VITAL STATS
Certification Status | Petal Certified & Zero Carbon Certified |
Version of LBC | 3.1 |
Location | Santa Rosa, CA, USA |
Project Area | 19,600 Sq Ft. |
Start of Occupancy | December 2018 |
Owner Occupied | Yes |
Number of Occupants | 11 regular occupants; 321 visitors |
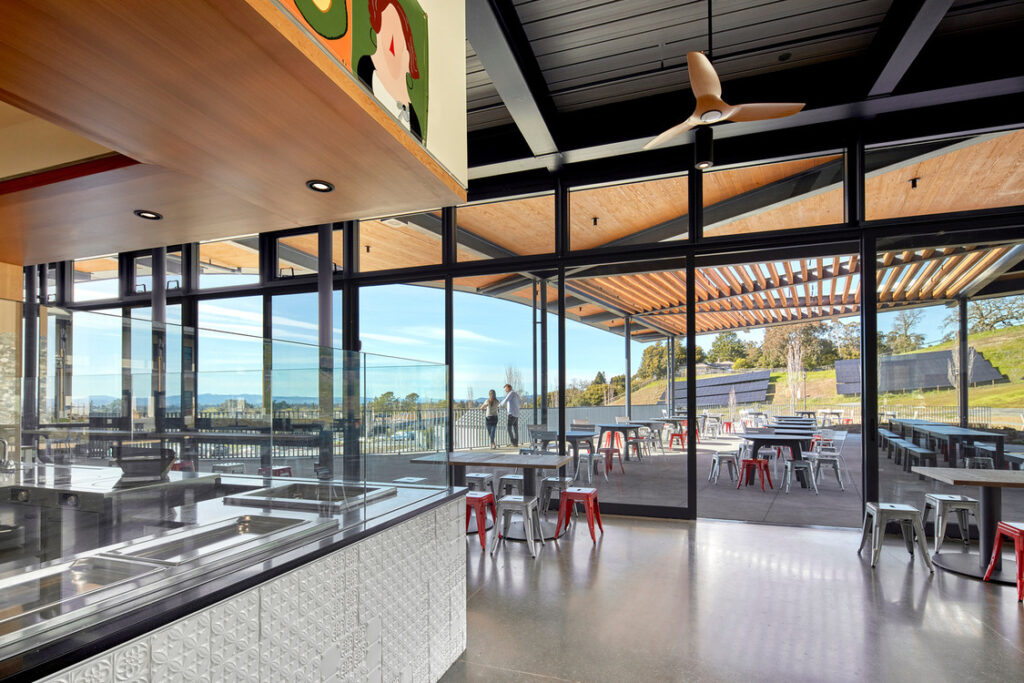
PROJECT TEAM
Owner | Sonoma Academy |
Architect | WRNS Studio |
Contractor | XL Construction |
Mechanical | Interface Engineering, Inc. |
Electrical | Integral Group |
Plumbing | Interface Engineering, Inc. |
Energy Design & Analysis | Interface Engineering, Inc. |
Geotechnical | RGH Consultants |
Civil | Sherwood Design Engineers |
Landscape | RHAA & Rana Creek |
Structural | Mar Structural Design |
Food Service Design | Vision Builders USA & Compass USA |
Acoustical | Salter |
Specifications | TopFlight Specs & Long Green Specs |
Commissioning | Beta Engineer |
Other | Wahaso; The Shalleck Collaborative, Inc.; Sonoma Co Dept of Health Services; City of Santa Rosa, Community Development; City of Santa Rosa Fire Department; City of Santa Rosa; California Code Check |
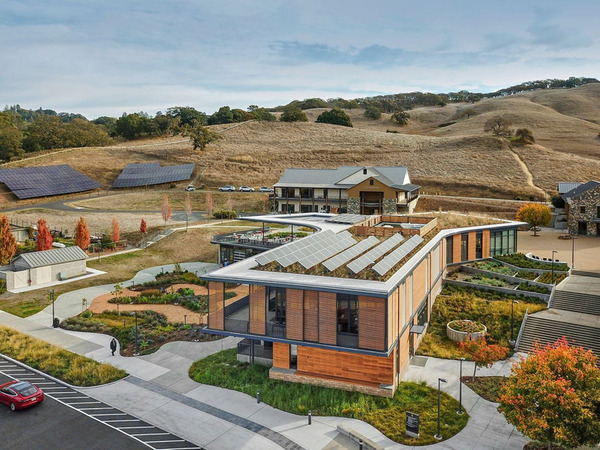
Place Petal
01. Limits to Growth Imperative
Before the construction of the Maker and Grange Studio, the site was an underutilized space on the Sonoma Academy campus. Early in conceptual design, the focus was to work with the natural, topographical flow of the site to reduce disturbance. This lead to a landscape concept that would spill from the top of the site into the lower garden. The design nestles the building into the hillside and reinforces natural pathways.
