VITAL STATS
Certification Status | Living |
Version | 3.1 |
Location | Portland, OR |
Typology | Building |
Gross Building Area | 58,000 SF |
Start of Occupancy | December 2021 |
Occupancy Type | Commercial |
Number of Occupants | 250 |
PROJECT TEAM
Owner | First and Pine LLC |
General Contractor | Walsh Construction Co. |
Architect of Record | ZGF |
MEP Engineer | PAE |
Interior Designer | ZGF |
Civil Engineer | KPFF |
Structural Engineer | KPFF |
Landscape | ZGF |
Green Building Consultants | Brightworks Sustainability and Integrated Eco Strategy |
Lighting Consultant | LUMA |
Water Systems Designer | Biohabitats |
Development Management | Edlen & Co. |
Real Estate Partner | Apex Real Estate Partners |
PLACE PETAL
01. LIMITS TO GROWTH
The PAE Living Building calls the Old Town neighborhood of Portland, Oregon, home. It is located on a light-rail line just blocks from the Willamette River and within walking distance from the heart of the city. The building stands on the site of the former 1883 Reid’s Block building demolished in the mid-1900’s. For nearly a century, the site was vacant or a surface parking lot. Home to one of the best collections of cast-iron architecture on the west coast and part of the Historic District, the area boasts many buildings over 100 years old, and is a fitting place for a structure aiming to last 500 years.
02. URBAN AGRICULTURE
As an urban building, the building integrates urban agriculture two ways: within the sidewalk landscaping, and plants on the fifth floor deckony, a portmanteau of the words “deck” and “balcony.” However, both have proven difficult to maintain. The fifth-floor amenity hosted seasonal herbs and plants with an automatic drip irrigation system. Even so, it was found that a dedicated green thumb is needed to keep the garden flourishing. On the ground level, blueberries, native ornamental grasses, shrubs, and street trees intended to bring changing colors and texture to the street. Unfortunately, these plants did not survive through the first winter as pedestrians, motorists, and vandalism took their toll. True to the spirit of the Living Building Challenge, the tenants in the building seized a new opportunity: a colony of bees now live in a hive with several honeycombs on a rooftop apiary.
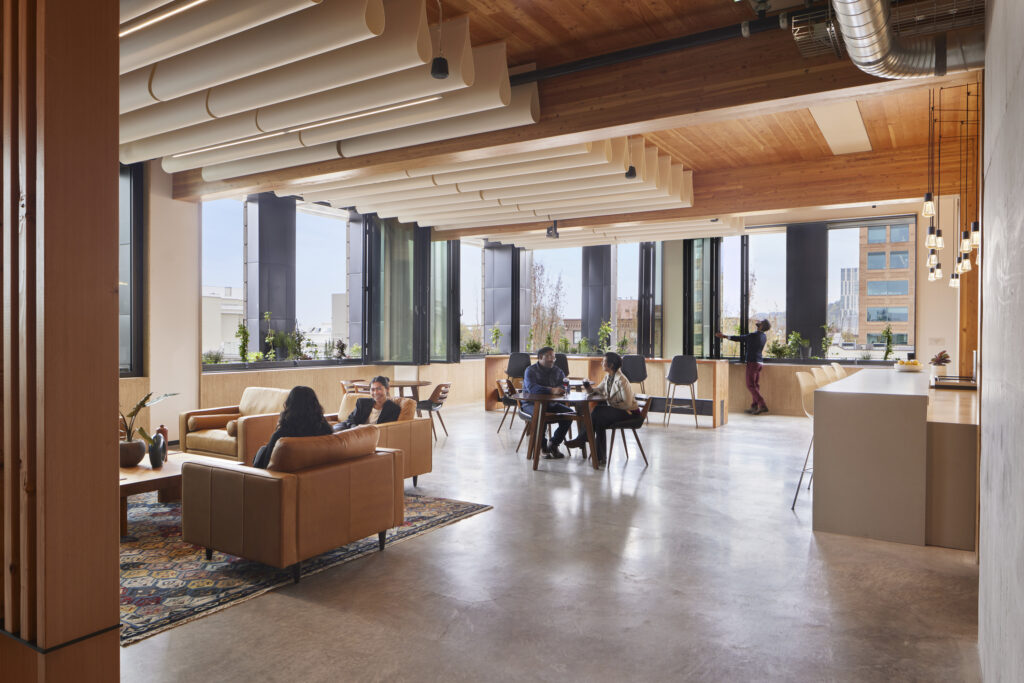
03. HABITAT EXCHANGE
The design and ownership team explored options to partner with local land trusts to preserve habitat within the project region. Surprisingly, there was a limited number of local opportunities, and it was not possible to find a solution that aligned with the requirement as well as the team’s aspirations. Thankfully, the team was able to contribute to the ILFI habitat preservation program.
