VITAL STATS
Certification Status | Zero Energy Certified |
Version | 1.0 |
Location | Medway, MA USA |
Typology | Existing Building |
Gross Building Area | 35,169 SF |
Start of Occupancy | December 2020 |
Owner Occupied | Yes |
Occupancy Type | Municipal Building |
Number of Occupants | 15 |
PROJECT TEAM
Owner | Town of Medway |
General Contractor | Colantonio, Inc. |
Architect | Helene Karl Architects, Inc. |
Mechanical Engineer | Seaman Engineering Corporation |
Electrical Contractor | John Murphy Jr. Construction and Electrical Engineering, Inc. |
Interior Designer | Helene Karl Architects, Inc. |
Plumbing | Seaman Engineering Corporation |
Civil and Structural Engineer | Symmes, Maini and McKee Associates |
Landscape | Helene Karl Architects, Inc. |
Certification Consultant | Helene Karl Architects, Inc. |
RENEWABLE PRODUCTION SYSTEMS INFORMATION
ENERGY PERFORMANCE
Renewable Type | Solar Electric (PV) |
Total Renewable Capacity | 250 kW |
Renewable Location | On-site |
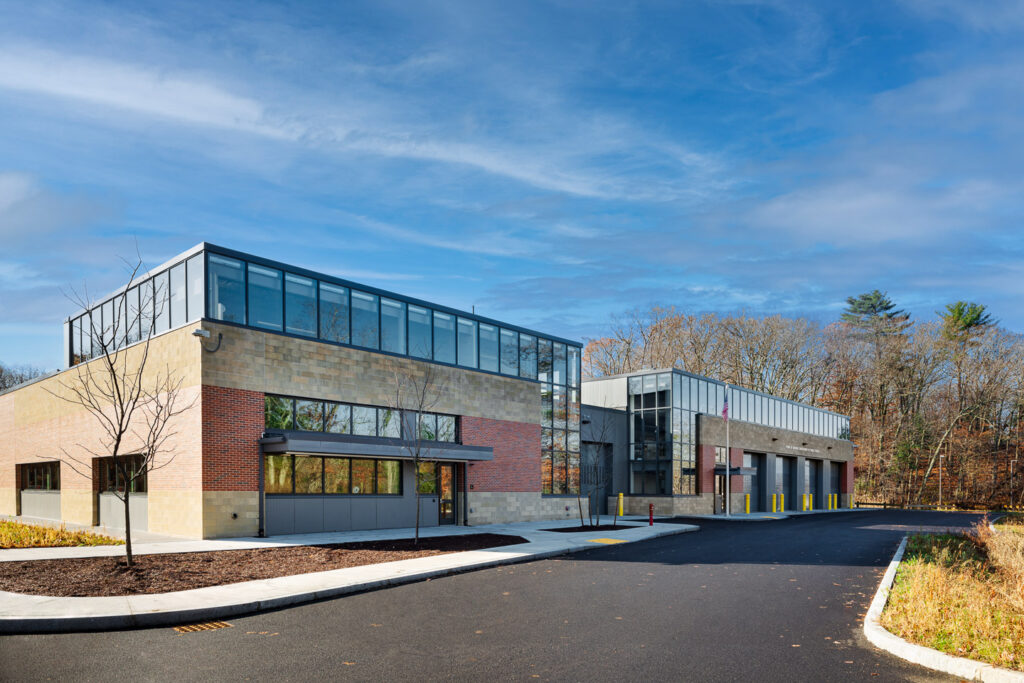
PROJECT LEADERSHIP AND STORY OF THE PROJECT
This is a story of public taxpayer dollars becoming a zero-energy certified municipal building in Massachusetts (MA). MA public construction bidding statutes, regulatory requirements, and public approval process are some of the strictest in the country. Despite the challenges, HELENE KARL Architects, Inc. (HKA) successfully negotiated the process to achieve zero-energy certification on the Town of Medway’s New Department of Public Works building.
Public Construction Process in MA
Public Bidding Laws – All projects that receive Massachusetts state and municipal funding are required to comply with the public bidding statutes – MGL c. 149 §44 and MGL c.30 §39M. The intent of the statutes is to make the public bidding process more transparent and to ensure fair competitive bidding. The statutes have unique provisions such as filed sub-bids and the “or equal” provisions. When specifying products (equipment, accessories, materials) for MA publicly funded projects, there must be three or more brands/manufacturers that can supply the products. By law, the products cannot be proprietary to ensure full competition for each product.
Code Requirements – MA leads the country in its commitment to building “green”. Massachusetts has enhanced building codes and executive orders mandating energy efficiency building standards (stretch energy code) that address all aspects of building — – types and sizes, mechanical equipment, building materials, construction techniques, and operating performance criteria.