Limited flora and fauna occupied the site prior to the project. The landscape design sought to repopulate the space and bring back diversity. Only native, water-conscience plant species were chosen as vegetation. A great emphasis was placed on producing more pollinators and re-growing the local habitat.
Sonoma Academy also wanted to bring a “grow your lunch” concept to the campus and student experience. The value of agricultural land is taught to students through the fruit, vegetable, and culinary herb garden in the lower garden.
The Academy’s successes are ever-growing. The Maker and Grange Studio building was designed to assimilate resilience with the Academy’s future expansions. Early massing compounded the Studio with a potential theater directly north. Aspects of the Studio’s final design, such as the upper terrace and lower maker classrooms enable a seamless and efficient evolution to exist in the future.
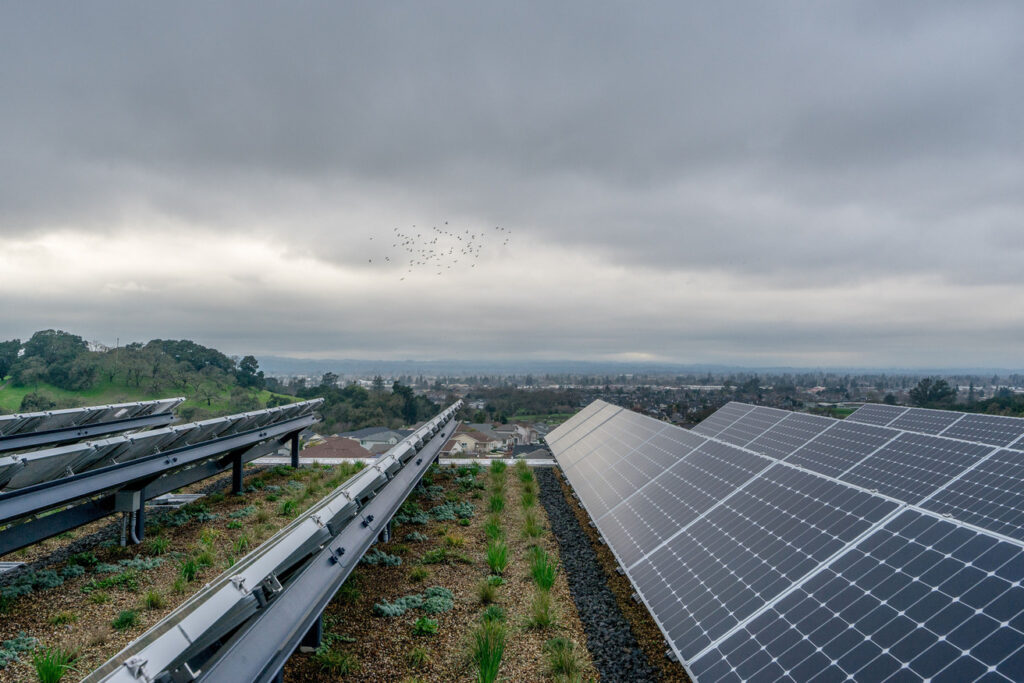
Energy Petal
06. Net Positive Energy Imperative
Active and passive mechanical design strategies are incorporated, taking advantage of the mild Bay Area’s climate. Natural ventilation and ceiling fans are used throughout the shoulder season, providing user control, passive cooling, and a high degree of user adjustability. Radiant heat and cooling are used during the more extreme months, which is provided by geo-exchange ground source heat pumps. The geoexchange system is able to provide compressor-less cooling during the milder shoulder season, when the ground loop is able to provide 65F or lower water temperatures.- expected to provide 10-15% of the annual cooling demand. The mechanical system captures waste heat from the ventilation air and refrigeration system in the commercial kitchen — used for space heating and domestic hot water production. The central heat pump is also used for domestic hot water heating — one of the largest demands due to food service.
As food service facilities often have an EUI above 400, a significant challenge included working with the food service provider and the school to tune choices and detail use schedules, resulting in aggressive load reductions in the maker and food service equipment in order to get to ZNE. The kitchen facility is 100% electric, including induction cooktops, reducing or eliminating energy consumption while idling.