04. HUMAN-POWERED LIVING
The downtown Portland location for the PAE Living Building was deliberately chosen for its walkability and transit connectivity, and parking was not required for this urban core location. Adjacent to the central business district, the building occupants have access to light rail and bus lines within two blocks and the location boasts a walkability score of 98. There are dedicated bicycling paths within one block and the project includes indoor storage for 40 bikes along with showers and changing rooms.
WATER PETAL
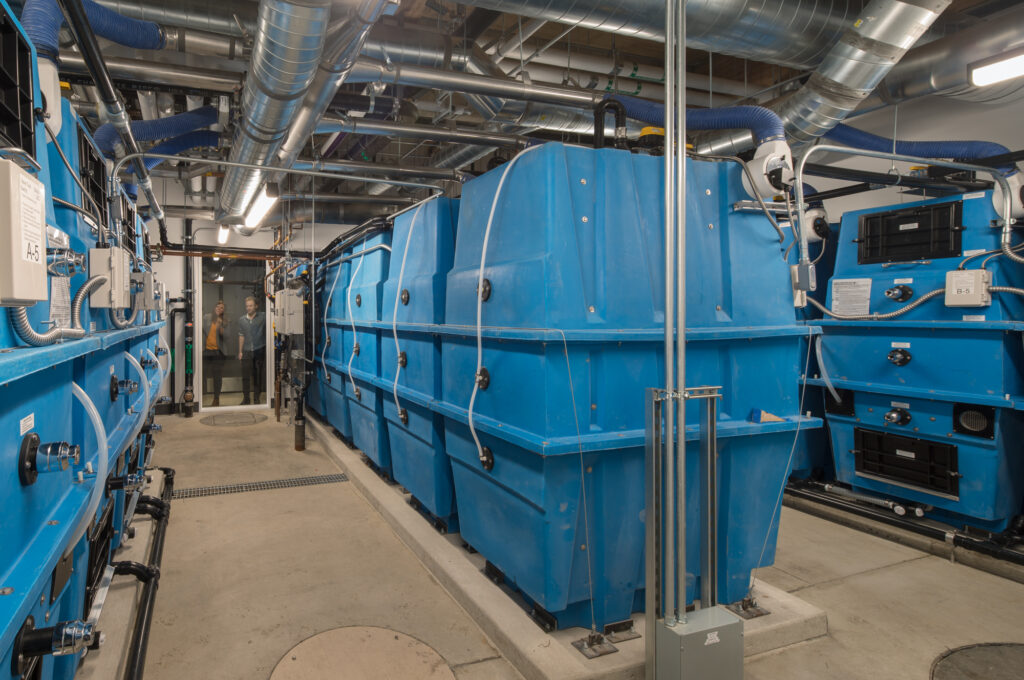
05. NET POSITIVE WATER
The PAE Living Building meets the Net Positive Water Imperative using several unique systems. From the first-ever multistory vacuum-flush toilets to fertilizer, the design team created innovative ways to harvest and harness rainwater.
- All potable demand from rainwater is collected from the roof, stored in a 71,000-gallon cistern, and then integrated into the building’s water needs.
- Before rainwater harvesting, there is a 73% water savings over a typical building of this kind built to code.
- Composting toilets are used on all floors reducing the blackwater waste stream.
- Wastewater, mostly greywater, is treated and reused onsite mostly for toilet flushing and irrigation. Due to the site’s poor soil infiltration and a high-water table, the project uses an exception for disposable graywater, and the building has the ability to connect to neighboring systems and has the capacity to rely on city’s sanitary system for any overflow.
- The first-of-its-kind multistory vacuum flush compostable toilets reduce water use and transform waste into a rich nutrient source. The vacuum-flush composting system has significant advantages over gravity flush systems, and the PAE Living Building incorporates significant lessons learned from another Living Building, the Bullitt Center in Seattle, Washington. Using 90% less water than a typical water closet, it boasts other sustainable advantages such as:
- The vacuum flush allows better management of the composters—waste can be routed to specific composters, which helps them rotate for optimum operation and they can be individually taken offline for maintenance.
- The pumped system incorporates a fallback option to send the unprocessed nutrients to the city sanitary system if a system-wide maintenance event occurs or the compost bins are unavailable.
- There is flexibility in piping because the waste lines are not required to slope.
- There is flexibility in composter placement because the effluent is pumped, rather than gravity drained. The material distribution system included controls to dose each of the 20 composters equally over time. Unequal loading of compost bins is a frequent problem for large foam flush systems that connect water closets and compost bins directly and has led to failures of composting systems in the past.
- The vacuum flush allows better management of the composters—waste can be routed to specific composters, which helps them rotate for optimum operation and they can be individually taken offline for maintenance.
