The Brock Environmental Center will be the beachhead for the Chesapeake Bay Foundation’s (CBF) lower bay programs, bringing the community together to solve complex environmental issues and empower the next generation of citizens through environmental education programs in the Chesapeake Bay. The center is located in Virginia Beach, Virginia, where the Chesapeake Bay meets the Atlantic Ocean, an ecologically vital area to the Bay ecosystem. This building serves as the hub for CBF’s Hampton Road office. It supports the Foundation’s education, outreach, advocacy, and restoration initiatives. In addition to offices for CBF and partner groups, the Center provides interpretative exhibits spaces, meeting rooms, and an 80-seat conference room.
Early charrettes with the client and neighbors led to a shared vision for the project, against which design options were evaluated and optimal solutions chosen. Previous collaborations between the project’s architect, engineer, owner, and green consultant allowed the team to candidly evaluate and draw lessons from past projects. This provided a comprehensive understanding of how CBF uses its centers. Based on these insights, we were able to make key design decisions including reducing workstation size, adding an outdoor classroom, and implementing targeted design decisions including selecting optimal glazing and renewable materials.
The project’s architect, engineer, owner, green consultant, and contractor worked closely throughout the design process. The team toured other Living Building Challenge (LBC) projects, including meeting with these project’s teams to learn lessons applicable to the Brock Environmental Center project. Next, to formulate a shared vision for the project, a full-day, pre-design charrette was held on-site, with participants including stakeholders from all design disciplines, such as local officials, community representatives, and outside experts in LBC / LEED.
Project partnerships between experts and the use of simulation tools in our iterative design process allowed the team to validate and maximize each design decision. Through pre-design as well as site and climate analyses, we discovered the site has unique potential for using wind as a renewable resource. Site analysis also included an investigation of the ecological function of the site from pre-colonial periods to the present, emphasizing the site’s potential to filter stormwater from beyond its own boundary. The architecture and MEP engineer worked closely, using a shared BIM model. To meet the challenges of the LBC materials petal, we held a “red-list” charrette during schematic design. The client, architect, contractor, green consultant, and interns from local schools developed shared online tools and formalized methodologies for materials vetting. The team partnered with the Center for Wind Energy at James Madison University to optimize the wind turbine design, and partnered with the US Fish & Wildlife Services to ensure these turbines would be safe for birds. Conversations with regulatory agencies began during early design and spanned throughout design and construction, enabling us to collect rainwater for potable use.
VITAL STATS
Certification Goal | Full Living Building |
---|---|
Version of LBC | 2.0 |
Current Certification Status | Fully Certified |
Certified Imperatives | 1, 4, 8, 10, 11, 12, 13, 14, 16, 17, 20 |
Location | Virginia Beach, Virginia |
Living Transect | Natural Habitat Preserve |
Typology | Building |
Project Area | 403,322 sf |
Gross Building Area | 10,518 sf |
Start of Construction | August 21, 2013 |
Start of Occupancy | January 5, 2015 |
Start of 12-month Performance Period | April 1, 2015 |
Owner Occupied | Yes |
Occupancy Type | Office |
Number of Regular Occupants | 27 |
Number of Visitors | 83 |
Hours of Operation | M-F, 8:30 am – 5 pm, occasional weekend events |
PROJECT TEAM
Owner | Chesapeake Bay Foundation |
---|---|
Owner Representative | Skanska |
Project Director/Manager | Chris Gorri |
Architect | SmithGroupJJR |
Contractor | Hourigan Construction |
Mechanical, Electrical, Plumbing, Lighting: | SmithGroupJJR |
Geotechnical | Engineering and Testing Services, Inc. Civil, |
Landscaping | WPL Site Design |
Structural | A&F Engineers |
Interior Design | SmithGroupJJR |
Specialty Consultants | Janet Harrison, J. Harrison, Architects |
PLACE PETAL

SITE INFO
01. LIMITS TO GROWTH IMPERATIVE
Originally a marsh, the land was filled with dredge spoil in the 1970s, turning it into a greyfield. The project site is located within the city limits of Virginia Beach, Virginia. It was slated for development in 2008. However, this project preserves the land’s ecological functioning, providing opportunities for CBF to protect the parcel’s varied habitats and wildlife. The Brock Center was sited to minimize impact to the successional landscape, limiting development beyond a 200-foot setback of wetlands/shore, clustering site elements along the edge of the successional maritime forest. Aggressive limits-of-disturbance were established to minimize impacts to the site during construction. A master plan for CBF’s parcel and adjacent natural areas will guide the restoration of the site back to thriving ecosystems. Remnants of maritime forest that border the site’s northern edge were preserved. CBF has reestablished once naturally occurring wetlands along the shoreline. Marshes formerly filled with dredge spoils are now experiencing ecological succession, and thereby transformation into vibrant salt meadows. Protecting these habitats has supported wildlife on the site. At least 122 species of birds have been identified using the site including for vital migration open space habitat. The northern diamond-backed terrapin, a species of concern, uses the property for nesting and foraging, primarily within one hundred feet of the edge of the tidal waters. Not only does the project protect the critical flora and fauna of the region, but the thriving habitats also allow CBF to use the center as a living classroom in its educational programs.
This site is a fantastic location for an Environmental Education Center, as it provides a wealth of opportunities to study both the ongoing restoration of the landscape and the interface where the land meets the water. The center will be an active demonstration site for important and relevant restoration projects, including living shorelines, oyster, wetland, and other habitat restoration, as well as water quality improvement initiatives. Students will be able to take advantage of the working dock to access the Lynnhaven River and the Chesapeake Bay. At the same site they can also pull a seine net along the beach, paddle up the creek, or do land-based activities.