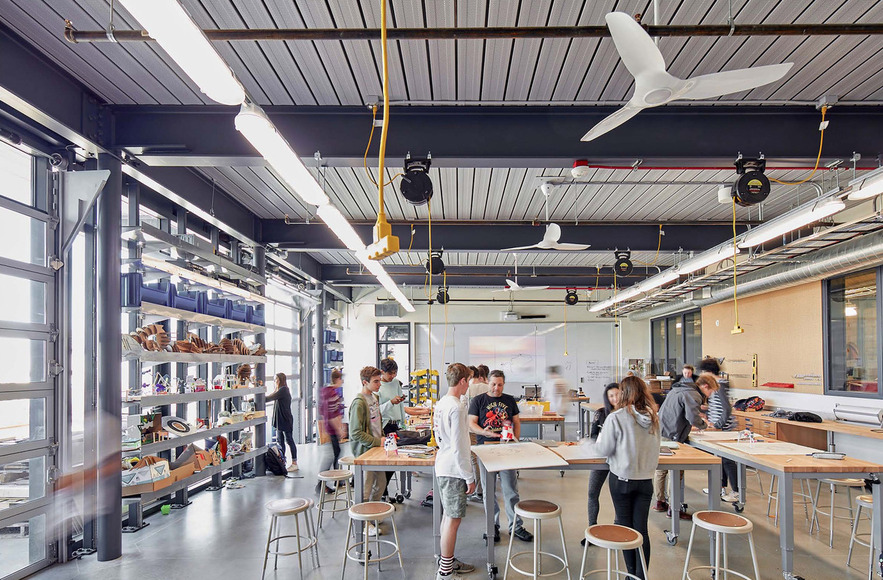
Health + Happiness Petal
07. Civilized Environment Imperative
Fresh air and daylight are in abundance throughout the dining and maker spaces. On the first floor, the electronics and wood maker spaces both incorporate overhead-stacking sectional doors. These garage-like doors open the façade up to 9 feet wide and nearly 10 feet tall. In total, three overhead doors allow the maker workshops to stretch beyond the walls of the building, into the lower gardens, and bring new inspiration and life into the classroom.
The dining hall, teaching kitchen, and professional kitchen prep spaces are each fit out with operable, sliding windows on all sides. The north side of the dining hall and the kitchen prep space also have overhead operable windows to offer opportunities for passive thermal comfort and fresh air. Sliding doors on the north and east sides of the dining hall open the space up to the dining patio and campus commons, respectively. Soft daylight floods the dining hall during the day, entering through the glass façade that encircles the space. The dining terrace that lay on the top hill is an extension of the indoors. These spaces act as one and give students and staff the opportunity to fresh air year-round.
The shallow floorplate of the building opens nearly every corner of the building up to outside air and natural daylight. The digital media room and audio/video recording studio intentionally positioned towards the back hillside so their programmatic function would not be interrupted by external noise or light intrusions. These spaces are designed to allow users complete control over visual and audio activities.
09. Biophilic Environment Imperative
Approaching the project through the lens of Sonoma Academy’s guiding principles of creativity, inclusive community, exploration, and innovation, the team engaged students, neighbors, educators, and staff s to uncover how these principles would translate into design. This nature-inspired education center stretches to the horizon and integrates back into the land. Designed around a series of outdoor experiences, two sweeping floors sheathed with an operable, transparent skin and a lattice of wooden slats, blur the lines between indoors and out.
An ode to nature, the Maker and Grange Studios is carefully located to frame natural views, create outdoor learning spaces, and actively engage with its surroundings. The design strengthens the strong sense of place apparent in the school and tells the story of the region’s geographical connection to architecture, landscape, people, sustainability, and everyday life
Made with a reductive, indigenous material palette, the transparent façade is reinforced with earth block, timber, and steel, and enmeshed in a medley of moveable wooden slats.
The butterflied roofline welcomes students, inviting them to wander in and out. Its curved silhouette hugs organic-shaped gardens which are connected by meandering pathways. Operable windows connect students to the outdoors. Maker spaces spill onto the central courtyard. This new cornerstone of the campus boasts enticing environmental features including sunlight, air, views, and vistas.
