The headquarters for The David and Lucile Packard Foundation in Los Altos, California brings staff, grantees and partners together to solve the world’s most intractable problems. Passive, bioclimatic design strategies support the core philanthropic mission while serving as the basis of LEED Platinum building certification and Net Zero Energy performance.
The Packard Foundation’s connection to the Los Altos community dates back to its inception in 1964. For the two decades, as the Foundation’s grant making programs expanded locally and around the world, staff and operations have been scattered in buildings throughout the town. This project enhances proximity and collaboration while renewing the Foundation’s commitment to their local community by investing in a downtown project intended to last through the end of 21st century.
The project’s focus on sustainability brings their facilities into alignment with their core work of conserving and restoring the Earth’s natural systems. Their new home, the largest Net Zero Energy office building in California, is the cornerstone of their effort to demonstrate how an organization can improve its effectiveness and the quality of life for its employees while emitting carbon at the rate needed to keep global temperature rise below 2°C.
PROJECT WEBSITE packard.org/about-the-foundation/our-green-headquarters/
Vital Stats
Certification Status | Net Zero Energy Building Certified on September 16th, 2013 |
---|---|
Location | Los Altos, CA, USA |
Bioregion | California |
Living Transect | L4 |
Typology | Building |
Occupant Type | Offices |
Project Team
Civil | Sherwood Design Engineers |
---|---|
Landscape | Joni L. Janecki & Associates, Inc. |
Structural | Tipping Mar |
Architectural | EHDD |
Interior Design | EHDD |
Plumbing | Integral Group |
Mechanical | Integral Group |
Electrical | Integral Group |
Lighting Design | J S Nolan + Associates Lighting Design, LLC |
Specialty Consultants | Ausenco (SCADA Engineer) |
Contractor | DPR Construction |
Subcontractor(s) | Site Utilities: SANCO, Landscape: Park West, Mechanical: Western Allied, Mechanical Controls: SYSERCO, Plumbing: ACCO Engineered Systems, Electrical: Redwood Electrical Group |
PLACE PETAL
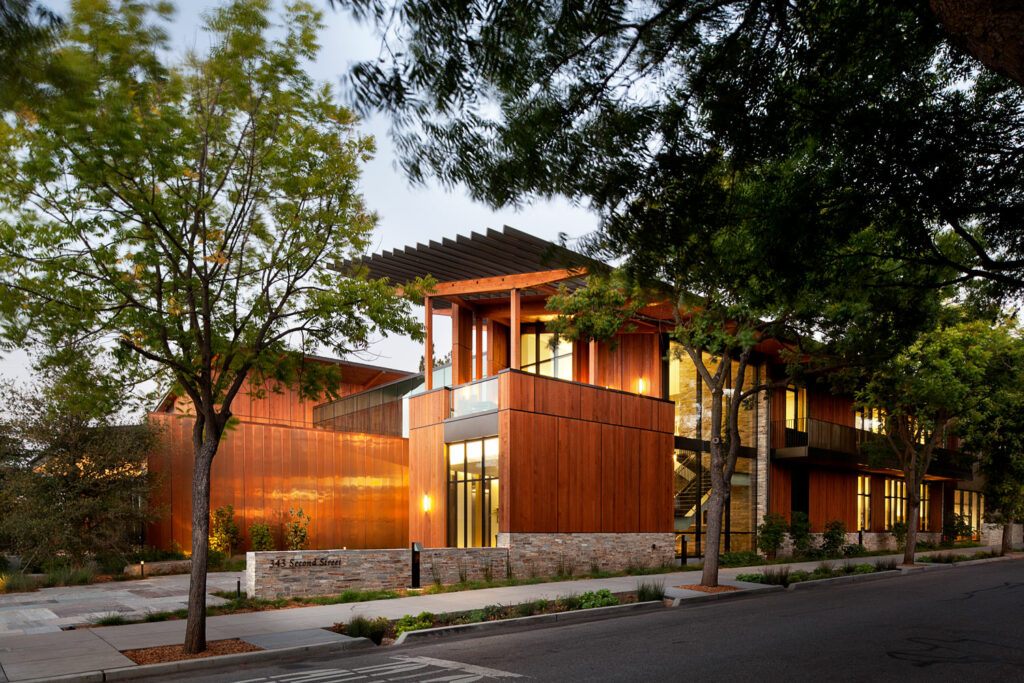
01. LIMITS TO GROWTH IMPERATIVE
As a previously developed site, this project meets the Site Petal’s Limits to Growth Imperative, which requires all project pursuing certification through the Living Building Challenge be built upon previously developed sites, greyfields and/or brownfields.