Locating the Center on an ecologically sensitive site allows the Chesapeake Bay Foundation to implement its advocacy, restoration, and education efforts all in one location.
URBAN AGRICULTURE
The project site is within the L1 Transect, a Natural Habitat Preserve. It was never developed with buildings but was altered by dredge spoil in the 1970s. Although the soil is sandy and not conducive to typical agriculture, we encouraged planting of native species, like blackberries, that will provide food and/or habitat for wildlife. We planted a pollinator garden to support the proliferation of our hardworking and essential pollinating species, like bees and butterflies. Although more aquaculture than agriculture, we are planting oysters in the Lynnhaven River, immediately adjacent to the center. Oysters are filter feeders, filtering and cleaning the water while they feed. They also clear the water by consolidating sedimentation by pelletizing it as part of their feeding process. The oysters in the Lynnhaven River are not intended for consumption but are a part of our education program. The students learn about the benefits of oysters and the part they play in the ecosystem.
04. HUMAN POWERED LIVING IMPERATIVE
Although our site is a Natural Habitat Preserve, it is within the City of Virginia Beach. People who do arrive by automobile are effectively persuaded to get out of their cars and walk the last stretch. Other than three ADA spaces, there is no parking on site. A wooded path connects the building to a nearby road. The existing road, previously improved in anticipation of large-scale site development, was converted to provide on-street parking for visitors. Shuttles take visitors to the Center during larger events. CBF partnered with the City of Virginia Beach to create new community parking north of the site, including preferred spaces for fuel-efficient vehicles and carpoolers.
WATER PETAL
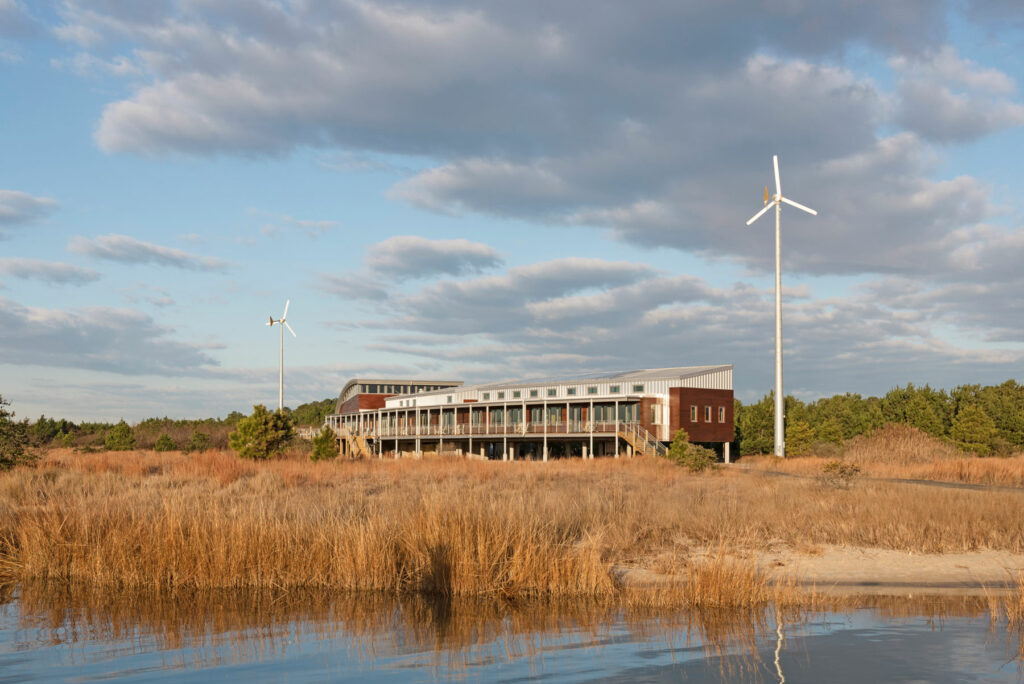
The Center is predicted to be truly net-zero water, possibly the first in the US to receive a commercial permit for drinking treated rainwater in accordance with federal requirements. Water demand calculations were performed for the building based on building occupancies, scheduled uses and design fixture flow rates in order to determine the daily water supply for the building. The design of this building includes several water-saving plumbing devices such as composting toilets, low-flow lavatories, low-flow kitchen sinks and a low-flow shower. All landscaping is native to the region and does not require permanent irrigation. Given the plentiful and consistent availability of rain, the challenge in achieving Net-zero water was primarily getting the regulatory approvals to allow treated rain to meet both potable and non-potable water demand. At the onset of design, the team met with regional representatives from the State Department of Health and the Virginia Office of Drinking Water (ODW). The design team’s challenge was to design a waterworks that met all NSF standards and state-regulations, but were appropriately scaled for a very small project, and can be maintained by an in-house staff operator on a daily basis. Two standing seam metal roofs capture rainwater, filling two 1650-gallon cisterns, enough to withstand 23 days of drought. Rainwater is filtered (four log filters) and disinfected (ozone and UV, chlorine was subsequently added and CBF is appealing this requirement), and supplies all water uses within the Center.
ECOLOGICAL WATER FLOW
Composting toilets reduce water demand while also treating waste on-site. Solid compost is used on-site, while leachate is stored and sent to a local struvite reactor and converted into commercially available fertilizer. Greywater from sinks and showers is piped to a greywater rain-garden (raised above sea-level) that treats the water, allowing it to infiltrate. Excess roof runoff is diverted to raingardens that naturally filter and infiltrate runoff, managing all stormwater on site. All hardscape is composed of permeable pavers and gravel, with adjacent raingardens and bioswales to treat runoff, allowing for infiltration. The design includes a City-owned parking area north of the site that features low-impact design strategies, which has become a model for future City projects.