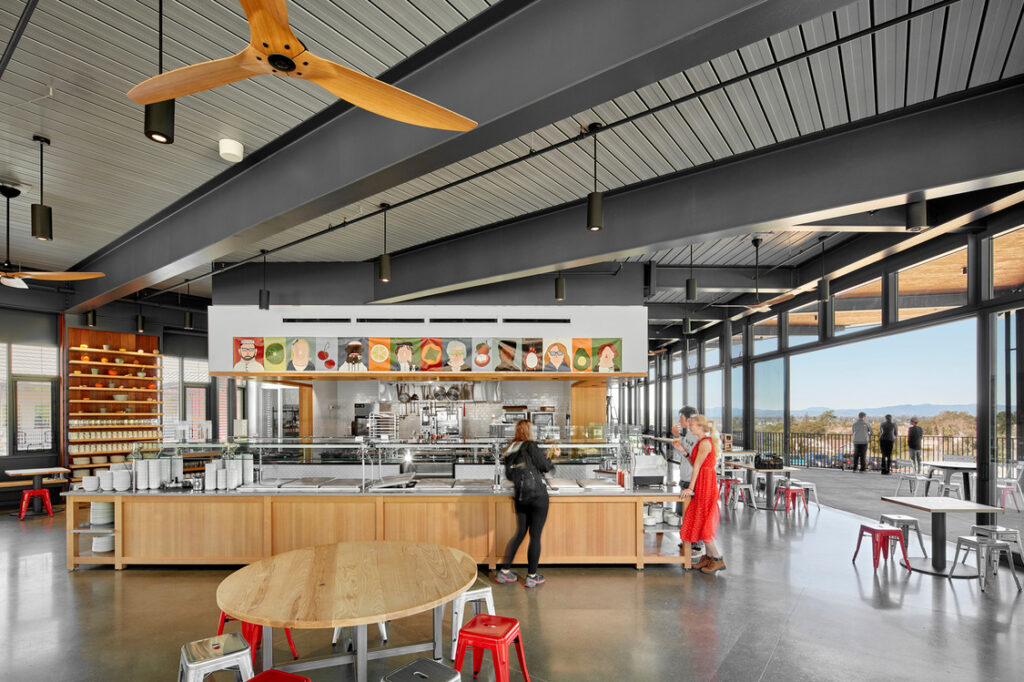
Materials Petal
10. Red List Imperative
The Materials vetting process was found to be very difficult for many different classes of products. Namely, electronics, kitchen equipment and mechanical equipment. The team utilized the small electrical component exceptions on many of the lighting fixtures within the project due to PVC in the wiring insulation of most products on the market. In many cases, this was the only Red List ingredient found within the product. The team placed emphasis on advocating for the industry make a concerted effort to remove the PVC from the product.
Another area of difficulty was the kitchen equipment. The complexity of the large appliances also presented a large challenge. For many manufacturers, our ingredient inquiries were the first time they experienced such requests. Manufacturers had to contact multiple other smaller sub-manufacturer’s they themselves sourced from. It often led to a race against the clock as lead times lengthened as we waited for greater ingredient information. Many appliance manufacturers were not able to produce the level of detail we were seeking. So for many of these powerful pieces of food service equipment (induction stoves, refrigerators, etc.) the project utilized the General Red List exception. Exceptions also had to be made for many of the plumbing fixtures for various Red List chemicals: Chromium IV, HPDE, and lead.
The team also had some wins during the material vetting process. While examining roofing materials, the manufacturer’s ingredient list revealed neoprene in the rubber roof assembly. The team made a request for the product to be manufactured without the Red List ingredient, which was easily honored by the manufacturer. Furthermore, the team was able to connect the manufacturer with a company working on a new bio-based, natural neoprene alternative made from the guayule plant.
11. Embodied Carbon Footprint
As the project goal was to make sustainable strategies and innovation evident to the students and community, the design team and client had a charette over a few basic principles: how to “live” with less, how to measure this approach, and how to make this decision evident in the spaces.
The first strategy was to try and reduce the materials used on the project. A reductive material palette and radiant heating and cooling through the slabs relayed simplicity, durability, honesty, transparency. Radiant concrete floors cover the building. Next, the team worked to find regional and reclaimed materials to reduce manufacturing and transportation impacts.
Materials were chosen for their beauty, durability, longevity, and ease of maintenance. Regional, CDPH, EPD, HPD, and Red List were filters for all material considerations. Regional resources were utilized to reduce the environmental impact of transportation and to support the local economy. Ceramic tiles were selected from nearby companies.
Their goal was to reduce the project Global Warming Potential (GWP) by utilizing a carbon calculator during the material selection process. Their design calculations led the team to utilize Watershed Block (reduced-cement masonry unit w/ locally sourced aggregate) instead of a typical CMU retaining wall. They were required to submit a testing program and alternate means and methods to utilize the Watershed block – this paved the way for other project teams to consider local earth-based construction methods in lieu of higher- cement retaining wall construction methods.