- Urine is diverted through semi-waterless fixtures and direct piped to an underground collection tank. In fact, about 8,000 gallons of urine per year is diverted to create liquid and powder fertilizer, an innovative first for commercial buildings of this type.
- The urine is the feedstock for a distillation process that captures the nutrients such as phosphorus and ammonium bicarbonate. After treatment, a clear liquid fertilizer solution with a high Ph, 6% ammonium-N, and phosphorous-rich is sold as retail-grade plant fertilizer.
ENERGY PETAL
06. NET POSITIVE ENERGY
The PAE Living Building is crafted to achieve net positive energy outcomes while prioritizing occupants’ comfort. This is accomplished through a comprehensive and multifaceted strategy.
As a first step, energy efficiency started with load reduction strategies and then applied simple but innovative heating, cooling, and ventilation systems. The team was able to optimize the building’s envelope, then proceed to design the internal loads, followed by the IT infrastructure and lighting design, and, finally, finish the design with the radiant systems. Specifically:
- The envelope was optimized by keeping the window-to-wall ratio to no more than 30% on any façade with operable, double-paned windows and fiberglass frames with special considerations for air tightness and insulation.
- Plug loads and lighting power were limited as part of the energy reduction plan. As a result of these systems and the passive-first design, the HVAC system could be simplified allowing the team to reach their goal of small, exposed ducts to highlight the rich mass timber interior.
- Radiant floors are the primary heating and cooling. Hot or chilled water is delivered through a two-pipe system based on the average outdoor temperature. The floors provide about 2/3 of the total heating and cooling capacity and it essentially “disappears” into the floor and operates as a slow base-load handling system.
- The dedicated outside air system provides ventilation air to the spaces through heat recovery systems located in the ceiling on each floor.
- There are six air source heat pumps on the roof of the building. This is a significant evolution from buildings like the Bullitt Center, which used 26 400’ft deep closed loop wells in its ground source heat pump system. While ground source heat pumps are still highly efficient and effective solutions, the air source heat pump system produces nearly the same efficiency at a fraction of the cost. This was a key element to making the developer-led proforma work.
The systems together brought the energy-use target modeled to about 19.5 kBtu/sf/yr with the actual operating EUI to about 16.1 kBtu/sf/yr.
In adding solar panels to the project, designers ran into an issue: the constraints of the Historical District meant insufficient space was available to reach 105% of the energy needs of the building because solar panels could not be visible from the street, and the utility’s grid could only allow minimal feedback.
The constraints ultimately led to solutions that improved the overall project.
Through the local community and an idea from the contractor, Walsh Construction Co., a clever solution presented itself: PAE built about 215 kW of solar panels on an affordable housing development a few miles down the road. PAE was then able to donate 60% of the PV panels and a boost of onsite energy at no cost, while PAE retains the Renewable Energy Credits.
- The PV was installed in an east-west “accordion” pattern which maximizes production, enables drainage, and flattens the power production curve, making the array more utility-friendly.
- A 280-kWh battery and microgrid system is used to buffer the peak production and stay within the 50kW back-feed limit set by the utility. The microgrid further enables the building to interact with the grid as needed. The building can be run fully off grid for about 100 days in the summer.
- The PAE Living Building has a net energy demand onsite and purchases renewable energy from the grid for this.
HEALTH AND HAPPINESS PETAL
07. CIVILIZED ENVIRONMENT and 08. HEALTHY INTERIOR ENVIRONMENT
PAE, part owner and anchor tenant, is committed to providing a healthy and productive environment to its staff while also recognizing the financial value of such an environment.
If occupying a Living Building results in staff being just 1% more productive, the firm would essentially break even on a return for investment. At a 2% increase in productivity, PAE would even generate a surplus. There is much research that indicates that well-lit, biophilic work environments can significantly enhance productivity, reinforcing the business case for such workplaces. Simply put, running PAE out of a Living Building that prioritizes the health and well-being of its occupants bolsters the firm’s financial stability while aligning with its core mission.
In aiming to increase daylight and ventilation in a constrained urban space, the optimal solution involved centrally locating the building’s core to maximize occupied space near windows. To enhance daylight penetration, perimeter beams on the south and north facades were positioned above the floor, allowing windows to extend all the way to the ceiling as they do on the east and west facades.
The team went into construction right as COVID emerged in early 2020 prompting immediate concerns about proper (and future-proofing) ventilation against airborne illnesses. Upon inspection, the engineering teams were pleased to discover that the existing systems were already sufficient and exceeded standards for natural ventilation.
After occupying the building for several seasons, the team realized that it would also be an even better measure to build in outdoor air quality sensors and monitors in the case that poor air quality is happening from the outside and not just the inside.