ENERGY PETAL
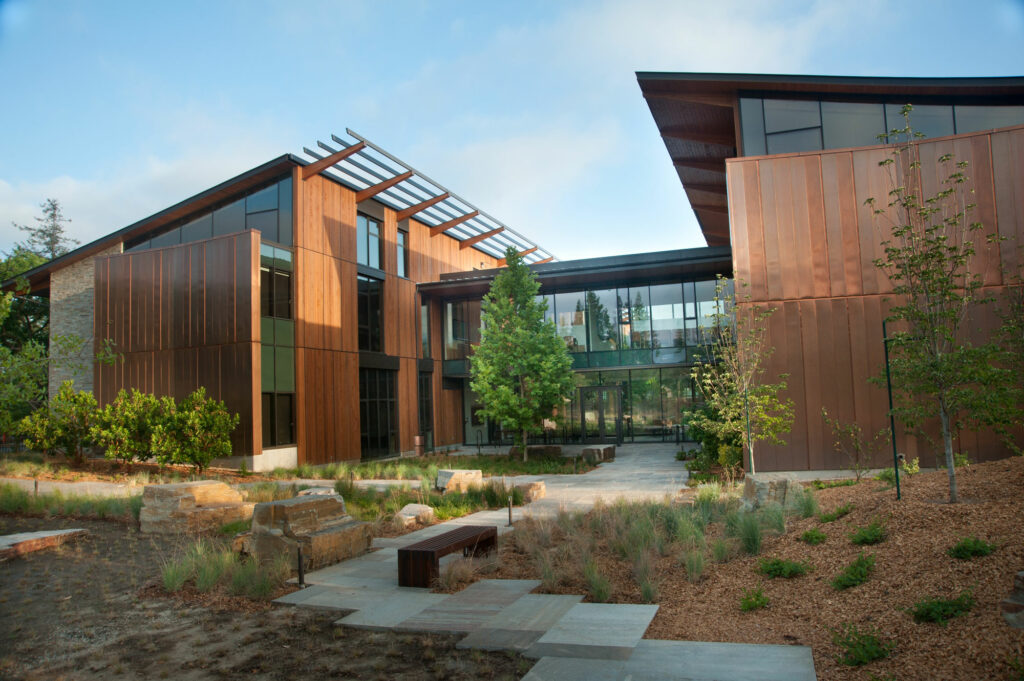
TYPE & SIZE OF RENEWABLE ENERGY SYSTEM
- Roof-mounted PV panels
- 309 MWhr/yr
- 285 kW capacity
The orientation of the building and slopes of the roof are not optimized for solar collection. The southwest/northeast orientation results in only about a 3% less production than facing due south. Panels on the Northern roof facing northeast have an additional 7% decrease in production versus the southern exposure.
Based on initial calculations performed for this project, it was determined that a photovoltaic system of approximately 291KW would be required to offset the building electrical load. A system this size would be able to fit on the roof of the building with careful design coordination. The photovoltaic analysis was based on the following information:
North Roof | South Roof | Parking Lot | Totals | |
---|---|---|---|---|
Number of Panels | 448 | 357 | 110 panels | 915 panels |
Watts per panel | 318 W | 318 W | 318 W | – |
Tilt | 12°, facing NW | 12°, facing NW | 0° | – |
KW | 142 KW | 114 KW | 35 KW | 291 KW |
Production | 130 MWh/yr | 133 MWh/yr | 42 MWh/yr | 305 MWh/yr |
Based on an energy model, designers anticipated the building would consume 247MWh/yr, so the PV production would allow an offset 100% of the building energy consumption with a 19% safety factor. Energy production calculations were based on the SunPower SPR-318 solar panel, the most efficient panel on the market at the time. These high efficiency SunPower panels were necessary to meet the anticipated energy demand because the team already maximized the amount roof and parking lot area that they could reasonably expect to cover with PVs.
ANNUAL ENERGY USE
Designed/Stimulated | 277 MWh |
Actual Energy Use | 351.30 MWh |
Actual Energy Use Intensity | 24.38 KBTu |
Annual Electricity Generated | 418.04 MWh |
Net Energy Use | -66.73 MWh |
END USE BREAKDOWN
Heating | 324,000 kWh |
Cooling | 106,600 kWh |
Lighting | 508,400 kWh |
Fans/Pumps | 390,000 kWh |
Plug Loads/Equipment | 745,000 kWh |
Domestic Hot Water | 535,000 kWh |
Other (heat rejection, exterior lighting) | 322,300 kWh |
NET ZERO ENERGY DESIGN STRATEGIES
ENERGY MONITORING
Individual branch circuit monitoring is employed so that the energy consumption of each load can be pinpointed and pieces of equipment which consume large amounts of power can be easily identified. This monitoring is accomplished using electric panelboards specifically designed for the task. Data can be extracted from the panelboards integrated datalogger and used in a variety of ways: scientific research, incorporation into a web-based interface, to monitor and control certain circuits, etc. The SquareD PowerLogic BCM panelboards are used for individual circuit monitoring. For loads connected directly to the switchboard such as the elevator and large mechanical loads, individual meters are used.