LESSONS LEARNED
We did learn that rainwater is very “soft” water and can be corrosive. Our team learned that the soft rainwater was taking on high levels of copper from the copper piping that distributes it. This could lead to long-term health concerns as well as to decrease the longevity of the copper piping. The solution was to install a calcium contactor – a water hardener – to stabilize the rainwater, improve its taste, and eliminate concerns over corrosion.
Learn more about the Brock Center’s approach to permitting their water system in this case study.
ENERGY PETAL
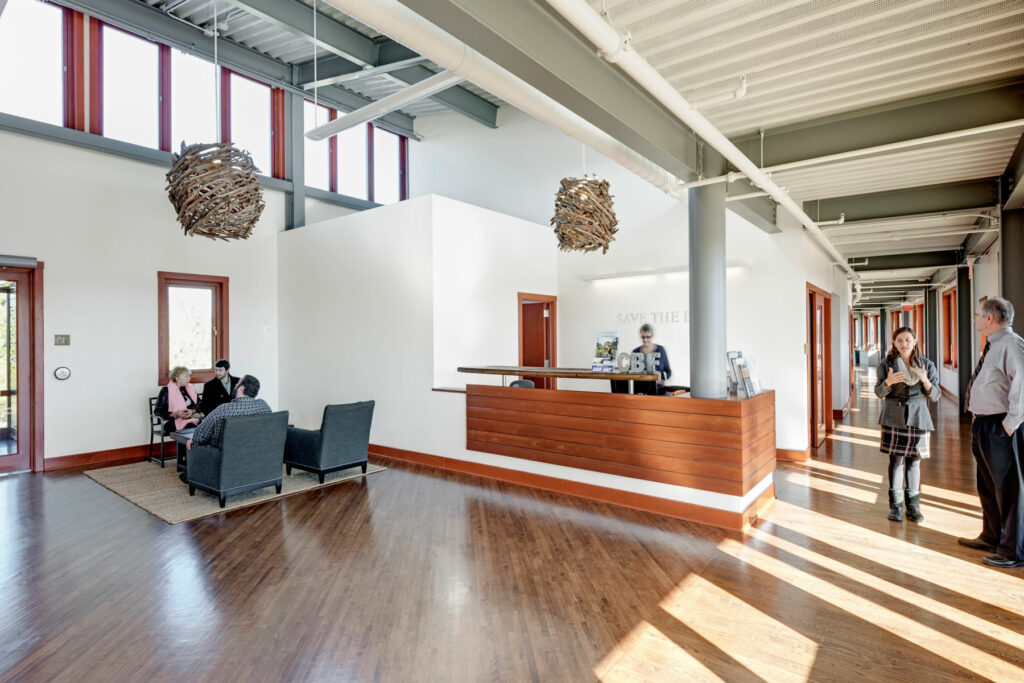
Our approach to achieving net-zero energy began by lowering the building’s electricity consumption as much as possible before designing renewable energy systems to offset that consumption. Conservation strategies were organized into passive and active approaches. The net impact of these conservation measures reduced Brock’s predicted energy consumption down to a very low Energy Use Intensity (EUI) of 15.5 kBTU/sf/yr.
Energy modeling efforts began during the earliest design phase and informed energy conservation priorities, as well as the building orientation and form. The team developed a natural ventilation strategy to address bi-directional wind patterns. The building was designed to take advantage of the natural breezes prevalent near the Chesapeake Bay, with windows and even walls designed to open up and take advantage of airflow. The building was designed to maximize diffused daylighting from the north while shielding the building interior from direct sunlight from the south. In all of these cases, extensive computer modeling was used to optimize each of these selections. Even the roof and wall construction were modeled to determine the optimal R-value.
An iterative design process was also used to determine the most energy-efficient active systems to implement on the project. The mechanical system uses a variable-refrigerant flow (VRF) system with geothermal wells. Electric lighting was modeled to ensure that target light levels would be provided and with no overlit spaces. In addition, a photosensor dimming-control system was used in almost every space to reduce the electric lighting when sufficient daylight is present.
The wind-turbine system consists of two 10-kW turbines, each on a 70-ft pole. The turbines were located off the east and west ends of the building, as far away as possible from nearby trees, but close enough to limit site disturbances. The design team chose wind turbines manufactured by Bergey because they were the only small-scale turbines whose output was certified by the Small Wind Certification Council (SWCC). The PV system designed for the building originally consisted of (141) 270-W modules for a total of 40 kWp (kilowatt peak). Solar insolation modeling was performed to determine the areas of the roof with the highest insolation values. The PV system was located on the sloped roof with additional space allocated for more modules to be added in the future. Shortly after construction was completed, the client team opted to install 6.5 kW of additional PV modules. Due to the early planning on both the roof system and the electrical system, they were added fairly easily.
LESSONS LEARNED
The wind turbines involved some regulatory hurdles to overcome due to air rights (i.e., possible aircraft interference) and local zoning ordinances. A permit was submitted to the FAA and to the City of Virginia Beach, and granted.