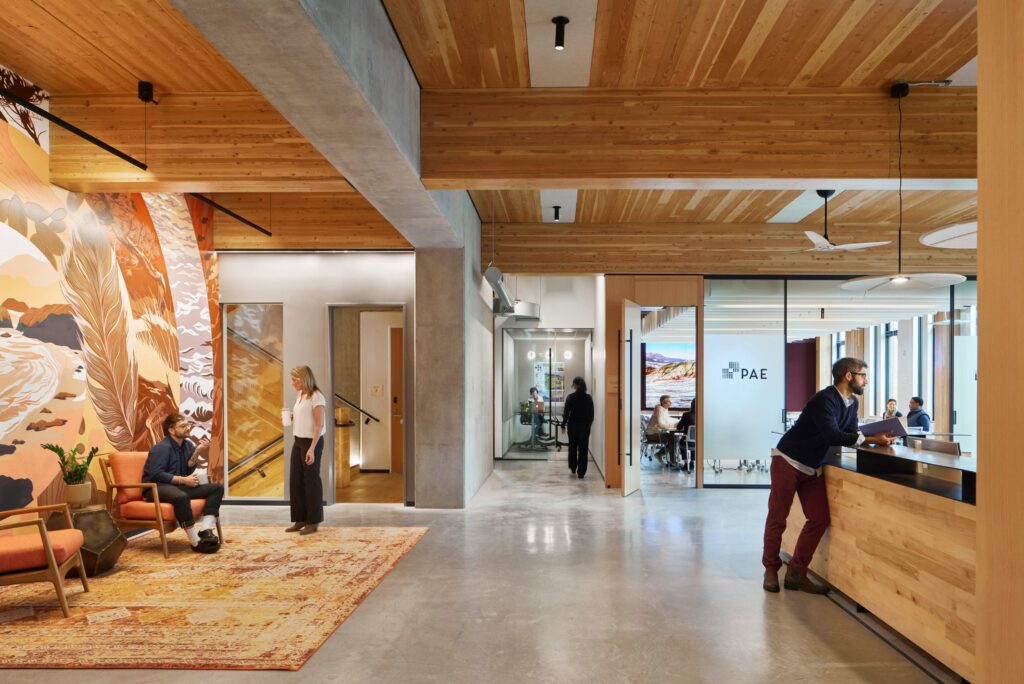
09. BIOPHILIC ENVIRONMENT
The fifth floor, open air deckony offers the most dramatic example of a multi-sensory biophilic environment of any space within the PAE Living Building. From the visual connections to the river and mountains, the fresh smells from plants growing on the exposed sills, the motion of leaves on the surrounding trees, the sounds of the bustling city, the feeling of lively air currents moving through the space, being immersed in glowing sunlight, and a sense of excitement that comes with a bird’s eye view, the deckony puts biophilia in full bloom.
Additional approaches can be found in the exterior façade, which connects the building to its historic surroundings by using the golden ratio, or Fibonacci series. Many of the underlying proportional relationships of historic architecture were rooted in the golden ratio, and its use suggests a powerful interrelationship between nature and our built environment. This intriguing proportion along with a focus on using natural resources provides the foundation and inspiration for the exterior and interior design. Inside, local artwork on the floors are immersed by exposed cross-laminated timber (CLT) showcasing the natural beauty and calming presence of wood. The building’s lobby celebrates local indigenous culture and art with a carved wooden medallion honoring the wind spirit of the Columbia and a captivating native basket weaving pattern from floor-to-ceiling, crafted by local Yakama Nation artist Toma Villa. Three murals by Jessilyn Brinkerhoff represent three different biohabitats of the Pacific Northwest: Coastal, Forest, and Alpine. Echoing the golden ratio in every detail, the murals highlight the biophilic patterns found everywhere on the floors like the custom wooden dividers or the window proportions.
MATERIALS PETAL
10. RED LIST
Knowing the materials Imperative would be one of the most difficult to achieve, the team hired a consultant with specialized expertise in Red List-free material sourcing and tracking.
Brightworks and IES brought their experience with Red2Green (R2G), a proprietary database used on Living Building Challenge projects that has been shown to significantly reduce the management efforts relative to traditional spreadsheet management.
Learning from previous projects, the design team also saved time with several strategies such as minimizing the overall number of materials used in the project, eliminating finishes, allowing mass timber and concrete to be exposed, and using a standard materials palette. Vetting materials via the Declare database was also helpful.
Walsh Construction Co. helped to facilitate the requirement among numerous subcontractors, with compliance varying initially and improving with the project’s progress.
Challenges included missing materials, last-minute additions, and rejected items. Weekly meetings addressed emerging issues, expedited vetting, debated preferences, and provided updates. Walsh’s oversight of timelines and product lists proved to be vital in streamlining tasks and improving the team’s focus.
