Sunshine Mathon designed and remodeled the Willowbrook house with the primary goal of providing his family with an inspiring and comfortable place to live. A critical aspect of the inspiration was to reduce the impact of his family’s lifestyle on the land, and the community in which they live.
Though Mathon had a tacit goal to achieve net zero energy with the house, he honestly did not expect to achieve it. The existing house, built in 1948, is located in a well-established neighborhood and aligned with the overall character of the area. The goal was to build an addition, remodel the existing house, and simultaneously retain the existing character while embedding a sense of personal craft.
Vital Stats | |
---|---|
Certification Status | Net Zero Energy Building Certified on May 21st, 2014 |
Location | Austin, Texas, USA |
Living Transect | L3 |
Typology | Building |
Occupant Type | Residential |
Project Team | |
---|---|
Owners | Sunshine and Emily Mathon |
Architectural | Sunshine Mathon |
Landscape | Sunshine Mathon |
Structural | Sunshine Mathon |
Interior Design | Sunshine Mathon |
Plumbing | Sunshine Mathon |
Mechanical | Sunshine Mathon |
Electrical | Sunshine Mathon |
Lighting Design | Sunshine Mathon |
Contractor | Sunshine Mathon |
Key Subcontractors | RM Mechanical (Mechanical), Lighthouse Solar (Solar Electric), Techsun (Solar Hot Water), Hill Country Insulation (Spray Foam), Green Oaks (Exterior R-ETRO Insulation Installation), Shiloh Travis (Construction Manager) |
PLACE PETAL

01. LIMITS TO GROWTH IMPERATIVE
SITE PRIOR CONDITION Previously developed and existing building
ENERGY PETAL
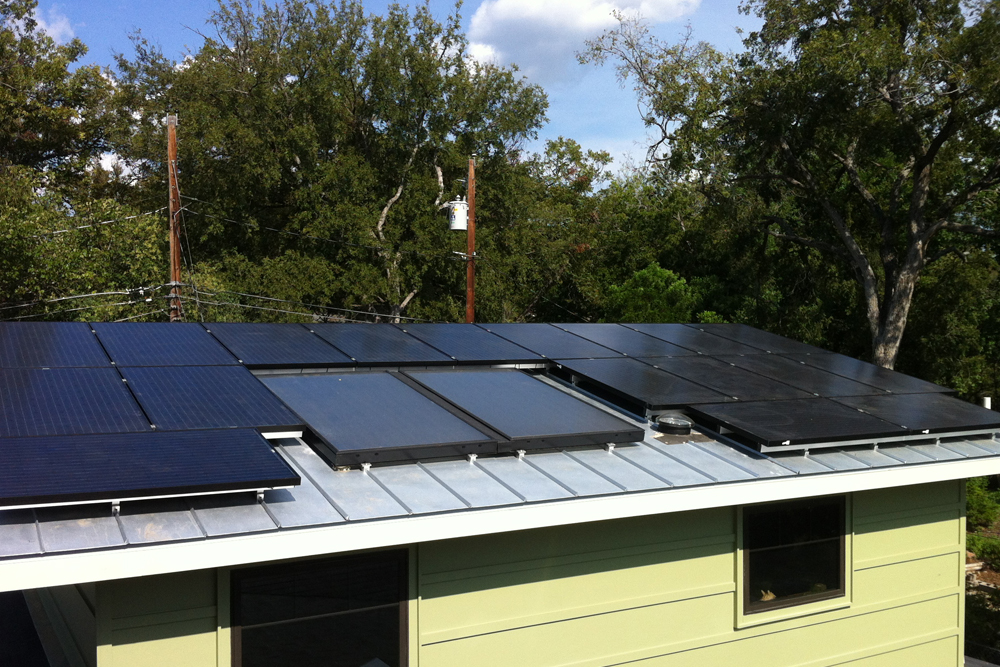
ANNUAL ENERGY USE
Actual | 5,310 kWh/yr |
Energy Use Intensity | 8.59 kBTU/sf/yr |
END USE BREAKDOWN
Heating | 228 kWh/sf/yr |
Cooling | 1,628 kWh/sf/yr |
Lighting | 100 kWh/sf/yr |
Plug Loads & Equipment | 3,167 kWh/sf/yr |
Domestic Hot Water | 187 kWh/sf/yr |
RENEWABLE ENERGY SYSTEM
- 4.5KW DC 18 250W panels + microinverters
- SOLAR HOT WATER 2 roof panels + 80 gal storage
DESIGN TOOL(S) & CIRCULATION METHOD(S)
eGauge circuit level data tracking utilized to track minute-level data on most circuits in the house.
