The stated goal of the program, building, and site development was to promote a healthy working environment where Google employees enjoy coming to work. The project encompassed a full tenant improvement fit-out. The building houses office, office support, and amenity spaces.
The project was intentionally designed to prioritize flexibility. Lean design strategies, including modular systems for meetings rooms, are used to accommodate rapidly changing tenants and flexible working conditions. These design strategies, rooted in adaptability and functionality, have resulted in lower renovation costs and significant carbon savings.
Additionally, the team used carbon-based materials selection and procurement processes. By prioritizing recycled and sustainably harvested materials, the team was able to further reduce the embodied carbon of the project.
Vital Stats
Certification Status | Zero Carbon Certified |
Version of LBC | 3.1 |
Location | London, United Kingdom |
Typology | Renovation |
Start of Occupancy | June 2016 |
Owner Occupied | No |
Occupancy Type | Office |
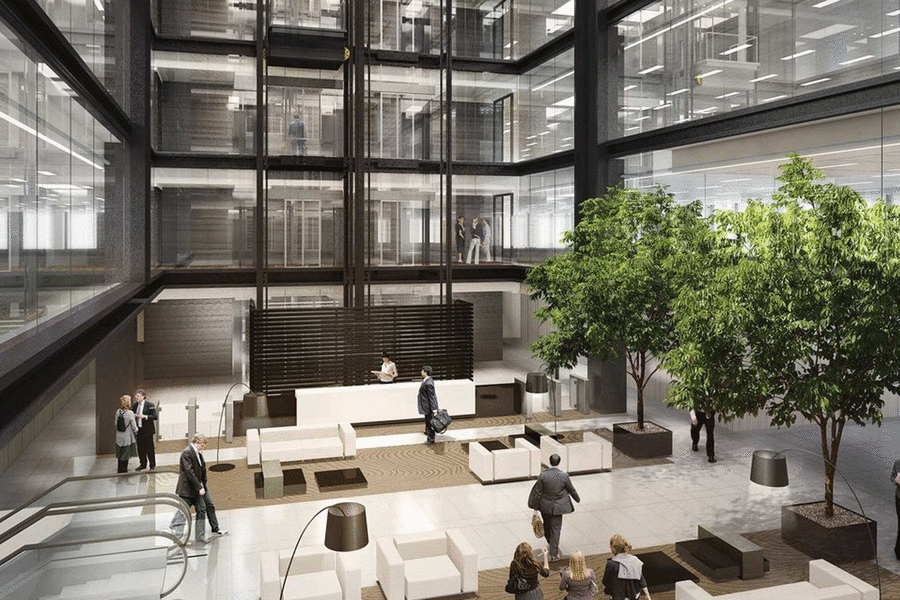
Owner | |
Project Manager | Phillip Putman & Stephen Adams – CBRE |
General Contractor | ISG |
Architect | Allford Hall Managhan Morris (AHMM) |
Mechanical Engineer | Cundall |
Electrical Engineer | Cundall |
Lighting Design | AHMM / GIA |
Plumbing | Cundall |
Commissioning | Facility Performance Consulting |
Sustainability Consultant | Hilson Moran |
Acoustics | Sandy Brown |
Test Lab Design | Arup |
Healthy Materials Consultant | Mott Macdonald |
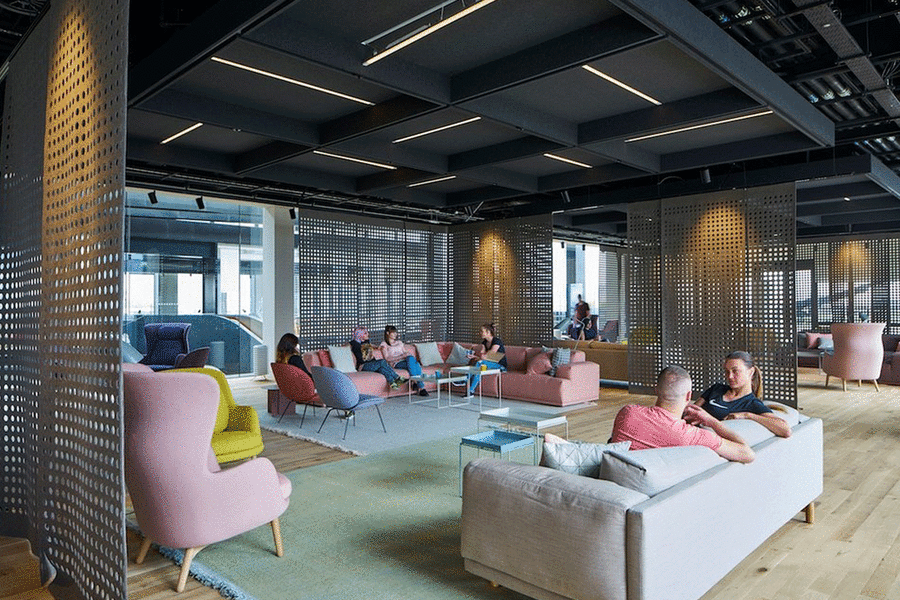
Embodied Carbon Reduction
The embodied carbon of this project is 12,850 metric tons of carbon dioxide equivalent, compared to a baseline project of equivalent material type, function, energy performance with an embodied carbon of 15,450 metric tons of carbon dioxide equivalent. The project as built represents a 16.8% reduction in embodied carbon from the baseline.
The team achieved two primary goals to reduce the embodied carbon of the project: use of low-carbon procurement, and use of low-carbon building design and construction.
Strategies for low-carbon procurement included: maximizing recycled content, local sourcing of materials, and reusing existing building materials and furniture where possible.
Low-carbon design and construction strategies included: design for reuse, optimization of lifespan and performance, recycling construction waste, and use of a carbon budget for construction emissions.