To help track the process, each consultant was asked to consider the carbon footprint of the system and material, along with the health and efficiency considerations. Early simple analysis measured the individual benefits, and assessed using Tally as the tool. A project report (Sonoma Academy material and carbon summary 2017 and a version dated 2018; uploaded) helps memorialize some of the tested metrics at that time. As information became clearer through collaboration with vendors and the construction team, updated information has been worked through to measure additional metric sources. The current data has been memorialized into a few documents that have been shared for the school ( SA Carbon benchmark; uploaded) that shows four different materials assessed with percent improvement, and a Greenbuild session in 2018 (Greenbuild Carbon slides for Sonoma – partial; uploaded) shared with the community.
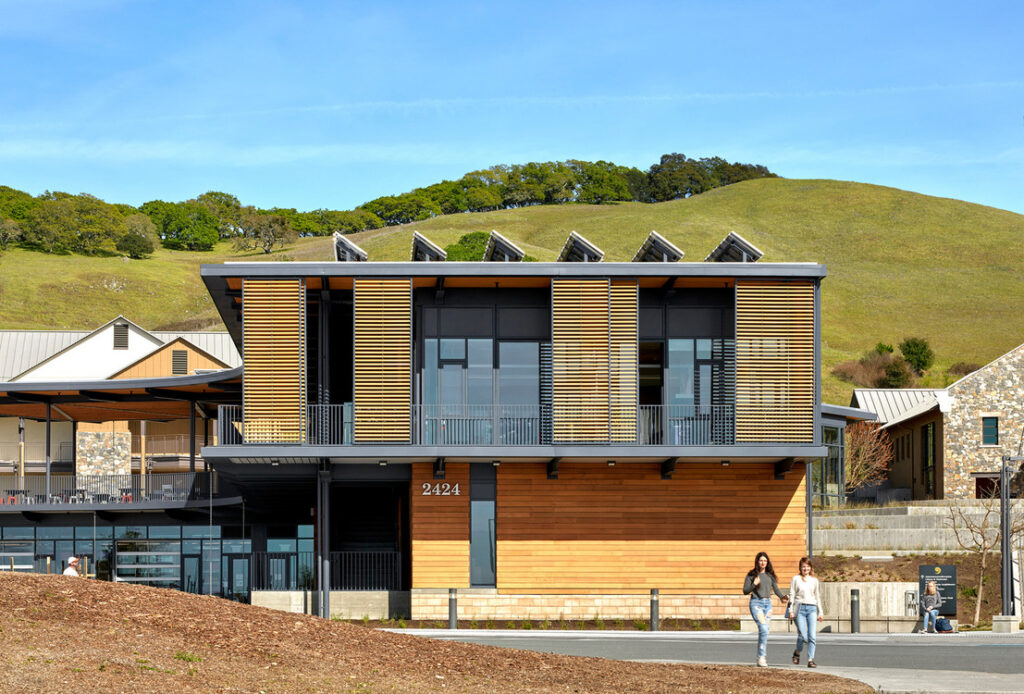
12. Responsible Industry Imperative
The entire project team was determined to advocate for the adoption of third-party standards to ensure raw materials used on the project were sourced ethically and sustainably. The team was able to integrate 11 different FSC Certified wood products as well as beautiful, locally salvaged wood. The project’s memorable exterior siding and beams were salvaged from a house in Marin, California, approximately 30 miles from the project site. The team also collaborated with a local company, Heritage Salvage located in Petaluma, to salvage timber from a tunnel near the northwestern coast, just 368 miles from the project site. All other wood on the project was FSC certified. A local craftsperson 60 miles south of the site, created all the Dining tables from FSC wood.
The team also utilized the Declare program to guide product choices. By selecting Declare products, the team was able to guarantee the project was support fair and healthy materials and manufacturers. Some Declare products in the project include the Prosoco interior floor concrete finishing, DR Johnson douglas fir CLT panels, and LF Illumination recessed lighting.
13. Living Economy Sourcing Imperative
The project team prioritized the use of regional resources to reduce environmental impact of transportation and to support the local economy. 15 products from Sonoma County as well as 143 products from California were utilized on the project. 43 products were sourced from within 100km of the project site and 105 are from within 500km. Locally crafted reduced cement block made from regional soils highlight local creativity, reduced carbon sourcing and specifics of place – 10 miles from the site. Constructed from local soil, the manufacturer and structural engineer worked with the city to accept this environmental alternative to cement blocks. These compressed earth blocks produce low carbon emissions and are energy efficient. They are long-lasting, naturally heat-regulating, water-resistant, easy to maintain.