EFFICIENCY MEASURES
From an energy perspective, the existing house performed quite poorly. The concrete block envelope had no insulation. The original single-pane, steel-framed windows did not close properly and provided near zero thermal performance. The insulation on the attic floor was 3”-4” thick at best. Though the attic was vented reasonably well, the central HVAC air handler and ductwork were located in a space that likely reached 160º+ in July and August. The air conditioning system and gas heat were a decade old, and though in acceptable condition, were far from efficient. The gas hot water heater was 30+ years old and on its last legs. From an energy consumption perspective, the house had only three redeeming facets to its character, all of which are actually critical to the current success of the recently amended house:
- The well-chosen solar orientation
- The well-designed overhangs, and
- The thermal mass of the concrete block
WINDOWS
The windows needed replacing. Mathon was working with a concrete structure, however, so he chose not to modify the openings. He had also decided that the new guise of the house would reflect the original character. As he specified the new fiberglass windows, he maintained the divided-lite ratios in similar casement forms.
Specifically, Mathon chose Pella double-paned, fiberglass-framed windows. With a U-value of 0.30, from a thermal performance perspective, the windows were sufficient, but nothing extraordinary. More critical, however, in Austin’s hot, humid climate, is the Solar Heat Gain Coefficient (SHGC) to control solar insolation. As a higher SHGC commonly translates to a lower visible light transmittance, he chose to specify different low-E coatings depending on shading and orientation of the window. An inclusive solar study of the house revealed which windows would be subject to significant solar exposure during hot, sunny periods of the year. These windows were specified with a 0.18 SHGC low-E coating; all others received a 0.24 SHGC coating.
The choice of the fiberglass frame was intentional. Fiberglass frames have similar excellent thermal resistance and rot-resistance properties as vinyl, similar rigidity and strength as aluminum, and a far better thermal expansion relationship to the glass of the window than any other framing material. As windows heat and cool, they expand and contract. When the expansion rates are dissimilar, such as between glass and vinyl or wood or aluminum, the seal between divergent materials eventually becomes compromised, affecting performance. Fiberglass expands and contracts at a very similar rate to the glass it frames, mitigating this issue.
ATTIC
As the attic was the only practical location for the air handler and ductwork, and the cost of a ductless minisplit was prohibitive, Mathon sealed and insulated the attic with 8 inches of open cell spray foam at the roof plane (~R-28). Although R-38 is the rule of thumb goal for attics in Austin’s climate zone, it assumes insulation on the attic floor and no ductwork in the attic.
NATURAL GAS
To position the house to achieve Net Zero Energy Building certification, Mathon disconnected the gas line. Two of the previous gas uses were straightforward to switch. The gas cooktop changed to an induction cooktop; and an air-source heat pump version of the air conditioning system replaced the gas space heating.
HOT WATER
The hot water, however, posed a puzzle that Mathon still continues to engage periodically. He had immediately assumed solar hot water was the clear answer. Mathon had overseen the installation of a great number of solar hot water heaters in Austin and had an established, trustworthy relationship with a local installer. However, part way through construction, he read an article by Martin Holladay (Senior Editor of Green Building Advisor) that caused him to reconsider. Holladay’s basic argument was that the combination of inexpensive solar electric and high efficiency heat pump water heaters challenged the decades-old assumption that solar hot water represented a more effective cost-payback proposition.
However, Martin did caveat his assertion with a few considerations. One of the most pertinent to his household related to how much hot water gets utilized in the household. The less hot water used, the less effective efficiency heat pump hot water heaters exhibit as heated hot water sits for extended periods and has to be reheated. Knowing that he was installing 1.0 gallon per minute showerheads and very efficient aerators on all the faucets, even though we was working with a four-person home, he suspected they’d use less than most households.