Notably, the PAE Living Building project spurred significant changes in the materials market. Several companies are now pursuing Declare labels for their materials, adapting product lines to expand offerings, or adopting Red List-free paint or finishes. Many manufacturers submitted Red List-compliant products for the first time and engaged in sustainable supply chain practices, all inspired by the Living Building Challenge.
- 2,487 products were reviewed for the project
- 1612 products are currently listed as approved for research
- An additional 875 records are marked No Longer Considered, but someone took the time to enter it into R2G
- 942 products were used on the project
- 511 products were LBC Compliant
- 476 were Red List Free under LBC v3. This is a very high percentage compared to v4 projects, as the transparency requirements for v3 are much lower than they are now.
- 341 products were LBC Unknown
- 90 products were LBC Non-Compliant
- 511 products were LBC Compliant
- 22 products were Salvaged
- 391 Different manufacturers were advocated to for better options in the future
11. EMBODIED CARBON FOOTPRINT
Exceptional design and engineering went into the creation of a building that aims to last 500 years, including careful artisanship and high quality Red List-free materials. Regardless of Living Building Certification, the project embodies a circular system just as in nature. In nature, nothing is waste, and everything is reused.
While constructed with glue-laminated, or glulam, timber and cross-laminated timber (CLT) certified by the FSC (Forest Stewardship Council), the building has a concrete core. This contributes to about 25% less embodied carbon than a comparable concrete or steel building while creating a strong and durable structure. The hybrid structural system supported both the design team’s carbon and aesthetic goals.
The windows are double-pane fiberglass windows with a very low U-value. The team expected to use triple-pane windows, but in comparing the embodied carbon and the operating carbon of both, the team found that double-pane windows were actually the better option for both cost and carbon savings.
An embodied carbon analysis using the Athena methodology revealed that the wood structure had lower embodied carbon than concrete and steel structures. From a cradle to construction perspective, the wood building has 30% lower embodied emissions than the steel structure and once biogenic carbon is included, the wood building’s structure has more than 60% less emissions than a steel building. A wood structure was ultimately selected as it reduced the carbon footprint of the building and dramatically improved the biophilic nature of the space.
The building’s total carbon footprint during construction is estimated at 2074 Mt CO2e, which was offset with a one-time purchase. Despite reducing steel and concrete usage by opting for a hybrid timber structure, they still contribute 60% to the carbon footprint. Future projects could improve by optimizing concrete and steel quantities and mixes.
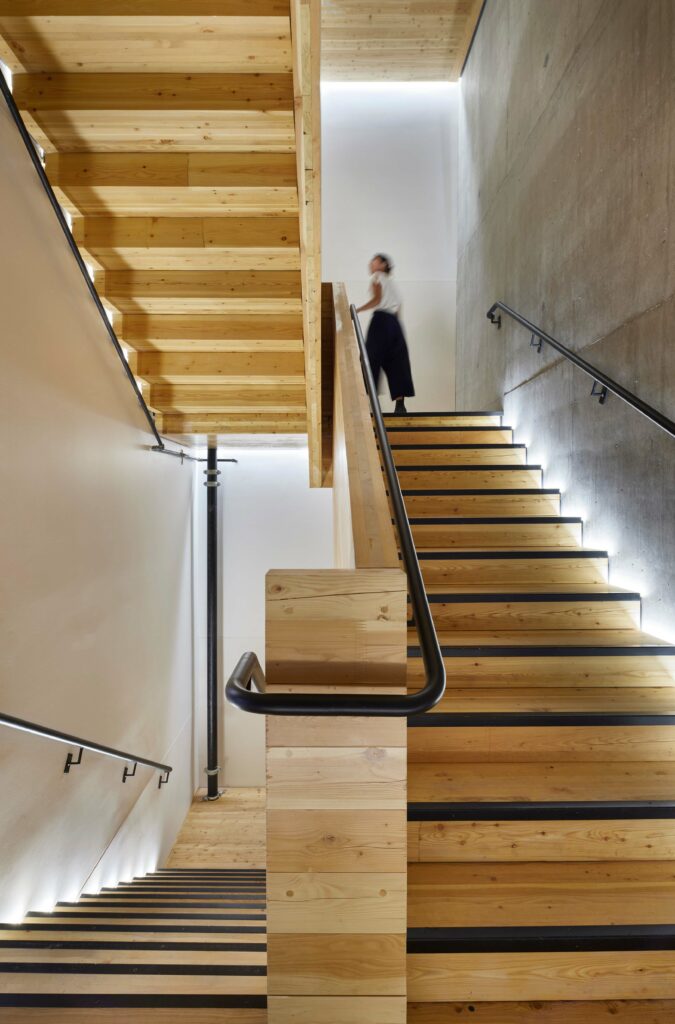
12. RESPONSIBLE INDUSTRY
All wood products, from cross laminated timber (CLT) and glue laminated wood beams to wood finishes and carpentry, were Forest Stewardship Council (FSC) certified with one exception for the salvaged red maple trees onsite. The project used a total of 57 unique Declare products.