Exterior wood siding and beams from a house in Marin and tunnel in the northwest provide regional authenticity- sourced from a company Petaluma 37 miles from the site. The original locations are a house 37 miles away and a tunnel 368 miles away. All other wood is 100% of FSC-certified – from 414 miles away. Ceramic tiles were selected from nearby companies.
A concerted effort to select from local sources resulted in the following: Heath Tile (66 miles) and Sonoma Tilemakers (11 miles). A local craftsperson 60 miles south of the site, created all the Dining tables from FSC wood.
14. Net Positive Waste
A holistic approach was developed from the start of the design through construction. Early discussions with the owner and builder identified on-site materials that could be used for reuse in the project, and a reductive material palette that would help with reduced carbon but also easier long-term maintenance. Existing exterior pavers that within the boundaries of the new footprint were carefully removed and stored on-site for future use. Extra pavers were offered to the construction crew and staff.
During Design Development, the structural engineer worked with local agencies to get reduced cement blocks approved for the structure. Locally crafted reduced cement block made from regional soils highlight local creativity, reduced carbon sourcing, and specifics of place. Constructed from local soil, the manufacturer and structural engineer worked with the city to accept this environmental alternative to a cement block. These compressed earth blocks produce low carbon emissions and are energy efficient. They are long-lasting, naturally heat-regulating, water-resistant, easy to maintain.
During the Permitting stages, reclaimed wood sources became available to the project. During this time and Construction Administration, the team worked to augment the rainscreen slightly in order to use this reclaimed wood. This effort saved material cost and didn’t add cost to the final project total, The exterior wood siding and interior dining panels all came from reclaimed sources Exterior wood siding and beams from a house in Marin and tunnel in the northwest provide authenticity. Locally sourced reclaimed wood is integrated throughout and all other wood is 100% of FSC-certified. The dining tables were sourced from a local craftsperson, who provided all the dining tables and helped the team to design to reduced wastage in the creation of the optimized size.
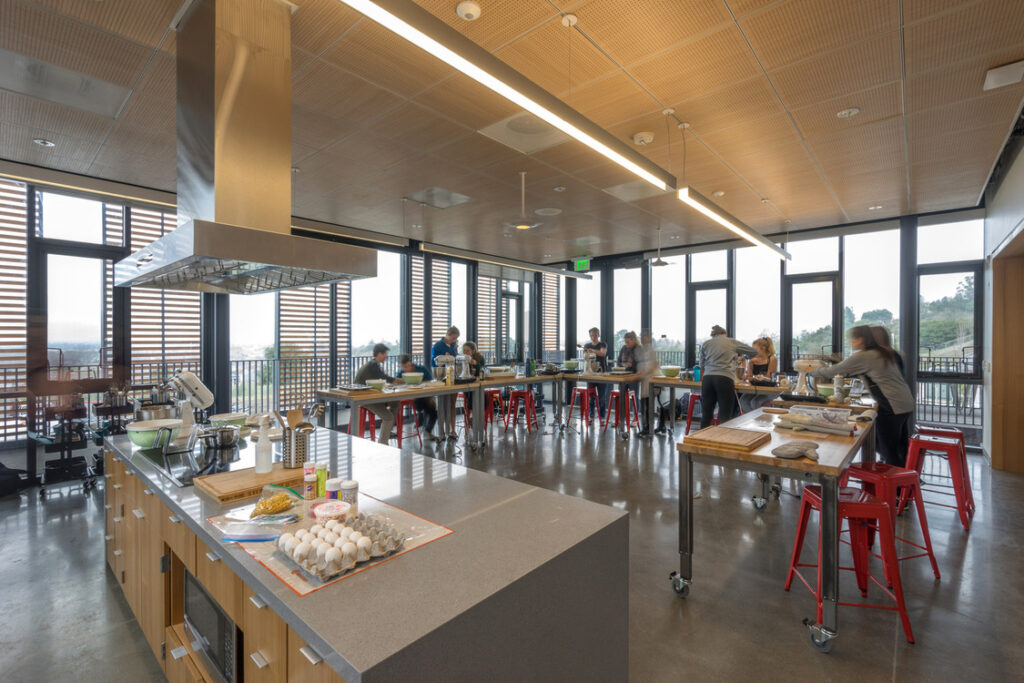
Equity Petal
15. Human Scale + Human Places Imperative
A place to be loud and not heard, a nook to reflect, a place that explains, expresses, and transforms. Sonoma Academy created guiding principles that spoke to equity, community, and exploration. The building and site attempt to stretch out and reflect the site and community. Inclusivity and collaboration as guiding principles meant that the planning of the project included aspects that relayed this importance. The dining space serves for impromptu collaboration, casual collisions, stretch space for the community. Gender-inclusive toilets, nooks for meditation, spaces for reflection, speak to the recognition that one approach doesn’t fit all and that all approaches matter.