Approval Process – The majority of municipalities in MA are governed by Town Meeting. Town Meeting is a form of local government in which residents of the Town gather twice a year and act as a legislative body — voting on the Town budgets, bylaws, and other matters for the Town’s operation. When constructing capital projects, this means that the designer must educate both the municipal department (user client) and the Town residents on all aspects of the design — 1) How the building will meet code requirements, 2) how “green” the building construction will be, 3) why certain systems or products have been chosen, and 4) justify the overall budget. The project first goes through multiple local municipal board approvals, such as the Conservation Commission, Zoning Board, and Planning Board. Then the Town residents vote at the Town Meeting and then at the ballot box (two-step process) to approve and fund projects.
How does anything get built!
With all the statutory, regulatory, and procedural restrictions in MA public construction process, you have to wonder how any project is able to be built — let alone achieve zero-energy certification. The building must conform to public bidding laws, meet the energy efficiency building criteria, satisfy the municipal budget constraints, fulfill functional requirements needs, and find consensus on an aesthetic that garners a ‘yes’ vote at the Town Meeting. It is not an easy task but possible!
DESIGN PROCESS
Approach – HKA approaches every project as if it will be zero-energy certified. HKA advises our clients that the nominal cost increases to provide energy efficient details, products, and systems result in an immediate payback through operational and maintenance savings (typically in the first year). HKA employs a standard and simple “kit of parts” to provide an energy-efficient and sustainable building. The specified products and installations are readily available in the marketplace, familiar to the contractors, and easy to use, manage & maintain by the client.
HKA initiates the programming dialog by understanding the client’s intended use of the building, seasonal use patterns, thermal comfort preferences, zones of use, maintenance capabilities, and operational expectations.
After capturing the requirements and expectations, HKA deploys specific design strategies to satisfy the overall energy efficiency goals in building to be zero-energy ready or to achieve zero-energy certification. The design strategies include the following.
- Architectural and structural detailing to minimize thermal bridging.
- Modeling and using insulation material and values to exceed code but not financially exceed the diminishing returns of cost to insulative value.
- Establishing an air sealing metric goal of 0.15 cfm/ft2 under a pressure differential of 0.3 in. water (1.57psf) (75 Pa) when tested in accordance with ASTM E 2178.
- Incorporating natural daylighting using triple-glazed windows as a primary light source supplemented by artificial LED lighting with an interior lighting power density of .3w/sf goal.
- Pairing ASHP/VRF and energy recovery ventilation systems with specific thermostatic set points tailored to the users in the spaces. Ensuring automated temperature setbacks are applied during times when the building is not used.
- Selecting highly energy-efficient plumbing fixtures and equipment, such as an appropriately sized 93% energy recovery electric water heater, to accommodate domestic hot water needs.
- When possible, installing solar renewable energy (PV panels) on the building roof or on exterior parking canopies.
Analysis – After developing the approved building efficiency goals and budget with the client, HKA prepares an Energy Efficiency Summary Memo (EESM) to identify the estimated site EUI of the project using three perspectives.
What if the project is built to –
- The code minimum requirements using traditional building and mechanical systems,
- HKA’s energy efficiency standards, detailing and application of highly efficient MEP systems, and
- HKA’s energy efficiency standards with the application of renewable energy. The EESM provides the list of available Federal, State, and local utility grants & incentive programs, a description of how the programs work, a description of the grant application process, and the expected grant financial benefits.
The EESM also includes a calculated “return on investment” (ROI) estimate that details the energy savings associated with the building design, the renewable energy production capacity, the total grants & incentives available, and the potential future utility energy cost savings.
ENERGY SYSTEMS NARRATIVE
Mechanical System – With the push towards electrification and less reliance on carbon-based fuels in MA, HKA typically employs a combination of ducted electric ASHPs (Air Source Heat Pumps) for heating/cooling and ERV (Energy Recovery Ventilation) with enthalpy for mechanical ventilation and outside fresh air.
Based on field data and monitoring of existing building operations constructed using HKA’s energy efficiency approach, HKA can document that the use of ASHPs for heating & cooling in common spaces (such as open office areas and general spaces) and single cassette electric ASHPs (in private offices, conference rooms or other spaces not regularly used) is a very efficient practice.
Likewise, HKA utilizes motion and CO2 detection to operate the ERV system to ensure that unoccupied or minimally occupied space ventilation is only supplied as required thus minimizing energy consumption. Augmenting the basic building mechanical system with large ceiling fans (basic economical technology) in spaces such as warehouse storage, vehicle repair garages, and vehicle storage garages [where most of the year garage doors are opened], the heating and cooling demand is minimized because the air circulation provides thermal comfort to the occupants.
