Vital Stats
Certification Status | Living |
Version of LBC | 2.1 |
Location | Santa Monica, CA |
Project Area | 44,292 square feet |
Start of Occupancy | April 2020 |
Number of Occupants | 240 |
Project Team
Owner | City of Santa Monica |
Project Manager | Amber Richane |
General Contractor | Hathaway Dinwiddie |
Architect | Frederick Fisher & Partners |
MEP Engineer | Buro Happold |
Civil Engineer | KPFF |
Interior Designer | Frederick Fisher & Partners |
Structural Engineer | JAMA |
Landscape Architect | Ahbe |
Certification Consultant | Buro Happold |
Geotechnical Engineer | Geotechnologies |
Lighting Design | Buro Happold |
The Santa Monica City Services Building is an inspiring model of green design aimed at efficient operations, a healthy and productive workplace, and positive contributions to one of America’s most successful municipalities. Connected to the historic City Hall’s South Wing, the building fulfills a vision to bring all core municipal operations into one City Hall Campus and create a centralized hub for public counter services.
Early Design Process
How was the team assembled? When was ILFI’s certification first discussed? Who was the first team member to bring up the possibility of certification? How did the team arrive at the decision to pursue certification? How was the decision communicated to all team members?
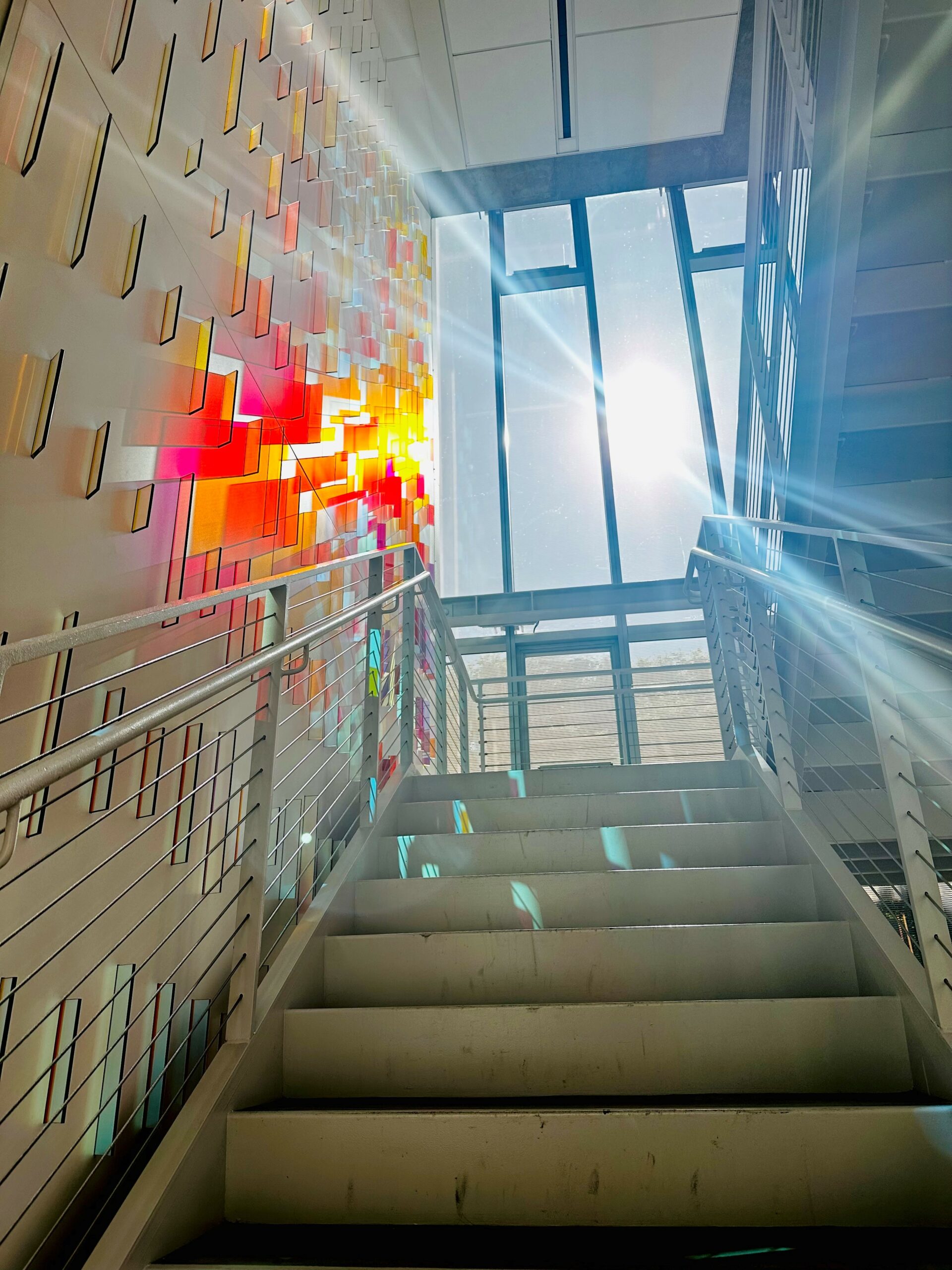
This project had the benefit of an early feasibility stage and being a design build project. Hathaway Dinwiddie was tasked with managing the Materials Petal and this helped to avoid any discontinuities with budgeting and procurement. Buro Happold provided dedicated materials support for MEP scope and Frederick Fisher for architectural finishes. The team worked to dematerialize and simplify finishes (such as exposed concrete shearwalls and ceilings) and assemblies and this greatly reduced the number of products expected on this project.
