manufacture of fabricated metal products, except machinery and equipment
rpp = Manufacture of rubber and plastics products
omf = Other Manufacturing: includes furniture
ele = Manufacture of computer, electronic and optical products
tex = Manufacture of textiles
See the Global Trade Analysis Project (GTAP) for additional information about goods and services classifications.
16. EQUITABLE INVESTMENT IMPERATIVE
In 2008, Humanscale began to work closely with the World Wildlife Fund (WWF) on a community and wildlife program that aims to restore and protect the Phnom Prich Wildlife Sanctuary in the Mondulkiri Protected Forest in the Eastern Plains of Cambodia. The initiative was a natural fit for Humanscale, as the company has always been concerned about the impact its operations have on biodiversity, and Founder and CEO, Bob King, has been a long-time supporter of WWF.
The program creates jobs within the local community as rangers maintaining the reserve – sometimes engaging the same people who had once been poachers. Crime is also reduced through the additional policing of illegal poaching. The land, which was once devastated from civil war, is being restored to the point that it can support the health and wellbeing of the local community. WWF works closely with the provincial government and the surrounding communities to address the challenges in the area, which include snaring, illegal logging, and poaching.
17. JUST ORGANIZATIONS
Humanscale’s Human Resources department gathered company-wide information about its employees and activities in order to pursue a JUST label. Information about employees in all regions of the world was evaluated. Countries with fewer than five employees were not included in the calculations since there was not a large enough population sample to represent diversity and equity issues. Information about worker happiness comes from an annual survey that Humanscale puts out to their employees to gain an understanding of employee satisfaction.
The process of obtaining a JUST label was an interesting learning experience for the company. Areas of key focus to their organization, such as animal welfare and employee happiness, were well featured. It also brought to light other areas where they can expand their focus. The JUST label was one of the factors that influenced the decision to expand parental leave in some locations. It caused additional discussions about gender diversity and company sponsored volunteering. Seeing the framework JUST used to evaluate different subjects was interesting and informative.
18. SOCIAL CO-BENEFITS IMPERATIVE
Humanscale has completed a variety of handprinting initiatives in order to have a net positive impact for its Living Product Challenge products. From tree planting to tire pumping, the company found it necessary to have a variety of handprinting actions in order to have a positive impact in all three categories; carbon, water and energy. Humanscale has been selective with the handprints it chooses to carry out to make sure that they create positive social change as well.
One impressive organization that Humanscale has partnered with is Green Light New Orleans. The nonprofit “invests energy in people by assisting New Orleans residents in person, one household at a time. Our volunteers install free energy efficient light bulbs, rain barrels and backyard vegetable gardens to demonstrate that a mass movement of individual actions creates a significant impact on our environment and community. We connect New Orleans residents to relevant, local opportunities and encourage individual actions so that everyone can benefit from a vibrant, resilient, and sustainable community.” The Executive Director and Founder of Green Light New Orleans, Andreas Hoffman says, “Green Light New Orleans has received thousands of applications for the energy-efficient light bulb program from residents of Jefferson Parish. Until recently, we were unable to install bulbs outside of Orleans Parish, but thanks to Humanscale’s support, Green Light can now help address Jefferson Parish residents’ needs for energy-efficient light bulbs.”
Besides reducing the CO₂ footprint of the city, the light bulbs will help reduce residents’ utility bills and will provide an opportunity to educate the community about other energy efficiency measures and Green Light’s other programs, which address other environmental issues such as healthy food access and stormwater management. The programs have been successful thanks to the efforts of thousands of volunteers. Humanscale’s support will provide more opportunities for volunteering and service learning, and will help create a strong sense of community through volunteers’ interactions with community members and community members amongst themselves.”
In fall of 2019, Humanscale supported the National Forest Foundation’s (NFF) 50 Million for our Forests campaign by sponsoring the planting of over 1,500 trees in an effort to restore forests in need and to promote carbon sequestration by trees. Through the planting of trees, the NFF is restoring America’s National Forests which have suffered from wildfires, invasive insects, disease breakouts and a plethora of other challenges. These forests are not just vital to the health of our environment by supporting ecosystems and habitats, stabilizing the climate, enriching soil, supporting biodiversity, etc., but are also invaluable to humans too. Among many other benefits, restoring these forests, ensures that they can continue to purify the air we breathe and the water we drink, and they have huge economic and recreational value too.
Humanscale has hosted multiple Tire Pumping Events during which employees and the public are invited to have their tires inflates (or deflated) to meet the proper pressure level sufficient for their tire and vehicle. Ensuring optimal tire pressure increases the fuel efficiency of vehicles. In addition to the environmental handprint, greater fuel efficiency saves the driver money, and properly inflated tires lowers accident risk and prevents premature wear to tires.
Most recently, Humanscale has sponsored the installation of solar panel systems at nonprofit organizations. Though our partnership with RE-volv, deserving nonprofits are able to save money on energy bills and better serve their communities. So far, Humanscale has sponsored the installation of solar panel systems at an animal shelter, a housing, support, and services center for people with autism and at an affordable housing organization that assists low-income and rural residents.