HEALTH & HAPPINESS PETAL
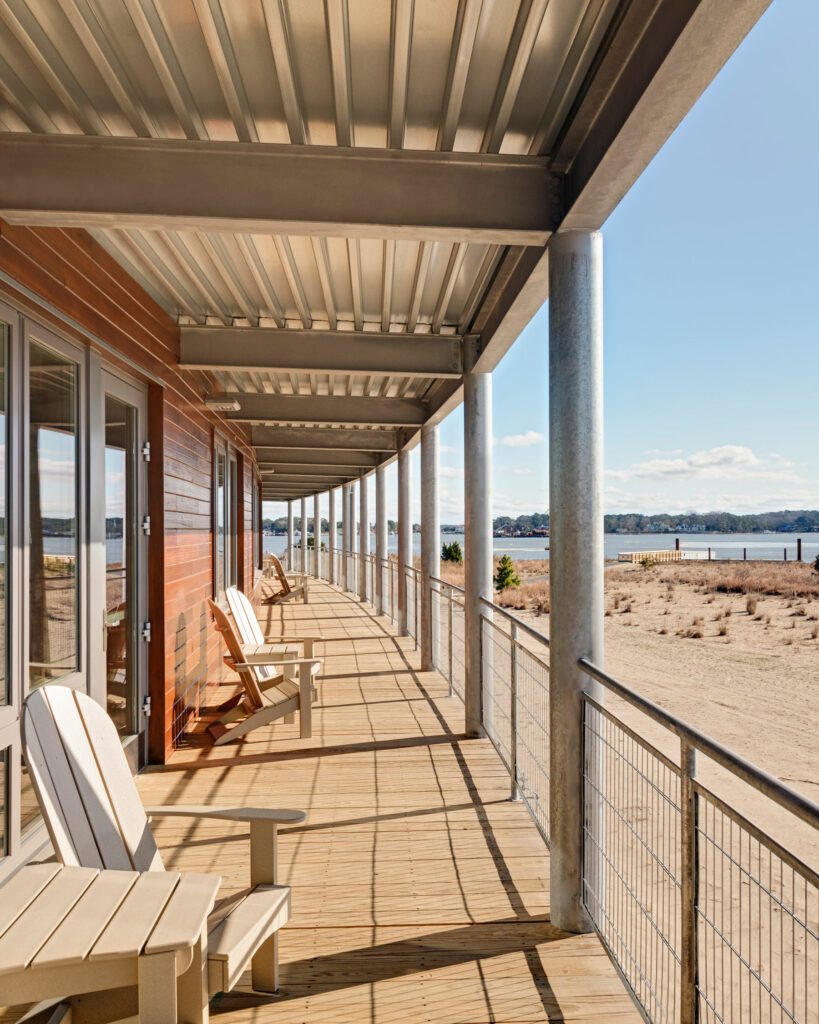
08. HEALTHY INTERIOR ENVIRONMENT IMPERATIVE
Creating a healthy, inspiring space for the occupants was a primary goal from the outset.
The occupants enjoy the clean air, daylighting, and a deep connection with nature provided by the sweeping view of the marsh and river. The users get fresh air and a bit of exercise walking to and from their cars, which are parked offsite. A charrette early in the design phase included a biomimicry brainstorm session, resulting in many biophilic elements to the design. The massing of the building is long and narrow, following the curve of the beach. The thin section allows ample opportunities for daylighting and natural ventilation. For a true connection to the outdoors, the center includes not only great views but also numerous opportunities for occupants to actually get outside. The decks are overflow space, easily accessible for breaks. The dog trot functions as a break room or eating space immediately adjacent to the kitchen/lunchroom. The education pavilion is an actual outdoor space so that students are totally immersed in the outdoors and can feel their feet touching the earth, while they are also sheltered from sun and rain.
There is a green cleaning policy in place to ensure that the air remains clean and toxin-free. During the construction phase an indoor air quality plan was implemented to ensure that the air in the building remained fresh and clean. Mobile units were rented so that the new HVAV system was not used before occupancy; all ductwork and equipment was kept wrapped and protected during construction. The filters were changed and air was tested prior to occupancy. All paints, coatings, other building products, and cleaning products were low VOC and non-toxic to protect the health of both workers and future occupants. Materials were kept dry and the construction site was cleaned daily.
CIVILIZED ENVIRONMENT
The Center uses natural ventilation and daylighting to provide lighting and passive cooling for all public spaces (excluding restrooms, MEP rooms, and storage areas). During design, simulation tools ensured that window glazing, configuration, size, and location optimized daylight, views, and ventilation without creating glare or unwanted solar gain. A white, acoustical metal deck ceiling and high, north clerestory windows maximize daylighting effectiveness. The building’s shallow (33’ deep) footprint facilitates the effectiveness of both daylighting and natural ventilation. The primary circulation corridor along the south edge buffers workstations from direct daylight and cool breezes, extending the natural ventilation season. Bi-directional breezes are captured with low inlets and high outlets on both North and South facades. When sensors determine climate suitability, mechanical cooling shuts and automated controls send an email to staff alerting them to open windows, using a combination of hand-crank and motorized operators. Motorized windows allow night-flush of the interior to pre-cool the interior during cooling-driven months.
The only exception to the availability of operable windows is one small meeting space that has borrowed light and air. We posted to the dialog to confirm that this would meet the intent of the imperative.
HEALTHY AIR
The Brock Center contains bathrooms, a warming kitchen, and a janitorial closet that are each exhausted to create negative pressure with respect to adjacent spaces when the doors to these rooms are closed. The kitchen and janitorial closet are each provided with a ceiling-mounted exhaust fan. The bathrooms use composting toilets that pull room air through the toilet fixture into the composting unit, maintaining negative pressure within each bathroom, preventing odors. The composting unit below is exhausted. The exhausts for the composting toilets are on battery back-up so that odors don’t create a problem during a power failure. Outdoor air supply systems serving all regularly occupied areas are sized to accommodate filtration media with a MERV rating of 13 or higher. New filtration media that met this MERV rating was installed after construction and prior to occupancy.