A workflow process was set up to act as a set of filters to capture as much as possible each step of the way. The team chose to research ahead of time and utilize the expertise of the team instead of relying on subcontractors. The team adopted a strategy shared by other LBC project teams to implement a “pre-submittal” process which captured information about products that were not going to be called out in the specifications. For example, it made more sense to ask an electrical subcontractor who they typically purchase conduit from and then research those vendors, than to fully vet and specify three of the many manufacturers on the market and potentially not receive a budget effective product. This also reduced the product data submittal review period and avoided holding up procurement for LBC vetting.
Upon contract award, each subcontractor was scheduled for an onboarding training, and required to complete the pre-submittal template. Every firm received a training about the LBC Materials Petal and documentation expectations. Due to the pre-submittal process, the subcontractors already had most, if not all, of the necessary LBC documentation for their products ready to submit. A submittal cover sheet template was provided, titled an Environmental Building Materials Certification Form, or EBMCF. We would review the cover sheet and backup against the pre-submittal and previously vetted specified items and stamp the cover sheet as verification of LBC approval. For the most part, this is where the success of the pre-submittal would bear out, as this LBC review turnaround could happen within 24 hours.
A separate training was created for the field. The project superintendent would spend 5-10 minutes after each worker’s first day mandatory safety orientation to provide a condensed summary of LBC, to enforce that all materials must have approved submittals, trucks and toolboxes should be cleaned out and hardware store runs had to be approved, and to follow Construction Waste protocols. After orientation, each worker signed a form and received a hard hat sticker.
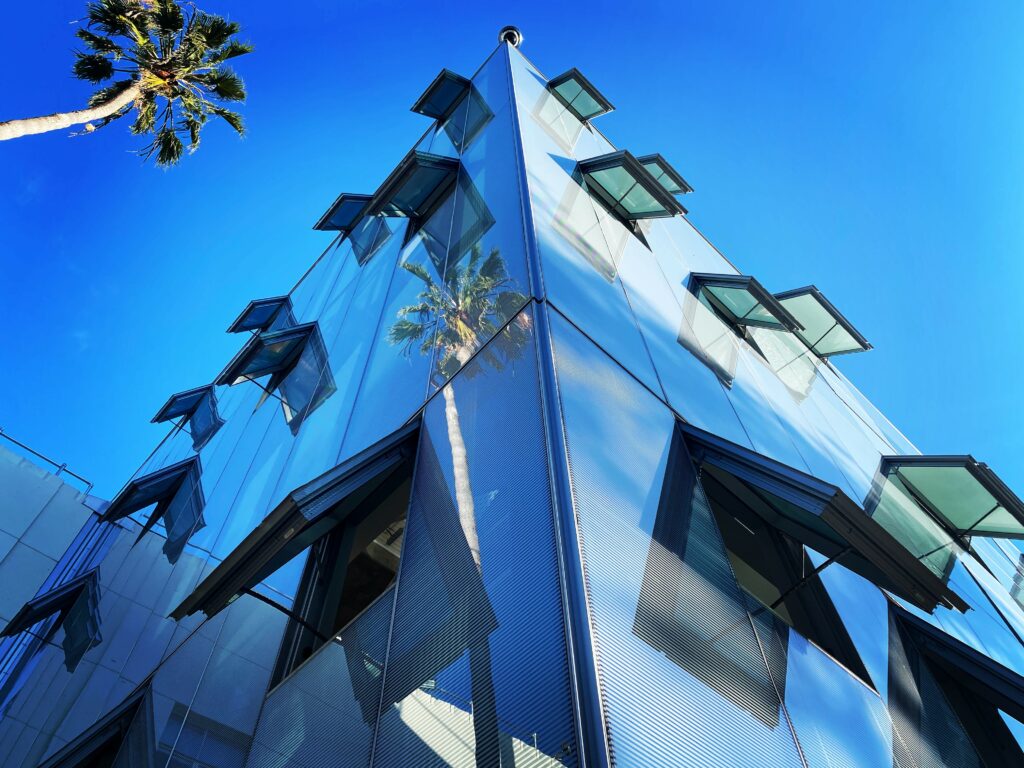
Advocacy to Manufacturers and Suppliers
When did advocating to manufacturers and suppliers result in changes to a product’s formulation or manufacturing process? Did a manufacturer choose to pursue a Declare label as a result of the team’s advocacy? What should teams keep in mind when working with manufacturers to identify the best product for the job?