Ultimately, Mathon chose to move forward with the solar hot water install, but the decision largely hinged on being far enough down the construction path to make alteration challenging. The original gas water heater was located in the garage. Maintaining this location would have made the plumbing runs to the new master bathroom, including laundry, quite long. Mathon designed a new hot water closet close to the center of the house with a clean vertical run to the solar hot water panels on the roof of the second story loft, thereby improving the efficiency of that system. Providing sufficient makeup air to a heat pump water heater in this location would have been challenging at best.
For sake of comparison, Mathon has two hot water panels on the roof, taking up the equivalent square footage as ~1.25kW of solar electric. Given the performance of the rest of the solar electric array, these panels would have produced ~1,725 kWh annually. Using estimates from both EnergyStar.gov and GE’s heat pump websites as references, a heat pump water would have consumed 1,800-2,200 kWh in the same year. Given that the solar hot water array utilized 187 kWh for circulation pumping and backup electric resistance heating on streaks of gray days, the scenarios are roughly equivalent from a simple performance perspective. Surprisingly, the comparison is also very close from a cost perspective. After local rebates and federal tax credits were accounted for, the solar hot water solution was marginally more cost effective.
The installed solar hot water drain-back system, with an 80-gallon storage tank, typically gets the household through three days of gray weather. In Austin, with an average of 300 days of sun a year, the electric resistance backup element energized only a handful of days last year.
THERMAL MASS
The concrete block envelope of the original house had zero insulation. Mathon recalled a phrase from his classes with Paco Arumi, a theoretical physicist turned architecture/building science professor at UT Austin, “Always place your thermal mass inside the thermal envelope.” Mathon applied his computational models to run scenario after scenario and the results were always striking.
For many people familiar with the concept of thermal mass in buildings, the idea is often conflated with ‘70’s “passive solar” architecture using southern-facing windows and Trombe walls, or equivalent, to capture and hold heat from day to night, or with vernacular architecture from arid regions that use stone or earthen mass to mitigate significant diurnal temperature swings. Though the both ideas are sound, they do not speak to the hot, humid climate and condition of central Texas.
Every wall in the existing house was built with concrete block, interior walls included. Mathon’s goal was to pull all that mass inside a newly applied thermal envelope. With the contractor he had hired to manage construction, he explored numerous methods for mounting, properly draining and flashing a significant amount of insulation outside the concrete structure. Mathon considered ZIP R-panels, which, incidentally, were used on the stick frame construction for the addition on the house, but that was going to provide only R-6.6. He considered two layers of polyiso rigid insulation, but the attachment methodology and labor costs were both challenging. His research lead to Quad-Lock’s R-ETRO, a system specifically designed to mount pre-cut, interlocking EPS foam blocks to the exterior of a concrete structure. Mathon chose to install the R-18 4-¼” foam blocks. This choice proved extremely impactful on the performance of the house as a whole.
Mathon makes the claim of importance for the thermal mass in part because the envelope of the 1,100 square-foot addition is satisfactory, but not extraordinary. The addition was framed with 2”x4” studs using advanced framing techniques to minimize wood and maximize insulation. The stud cavities were filled with open cell spray foam (R12.6) and sheathed with ZIP R-panels, which are impregnated OSB sheathing that functions as an integral weather barrier with an additional sheet of polyiso insulation (R3.3) laminated to the interior side of the sheathing, thereby breaking the thermal bridge of the wood studs. The insulated roof, the vaulted ceilings of the addition, follows the same methodology, just more of it. The ceiling joist cavity has an R-value of 26.1 with a continuous insulation R-value of 6.6. Satisfactory, but not extraordinary.
COOLING
Properly sizing an air conditioning system in Austin’s hot, humid climate is critical. Moisture management is key. Some estimates suggest that roughly half the energy consumption from air conditioning in Austin’s climate just dehumidifies the air. This issue is even more critical in buildings with high performance envelopes as the sensible load, the simple heat in the air, is more passively managed by an effective envelope.
Mathon had professional experience with variable speed heat pump systems. The enormous potential variable speed systems have in the project’s climate is that they adjust their effective sizing, and the amount of energy consumed for both latent and sensible load control, as conditions evolve. The challenge in variable speed systems (at least in the Austin area) lay in their first costs.