EQUITY PETAL LESSONS LEARNED
The Equity Petal has a strong emphasis on social impact, which can be harder to define and measure. Both the JUST label and the supplier assessments have given us a deeper understanding of the influence we have on social issues. Unlike addressing energy or water use which can be solved by changing equipment, social impact requires engagement from many individual people on many levels in many locations. It seems to be most effective not to approach improvement as a series or projects, but as culture change – open to dialogue and influenced by those who are affected.
beauty petal
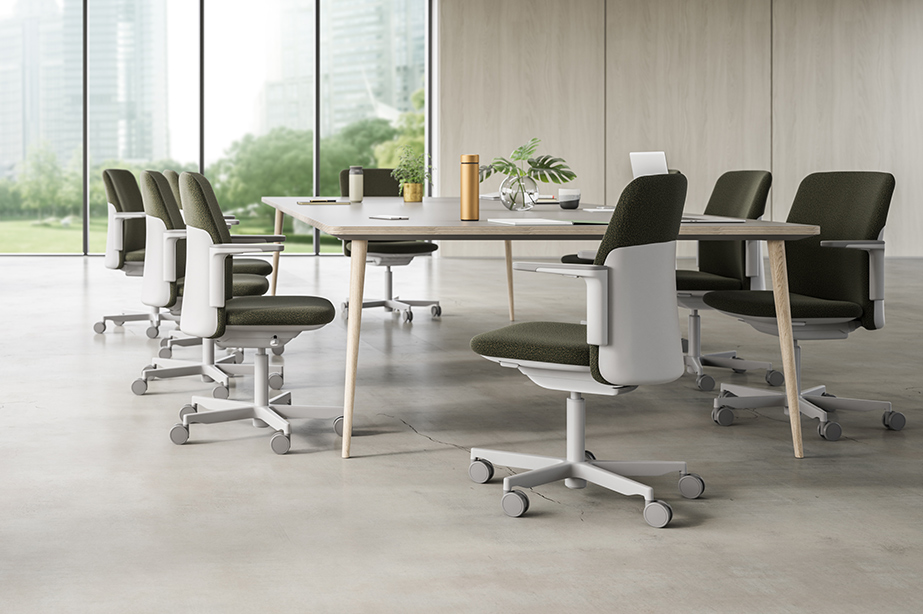
19. INSPIRATION + EDUCATION IMPERATIVE
Humanscale manufactures products for the workplace environment with the aim of making “a more comfortable place to work.” Working in uncomfortable or unhealthy postures is known to lead to long term health issues. Humanscale believes that work tools and technology should fit the human body, rather than the reverse. The in-house Design and Ergonomics teams work together to ensure that all products are developed to optimize the ergonomics and provide maximum health benefit to the user. The Path chair went through this standard consideration during the product development process.
LPC PAGE URL: https://www.humanscale.com/about/living-product-challenge/
20. BEAUTY + SPIRIT IMPERATIVE
Humanscale’s design philosophy can be illustrated by this quote by Niels Diffrient: “The best designs in the world are based on purpose and function. When a design solves a functional problem as simply and elegantly as possible, the resulting form will be honest and timeless.” Simple and elegant solutions can seem obvious once they have been defined, but they take a concerted refinement effort to achieve. Based in the New York headquarters, Humanscale’s Design Studio works hard to ensure that every product is simple and elegant enough to be considered beautiful. Their efforts have been acknowledged by numerous design awards, including the Red Dot award – possibly the most prestigious design award worldwide.
BEAUTY PETAL LESSONS LEARNED
Humanscale always aims to create timeless, simple, beautiful products. It’s interesting to realize that this also makes the product most sustainable, since people who love their products will care for them and use them for as long as possible, and therefore use less resources in making new products.
SUMMARY OF PROCESS AND BENEFIT OF PURSUING LIVING PRODUCT CHALLENGE
The Living Product Challenge provided Humanscale with a good framework for the company to evaluate when its products are net positive, and in which ways. This framework aligned internal teams around a unified and wholistic understanding of sustainability. When Humanscale achieved the Living Product Challenge for its first two products in 2016, the company noticed how exciting it was for many of its employees that Humanscale manufactures and leaves the world better off in a measurable way. Expanding this program to include 24 additional products and to all manufacturing locations was a big undertaking but a natural next step for the company. Humanscale’s internal global teams were excited and rose to the challenge, expanding its sustainability program by, among other things, pursuing the JUST label for each manufacturing location, installing rainwater capture systems so that all water used in final assembly is provided by rainwater harvested on-site, and receiving third party verifications for its product Life Cycle Assessment (LCA) reports. By assigning tasks to different teams, the effort was more evenly spread out across the company and departments felt greater ownership of the work that Humanscale was doing—because everyone had a role to play.