HKA incorporated all of these mechanical system strategies to achieve zero-energy on the Medway DPW building.
Lighting System – HKA priorities natural lighting for all spaces in the building resulting in significant energy efficiency. HKA locates spaces heavily occupied by people, such as offices, workspaces, and meeting rooms, at the perimeter of the building to maximize the natural lighting with the use of windows and shades. In less occupied spaces, HKA uses clerestory windows and skylights for spaces such as restrooms, storage rooms, and vehicle repair & storage garages. This simple technique of prioritizing natural light typically allows the building occupants to use these spaces during the daytime without having to turn on artificial lighting.
HKA establishes a lighting power density goal of .3 W/sf for projects and specifies highly efficient LED lighting for all interior artificial lighting. Occupancy sensors and photosensors for dimming control the lighting on the interior, and photosensors and timing controls manage exterior lighting. During the commissioning process (Cx), HKA participates in setting the footcandles in the various spaces to ensure comfortable and appropriate lighting levels for all times of the day.
HKA incorporated all of these lighting system strategies to achieve zero-energy on the Medway DPW building.
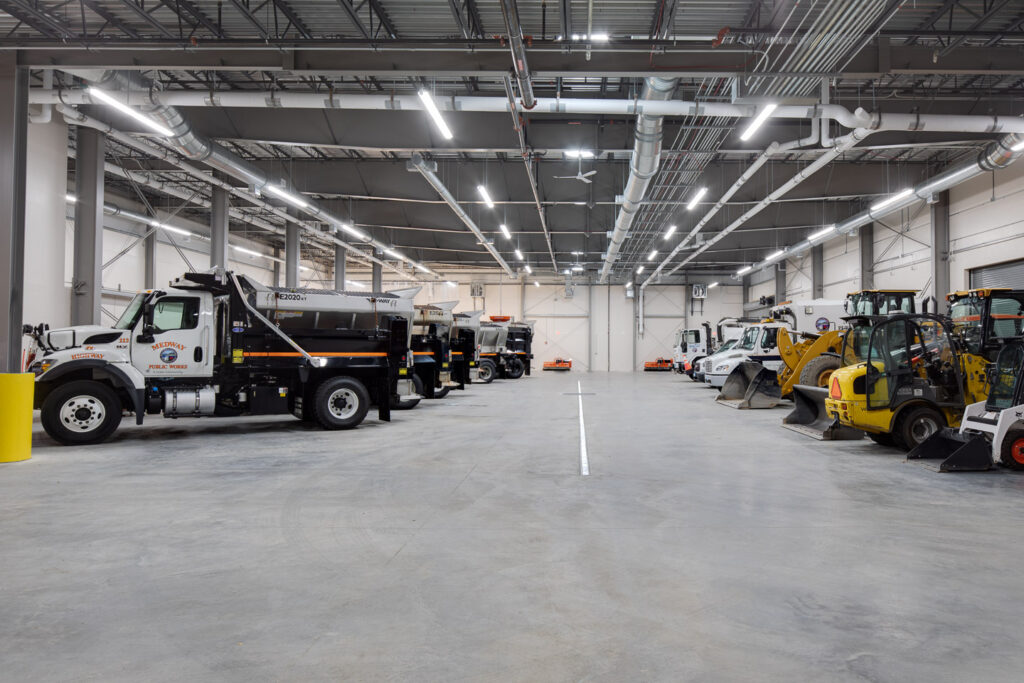
BUILDING COMMISSIONING, START-UP, AND OPTIMIZATION
MA statute requires commissioning of all buildings where the total mechanical equipment capacity is less than 480,000 Btu/h (140.7 kW) cooling capacity and 600,000 Btu/h (175.8 kW) combined service water-heating and space-heating capacity. However, HKA continues to advocate for commissioning, if not enhanced commissioning, on all our projects. The commissioning process is broad, comprehensive, and incorporates all the mechanical, electrical, plumbing, and automatic temperature control systems. While the process can be laborious and challenging, deploying simple building systems greatly expedites the process and leads to greater success for the client to manage the building.
The goals of the commissioning effort are as follows.
- To ensure that all the building systems are completely and correctly installed.
- To certify that the building equipment and systems function together properly and operate per the design intent.
- To deliver the client with a more efficiently operating building that has fewer MEP-related warranty issues than a non-commissioned building.
- To provide the client maintenance personnel with enhanced training and documentation to ensure proper operation of the building systems in the most energy-efficient manner.
The most successful commissioning process engages the commissioning agent at the outset of the design effort to conduct periodic design reviews. During construction, the agent then supports the design team with the submittal review of critical building systems, the on-site start-ups of equipment & systems, and the final performance testing & documentation of the building systems. A good commissioning agent will provide the design team, construction team and client with an added level of expertise and understanding of the building system that allows all parties to make informed decisions.
