VITAL STATS
Certification Status | Petal Certified |
Version of LBC | 3.1 |
Location | Seattle, WA |
Gross Building Area | 72, 400 SF |
Start of Occupancy | July 2020 |
Full Time Equivalent Occupants | 350 |
TEAM ROSTER
Owner | Fremont Watershed Realty, LLC |
Architect | Weber Thompson |
General Contractor | Turner |
MEP | WSP |
Structural Engineer | DCI |
Civil Engineer | KPFF |
Landscape | Weber Thompson |
Certification Consultant | Weber Thompson, Jared Siliker and Skanska |
TI General Contractors | Shuchart, DowBuilt |
TI Architects | Kang Modern, Gensler, JPC Architects, Weber Thompson |
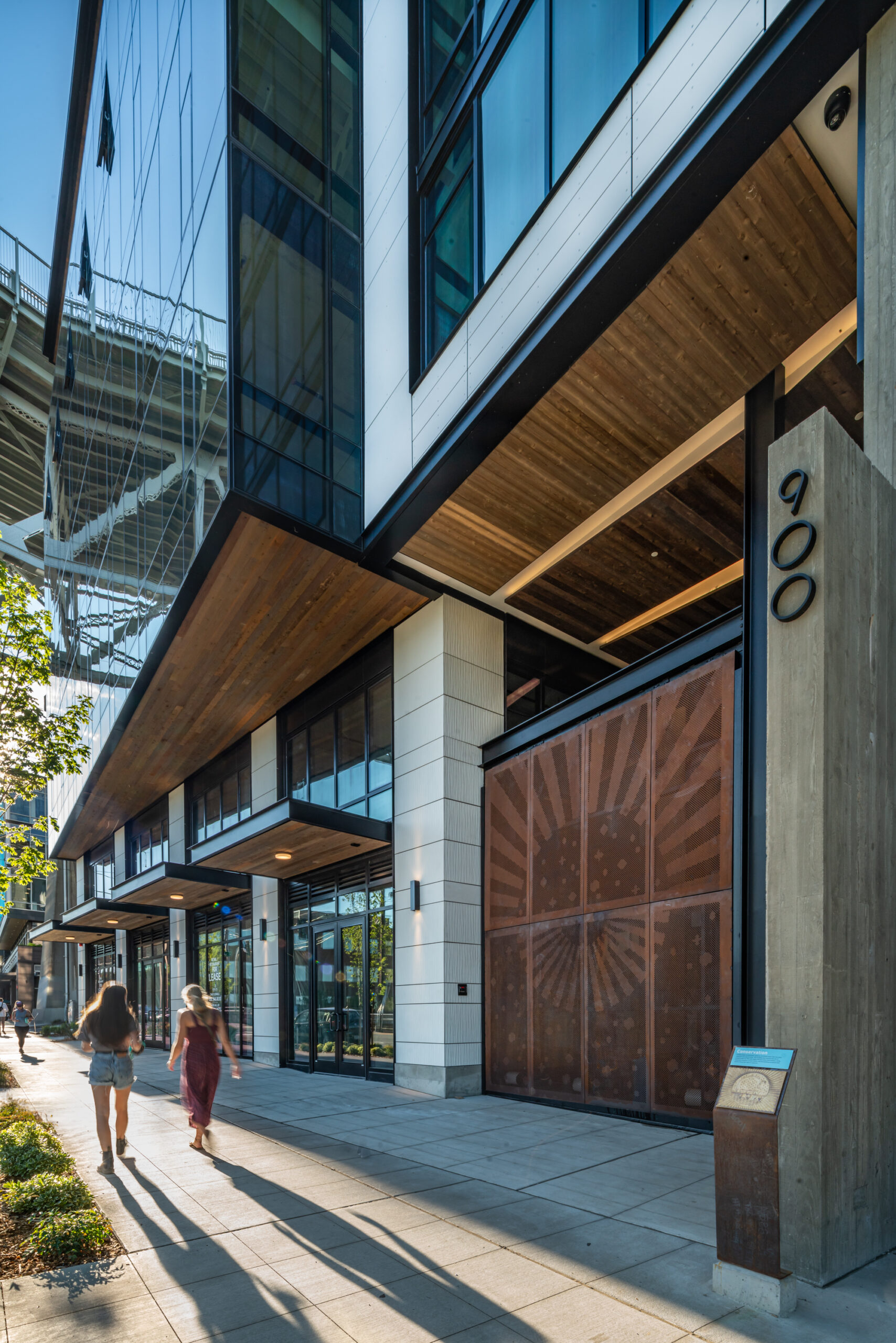
The Watershed Building (previously called the Titan Living Building Pilot Project) is a developer led Core and Shell/TI commercial building located in the Fremont neighborhood of Seattle. The location of the site near the popular Burke Gilman Trail, as well as its proximity to services and transit in the Fremont neighborhood made it an ideal candidate for the Place Petal of the Living Building Challenge. The project also was in a unique location under the Aurora Bridge, and on a slope that leads to Lake Union and the Ship Canal, making it an ideal candidate for the City of Seattle Living Building Pilot Program, based on the stormwater and water reduction requirements within that program.