13. LIVING ECONOMY SOURCING
This Imperative calls for construction materials to be sourced from 311 to 3,107 miles around the project site.
The reality of geography meant that the 311 miles distance from Portland included most of the industrialized Pacific Northwest, including not only Seattle and the entirety of Washington and Oregon, but also parts of British Columbia (where the mass timber was ultimately sourced from), and a large stretch of the Pacific Ocean.
The project achieved at least 47% of products (measured by dollar value) sourced within 311 miles of the project site, including major materials like cross laminated timber (CLT), glue laminated wood beams, and façade masonry. This is more than double the 20% rate required by the Imperative.
The project fell slightly short of the next radius, achieving 49.87% of the 50% of materials sourced from 621 miles, though missing data would have put the project over that goal.
The final radius material sourcing requirement is a combined 75% of product value must be sourced within 3,107 miles, which is effectively all of North America. The project was able to achieve at least 78%.
In addition to PAE salvaging items of furniture and equipment from their former office such as ceiling fans and a kegerator, the team also found an opportunity to salvage the red maples that once stood along the SW 1st Avenue, removed to construct the building. The team worked with a local lumber mill committed to the reuse of urban trees, Epilogue, to create a beautiful new desk for the reception area.
Finally, most of the project team worked within walking distance of the project site, around ½ a mile or less; Walsh Construction and one other consultant were located in south Portland, less than 3 miles away, far less than the 1,553 miles required by the Imperative.
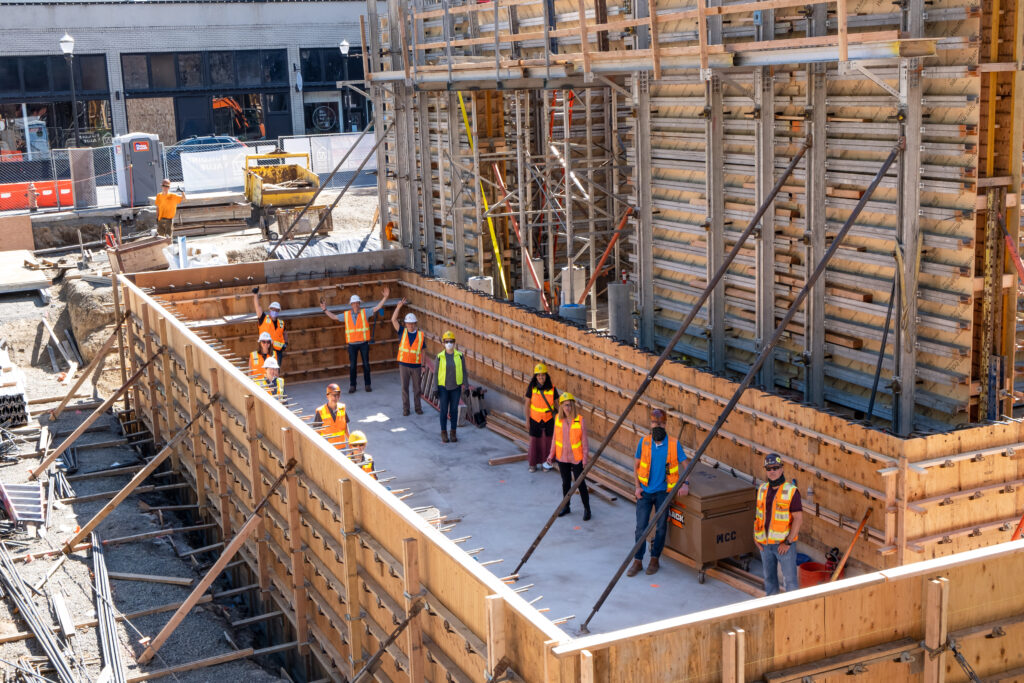
14. NET POSITIVE WASTE
The PAE Living Building is designed to be a 500-year structure, through its enhanced structural resilient design and durable materials. Because the building is built to Category IV seismic criteria, damage from potential sway is reduced and the building will likely be usable after a Cascadia subduction event. The floor-to-height ratio also supports future reprogramming, if needed.
During construction, materials like the cross-laminated timber (CLT) and glulam structure helped limit waste through a prefabricated, factory-sized process. Other prefabricated materials included pre-assembled fiberglass and glass window units, metal connections and canopies, PV racking, and shower inserts. Walsh Construction Co. developed a detailed construction waste management plan to divert the main materials used. Ultimately, metals, paper, cardboard, clean soil, and biomass achieved 100% diversion with all other waste materials reaching 98%.