Overall building energy monitoring and power generation monitoring is provided in accordance with the California Energy Commission rebate program. All monitoring devices are connected to the building Supervisory Control and Data Acquisition (SCADA) system. Nearly 15,000 monitoring and control points are part of the building automation system.
DAYLIGHTING
The building design, consisting of two long, narrow wings surrounding a center courtyard, reduces energy consumption by maximizing daylighting. The buildings shape, orientation and window placement results in a 30% reduction in the amount of energy consumed by artificial lighting that a comparable standard commercial building. Automated systems throughout the building measure free, natural daylighting levels and automatically dim or brighten artificial light as needed. Light shelves project natural light farther into space and reflect it off the ceiling to diffuse daylight throughout the space.
ENERGY-SAVING FEATURES
- Energy-efficient T-8 fluorescent bulbs
- LED task lighting
- Workspace occupant sensors that turn lights off and put computers and monitors to sleep when spaces are unoccupied
HEATING, VENTILATION & AIR CONDITIONING (HVAC)
In cold weather, the building is warmed to a target temperature of 74°F starting three hours before employees arrive at work. Once the workday begins, the heating system typically turns off and the building relies upon heat gain from office equipment and the occupants themselves to maintain a comfortable temperature. The building is heated by a combination of air handlers, and in certain areas, by heated water in the (chilled) beams.
In warm weather, water is cooled at night by a compressor-free cooling tower and stored in two 25,000-gallon underground tanks. During the day, the cool water is pumped into the pipes that run through the chilled beams. Three major air handling units pull in 100% outside air, then filter and dehumidify it. Air flowing across the beam is sufficient to cool the interior spaces.
The chilled water is moved through the system using variable speed bumps and pipes angled at 130°rather than typical 90° angles. This is much more efficient than standard practices, allowing for a 75% reduction in ductwork and a 75% reduction in pump energy.
When possible, occupants reduce energy consumption by operating in natural ventilation mode with windows and doors open, instead of depending on the HVAC. The building management system has a dashboard that informs users when to open and close windows and sliding doors in order to optimize natural ventilation and reduce energy consumption.
DESIGN TOOL & CALCULATION METHOD
- eQuest
EQUITY PETAL
The building does not block access to, nor diminish the quality of fresh air, sunlight and natural waterways to any member of society or adjacent developments. The building is sited at a minimum distance of 60’ horizontally or any adjacent neighboring structure. The altitude angle of the sun at winter solstice between 10:00 am and 2:00 pm (which determines the maximum shading allowance) is 29.5 degrees. The height of the roof at the exterior edge of the building is 25.4’. The length of shadow, therefore, at that time is 45’. Since a 10m shade height is allowed on an adjacent façade, and the shadow does not reach any part of any adjacent façade, the building complies with this requirement.