All visitors and staff will enter into the Brock Environmental Center at the front door. A stainless steel foot grille has been provided at this access point. While there are additional exterior exits from the building, they will be used significantly less, primarily to access the project’s elevated decks. In lieu of providing permanent entryway grilles at each of these doors, the design team has provided foot grilles at the tops of all ramps and stairs that lead to the building’s elevated decks. Refer to the diagram below. Thus, no matter where you enter the building you will walk across 10’ of foot grille, preventing the occasional staff member from tracking sand from the site onto the decks and into the building.
BIOPHILIA
The Brock Center incorporates natural materials into the building facades, most notably the reclaimed cypress left with a transparent finish. This material makes a connection to the adjacent maritime forest, connecting the building with its setting. The Center also uses color to reinforce a connection to the site. The color of accent walls inside the Center was selected by sampling colors found on site. The long attenuated building form, orientation, and elevation above grade creates abundant vistas to the shoreline creating a connection to the site.
The curved shape of the conference room recalls natural shapes and forms – the diamondback terrapin shell, an oyster shell, or the wingspan of a gull. The roof is clad in metal tiles recalling fish scales. The interior vaulted shape resists straight lines, with beams that recall curving limbs of windswept live oaks found on site.
The diagonal wood flooring pattern found throughout creates a unifying geometry despite the irregular shape of the building, integrating the various rooms that comprise the center into a cohesive whole. The floor pattern inside the conference room builds on the diagonal pattern evolving it into a spiraling fractal. The pattern spirals towards the center of the room, creating a central focus point in contrast to the room’s complicated geometry.
Along the building’s length, interior volumes are comprised of two parallel spatial elements: a relatively low, flat ceiling space that abuts the taller sloped ceiling space. The lower space is half interior and half exterior, with the building enclosure running down the middle. The exterior porch and interior corridor have parallel forms, blurring the distinction between inside and outside. The taller office volume uses the element of spaciousness with its tall ceilings and openness, contrasting the space of the lower porch/corridor.
The Center’s massing responds to the unique characteristics of its site. The horizontality of the building form reflects the site: low marshes, extended horizons, extensive shoreline. The form was inspired by regional cultural elements influences, including Native American “long houses” (simple, vaulted shapes and long building forms), plantation houses (elevated on stilts with wrap-around porches), and southern vernacular dogtrot houses (two masses with an open porch in the middle, united by a consistent roof).
The visitor arrival sequence captures the idea of exploration and discovery. Visitors park off-site and the 5-10 minute walk along a path through the maritime forest fosters a sense of exploration and discovery. At the end of the path, the site opens up revealing the shoreline and the Center. Visitors arrive at the open-air pavilion whose form offers both prospect and refuge from the elements overlooking the vistas to the south and west. Programmatically it is a literal example of security and protection providing shelter from the elements on rainy days – allowing its inhabitants to engage with nature while remaining protected from its forces.
MATERIALS PETAL

Our approach to achieving the Materials Petal Imperatives was a monumental team effort. We considered strategies for each phase of the project, from design to construction to operation, through adaptive reuse or end of life/deconstruction.
Early in the design phase, we held a materials charrette to start to sort out our priorities and responsibilities. Our overall strategy was to focus on pure, simple, local, natural, uncomplicated materials. We first reduced the size of the building, and therefore the materials needed, by tightening up spaces and providing outdoor spaces where possible. We considered the appropriate durability of (Stewart Brand’s) different layers; site, structure, skin, services, space plan, and “stuff.” For the structure, we balanced the embodied energy cost of concrete against the durability needed on this coastal site. For the skin, we weighed the environmental issues of foam against the advantages of a tight and well-insulated envelope.
During construction, vigilance was key to making sure we followed through on the materials goals. We used the submission process to double check all materials to make sure they complied with the Red List, responsible industry, and sourcing requirements. Some product information had changed since the original research so we had to react quickly when revetting materials during construction. It turned out to be a challenge to find wood products that complied with both responsible industry and sourcing, so salvaged wood was used extensively. Construction waste was sorted offsite for a recovery rate of over 95%.
In their operations, the Chesapeake Bay Foundation naturally has a strong ethic of conservation. This is expressed both in their building and in their office policies. Consumables, i.e., paper, bottles, and cans are recycled. Durables, i.e., computers, cell phones, and other electronic equipment are recycled. Kitchen scraps are composted. Solid waste from the toilets is composted, including the toilet paper. Even the liquid waste from the toilets is converted to fertilizer at the struvite plant. For events, whether in house or as part of catering contracts, they follow green policies which address printed materials, catering, meeting materials, transportation, and cleanup.
Our goal was to postpone the end of life phase of the project as long as possible by making the building flexible, beautiful, and durable. The flexible open plan will allow changes in use. A beautiful building is more likely to be cared for and less likely to be demolished. The building is durable, designed for the onset of sea-level rise and more numerous hurricanes. But if and when the time comes, the center’s design also anticipates its future disassembly. Materials such as uncoated, panelized materials like zinc shingles, standing seam roofing, panelized PVs, and fastener-attached assemblies, can be disassembled to be reused or easily recycled.
10. RED LIST IMPERATIVE
The Red List imperative was a significant challenge, in which the key to success was staying abreast of the research and providing transparency throughout.
We tackled the Red List early in the design phase, where a charrette was held to begin the research. The first step was to understand the requirements. Then we researched materials that would be acceptable prior to making decisions on construction materials. Key to making decisions on appropriate materials, sourcing and construction, was the formation of a Red List team consisting of the owner, architect, contractor, owner’s rep, and green consultant, meeting weekly to track issues and progress. Our best successes were when we were able to start real conversations with the manufacturers.
The biggest impediment to complying with the Red List was transparency, so the proprietary exception was used extensively. Another challenge was getting information on all the tiny parts of complicated products, so the complex components exception was invaluable. The sheer volume of tiny parts was overwhelming, so the miscellaneous hardware exception was useful.