EQUITY PETAL
15. HUMAN SCALE + HUMANE PLACES
The PAE Living Building strategically revitalizes a human-scale environment within Portland’s historic Old Town, situated in a challenging urban location. Transforming a former private surface parking lot, the development now accommodates ground-level retail spaces along with an additional four floors dedicated to office use. The conversion fills a void and now offers a pedestrian-friendly neighborhood amenity and workspace. In drawing pedestrians in with welcoming sidewalks and retail spaces, the building is directly supporting surrounding Old Town businesses and commerce.
Internally, the lobby serves as a mixing chamber and gathering place with the frequent building tours gathering in the place for general orientation before exploring further. The second internal connecting place is the deckony, the social heart of the PAE Living Building. Not just for gathering, it is also an ideal place to end building tours and has functioned not only to foster social cohesion among the building occupants, but also the greater sustainability and design community. For example, a lively Green Drinks event by the Sustainable Buildings initiative is held in the deckony every month.
As of the performance period, the building is 85% leased out, an impressive fact when the rest of Portland’s leases for commercial workplaces are at 40%
16. UNIVERSAL ACCESS TO NATURE & PLACE
A new construction in such a storied Historic District required the design team to take extra care when considering aesthetics, district regulations, and even materials. In keeping with historical guidelines, rooftop solar panels were limited within height and overhang restrictions.
Responding to its historic 1800s context, the building is derived from proportions from the golden ratio, a concept used for millennia by artisans and designers and seen throughout the neighborhood. Tied to the Fibonacci series, this mathematical proportion results in aesthetically pleasing proportions and helps the new building connect to and respect the Historic District it sits in today.
By revitalizing a vacant surface parking lot into a community cornerstone, considering sustainability and neighborhood preservation at every decision, and honoring the design history of the neighborhood along with the longer history of the area at large, the PAE Living Building is a sustainable, long-lasting structure that will anchor, honor, and help care for our Historic District for hundreds of years to come.
17. EQUITABLE INVESTMENT
Because the Historic District limited overhangs or a solar array canopy visible from the street, the building could not add enough solar panels to achieve 100% energy capture on the roof. The solution came from Walsh Construction, who was working on a neighboring affordable housing unit project, in the form of a partnership with a local nonprofit that provides free electricity, allowing the PAE Living Building to serve Portland residents in a tangible way.
By placing another PV at the neighboring affordable housing unit Renaissance Commons, they could achieve the energy goals. Together, both systems will generate enough energy to power Renaissance Commons’ common areas and about 5% more electricity than what the PAE Living Building needs annually. This energy donation translates to annual funds that REACH Community Development would otherwise be paying for electric bills and can now devote to other services that benefit its residents directly. There was also a donation of solar PV infrastructure, and the PAE Living Building ownership group made a cash donation to REACH to deepen its commitment to the organization, and further tie the project’s energy and equity missions as a part of the certification requirement. The PAE Living Building retains the Renewable Energy Credits (RECs), while the affordable-housing development gets the financial benefit of free onsite energy.
In looking beyond the limitations that prevented Net Positive Energy onsite, the project shows a potential new path to net positive energy for urban, site-constrained projects. The partnering and donation approach goes beyond the environmental sustainability provided by the PV and creates a substantial social benefit to the community.
18. JUST ORGANIZATIONS
The PAE Living Building is notable for including four key partners that just adopted JUST label declarations and committed to the program’s ethics around organizational policies.
PAE was an early adopter of JUST, publishing its first JUST label in August 2018 and recently updating to version 2.0 as well as becoming a Certified B Corporation. Recognizing the value, ZGF joined the JUST program in 2020. BioHabitats is a Certified B Corporation and also received a JUST label, while Edlen & Co. was introduced to the JUST program through this effort and is pursuing documentation. The last project-related JUST participant was not involved with the project, but is the building’s second largest tenant: Beneficial State Bank. The values-driven bank completed JUST registration in January 2022 and is also a Certified B Corp.
BEAUTY PETAL
19. BEAUTY + SPIRIT
The PAE Living Building draws upon its historic site context while looking to the future. Built on an existing parking lot in Portland, Oregon’s Old Town Historic District, the project responds to detailed district regulations addressing aesthetics and material selection. With a nod to the style and scale of the surrounding structures, the building’s brick, glass, and metal facade utilizes the golden ratio, based on the Fibonacci sequence, as a proportional guide. Found both in nature and classical architecture, the golden ratio proportions result in a facade that is aesthetically pleasing, respects the historic district, and is modern and timeless.