BEAUTY PETAL
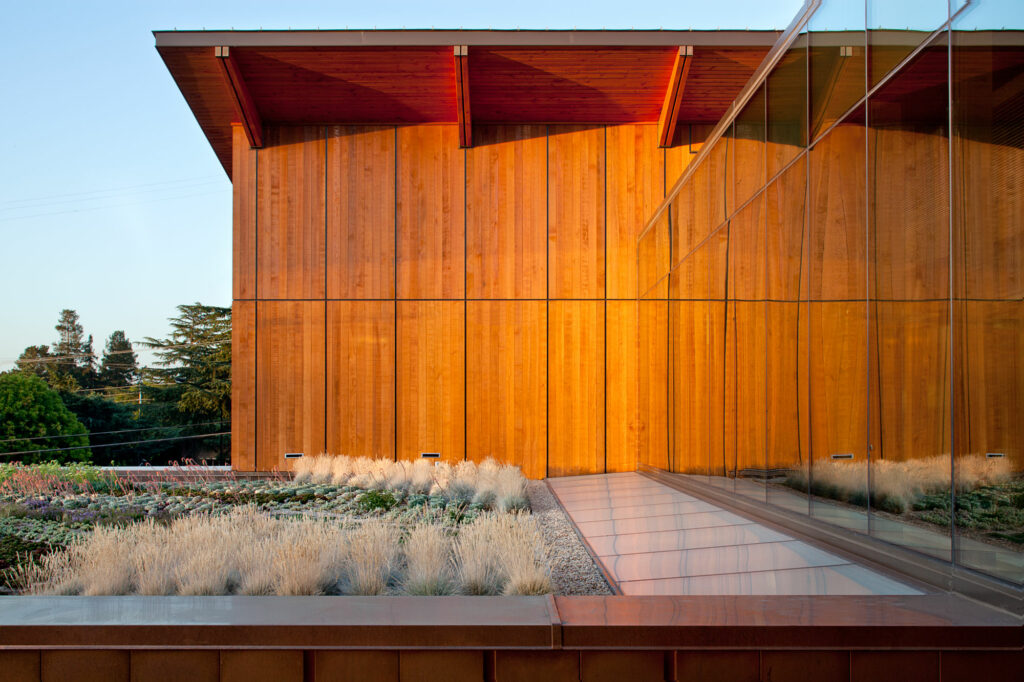
20. INSPIRATION & EDUCATION IMPERATIVE
THE ROLE OF BEAUTY, FROM PROJECT ARCHITECTURE FIRM EHDD
In designing a new home for their family foundation, The David & Lucile Packard Foundation set out to show that a more sustainable life is simply a better life, through a building whose architectural design stimulates the senses and enriches people’s ability to work together on solutions for critical problems facing our world.
The family wanted a building that “fit in” architecturally to Los Altos and was responsive to the California climate. Early on, the design team chose to conform the building to the street grid – which is oriented 40 degrees off true north — in order to be good neighbors and affirm that sustainable buildings don’t have to stand apart from their neighbors. The energy penalty associated with being off the solar axes was accepted in favor of a massing that contributed to the urban fabric of the community.
The resultant design emphasizes connectivity between indoor and outdoor spaces and an operable façade that opens up through small and large openings to invite staff to access the outdoors. The entry design welcomes the visitor off the street through a landscaped path that reflects the importance that Lucile Packard placed on being a gracious host.
The design is tuned for the uniquely benign California climate emphasizing connectivity between indoor and outdoor spaces. The largest “room” in the project – the outdoor courtyard – functions as a casual meeting space set in a bucolic California landscape. It is the heart and soul of the project. As you move around the building on both floors you are rewarded with a constantly changing view of the courtyard landscape and the building wing beyond. Detailed design studies tested options to ensure a good outdoor micro-climate that would be inviting and comfortable all year round, with an optimized length, width and height for both winter warmth and summer cooling.
This is a building shaped by daylight and access to the outdoors. Two narrow, 40-foot wide office wings ensure all occupants are within easy reach of daylight, views and operable windows. The daylighting design achieves “perceptual brightness” – a space so well daylight that no one thinks to override the lighting controls. This is design for human delight and perception, not meeting a prescriptive footcandle level.
Sunshading is built into the design with elements such as deep external sunshades, overhangs, balconies, trellis and trees that do much more than simply keep sun off of the facades. They create a rich layering of light and shade that animates the building and outdoor spaces in a constantly changing play of light.
The end result is a porous and transparent building set in a climate-appropriate landscape that enriches the daily life of staff and the community. The landscape is split down the center of the site into “grassland” and “woodland” ecosystems, reinforcing the building parti while demonstrating the layered landscape of native plant communities. A green roof visible from the second floor hallways and boardroom is enlivened by a variety of shallow rooting, low growing succulents planted to create a mosaic similar to the bluffs on the California coast. This green roof is carefully arranged to be visible from a seated position in the boardroom and to instill biophilic elements along the circulation path.
Both interior and exterior architecture express the natural beauty of stone, wood, copper and glass. The elements are assembled in a way that honestly expresses contemporary construction practices while highlighting the expressive nature of naturally-finished materials. All wood is FSC Certified or salvaged including wood veneer sourced from Eucalyptus trees felled during the Doyle Drive rebuilding project in San Francisco. Exterior wood is FSC-certified Western Red Cedar. Stone is Mt. Moriah from the border of Utah and Nevada, within a 500- mile radius from the site. The exterior copper is 75 percent recycled, with a long life span and integral finish. The rich colors and textures inherent in these natural materials imbues the space within and without with a permanence and beauty befitting the institution and the town.
TOUR INFORMATION & EDUCATIONAL OPPORTUNITIES
The Packard Foundation offers tours of its headquarters on a monthly basis, in addition to a virtual tour.