The Scope of the Core and Shell portion of the project consisted of the structure and enclosure of the building, as well as all common and shared areas, including entrances to the building, bicycle storage and showers, and vertical circulation. Also included was the exterior site and right of way work to meet the City of Seattle stormwater and water reduction requirements.
The Core & Shell General Contractor on the project did change prior to construction, so a concerted effort was made to select a new GC that was committed to executing the project and understood the requirements of the Living Building Challenge certification process. Education was provided and shared with Turner key staff, prior to and after their selection. Turner worked with Skanska to then educate and manage key subcontractors through the submittal and documentation process.
Core & Shell work began very early in the design phase in 2016, under the LBC v3.0 Standard, to establish the other petals that would be achieved (Place and Beauty), and to set up a material petal vetting and documentation process that would enable informed specification selection by the Core and Shell architect, Weber Thompson and documentation by the specification writer, Beth Stroshane. This included using the available version of the v3.0 Material Tracking Spreadsheet to track product specification and vetting, and initiated a “red, yellow, green” process for tracking products that were vetted and met LBC requirements during that design selection phase.
As the project moved to construction, Turner was selected as the General Contractor and engaged with the team to provide the documentation for the vetting process through the submittal and procurement phases. The Material Tracking Spreadsheet continued as the mechanism for tracking and documenting product submittal review and approval for LBC compliance, following the same “red, yellow, green” process, and using Master format specification structure for the tracking of submittals and LBC documents. Over the course of the project, the project transitioned to LBC v3.1.
As part of the selection process for the subcontractors, LBC information sessions were held prior to RFP response, to ensure subcontractors understood the LBC requirements and documentation process prior to providing their proposals. Weekly meetings were held throughout the construction process between Turner, the MEP subcontractors and the Watershed team to ensure LBC specific questions could be answered and submittal documentation was reviewed and meeting requirements.
Core and Shell construction was completed in March 2020.
PLACE PETAL
The Watershed project team chose to fulfill the urban agriculture requirement of the Place Petal by creating an apiary for honeybees to produce honey for occupants of the building to use and enjoy. The team was drawn to the broad, ancillary benefits of introducing pollinators into the ecosystem and the opportunity to produce a food product that could be enjoyed by all on a regular basis.
The team chose honeybees for many reasons, both practical and aspirational. By creating a bee colony, the team believed it could produce a food product with enough volume so that all building users could enjoy at least some of it (hopefully on a regular basis). Further, because an apiary uses little water and no electricity, the team felt this path was in line with Watershed’s goal of reducing water consumption and minimizing energy usage.
As “generalist pollinators,” honeybees also have an added, broader environmental benefit to a diverse range of plants within the 3-mile range of our bees. Watershed’s proximity to multiple green spaces made this location a great candidate for bees. Supportive green spaces include:
- Gas Works Park (0.5 miles)
- The Fremont Cut (0.5 miles)
- Burke Gilman Trial (150 feet)
- Seattle Pacific University, including many managed florals (0.7miles)
- Woodland Park (1.2 miles)
- Meridian Park and Tilth Garden (1.2 miles)
Overall, the amount of nearby forage made Watershed a good candidate to support a large bee population. In turn, the bee population maximizes health and biodiversity of the local ecology. Consulting with a beekeeper, the team confirmed that the project site was supportive of the proposed honeybee species. In addition to its proximity to green spaces (as mentioned above), Watershed is also supportive of bees because it is close to water (Lake Union), and the project’s bioswales provide ideal “brackish or standing water” our beekeeper recommended.