Aerocel Aeroflex elastomeric insulation required a General Red List exception after extensive research. Through our advocacy the manufacturer indicated in an email in May of 2019 that our requests and conversations provided helpful information for them to build a case for non-HFR products. A follow up in June of 2020 indicated significant progress on their R&D attempts to eliminate HFRs while still meeting ASTM and many new transparency documents. As well as a commitment from their CEO to create a Red List Free product for the market.
The team sourced Forest Stewardship Council certified wood for shoring lagging, formwork, millwork cabinets and veneers, and doors. We were also able to incorporate salvaged wood from other projects for lagging and formwork. A clarification was issued as construction began that temporary formwork no longer needed to be FSC, however the project team chose to still require and purchase FSC formwork to support the sustainable forest industry.
The carpet selection is also conscious of material conservation in maintenance and its end-of-life. Entrance design includes walk-off mats to reduce soil build-up in carpeted areas, mitigating fiber damage. The manufacturer Bentley Mills has a FULFILL™ reclamation program, that recycles the carpet material and 100% diverts from landfill. The design of module tile carpet grants high degree of replaceability, and further conserves material in repairment.
The construction phase utilized CDR, Inc., the only RCI third-party verified waste facility in Southern California. They consistently achieve high diversion rates, do not use ADC, and provide extensive sorting, recycling, and reuse. They also separate out gypsum, and grind into dust to be sold as an agricultural soil amendment. Separate paper/cardboard, and metals bins were provided alongside commingled bins as well as concrete washout bins provided during pours. Every subcontractor was informed of the waste management goals during their onboarding as well as each individual field worker during their LBC orientation on the first day of work onsite.
Lessons Learned
Are there discussions the project team would have initiated at a different time in the process? Are there processes or documents the team wished they had implemented during construction to help with certification compliance? What worked well in the team’s design process that other teams should consider implementing?
It is incredibly important to balance gray water irrigation supply, ease of maintenance, native/adaptive plantings, onsite habitat restoration considerations, historic requirements, climate considerations, plant production seasonality, and the urban agriculture area requirement. For future projects, having an integrative workshop on landscaping with irrigation consultant, plumbing engineer, biodiversity specialist, architecture and owner/operator is essential, and if a full day workshop is difficult, creating a matrix of plant selection and the various considerations can be incredibly valuable.
Complex MEP equipment requires an early start and a long timeline to fully vet. Light fixtures were especially complex, and they are purchased by a subcontractor through a vendor who has relationships with limited numbers of manufacturers. There were added layers of contacts to address and limits to substitutions due to the purchasing agreements. It took about 14 months to vet all fixtures, and in the future the team may try to limit the quantity of fixtures as well as the variety of different manufacturers.
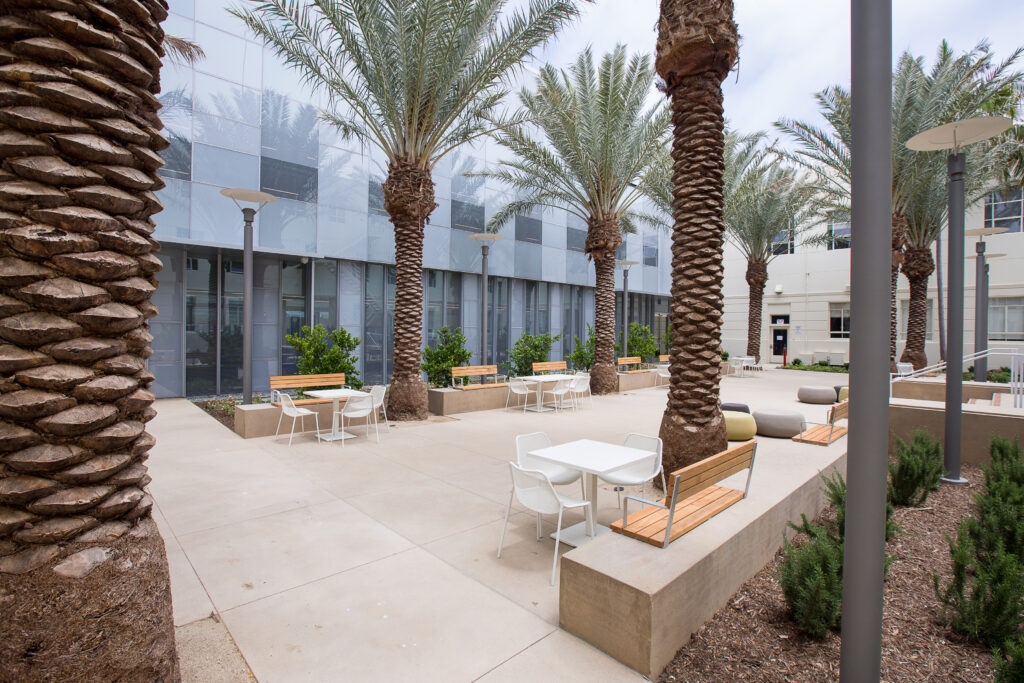