11. EMBODIED CARBON FOOTPRINT IMPERATIVE
In order to achieve a true zero carbon building, we not only operate at net zero energy every year but have also offset the environmental cost of construction and materials. We purchased 1,234 metric tonnes of carbon offsets through Sterling Planet to support a Landfill Gas to Energy project in Dartmouth, Massachusetts. The Greater New Bedford Landfill Gas Utilization Project diverts the landfill gas for use as fuel in four reciprocating internal combustion engine-generator sets that are specially designed for combustion of LFG.
Landfill gas (mostly methane) is generated during the natural process of bacterial decomposition of organic material contained in municipal solid waste landfills. If allowed to be released into the atmosphere, it is a powerful greenhouse gas. Instead it can be captured and put to productive use as a fuel to produce energy, taking the place of natural gas, fuel oil, or coal.
12. RESPONSIBLE INDUSTRY IMPERATIVE
All virgin wood was FSC-certified. However, certified wood was not easily sourced in the Hampton Roads region. The lack of local supply necessitated several zone jumps.
Even when expanding the zone to include more distant suppliers, it was a challenge to find and document certified wood. But we didn’t want that to discourage the use of wood. Wood is a natural renewable resource. It is a warm and wonderful product, each piece with its own fingerprint, its story recorded in the rings. Instead, the challenge inspired an ambitious search for salvaged wood products. Now each piece of salvaged wood holds layers of stories, first the rings from its life as a tree, then more from its previous life in other forms.
All wood doors were salvaged from local demolition projects. Maple floors from a local gymnasium were transformed into interior flooring. All interior wood trim was made from salvaged school bleachers (students’ carvings/graffiti were preserved). The wood siding was milled from cypress “sinker logs” – remnants from 19th-century logging, recovered from the bottom of rivers centuries later.
13. LIVING ECONOMY SOURCING IMPERATIVE
Whenever possible, natural materials from the US Southeast (wood, uncoated metals) were selected to reinforce a sense of place and biophilic goals. Products were locally sourced (500 km radius for dense materials) and the vast majority of materials, like wood siding, zinc shingles, drywall, lighting, mechanical systems, appliances, and finishes are all US-made.
Complicated products were some of the most challenging to source, so the “complex components” clause was a helpful exception. As with the Red List, transparency remained one of the toughest challenges for appropriate sourcing. The proprietary exception was particularly helpful. Another invaluable policy was the fact that miscellaneous hardware was not tracked.
We struggled to find drywall within our radius that was not intentionally made of coal ash with traces of mercury. In the end, the manufacturer helped us by making a special custom edition out of natural gypsum.
14. NET POSITIVE WASTE IMPERATIVE
CONSERVATION AND REUSE
The Brock Conservation Management Plan considered material efficiency as an issue in all phases of the project, from conception to construction, occupancy, and eventual deconstruction.
In the design phase, much thought was put into how to prolong the life of the building and delay any deconstruction. Considerations to minimize waste over the anticipated life of the Brock Center informed the project planning, design, and material selection.
During construction, much salvage was used to eliminate production of new materials. All materials were optimized and re-purposed to the greatest extent possible. For example, all concrete waste was reused as crushed aggregate for the entry road and fire lane. The majority of the wood framing scraps were re-used for blocking and support within the walls. The foam insulation scraps were sent back to the factory to be reborn as new insulation. All materials that were deemed unsuitable for re-use or optimization on the project were recycled to the furthest extent possible. Overall, more than 95% of the construction waste was recycled.
For operations, there is a strong policy of conservation, reusing, recycling, and composting everything, from kitchen scraps to toilets waste. The building is designed to be easily disassembled, with pure uncomplicated panelized materials like metal shingles and standing seam roofing.
SALVAGED MATERIALS
Salvaged building products were used extensively and celebrated within the design.
- All cabinets, countertops, mirrors, sinks, toilet accessories, lockers, etc. were salvaged from local demolition projects. Cabinet pulls were made from salvaged champagne corks, a reminder of happy occasions.
- The wood siding was milled from cypress “sinker logs”—remnants from 19th century logging, recovered from the bottom of rivers centuries later.
- All interior wood trim was made from salvaged bleachers, full of character where students’ carvings/graffiti were preserved.
- All wood doors were salvaged from local demolition projects. After struggling to find the correct size, a creative solution was found – the doors are trimmed top and bottom trim with the bleacher wood to add a few inches.
- Maple floors from a local gymnasium were transformed into interior flooring. The salvaged aspect of the gym flooring was highlighted by keeping a patch of unfinished flooring in one of the small telephone rooms. The flooring is in its “found” state, complete with a delightful random colorful pattern made from the shuffled stripes of the gym flooring. Adjacent to the finished product, it is a popular teachable moment on the building tours, as is all the salvaged wood.