Both the aesthetic appeal and sustainability approach are rooted in simplicity. The design team left structural materials exposed to eliminate additional finish materials as much as possible; utilized a curated materials palette; and ensured materials served multiple purposes. Interior components celebrate the aesthetic and structural value of mass timber with exposed cross-laminated timber ceilings, glulam columns and beams, and salvaged wood throughout the project, a nod to Oregon’s timber industry and a low carbon, biophilic finish.
A key component of the building’s beauty is embracing the natural wonders of the Pacific Northwest. Large windows celebrate views to the outdoors and access to ample natural light and fresh air, while the deckony provides physical and visual connection to the outdoors. Artwork and visual patterns throughout elicit delight and further connect occupants to the region. To honor the history and people who first lived on the site, the project commissioned artwork from Toma Villa, a Portland-raised member of the Yakama Nation. Toma’s wood carving and inscribed motif of indigenous basketry designs welcome visitors on the ground floor. Floor-specific palettes of levels 3, 4, and 5 celebrate distinct regional themes through colors, textures and imagery, and support wayfinding. On the deckony, a mirror above the kitchen counter displays an etched profile of snow-capped mountains and a small tree on the slope. The mirror both reflects the expansive views from Old Town to Mount Hood and honors the analogy of a Living Building being like a tree on a mountain—something that can only survive by using the sun, water, and nutrients that fall within its reach.
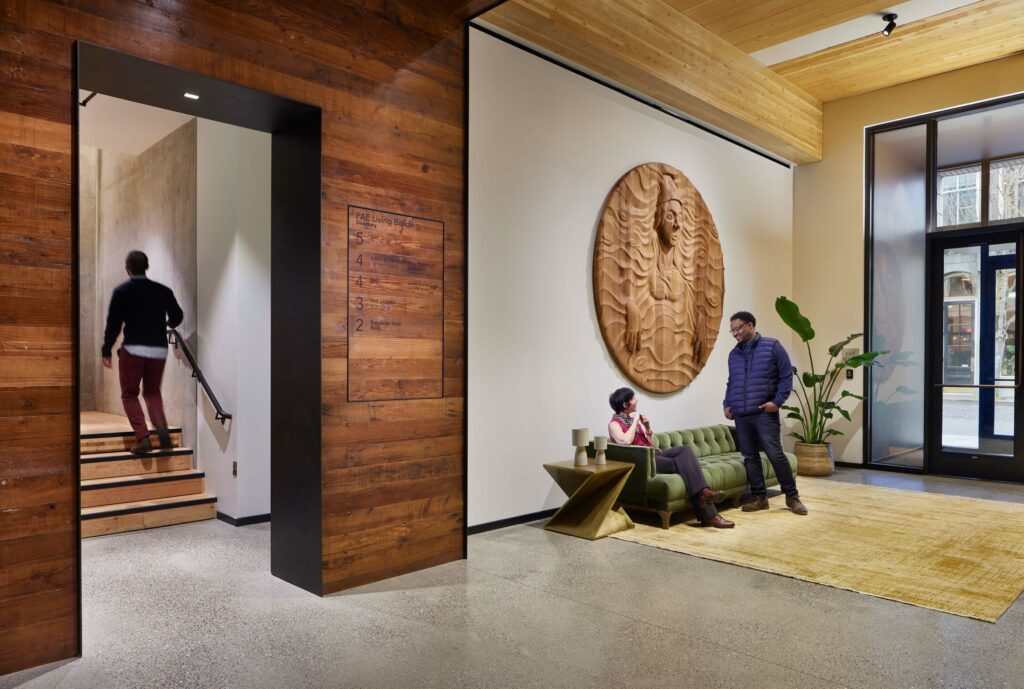
20. INSPIRATION + EDUCATION
Proving that a Living Building was possible and sharing how a developer-led project could be environmentally sustainable and economically viable was a fundamental goal of the PAE Living Building since its conception. Since it’s opening in late 2021 to early 2024 over 3,400 people toured the building, and multiple events were held for various conferences and initiatives.
PAE schedules informational visits or whole building tours when requested, and all tenants have access to share the building with their visitors as well. A specific group of staff are trained to give tours, and informative graphics and diagrams are posted near the most complex and consequential features. As a result, any staff member is capable of conducting a great visit. Visitors have included local and federal government officials like the Oregon mayor, the governor of Portland, and the U.S. director of the EPA, the general public, many industry associations and non-profit organizations such as the NAACP, college and university planners and students, architecture firms, high school STEM and engineering groups, and even a batch of local fifth graders.
The building has educational signage in its ground floor circulation space, in addition to information at the REACH Renaissance Commons about the unique offsite PV arrangement. Online content is available at: https://www.pae-engineers.com/about/pae-living-building.