The specific location of the hives on the roof also provides opportunity for direct sunlight on a regular basis. Overall, bees need access to water, a forage range, and sunlight, all of which Watershed was able to provide.
In our research and evaluation, the team recognized that direct physical access to the beehives posed a challenge. As the beekeeper advised, “a curious person poking his or her head into the front of a beehive will engage a defensive reaction from the bees and is likely to get stung.” To handle this obstacle, the team placed the beehives on the roof of the project. There is a ladder for access.
Because the location poses a challenge for regular interaction and harvesting by users, the team relied on sharing images and providing updates.
Along with showing the building’s energy, water and carbon performance, a dashboard in the lobby shows images of the beehives and describes the beekeepers’ means and methods for harvesting. Tenants have also reported seeing bees drinking from the project’s stepped weirs.
Finally, the project makes the final connection between user and agriculture by packaging the honey into jars and distributing it to tenants for daily use and enjoyment. The initial batch yielded about 50 small jars and the team expects this year’s harvest to be even more successful. The team believe that the frequent use and availability of the honey enriches the experience for tenants and provides a daily reminder of the site’s connection to its ecological surroundings.
MATERIALS PETAL
Watershed was a multi-year project that chose to undertake ambitious goals to model the highest possible sustainability standards for a commercial office project. The development team’s goal was to demonstrate that Living Building Challenge Petal Certification was achievable for a speculative, multi-tenant office project. Along the way, there were many lessons learned that the team has sought to document here. The team hopes this will make the path easier for future developers seeking a commercially viable project while demonstrating a deep commitment to sustainability.
General
- All exceptions used on the project will be saved to a master database to be used and shared for future LBC projects. This database will be and has been shared with other teams pursuing Living Building Challenge projects in an effort to scale and streamline Living Building Challenge Materials Petal.
- Do not take a manufacturer letter that states their product is Red List free at face value. Make sure to check and vet supporting documentation (with CAS numbers) against the applicable Red List CAS guide. Manufacturers can make honest mistakes during their own vetting process. For example, a manufacturer may see “rubber” as an ingredient and assume it is a natural rubber that is Red List free, when in reality, that rubber could be neoprene, which is a Red List chemical.
- The team has compiled a list of manufacturers and contacts who typically are responsive and accommodating to the LBC/Red List requirements. This list will be used for future LBC projects.
- While EPDs are not specifically cited as an acceptable form of Red List documentation, some EPDs do provide a full inventory of product components. This can be used as a good reference point with manufacturers that can allow the team to ask more specific questions when requesting complete Red List documentation.
Considerations for Multi-Tenant Projects That Span Multiple LBC Versions
- Watershed’s approach to Tenant Improvements was to give each tenant team as much freedom as possible (a typical commercial model.) The team would now recommend a deeper coordination effort between the individual tenant teams and the core & shell’s Living Building consultant. Assembling information after the fact proved cumbersome and there were missed opportunities to share information.
- Watershed also recommends ensuring Living Building certification documentation and correspondence is not siloed with only specific project team members; because of the length of the project (including COVID-19), Watershed faced staff turnover which posed challenges in ensuring consistency over the life of the project. Watershed recommends redundancy within a project and consistent communication to ensure smooth transitions between unavoidable staff turnover.
Electrical Wiring
- Standard THHN electrical wire contains PVC, standard XHHW electrical wire contains HFRs. THHN is thinner, more maneuverable, and less labor intensive to install and is preferred by electricians for interior use. XHHW is thicker, stiffer/less maneuverable, but more resilient to changes in temperature, chemicals, fire, etc. and is preferred by electricians for exterior/outdoor uses. Watershed recommends future teams educate electricians about the potential Red List pitfalls of both types of wire. Start with evaluating non-PVC, LSZH options for both. If LSZH is not viable (likely due to minimum order quantities or market availability), utilize XHHW where possible and use the appropriate Red List exception. Use of XHHW wire for interior applications may result in higher labor and material costs so strategize with the electrician in preconstruction, not during submittals/construction.
- During the time of procurement for Watershed (2019-2020), very few LSZH MC cable options existed. The market has improved and LSZH is more common/available now.
- As of March 2023, Southwire, and General Cable both offer LSZH MC cable products. Encore Wire does not.
Fire Suppression Systems
- It is extremely difficult to find a non-PTFE/Teflon based sealant tape for fire sprinkler heads, the Misc. Hardware exception was utilized for this reason, although the General Red List exception could have also been utilized. This same issue was identified in multiple other Skanska LBC projects. Watershed recommends continuing to advocate with manufacturers for non-Teflon sealant tapes.