Mathon contemplated a few variable speed solutions, from a ducted whole house air handler, with no zoning, to multiple non-ducted air handlers with independent zoning control. The cost was prohibitive. In the end, he specified a 19-SEER Carrier Infinity heat pump system with similar, yet limited, properties to variable speed systems. Though the outdoor unit is technically 3-ton system, it is capable of stepping down to a 2-ton capacity when the loads are small. Mathon found the system runs in 2-ton mode most of the time.
The indoor air handler is also variable speed and is ducted to the three zones throughout the house, each with an independent programmable thermostat control. On summer nights, as one zone, the temperature and humidity in the bedrooms are controlled to a comfortable sleeping level, typically 80º and 52% (or less) relative humidity. The other zones, the daytime living spaces and the loft, are left unconditioned. During the day, at times when the home is occupied, the conditions are reversed. The bedrooms stay unconditioned and the daytime living spaces are managed, usually set to 78º or 79º, with the same relative humidity level.
FANS
In all cases, however, ceiling fans play a critical role. Mathon estimates that ceiling fans allow him to keep the room temperatures 2º-3º higher than would otherwise be comfortable. Not all ceiling fans are made equal, however. Knowing that ceiling fans would spinning through much of the year, Mathon searched extensively for affordable fans with induction motors, which can often push 2-3 times as much air for the same energy compared to more basic Energy Star-rated fans.
VENTILATION
Given that he was replacing windows, providing an opportunity to flash and seal them properly, and was adding so much insulation to the exterior of the existing structure with careful attention to air sealing details, Mathon suspected that the overall house would be relatively airtight, though not extraordinarily so. Such an envelope requires effective ventilation management to be sure that ample fresh air is provided, yet without a huge energy penalty to condition it.
Energy recovery ventilators (ERV) quasi-passively transfer the embedded energy in conditioned air to fresh outdoor air as the two air streams, one out and one in, are blown across either side, respectively, of a heat and moisture exchanger. The fresh air is effectively pre-treated as it enters the house. During the summer and winter, when windows are rarely opened, the ERV operates during the most energy-beneficial portions of the day or night, depending on the season. In all seasons, the ERV acts as the bathroom fan, via timer switches, to manage high moisture loads in those specific spaces.
ENGAGEMENT
Having spent much of his childhood in Vermont chopping firewood for the woodstove and, at times, hand pumping water from a well, Mathon gravitates towards engaging his home as a place that compels tend and care, providing comfort and shelter in return. He pays attention to the weather two to three days out, strategizing when to open the windows to cool or heat the thermal mass. He pays attention to the rain, planning when to do a load of laundry so that it can hang dry before the rain arrives. He pays attention to a forecast of two or more days of cloudy weather, planning the use of hot water carefully. While some might find these efforts burdensome, Mathon finds them cathartic and cyclically engaging, as by the season.
EQUITY PETAL
16. UNIVERSAL ACCESS TO NATURE & PLACE IMPERATIVE
Mathon directly engaged with immediate neighbors on all adjacent lots during the addition design process – particularly the loft that reached two stories. Two of the four adjacent neighbors had concerns about either shading or view from the loft. Mathon intentionally set back the loft portion from the sides of the house to minimize shading and placed windows to minimize view into adjoining lots.