EQUITY PETAL
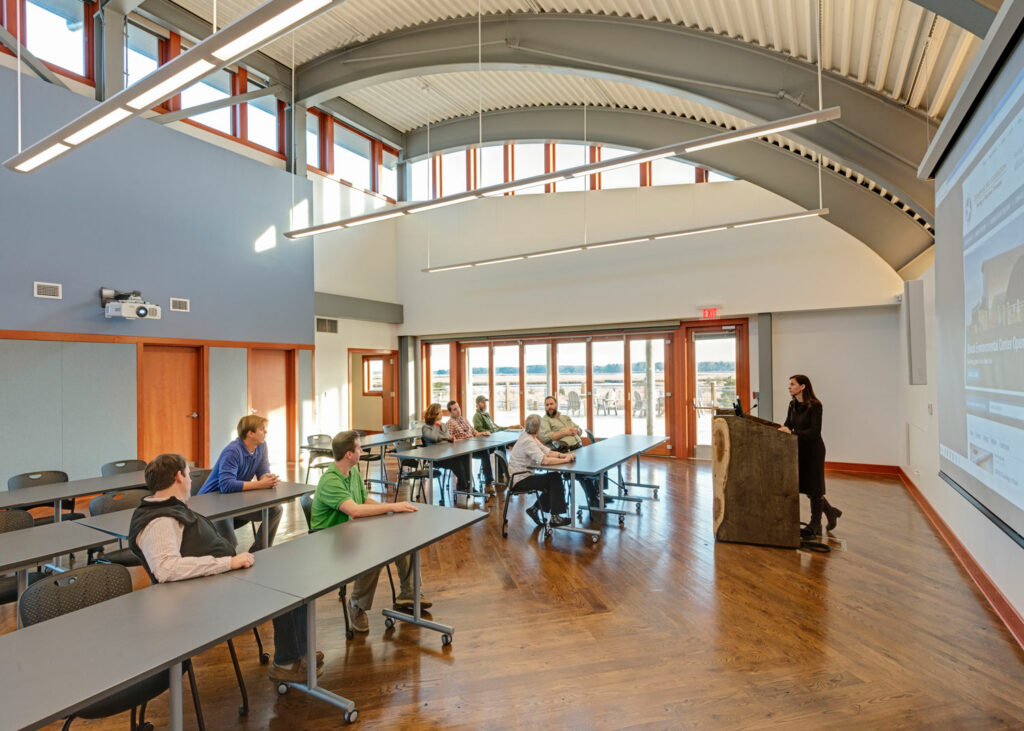
The Brock Center’s design is focused on human-scaled places that enrich the human experience. Other than three ADA parking spaces that provide universal access to the Center, there is no parking on site. The roads in the adjacent Ocean Park community, previously improved in anticipation of large-scale site development, were converted to provide on-street parking for visitors. Locating parking within the community also promotes connection and interaction with the neighbors. An 8-foot-wide path meanders through the site’s maritime forest, connecting visitors from the community to the Brock Center, while providing decompression from the world of automobiles. Visitors pass through a human-scaled gateway made from local driftwood, providing a sense of arrival and a threshold to a place where cars are no longer present; instead this is a place for people.
The Center itself is human-scaled. Its one-story design and features like porches and decks provide a comfortable, human scale. While there is no zoning height limit for the Brock Center, the design respects the height limit of the adjacent community, connecting it to the adjacent Ocean Park neighborhood without compromising neighbors’ views. The site is fully accessible to the community who use it for birdwatching, fishing, and connecting to this unique place. Prominent outdoor spaces provide places for gathering, and the circular shape of the south deck promotes a sense of community.
Inside the Center, tenant office space is provided for local environmental groups and the center’s open design promotes collaboration between partners with related missions to protect the Bay. Since opening, the Hampton Roads chapter of the US Green Building Council uses the Center for its monthly meetings and frequent events. The Center’s multi-purpose room is available to the local community and in a sense the Brock Center serves as a community meeting place for the Ocean Park neighborhood.
16. UNIVERSAL ACCESS TO NATURE & PLACE IMPERATIVE
DEMOCRACY & SOCIAL JUSTICE
Because of its unique location within the City of Virginia Beach yet at the water’s edge, this once-private site has historically attracted much recreational use. A community partnership with CBF, the City of Virginia Beach, and the Trust for Public Land purchased the land, preserving it for open space, passive recreation, and environmental education. The preservation of Pleasure House Point saved this once-private parcel from over-development, transforming it to a public, preserved natural area serving the local Ocean Park community. One hundred acres of the original site now comprise a city park. The other ten acres was purchased by CBF for the Brock Center and remains open to the public. Neighbors continue to walk, run and fish on the property. There are no gates that separate the existing trails on site from the Brock property, beyond those required to control access to the Center itself after hours for security purposes.
Effortless accessibility for all was a guiding design principle from the start for the Brock Center. All spaces within the Center meet the latest federal regulations for accessibility. The only parking on the Brock Center site consists of three ADA parking spaces located close to the building entrance. Although the site conditions dictated that the whole building be raised well above grade, the center itself is one level. The permeable paved path that leads to the Center transforms into a wood walkway that ramps to the elevated plinth on which the Center sits. A second ramp leads from the South deck back to grade insuring accessibility.
The project designer broke his leg in a bicycling accident 3 months before the Center’s construction was completed, and was bound to a wheelchair during the final construction and the building dedication. He completed the building punchlist, inspecting all portions of the building while in a wheelchair, and learned (the hard way) the importance of universal accessibility.
RIGHTS TO NATURE
The Brock Center is located far from adjoining properties and is only a one-story building. Even its tallest element – the two 70’ tall wind turbines – do not cast shadows that leave the property line nor do they shade adjacent structures.
The project boundary is more than sixty meters long, parallel to the edge of an adjacent waterway. The eastern edge of the property line consists of approximately 195 meters of shoreline of Crab Creek on the Lynnhaven Inlet. The Brock Center did not restrict access to any of the existing pathways that follow the shoreline. The community that uses Pleasure House Point, the natural preserve that surrounds the Brock Center, have unrestricted access and no fences or boundaries existing restricting access to the entire preserve, including the shoreline.