Additionally, the design gives back to the community and encourages “act locally, think globally” mentality through its food program — a partnership with local farms and ranches to provide healthy meals and educate students about the relationship between the food we eat and the economy, the environment, and issues of equity.
16. Universal Access to Nature + Place Imperative
Sited at the base of Taylor Mountains, the landscape rushes down the hill and over the building. It integrates into the land and contributes back in native plantings that invite pollinators. The dining rooms open to the hill and city, with deep overhangs providing shading and intimate in-between spaces. The dining room is for gathering and meeting and one-on-one connecting. Big farm tables made locally provide collaboration space while bar height counters provide an option for much-needed focus. The teaching kitchen doubles as a classroom, meeting room, and event spaces – with views to the west. Maker spaces open out to the productive garden for extended classroom space. The garden acts as a classroom, park, and gallery. Making with tools, making with food, and making with technology blend at the garden. The beauty of the site inspired the organization of two sweeping floors that stretch to views, grab onto the hillside and work to blend this campus with many levels. With the open sliding doors, students are encouraged to wander in and through, making this building a part of everyday pathways.
18. Just Organizations
The following team members completed Just labels: WRNS Studio, Integral Group, and XL Construction.
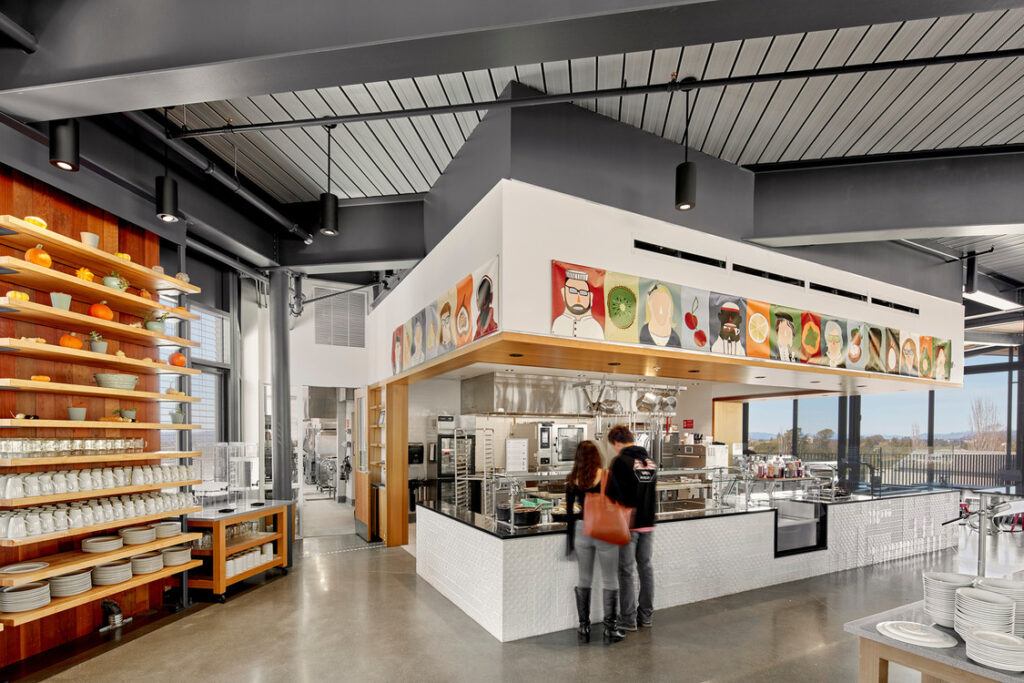
Beauty Petal
19. Beauty + Spirit Imperative
In today’s techno-centric world, people spend more time looking down at devices versus connecting to their place. For Sonoma Academy, a high school on the outskirts of Santa Rosa, their goal was to have people look up and out, to create a campus heart, and to bring the school and community together through dining and making, all while celebrating the region’s beauty.
For the new Janet Durgin Guild & Commons — a program with maker spaces, teaching kitchen, kitchen/dining spaces, gardens, digital media center — the design needed to support their STEAM-based curriculum and their community-and-environmentally engaged culture.