Procurement Strategies
The team employed the following strategies related to low-carbon procurement:
- Low-carbon materials, high recycled content: the team followed BREEAM requirements for low-carbon responsible material sourcing, and all timber elements FSC/PEFC certified.
- Local sourcing: most project materials were sourced from within a 500 mile travel distance.
Design & Construction Strategies
The team fulfilled the following metrics and strategies related to low-carbon design and construction:
- Design for reuse: 27% of components (by cost) for the interior fit-out can be dismantled and re-used for the same purpose (not down-cycled), reducing likely end-of-life impacts.
- Optimize lifespan: the project incorporated a modular, flexible system for private video conferencing booths and small meeting rooms, that can easily be assembled, disassembled, and moved for future flexibility.
- End of life/recycling: the project team specified 100% recyclable materials for the fit-out, and incorporated mechanical fasteners wherever possible. All metal elements on the project can easily be reused or recycled. Most steel on the project is bolted, rather than welded to maximize the possibility of later reuse. The Jack interior partition system, a unique feature of this project, was designed such that it can easily be disassembled and reused in a new configuration, to allow the occupants maximum flexibility for future growth and change.
- Construction phase impacts: site energy use and waste were tracked during the construction phase. The site energy use was approximately 22% less than general good practice. Furthermore, no timber waste was generated on-site, and 98.1% of construction waste diverted from landfill
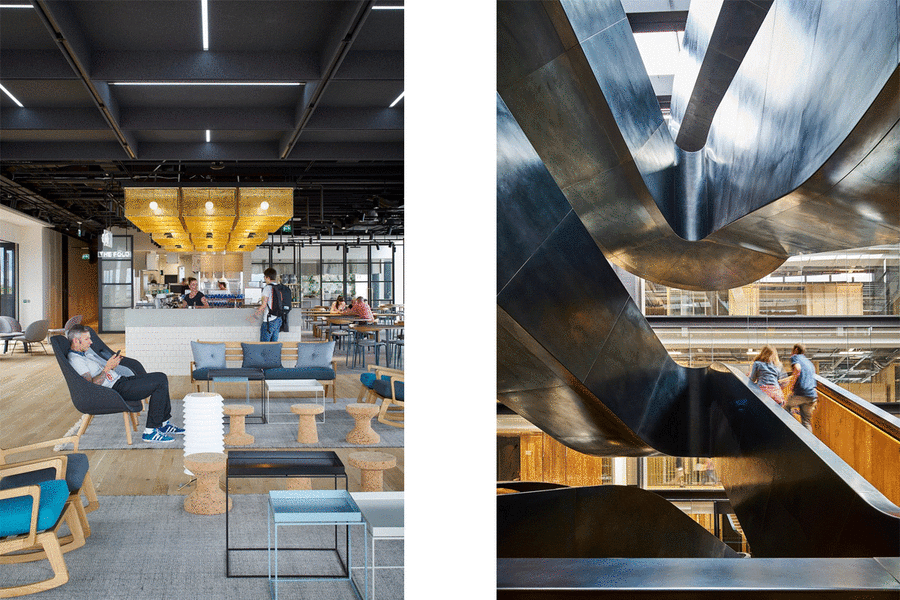
Energy Efficiency
Building Type | Existing Building |
Required EUI Reduction | 30% |
Actual EUI Reduction | 47% |
Zero Energy Performance
Renewables Location | Off site |
Percentage of Energy from District Steam Purchased | 37.3% |
Percentage of Electrical Energy Purchased | 62.7% |
Lighting
Lighting design incorporated LED overhead to reduce energy use. Finishes were selected to enhance visual comfort. Daylight was used wherever feasible with a minimum of one daylight control zone at each building facade, with continuous dimming ballasts or dimmable drivers in all regularly occupied spaces within that zone.
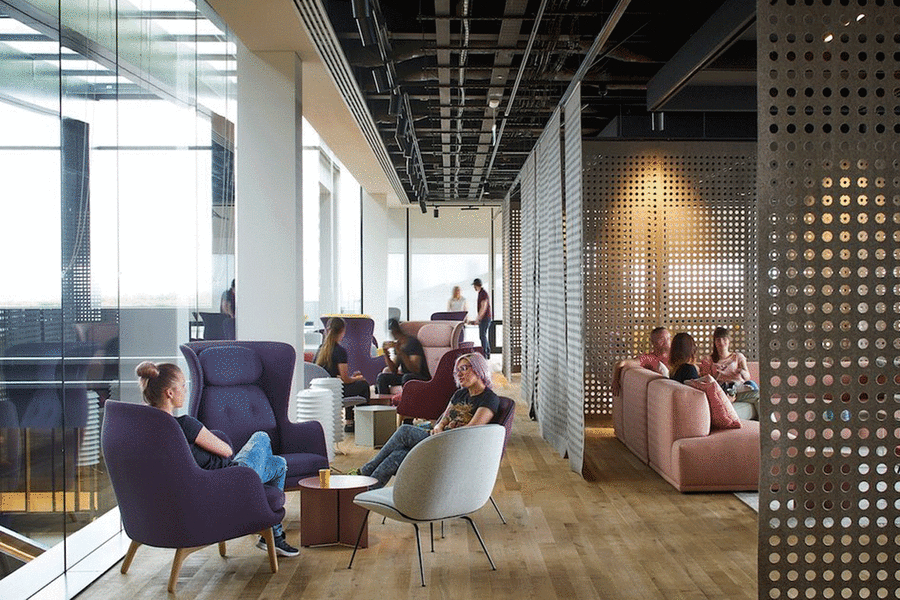
Project Leadership and Story of Project
Visit https://blog.google/outreach-initiatives/sustainability/andreas-gyr-living-future-hero/ to learn more about the project.