BEAUTY PETAL
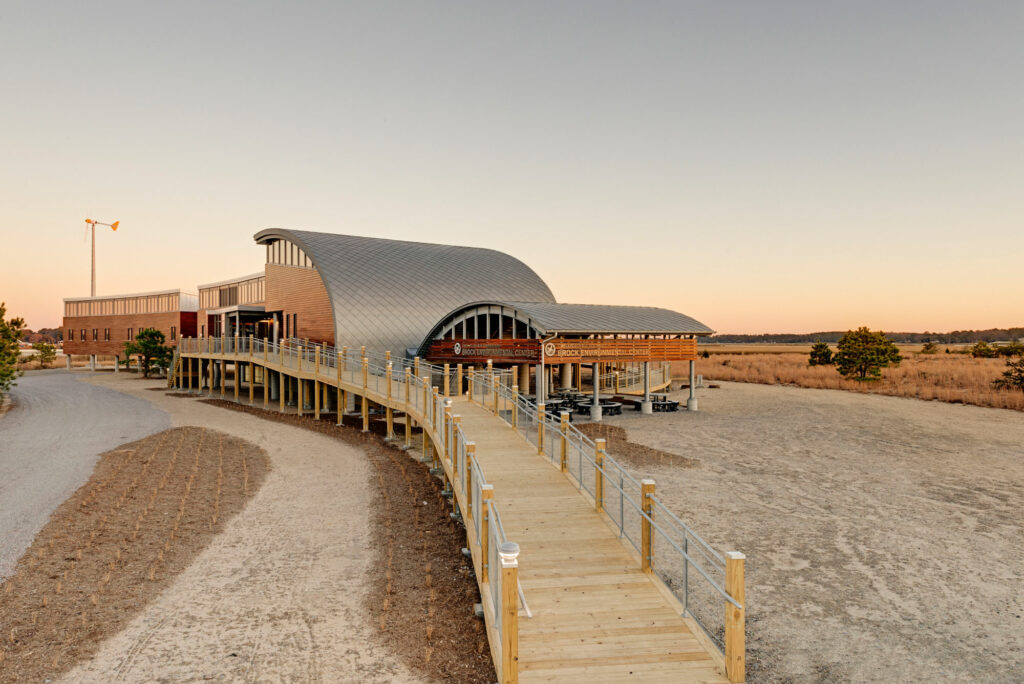


The major conceptual design moves for the Brock Center were not only informed by resource efficiency, performance, and passive design strategies, but also an effort to make the center beautiful and compelling – a memorable place that draws visitors in and celebrates the client’s mission and site.
The iconic curved elements of the Brock Center’s westernmost form were a response to the pedestrian approach to the Center. Since no cars park on the site, both staff and visitors approach the Center from the northwest. As a result, the Center’s westernmost portion is highly prominent – an opportunity to engage those who arrive and to excite them to see more, providing a threshold to the exquisite landscape beyond. The design for this frontispiece sought to create something iconic, beautiful, and to capture the spirit of CBF and the site. Prominent, curving roofs recall forms of the site’s windswept live oaks, the wings of a gull (CBF’s logo), and the protective shell of an oyster. The zinc shingles that clad the composition recall fish scales adding texture and interest. Their subtle reflectivity catch the light, shimmering like the Bay itself.
The Center curves in plan as well. Sustainable design strategies resulted in a very long building form. Our design sought to avoid the look of a long interior corridor that provides circulation from end to end. The solution was to curve the footprint in plan so one never sees the end of the corridor until you’ve arrived near its end; instead, the convex shape draws one’s focus outward, compelling guests to explore the building’s length.
Salvaged materials all had a unique story and they were incorporated in a manner to celebrate their past lives. Wood trim and casings were made from bleachers salvaged from a local high school. Rather than refinishing the wood to look like new, instead they were left imperfect – students’ carvings and bolt holes left intact giving clues to their former life. Maple gym floors were salvaged and refinished with the exception of in one room where the strip gym floor planks were left in their original state so visitors can appreciate their former history. Some visitors to the Center grew-up playing sports on these very floors. Cabinet pulls and artwork in the staff dining room utilized champagne corks salvaged by local neighbors and staff during the design and construction of the center. These corks hold the memory of celebrations and the collective contributions of the community that surround the Brock Center. These details are rich with memory, contributing to the sense of delight and the celebration of culture, spirit, and place.
20. INSPIRATION & EDUCATION IMPERATIVE
The Brock Center serves as CBF’s lower Bay beachhead, integrating CBF advocacy, restoration and education programs into one site. The site was chosen as an ideal platform to conduct education programs, that both inspire people to the Bay’s richness and delicate balance, as well as being an example of how to mitigate the effect of the built environment to maintain a preferred balance between people and environment.
The cornerstone of the education conducted at the Brock Center is the hands-on, field-based environmental education program. This program provide significant outdoor learning experiences by engaging over 2,000 students, teachers, citizens, and community leaders each year. Participants use the center’s education pavilion, waterfront pier, education vessel, canoes, marsh and beach as platforms to investigate the local environment. The education vessel embarks to the Lynnhaven River and Chesapeake Bay engaging participants in open water studies, including catching marine life through trawl nets and testing water quality. The canoes, hikes and seining conducted in and around the marsh and beach provide lessons in the land/water interface so vital to Bay health.
These hands-on activities are the basis for participants to engage in critical thinking to evaluate the health of the ecological system, and promote a healthy balance between human activity and water quality, fisheries, and economics.
In addition to these outdoor educational experiences, the building is designed as a teaching laboratory for all visitors. The components of LBC are brought to life for the visitors through engaging displays and signage, creating a unique educational experience. To promote these features of the building, there is a strong outreach component, including guided tours of the building, making the building available for meetings of local groups, educating architects, engineers, contractors, public officials, and sharing detailed knowledge about green building with other LBC teams.
The Brock Center intends to be an educational platform for all participants and visitors to better learn and act in responsible ways. The result is an exceptionally informed and inspired constituency that values the Bay and its watershed as a living, connected system.