Early on, the project team collaborated on how place-based relationships could inform the system selection, planning, and details. Geoexchange, radiant heating, and cooling in slabs and panels, cross-laminated timber eaves, north-facing operable windows, and sliding doors, rainwater moving through rain chains, PVs layered over a green roof, water collected through landscape terraces for reuse, sliding wooden shutters and building-managed shades reflected how technology and nature can be intertwined and supportive and evident and celebrated. Elements and systems invite interaction, adaption, and curiosity. Reused and reclaimed materials reflect history and memory.
The beauty of the site inspired the organization of two sweeping floors that stretch to views, grab onto the hillside and work to blend this campus with many levels. With the open sliding doors, students are encouraged to wander in and through, making this building a part of everyday pathways. Exposing the materials, the radiant manifolds, the structure, and the systems invite the user into the daily functions of the building. Biophilic principles providing guidance for planning and material selection – everything was thought of as a critical piece of the story.
The resultant design strengthens the strong sense of place apparent in the school and tells the story of the region’s architecture, landscape, people, sustainability, and everyday life.
20. Inspiration + Education Imperative
Ecoliteracy is embedded throughout the culture of Sonoma Academy. As an academic institution, Sonoma Academy used the Maker and Grange Studio project as an opportunity to create an immersive learning space where students can explore the impacts today’s built environment has on the natural world and resources.
Throughout the building is a signage plan, highlighting various resource conservation achievements of the campus addition. Signs are purposefully located to teach students about their surroundings and how they were designed to in harmony with the natural environment. For example, the project’s water story is spotlighted at various spots in the garden, next to the cistern, and in the bathrooms.
Sonoma Academy also has launched a Connections program that brings the principles of sustainability into the classroom curriculum. The 9th-grade program includes classes such as Literature of the Environmental Movement and Environmental Science, and an Exploratory course revolving around food and the garden, just to name a few.
Additionally, Sonoma Academy holds Open Houses and campus tours to prospective student families as well as Community Fundraiser events. These Open Houses and fundraising events are held multiple times a year and open to all. The project’s educational brochure is provided at the open house and highlights the building’s design and environmental features.
Sonoma Academy, proud of their eco-learning opportunities, also has an About Sustainability page on their website. It educates visitors about their achievement of 100% local renewable energy campus, water conservation and recycling systems, garden and food programming, Connections curriculum, and more.
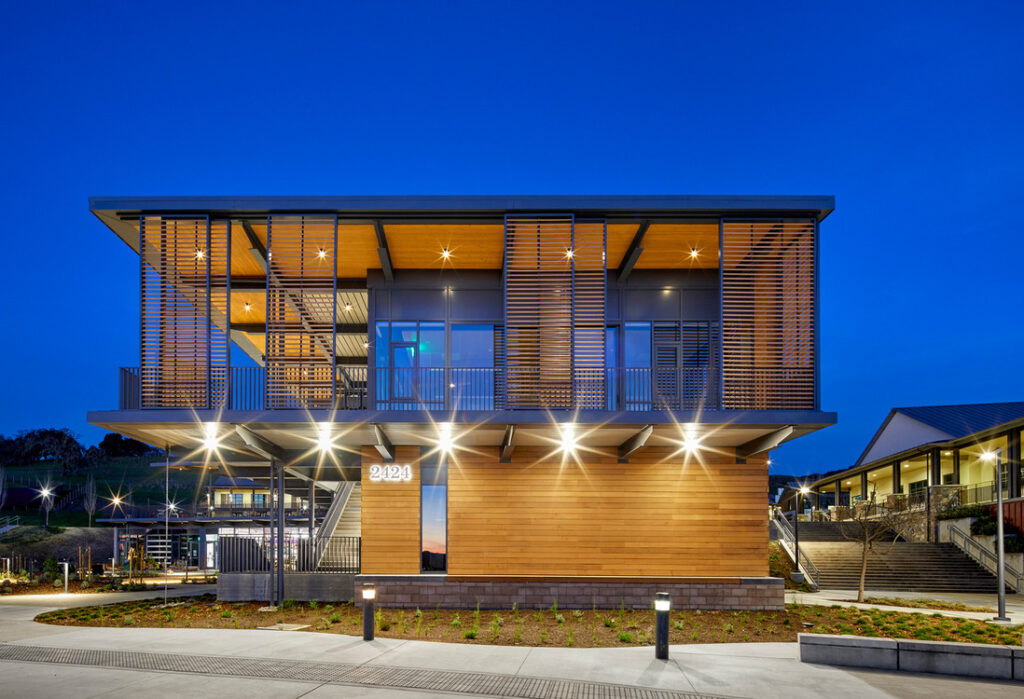