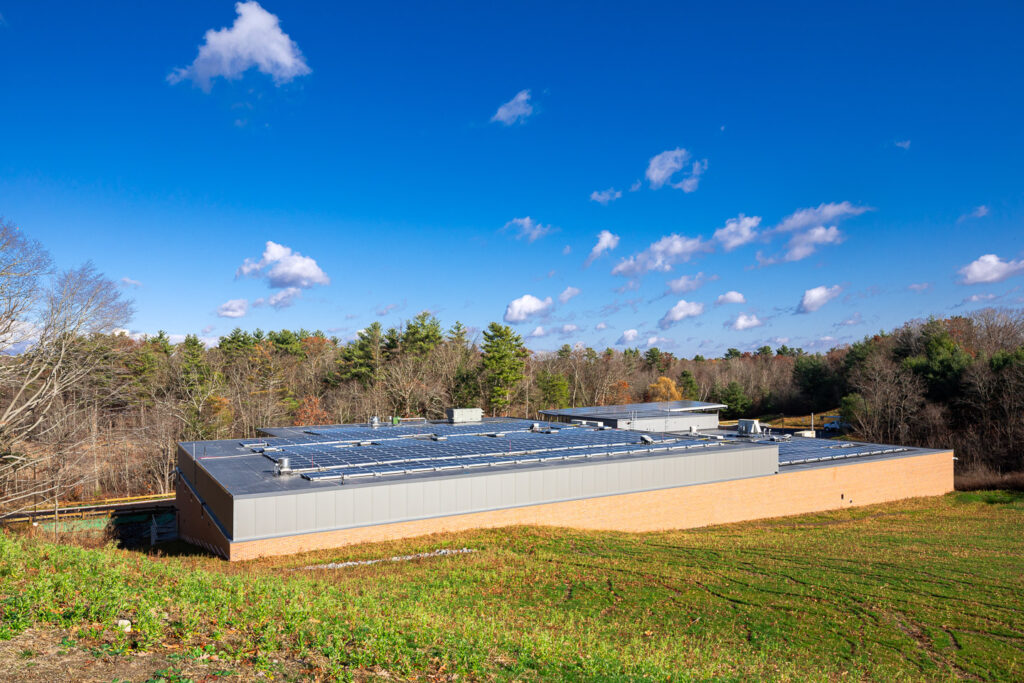
LESSONS LEARNED
HKA has learned that building occupants are unpredictable, and you cannot tell someone how to work or live in a building. More importantly, it is hard to change people’s behavior, so why dictate the way the building is to be used to achieve energy efficiency? Design simple systems that adapt to the user’s behavior so the systems enhance their experience rather than becoming a pain point. Likewise, the building’s original intended use will mostly evolve and change even prior to building occupancy. The construction duration for most new buildings takes a minimum of 12 months, and clients make lots of changes during this period. Clients typically add new functions or reallocate spaces originally intended for one use to another use. Therefore, flexible building systems are critical to satisfying client’s expectations while still maximizing energy efficiency. The building systems must be adaptable to the client’s changing needs/desires during construction and after occupancy of the building.
Goal #1 is to focus on the building envelope to create the most energy-efficient building shell. This single goal provides the greatest and highest value impact on the energy consumption in the building. A highly efficient building envelope (shell) provides the most flexibility to promote energy efficiency. Any systems used in the building will not have to work as hard to adapt to the client’s ever-changing needs and desires.
After creating an efficient building shell, Goal #2 is to select readily available and simple MEP systems deployed in a creative and innovative manner. Start with the basic concept, “If you can use an abacus to satisfy the client’s needs, don’t specify a calculator.” It sounds crazy, but the client’s focus is on their business, not managing the building systems. They don’t care about sophisticated features for future use. The client wants to turn the system on and forget about it. It’s like driving a car; most people know how to start the ignition and drive but have minimal knowledge of how to fix the car when something goes wrong. The building should be the same, so keep it simple.
Remember, most clients struggle to simply maintain the building much less operate the building. If the systems are basic, with the appropriate level of automation and features to meet the client’s need, then maintenance becomes easier because the in-house staff or outside vendors can operate and maintain the systems without specialized expertise or training. Ultimately, if someone doesn’t feel the building is user-friendly, then it gives “green” buildings a bad reputation and thwarts environmental stewardship. Providing the client with a challenging building to operate is counterproductive to setting the new standards of energy efficiency our industry is trying to accomplish.
By approaching the energy efficiency of every project in this manner, HKA is able to navigate the other challenges of funding, consensus building, and the public construction process. That’s how you achieve zero-energy certified buildings on a budget in the public process.