BEAUTY PETAL
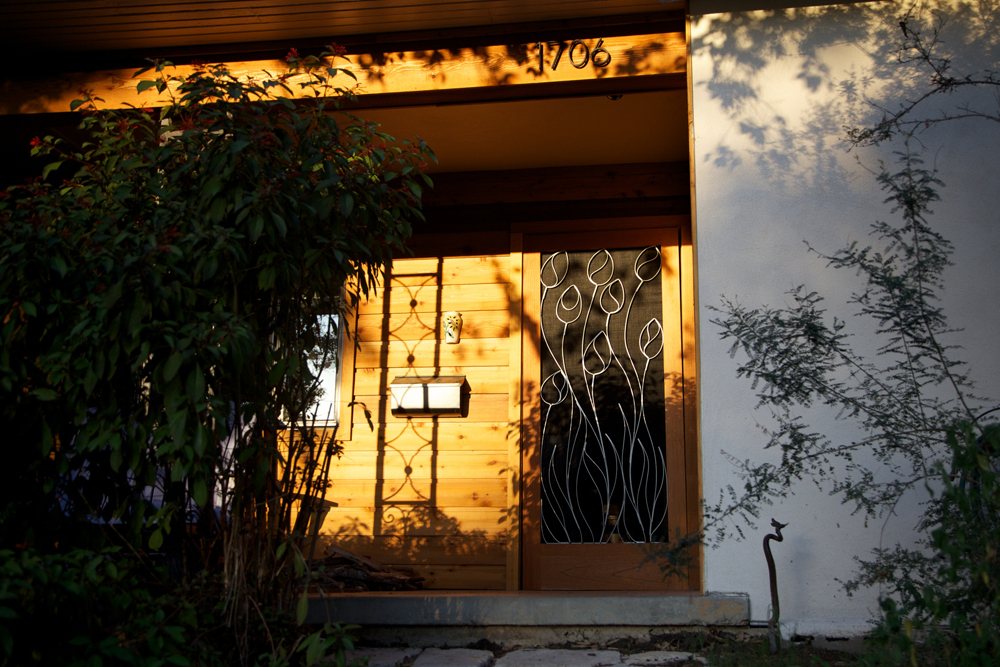
THE ROLE OF BEAUTY, FROM OWNER SUNSHINE MATHON
Set on a slope, six feet above the street frontage, the original house was built in 1948, one of many in the neighborhood built during the post-WWII housing boom. Most of the houses in the area, both duplexes and single family, were built with the durable, somewhat innovative, and readily available material of the time, concrete block. With an unassuming white stucco exterior, lathe and plaster interior wall finishes, and black steel casement windows carefully located throughout the well-proportioned form, the house modestly hinted at the mid-century modern design ethos that was emerging at the time.
The entry to the house, an 8-ft by 14-ft extension of the slab foundation, was held between the forward-shifted footprints of the bedrooms and garage. The roofline carefully covered the slab with clear understanding of its southwest orientation. Whomever designed the original house thought quite carefully about the depth of roof overhangs and entry shading. The sun merely trims the edge of the porch slab during the searing summer months, yet during the winter, the sun is welcomed, carrying deeply into the interior of the house during the afternoon hours.
- CRAFT
Hand-crafted from hollow black steel and translucent glass, the entry to the house is not simply beautiful, it communicates a moment of singularity. The front door, through the care and craft of its design and hand-built nature, claims simultaneous expression and character. The decision to keep the door, though its thermal performance is very poor, was not difficult to make. - PECAN
In the 1940s, freshly cut boards of dense, variegated Pecan, striated with shades of rust and soil and limestone, were laid atop a fifty-year old, worn warehouse floor in Waco, TX. Decades later, smothered in layers of dull paint, the floor was saved during the demolition of the warehouse. The planks were planed and sanded. The rust and soil and limestone are exposed as stairs and flooring throughout the addition to the house. - STAIRS
The stairs spatially frame and connect distinct regions of the common space of the house – living room, art space, children’s corner. The treads, six-quarter slabs of hundred-year old Longleaf Pine, rest atop a rising pattern of climbing Pecan, turning vertical, horizontal, vertical, reaching and growing upwards towards the loft. - STEEL
Thin plates of blackened steel adhere to an open wall, skewed to the left and then to the right and then back again. Separated by equidistant ranges of white paint, the horizontal plates create a wide, flat, seven-foot tall ladder on the wall. My photographs, mounted on varying magnitudes of black foam core, magnetized to the steel, span black, white, black. - BEAMS
Where once concrete block ended the rear of the house, cautiously open spans were broken through. At the meet of Pecan and Oak on the floor, woods of the same era, squared Cedar trunks bridge above, carrying the seam of old and new. Though the story is lost, the texture of saw teeth and sheer dimensions imply a stout and functional history. I am almost always compelled by craft, compelled by the result of a careful creation of a thing, a somatic, sometimes speculative, articulation of an imaginable function.