- Fire sprinkler fittings and couplings sometimes come with an industry standard orange enamel paint. This paint may contain Phthalates. Watershed recommends working with fire sprinkler trade partners to continue to search for a Red List free substitute for this orange enamel paint, the L6 & L7 TI team was unable to find one.
Plumbing
- Many codes (including Seattle code) require no-hub cast iron pipe couplings to use neoprene as the gasket material for couplings. Make sure to show strong advocacy documentation to the local AHJ around this topic. Alternatively, see if non-cast iron materials (like ABS) may be suitable for a given application.
BEAUTY PETAL
Watershed sought to fulfill the goals of the Beauty Petal with a thoughtful design that quietly celebrated the project’s many green strategies while inviting occupants and pedestrians to enjoy respite and discovery at the site.
The project’s water story is featured throughout Watershed’s design. The project addresses the polluted stormwater runoff coming from the neighboring Aurora Bridge with a unique stepped series of lushly planted bioswales along the Troll Avenue right of way improvements. Cleaning nearly 400,000 gallons of roadway runoff annually. The lush landscape around the bioswales is interspersed with benches so people can pause and enjoy the area.
In addition to capturing stormwater from the bridge, Watershed’s design features its unique system for capturing rainwater on site. Its overhanging, sloped roof is ideal for capturing rainwater and the roof’s form is celebrated with a cantilevered front edge, clad in stained cedar, uplit, and visible from street level.
From the sloped roof, a sculptural steel gutter system cascades down the alley side elevation to an oversized, folded weathered steel scupper directing the water to the underground cistern. During a rain event, the weathered steel scupper functions as a public art piece that highlights the water being captured. The combination of exterior features add to the sense of discovery surrounding the building’s operation, and educates the public about the rainwater catchment aspect of the project.
The project includes educational signage integrated into the landscape so passersby can learn about the building’s visible rainwater and stormwater systems. The plaques include patterns etched in steel for visitors to make rubbings with paper and chalk. We have enjoyed seeing children learn using the plaques!
As building visitors enter through the open-air lobby, a light well open to the sky allows rainfall to be part of the visual, acoustic, and tactile entry experience. On the east wall of the light well, across from the primary stair, a quote from Benjamin Franklin provides inspiration and contemplation: “When the well is dry, we know the worth of water.”
Materiality and the Neighborhood’s Industrial history
A simple palette of neutral, natural exterior materials adds another layer to the story. The suspended glass cube form is comprised of electrochromic glass with minimal frame; this simple form reflects the dramatic steel truss structure of the 1932 bridge overhead. The dynamic and responsive high performance glazing changes from light to dark and back to light again throughout the day in response to the sun’s position, signaling the smart management of heat gain and glare.
The concrete masonry unit wall on the eastern edge of the building is laid out in a gradient pattern made up of rough and smooth blocks. The dramatic weathered steel hanger door features a laser-cut design celebrating the neighborhood’s renowned annual Solstice Parade through celestial imagery. The weathering steel weir walls, bridge grates, and gabion walls in the landscape express the connection to the industrial past.
Biophilia and Connection to Nature
Watershed’s design includes many features meant to enhance occupants’ connection to nature. They included:
- Reinforced concrete panels at the base that continue the movement of water with its rippled form.
- Board-formed concrete in the entry and lobby space offers the texture and visual grain of wood.
- Reclaimed formwork is reused as an accent wall in the interior elevator lobby as well as for an art piece in one of the tenant spaces.
- On the north façade, facing a multi-family building across the alley, sixty vertical feet of stainless-steel wire provides a trellis for growing vines up the building.
- The punched window patterning on the north and west facades is staggered between floors to imply a cascading movement.
- The lush landscape with pollinator plantings connects to an existing neighborhood pollinator pathway plan and helps support our bee hives located on the roof. The plantings soften the urban terraces stepping down the hillside along Troll Avenue.
- Angled concrete walls in the right of way recall patterns from the neighborhood’s lumber mill history. Historic images taken from the Watershed site showed logs floating in the lake beyond, at the base of the Aurora Bridge. The walls also slow the building’s stormwater runoff to encourage opportunity for evaporation, an ecological function that was once plethoric in the forested environment that existed pre-development.